Blog
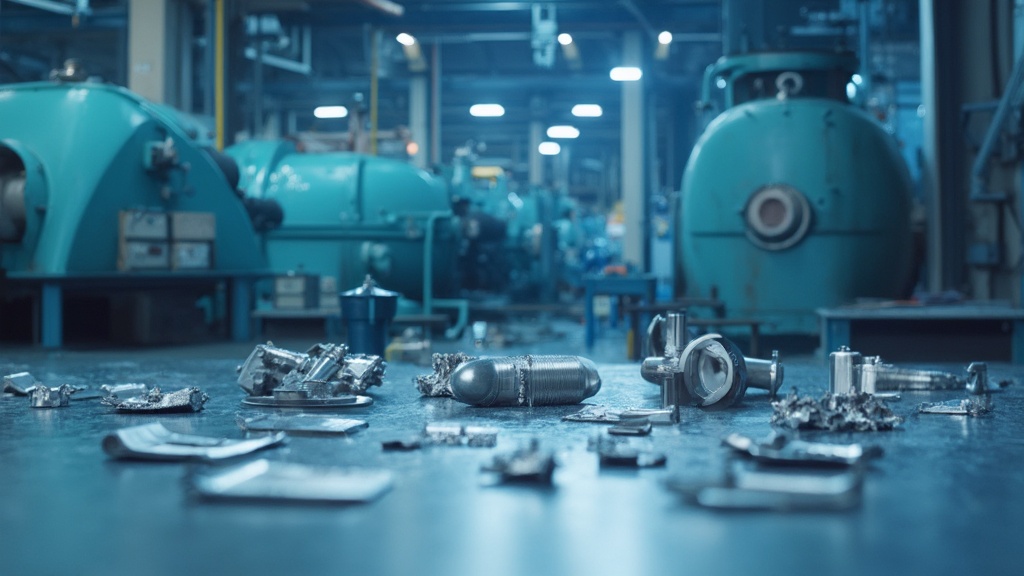
Understanding the Composition of Hastelloy Alloys in Industry
Introduction
In the world of high-performance materials, Hastelloy alloys stand out as a benchmark for exceptional durability and resilience. Widely recognized for their unparalleled resistance to corrosion and stability under extreme temperatures, these alloys have become indispensable in demanding industrial environments. Comprised primarily of nickel, molybdenum, and chromium, each element contributes uniquely to the alloy’s superior performance.
Nickel enhances ductility and oxidation resistance, molybdenum fortifies against pitting and crevice corrosion, and chromium boosts overall strength and corrosion resistance at elevated temperatures. This article delves into the critical components and roles of these elements in Hastelloy alloys, explores the various types and their specific industrial applications, and highlights the numerous benefits of using these advanced materials in sectors ranging from aerospace to chemical processing.
Key Components of Hastelloy Alloys
Hastelloy materials are renowned for their exceptional durability against rust and stability at elevated temperatures, rendering them essential in demanding industrial settings. These alloys are primarily composed of nickel, molybdenum, and chromium, each contributing distinct attributes to their overall performance. ‘Nickel, the base metal, imparts ductility and protection against oxidation, which are crucial in maintaining structural integrity under extreme conditions.’. Molybdenum greatly improves durability against pitting and crevice degradation, an essential aspect in uses involving aggressive chemicals. Chromium, conversely, improves overall decay prevention and enhances strength at high temperatures.
The elevated resistance to corrosion of these materials is similar to that of austenitic stainless steel, which comprises 16 to 26 percent chromium and up to 35 percent nickel. This composition enables the material to endure harsh conditions, similar to Multi-principal element materials (MPEMs) which are recognized for their high strength, hardness, and toughness across a range of temperatures.
Recent advancements in materials science, such as the development of stainless steel for hydrogen applications by Professor Mingxin Huang’s team, highlight ongoing innovations in metal technology. This new stainless steel, intended for application in green hydrogen production, demonstrates high corrosion resistance, highlighting the potential for alternative materials to be adapted for future sustainable solutions.
Furthermore, the importance of these materials in the worldwide market is highlighted by the growing recognition and application of advanced stainless steels in multiple industrial sectors. The accelerated production and utilization of these materials in North America, driven by their advantages in automotive, construction, electronics, and renewable industries, reflect a growing trend. Key industry participants are concentrating on collaborations and advancements to sustain a competitive advantage, further driving the use of high-performance materials in various applications.
