Blogs
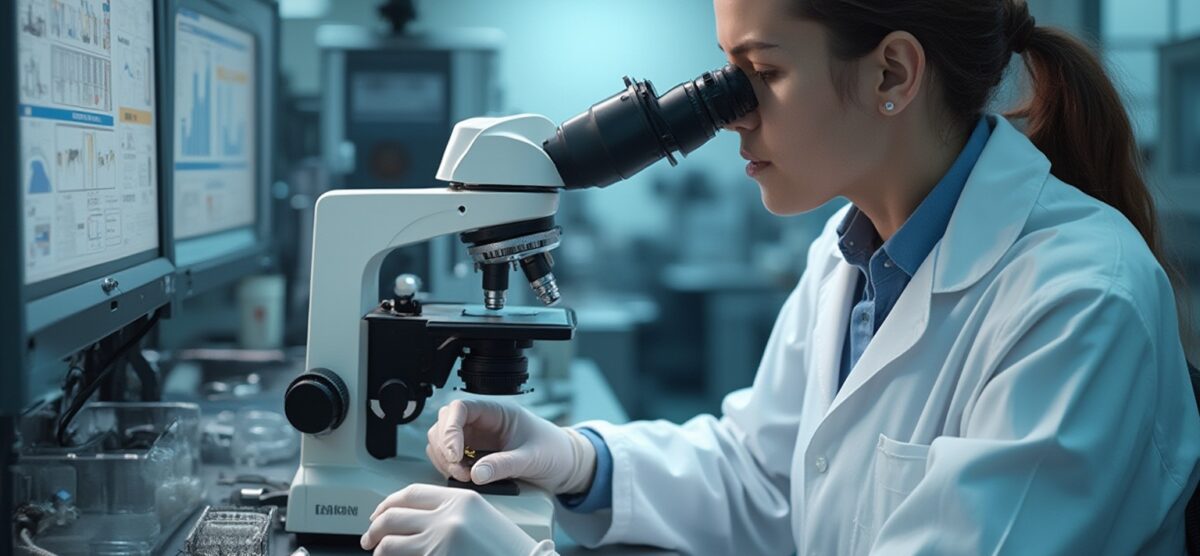
How to Choose Nickel Iron Molybdenum Alloys for Magnetic Circuits: A Step-by-Step Guide
Overview
Choosing nickel iron molybdenum alloys for magnetic circuits requires careful consideration of unique properties such as magnetic characteristics, mechanical strength, environmental resistance, and supplier reliability. The article emphasizes that understanding these factors, along with rigorous testing and cost analysis, is essential for procurement managers to ensure optimal performance and reliability in their applications.
Introduction
Nickel iron molybdenum alloys have emerged as indispensable materials in a variety of industrial applications, particularly due to their unique magnetic properties and impressive performance under demanding conditions. With a rich history of supply from experts like DOMADIA Group, these alloys are characterized by their high permeability, low coercivity, and exceptional corrosion resistance, making them ideal for critical components such as transformers and inductors.
As procurement managers navigate the complexities of selecting the right alloy for specific applications, understanding the essential properties, environmental factors, and supplier capabilities becomes paramount. This article delves into the intricacies of nickel iron molybdenum alloys, offering strategic insights into their selection, testing, and cost analysis, ensuring that decision-makers are well-equipped to leverage these materials for optimal performance and reliability in their projects.
Understanding Nickel Iron Molybdenum Alloys: Properties and Applications
The nickel iron molybdenum alloy for magnetic circuits, skillfully provided by DOMADIA Group since 1952, is celebrated for its exceptional properties, defined by high permeability and low coercivity, making it especially suitable for circuit applications. These materials, which comprise varying ratios of nickel (Ni), iron (Fe), and molybdenum (Mo), are a nickel iron molybdenum alloy for magnetic circuits that provides improved performance in electromagnetic fields. They exhibit superior corrosion resistance and high-temperature stability, essential for demanding applications.
The versatility of nickel iron molybdenum alloy for magnetic circuits is evident in its applications across critical components such as:
- Transformers
- Inductors
- Shielding
A thorough understanding of essential properties—including temperature stability, saturation magnetization, and electrical conductivity—is vital when selecting the suitable material for specific needs. For instance, the nickel iron molybdenum alloy for magnetic circuits, which includes permalloy made up of 80% Ni and 20% Fe, is preferred for its outstanding permeability.
