Blogs
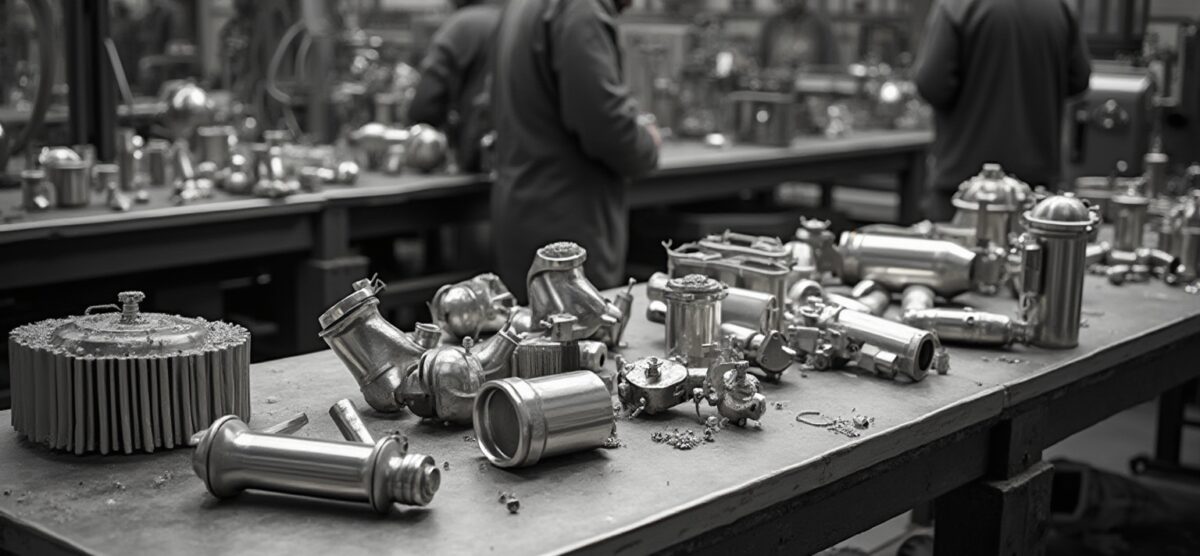
What Are Nickel Alloys Applications? A Comprehensive Overview
Overview
Nickel alloys are widely applied across various industries, including aerospace, marine, chemical processing, and electronics, due to their exceptional properties like corrosion resistance, high-temperature stability, and ease of fabrication. The article highlights key advancements, such as the introduction of Sanicro 625 in aerospace and Monel 400 in marine applications, underscoring the materials’ significance in enhancing operational efficiency and safety in demanding environments.
Introduction
Nickel alloys have emerged as indispensable materials across various industries, renowned for their unique properties and outstanding performance. From the aerospace sector, where they withstand extreme temperatures in jet engines, to the marine industry, where their corrosion resistance is vital for shipbuilding, the applications of these alloys are both diverse and critical.
As industries evolve and innovate, the demand for nickel alloys continues to surge, driven by their ability to meet stringent operational demands in challenging environments. This article delves into the multifaceted roles of nickel alloys in sectors such as aerospace, marine, chemical processing, and electronics, exploring their key properties and the future trends that will shape their applications in a rapidly changing industrial landscape.
Diverse Applications of Nickel Alloys in Industry
The applications of nickel alloys are integral to numerous industries, celebrated for their distinctive properties and outstanding performance capabilities. In the aerospace sector, these materials are essential in the construction of turbine engines and combustion chambers, where the ability to resist high temperatures and maintain structural integrity is crucial. A notable advancement in this area was the introduction of the Sanicro 625 bar (UNS 06625) by Sandvik in April 2022, which can endure temperatures as high as 593°C (1100°F), enhancing the reliability of aerospace components.
The marine sector similarly utilizes the benefits of metal mixtures, especially in ship construction, where parts must demonstrate outstanding corrosion resistance to endure the severe conditions of seawater. In chemical processing, these materials are preferred for constructing reactors and heat exchangers due to their ability to endure aggressive chemicals, ensuring safety and longevity in operations. Furthermore, in the field of electronics, nickel-based materials play a crucial role in producing connectors and battery parts, highlighting their adaptability.
As industries keep advancing, the uses of metal mixtures derived from nickel are growing, especially with the recent creation of a new supermaterial for additive production by Aubert & Duval and Alloyed in July 2024. This trend emphasizes the continuous development of nickel alloys applications to address the varied requirements of industries like aerospace, marine, chemical, and electronics, underscoring their significance in modern industrial practices. As mentioned by Haynes International, Inc., “We are acknowledged for our proficiency in high-performance metal mixtures, which we utilize to satisfy the particular needs of essential sectors, thus aiding in the advancement of the industry.”