Role of Nickel in Hastelloy Alloys
Nickel dominates the composition of most Hastelloy mixtures, typically making up over 50% of their structure. Its main purpose is to offer excellent durability against rust and mechanical characteristics, including toughness and ductility, which are crucial in challenging settings. Nickel encourages the development of a protective oxide layer on the metal surface, enhancing durability. This is particularly beneficial in applications like chemical processing, aerospace, and energy production. For example, in nuclear power facilities, nickel alloys are employed in thermal transfer and cooling systems, as well as in containers for radioactive waste, because of their ability to withstand heat and deterioration. The growing demand for nickel in aerospace, driven by increasing aircraft orders, is impacting supply and prices, which could affect other sectors relying on nickel for new energy infrastructure projects.
Role of Molybdenum in Hastelloy Alloys
Molybdenum is an essential alloying component in this particular alloy, greatly improving its resistance to localized corrosion, particularly in reducing environments. This element enables the alloy to withstand chlorides and other harsh substances, rendering it extremely appropriate for sectors such as oil and gas extraction and chemical processing. Depending on the specific grade, the molybdenum content in Hastelloy materials can vary from 5% to 30%. Research has indicated that molybdenum’s presence in the mixture composition is essential in creating a strong passive layer on the material’s surface, safeguarding it from corrosive assaults. Electrochemical studies and mass loss tests affirm that the inclusion of molybdenum substantially decreases the corrosion rate, reinforcing the material’s durability and effectiveness in harsh conditions.
Types of Hastelloy Alloys
Certain alloys are categorized into distinct families, each tailored for specific applications based on their unique composition and properties. The B family of alloys performs well in settings with hydrochloric acid, offering outstanding durability and dependability. The C family of alloys is distinguished by its adaptability, providing strong durability against a broad range of corrosive substances, which makes it a favored option in multiple sectors. Meanwhile, the G family is particularly noted for its excellent resistance to sulfuric acid, ensuring durability and performance in harsh environments. These characteristics make each alloy type indispensable for targeted industrial applications, ensuring optimal performance and longevity.
Applications of Hastelloy Alloys in Industry
Certain alloys are renowned for their exceptional performance in extreme environments, making them indispensable across various industries. In the chemical processing sector, they are crucial for reactors and heat exchangers due to their ability to withstand corrosive substances and high temperatures. The aerospace sector utilizes a high-performance alloy for essential parts subjected to extreme thermal and mechanical pressure. Nuclear reactors also benefit from the material’s robustness in maintaining structural integrity under radioactive exposure and high-pressure conditions. Additionally, waste processing facilities depend on a durable alloy to handle harsh chemical waste without degradation. The exceptional durability of these materials in challenging environments highlights their essential contribution to enhancing industrial capabilities.
Benefits of Using Hastelloy Alloys
Specialized metal mixtures provide many benefits that go far beyond their famous resistance to corrosion. Their high strength at elevated temperatures makes them ideal for demanding applications across various industries, such as aerospace, manufacturing, and hi-tech sectors. For example, Sandvik Mining and Rock Solutions have effectively integrated a high-performance alloy in their equipment, enhancing productivity and safety while minimizing downtime and maintenance expenses. Furthermore, the resilience of these metal mixtures greatly reduces upkeep costs, thereby enhancing operational effectiveness.
The long-term performance of this alloy often justifies its higher initial cost, as it provides reliable solutions in challenging environments. Morgan Advanced Materials demonstrates this by utilizing sophisticated metal mixtures to enhance efficiency and reduce carbon emissions in their operations. As sectors persist in functioning under severe circumstances, the requirement for substances that retain their durability and efficiency becomes progressively essential. This reliability and performance in harsh conditions are what make Hastelloy alloys a valuable investment for businesses aiming to enhance their operational efficiencies and meet stringent service requirements.
Conclusion
Hastelloy alloys represent a pinnacle in high-performance materials, distinguished by their exceptional resistance to corrosion and stability under extreme conditions. The unique composition of these alloys, primarily featuring nickel, molybdenum, and chromium, contributes to their remarkable durability and mechanical properties. Nickel enhances ductility and oxidation resistance, while molybdenum provides critical protection against localized corrosion in harsh environments.
Chromium further strengthens the alloy’s overall resilience, particularly at elevated temperatures.
The various families of Hastelloy alloys, each tailored for specific industrial applications, underline their versatility and indispensable role in sectors such as chemical processing, aerospace, and nuclear energy. From reactors and heat exchangers to critical aerospace components, the application of Hastelloy alloys ensures not only performance but also longevity in demanding environments. Their ability to withstand corrosive substances and high temperatures positions them as a strategic choice for industries aiming to enhance operational efficiencies.
Moreover, the benefits of using Hastelloy alloys extend beyond corrosion resistance and strength. Their durability translates into reduced maintenance costs and improved operational efficiency, making them a valuable investment. As industries continue to face increasing challenges related to extreme conditions and sustainability, the reliance on advanced materials like Hastelloy will only grow.
The strategic adoption of these alloys can provide companies with a competitive edge, ensuring they meet stringent service requirements while optimizing productivity.