Recent insights from G.N. Flint demonstrate that iron-nickel mixtures, particularly those within the Fe–36%Ni range, exhibit unique magnetic characteristics and low thermal expansion coefficients, with a room-temperature thermal expansion coefficient of less than 1 × 10^-6 per °C, making them invaluable in high-performance applications. Moreover, Bertotti emphasizes that the combination of low hysteresis losses and low classical losses makes the nickel iron molybdenum alloy for magnetic circuits ideal for applications at high frequencies.
Furthermore, a case study titled ‘Nickelocene as Precursor for Carbon Nanocomposite’ examines the innovative uses of nickel-based materials in creating advanced nanocomposite substances. The image showcases three coils of wire piled together, highlighting the metallic quality of the materials, likely composed of iron or a similar metal, neatly wound into circular forms. As progress in iron molybdenum combinations persists, along with continuous investigation into their attraction characteristics, procurement managers are urged to remain knowledgeable about the newest advancements to utilize these resources efficiently in diverse industrial uses.
Key Considerations for Selecting Nickel Iron Molybdenum Alloys in Magnetic Circuits
When choosing nickel iron molybdenum mixtures for electromagnetic systems, especially the DOMADIA Nickel Molybdenum Iron Combination, it is crucial to take into account several key factors to ensure optimal performance and reliability:
Unique Characteristics:
The DOMADIA Nickel Molybdenum Iron Alloy is distinguished by exceptional strength, corrosion resistance, and thermal stability. These properties make it a preferred choice for critical applications across aerospace, automotive, petrochemical, electronics, and renewable energy industries. Understanding these unique characteristics can guide your selection process.Magnetic Characteristics:
It is essential to assess the specific properties related to your application, including parameters such as permeability, saturation magnetization, and losses. For example, the minimum thresholds for 60 Hz AC electromagnetic characteristics are established at 220,000, acting as a quantitative standard for assessing material performance. Various metal mixtures display unique magnetic properties, making it essential to consult detailed technical datasheets to identify the most suitable option.Mechanical Properties:
Evaluate the mechanical strength and ductility of the material, especially if your application involves significant mechanical stress or requires forming processes. The mechanical integrity of the DOMADIA material plays a vital role in its performance under operational conditions. A case study on the mechanical mixing of NiFeCoMo compositions highlighted the successful synthesis of nanocrystalline structures, demonstrating promising mechanical properties that could be beneficial in various applications.Environmental Resistance:
Understanding the environmental conditions the material will encounter is necessary. Factors such as humidity, extreme temperatures, and exposure to corrosive substances can significantly impact the durability of a metal. Choosing materials with appropriate resistance properties can improve the durability and lifespan of your components.Quality Assurance:
At Domadia, the quality assurance processes for the Nickel Molybdenum Iron Alloy involve rigorous testing and inspection procedures to ensure compliance with industry standards. This includes thorough evaluations of mechanical and magnetic properties, as well as environmental resistance tests. Such quality assurance measures are critical for procurement managers to verify that the materials meet the required specifications, thereby mitigating risks associated with supply chain disruptions.Cost and Availability:
Conduct a thorough analysis of the cost-effectiveness of the selected metal. While high-performance materials like DOMADIA’s may offer superior characteristics, their pricing must align with your budgetary constraints, and their availability in the market should be considered to avoid delays in procurement.Supplier Reliability:
Building relationships with suppliers recognized for their quality and adherence to international standards is essential. This ensures that the materials meet required specifications and mitigates the risk of supply chain disruptions. For instance, the HyMu 80 mixture, a unoriented 80% iron-molybdenum composition, exhibits exceptionally high initial permeability with minimal hysteresis loss, emphasizing the significance of choosing the appropriate mixture based on its performance traits.
By thoroughly addressing these factors and incorporating insights specific to DOMADIA Molybdenum Iron Composition, purchasing managers can make informed choices when selecting nickel iron molybdenum alloy for magnetic circuits, ultimately improving the efficacy and reliability of these magnetic systems.