Key participants in the base metal market, including HAYNES INTERNATIONAL, Sandvik AB, and Berkshire Hathaway Inc., persist in promoting innovation and quality in this area. Furthermore, a Global Consulting Firm deemed the accurate information in Persistence Market Research’s reports essential, resulting in substantial strategic choices based on the examination of metal mixtures.
Key Properties of Nickel Alloys That Drive Their Applications
Copper-based materials are characterized by various key attributes that render them suitable for high-performance uses, especially in nickel alloys applications. One of the most paramount attributes is corrosion resistance, which is notably superior in marine environments compared to stainless steel, allowing these materials to endure harsh conditions commonly encountered in marine and chemical processing sectors. For example, copper and other metal combinations are particularly acknowledged for their outstanding resistance to corrosion, making them the favored option for uses in seawater settings, such as shipbuilding and offshore structures.
Furthermore, they exhibit excellent thermal and electrical conductivity, which is crucial for electrical uses, including heat exchangers and electrical connectors, as well as good ductility, facilitating the creation of complex shapes without the risk of cracking—an essential factor in the design of intricate components utilized in electronics and automotive sectors. Their ease of fabrication adds to their appeal, enabling efficient production processes. Furthermore, the antimicrobial characteristics of copper metal mixtures render them appropriate for uses where cleanliness is crucial, such as in medical instruments and food preparation.
Collectively, these properties not only enhance the performance and reliability of the final products but also significantly contribute to the longevity of the equipment in which they are integrated. As the worldwide sector for nickel alloys applications is anticipated to expand from USD 15.02 billion in 2023 to around USD 25.99 billion by 2034, fueled by rising demand from different industries, the importance of these essential characteristics becomes more evident. Significantly, the automotive sector prevailed in the industry of nickel alloys applications in 2023, emphasizing the essential function these substances serve in contemporary vehicle production.
Key participants in the composites sector, such as AMETEK, Inc., Polymet, NIPPON STEEL CORPORATION, and ThyssenKrupp AG, are essential in promoting these high-performance substances. As highlighted by Haynes International, Inc., ‘Haynes International, Inc. is acknowledged for its proficiency in high-performance metal mixtures, which it employs to fulfill the particular needs of essential industries and thus aid in the advancement of the market.’ This highlights the increasing significance and usage of metal mixtures across diverse high-demand sectors, especially in improving product performance and tackling industry challenges.
Nickel Alloys in Aerospace Applications
In the aerospace industry, metal mixtures are crucial because of their outstanding performance in extreme conditions. Notably, Inconel 718 is widely utilized in jet engines and gas turbines, where its ability to endure high temperatures and pressures is critical. The mixture’s capacity to retain mechanical integrity at elevated temperatures directly influences flight safety and operational efficiency.
Beyond jet engines, the applications of nickel alloys include various structural uses, such as fasteners and landing gear, where their superior strength-to-weight ratio offers significant advantages. Key participants in the nickel-based material market, including Precision Castparts Corp. and ThyssenKrupp AG, play an essential role in the supply chain, ensuring the availability of high-quality resources for aerospace uses. Moreover, the rigorous testing protocols and compliance with international standards additionally affirm the dependability and strength of these materials, reinforcing their role as a fundamental component in aerospace engineering.
As per the Nickel Institute, stainless steel by itself represents more than two-thirds of worldwide consumption of this metal, emphasizing the relative importance of nickel-based materials in aerospace uses. As the sector progresses, the incorporation of nickel alloys applications in advanced aerospace uses continues to develop, propelled by persistent innovations and market needs. Additionally, the rising global demand for renewable energy is increasing the use of nickel alloys applications in components such as turbine blades and battery materials for energy storage, underscoring their relevance in contemporary aerospace engineering.
Nickel Alloys in Marine Environments
Marine environments present significant challenges to materials, characterized by corrosive saltwater and fluctuating temperatures. In this context, the choice of appropriate materials is paramount. In shipbuilding and offshore structures, nickel alloys applications, particularly Monel 400, are favored due to their exceptional resistance to seawater corrosion.
Monel 400’s properties include a high modulus of impedance, with values reaching a maximum of 6619 Ω·cm² after 672 hours of immersion, emphasizing its durability under extreme conditions. These materials are also essential to the production of critical components such as:
- Pumps
- Valves
- Heat exchangers
where their longevity contributes to reduced maintenance costs and enhanced operational efficiency. Additionally, recent research shows that metal mixtures display exceptional biofouling and erosion resistance, which is crucial for maintaining the integrity of marine vessels and equipment.