Evaluating Supplier Capabilities for Nickel Iron Molybdenum Alloys
When assessing providers of iron molybdenum blends, purchasing managers should take into account the following crucial criteria:
Quality Assurance: Verify that suppliers have stringent quality control processes, including international certifications such as ISO 9001, which ensure compliance with global standards and reinforce their commitment to excellence. At Domadia, our pure metal products undergo rigorous quality assessments to guarantee unmatched purity and reliability, making us a top choice for procurement managers.
Technical Expertise: A supplier’s technical knowledge regarding iron-based molybdenum materials is paramount. Suppliers should provide comprehensive information about the materials, detailing their properties, applications, and performance metrics, enabling informed decision-making. Domadia’s extensive industry experience equips us to offer tailored solutions, ensuring you receive products that meet your exact specifications.
Production Capacity: Assessing the supplier’s production capacity is vital, especially for large-scale projects. Inquire about their lead times and ability to accommodate urgent orders to ensure they can meet your demands without compromising quality. Our extensive selection of pure metal products, available in various forms—from sheets to custom components—ensures that we can fulfill diverse requirements promptly.
Past Performance: Reviewing a supplier’s track record with similar projects can offer valuable insights into their reliability and service quality. Look for case studies or client testimonials that demonstrate their experience and success in delivering nickel iron molybdenum alloy for magnetic circuits. For instance, research on the photomagnetic properties of Fe(ii) spin-crossover complex can illustrate the advanced applications of these alloys in materials science, reflecting our capability at Domadia. Our satisfied clients often share their positive experiences, further affirming our commitment to quality and service.
Customer Support: The quality of customer assistance offered by the supplier can greatly influence your purchasing experience. A responsive and knowledgeable support team is essential for addressing technical queries and resolving issues quickly. Domadia takes pride in outstanding customer service, ensuring that purchasing managers receive the support they need throughout the acquisition process.
Competitive Pricing: We understand the importance of cost-effectiveness in today’s competitive market. Domadia provides competitive pricing on all our pure metal products, ensuring you receive the best value for your investment.
Additionally, consider the role of specialized tools, such as non-sparking tools, in environments where explosive potential exists. Understanding the importance of these tools can further inform your choice of suppliers for related materials, such as electrical insulation and high-temperature components. This strategic approach not only improves supplier relationships but also guarantees adherence to pertinent regulations, such as REACH, requiring careful management by qualified personnel.
By thoroughly assessing these criteria, procurement managers can identify suppliers capable of providing high-quality iron molybdenum materials customized to their specific project needs, ensuring they make informed, strategic choices in their procurement processes.
Testing and Verification of Nickel Iron Molybdenum Alloys
To ensure nickel iron molybdenum alloys meet the necessary specifications, it is crucial to implement a thorough set of testing and verification procedures:
Material Composition Analysis: Initiate a comprehensive chemical analysis to confirm that the alloy composition aligns with specified standards. Utilizing techniques such as X-ray fluorescence (XRF) allows for precise and reliable results, ensuring compliance with stringent specifications.
Magnetic Characteristic Evaluation: Conduct tests to accurately measure critical properties, including permeability and coercivity. Advanced instruments like vibrating sample magnetometers (VSM) are essential for obtaining precise measurements, which are vital for applications requiring specific magnetic characteristics.
Mechanical Testing: Evaluate the mechanical properties of the materials through rigorous tensile and fatigue testing. These evaluations are necessary to confirm that the materials can endure the operational stresses encountered in their intended applications, thereby preventing premature failure.
Environmental Testing: If relevant, conduct environmental testing to assess the material’s performance under different conditions, such as extreme temperatures or corrosive environments. This guarantees the material’s reliability and durability in real-world scenarios.
Documentation and Reporting: Maintain meticulous records of all testing procedures and outcomes. This documentation is not only critical for compliance but also serves as a valuable reference for future projects, enhancing traceability and accountability.
In addition to these procedures, purchasing managers should be aware of the financial implications of their orders. For instance, shipping and handling fees for orders exceeding $5000.00 amount to $225.00, which is an important consideration when budgeting for materials.
Furthermore, as noted by Toshio Yonezawa, “Alloy 825 (UNS N08825) was developed from Alloy 800 with the addition of molybdenum (about 3%), copper (about 2%) and titanium (about 0.9%) to provide improved aqueous corrosion resistance in a wide variety of corrosive media.” This insight highlights the significance of comprehending material specifications and the improvements implemented in newer variants.
Lastly, the case study on Alloy 625 highlights its characteristics: originally developed for high-temperature applications, Alloy 625 is now widely used in wet-corrosion services. While it has good mechanical strength and corrosion resistance, it is increasingly being replaced by Alloy 31 (EN 1.4562/UNS N08031) in phosphate ore processing and flue gas cleaning due to better performance and cost-effectiveness. This real-world example underscores the importance of rigorous testing and verification to ensure optimal material selection.
By adhering to these thorough testing procedures, purchasing managers can confidently choose nickel iron molybdenum alloy for magnetic circuits that meet their performance and reliability standards, ultimately aiding in the success of their projects.
Cost Analysis and Budgeting for Nickel Iron Molybdenum Alloys
To effectively analyze costs and budget for nickel iron molybdenum composites, purchasing managers should follow a structured approach that ensures comprehensive financial planning and risk management:
Identify All Costs: Begin by identifying all costs associated with purchasing. This includes not only the initial material costs but also shipping, handling, and potential processing fees, ensuring a holistic view of the financial commitment.
Supplier Quotes: Solicit quotes from multiple suppliers to facilitate a competitive pricing analysis. It’s essential that these quotes include a detailed breakdown of costs, allowing for accurate comparisons and informed decision-making.
Total Cost of Ownership (TCO): Assess the total cost of ownership by factoring in long-term considerations such as maintenance needs, durability, and the costs associated with potential failures. Sometimes, a lower initial price may lead to higher expenses over time due to a shorter durability of the material. According to Procurement Resource, with the current drastic rise in the price trend for Nickel, the market is expected to strive for stabilization, indicating the importance of considering TCO in light of price fluctuations.
Contingency Planning: Allocate a percentage of your budget for unforeseen costs, which is crucial in mitigating risks linked to price volatility or supply chain disruptions. This proactive approach safeguards your project against unexpected expenses.
Budget Approval: Compile your cost analysis and present it to stakeholders for approval. It’s essential to validate the choice of certain alloys according to their performance, reliability, and overall value proposition, thus obtaining the required funding.
By carefully performing a comprehensive cost analysis and budgeting process, purchasing managers can improve the financial feasibility of their projects while ensuring the acquisition of high-quality iron molybdenum alloys. This structured method is especially pertinent considering recent market dynamics, where an anticipated surplus of 204 thousand tons in the metal by 2025 suggests possible changes in pricing and availability. Additionally, the case study of Vale, the world’s largest nickel producer, adjusting its production forecast due to adverse weather and COVID-19 lockdowns exemplifies the ongoing challenges in the nickel market that procurement managers should consider in their budgeting process.
Conclusion
Nickel iron molybdenum alloys stand out as essential materials in various industrial applications, thanks to their superior magnetic properties, corrosion resistance, and thermal stability. Understanding the unique characteristics of these alloys, such as their permeability and mechanical strength, is crucial for procurement managers aiming to select the right materials for their specific needs. With applications spanning from transformers to advanced nanocomposite materials, the versatility of these alloys cannot be overstated.
When evaluating suppliers, it is imperative to consider factors such as:
- Quality assurance
- Technical expertise
- Production capacity
- Customer support
These elements play a significant role in ensuring that the selected alloys not only meet stringent specifications but also enhance the overall performance of the projects they are intended for. Rigorous testing and verification processes further reinforce the reliability of these materials, confirming their suitability for demanding environments.
Lastly, a comprehensive cost analysis and budgeting strategy are vital in navigating the financial landscape of procurement. By identifying all associated costs and assessing the total cost of ownership, procurement managers can make informed decisions that align with their project goals while mitigating risks related to price fluctuations and supply chain disruptions. In a rapidly evolving market, staying informed about the latest developments in nickel iron molybdenum alloys will empower decision-makers to leverage these materials effectively, ultimately ensuring the success and reliability of their industrial applications.