Significantly, research from the Center for Advancing Materials Performance from the Nanoscale (CAMP-Nano) highlights the corrosion resistance of these materials in seawater, offering procurement managers valuable insights for strategic sourcing decisions in shipbuilding. Furthermore, a case study titled “O Spectrum Analysis of C71500 Metal” examined the corrosion products of metal mixtures over time, uncovering substantial insights into their oxidation states and corrosion behavior. As noted by Ming Liu, this research emphasizes the importance of understanding these materials’ performance in challenging environments.
Moreover, the use of antifouling subsea markers composed of copper-nickel emphasizes the practical nickel alloys applications in marine environments, further illustrating their significance. As the market demand for Monel 400 keeps growing in 2024, understanding its performance in nickel alloys applications, particularly for marine uses, becomes increasingly vital.
Nickel Alloys in Chemical Processing
Nickel alloys applications play a pivotal role in the chemical processing industry, particularly in scenarios requiring materials that can withstand corrosive chemicals and high-pressure environments. Among these, Hastelloy C-276 stands out due to its remarkable resistance to a broad spectrum of corrosive agents, including various acids and chlorides. This metal is highly favored for critical components such as:
- Reactors
- Heat exchangers
- Piping systems
The durability and dependability of these metal mixtures not only improve operational efficiency but also greatly reduce the risk of leaks and failures, ultimately promoting a safer working environment. Recent insights suggest that corrosion-resistant metals are the predominant class in nickel alloys applications, according to Cognitive Market Research, reflecting the increasing demand for substances that adhere to strict industry standards and regulations in chemical processing operations. Moreover, North America accounted for around 40% of the global revenue in 2024, underscoring the regional significance of this market.
As the worldwide emphasis turns towards sustainable energy, the utilization of metal mixtures is anticipated to grow, especially in energy storage systems and hydrogen infrastructure, as demonstrated by the case study titled ‘Demand for Renewable Energy Continues to Increase.’ This emphasizes the essential function of metal mixtures in future developments. The market dynamics, influenced by price volatility and demand fluctuations in major regions like China and Indonesia, highlight the necessity for procurement managers to stay informed about these trends to make strategic sourcing decisions.
Future Trends in Nickel Alloy Applications
The future of nickel-based materials is poised for significant growth, fueled by sectors increasingly emphasizing substances that provide improved performance and sustainability. Innovations in metal compositions and advanced processing techniques are projected to significantly improve key properties, including strength, corrosion resistance, and weight reduction. Significantly, the corrosion-resistant category has risen as a frontrunner in the nickel-based materials sector, illustrated by its prominent function in marine uses like pumps and valves, as shown in the case study emphasizing its expansion due to the demand for high corrosion resistance in severe conditions.
Furthermore, the market is expected to grow at a CAGR of 5.11% from 2024 to 2034, reflecting the rising global demand for renewable energy technologies. As the worldwide drive for renewable energy technologies accelerates, the need for metal mixtures in components, including turbines and energy storage systems, is anticipated to increase. Aditi Shivarkar, an expert in the field, underscores the importance of these developments:
She is not just an expert—she’s the linchpin that ensures the accuracy, relevance, and clarity of the insights we deliver.
As industries strive for greater efficiency and environmental responsibility, the versatility and adaptability of nickel alloys applications will be crucial in meeting these evolving demands, thus positioning them as integral to future innovations.
Conclusion
Nickel alloys are proving to be fundamental materials across a variety of industries, thanks to their exceptional properties and reliability. From aerospace to marine, chemical processing, and electronics, these alloys are uniquely equipped to meet the demanding challenges presented by each sector. Their corrosion resistance, thermal stability, and ease of fabrication make them indispensable for applications that require both performance and safety.
The advancements in nickel alloy technology, highlighted by innovations such as the Sanicro 625 and Hastelloy C-276, underscore the ongoing evolution of these materials. As industries increasingly adopt nickel alloys to enhance product reliability and operational efficiency, the market is expected to witness significant growth. This trend is particularly evident in the aerospace and renewable energy sectors, where the demand for high-performance materials is rapidly increasing.
As the landscape of industrial applications continues to shift, the strategic importance of nickel alloys becomes even more pronounced. Procurement managers must remain vigilant in tracking these developments to leverage the benefits of nickel alloys effectively. By understanding their unique properties and applications, stakeholders can make informed decisions that will not only enhance operational efficiency but also ensure long-term sustainability in their respective industries.