Blogs
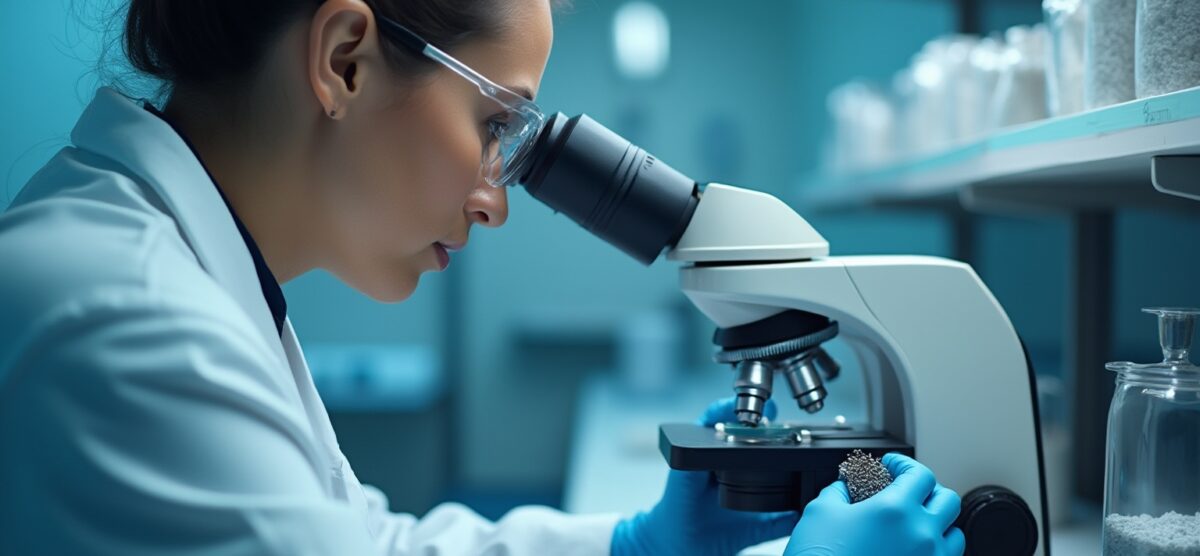
How to Use Permalloy 80 for Effective Cryogenic Shields: A Step-by-Step Guide
Overview
The article provides a comprehensive step-by-step guide on effectively using Permalloy 80 for cryogenic shields, emphasizing its unique properties and applications in low-temperature environments. The guide outlines essential steps such as identifying requirements, engaging reputable suppliers, material preparation, design, implementation, and maintenance, while highlighting the importance of the alloy’s magnetic properties and its role in enhancing the performance of superconducting magnets and particle accelerators.
Introduction
In the realm of cryogenic applications, the choice of materials can significantly impact performance and efficiency. Permalloy 80, with its unique composition of 80% nickel and 20% iron, stands out for its exceptional magnetic properties, making it a preferred option for shielding sensitive components in environments where precision is paramount.
This article delves into the composition, properties, and multifaceted applications of Permalloy 80, particularly in superconducting magnets and particle accelerators, while also offering a comprehensive guide for procurement managers on implementing this alloy effectively.
As advancements in materials science continue to evolve, understanding the nuances of Permalloy 80 will empower decision-makers to optimize their sourcing strategies and enhance system reliability in high-stakes cryogenic settings.
Understanding Permalloy 80: Composition and Key Properties
Alloy 80 is a highly specialized mixture, consisting of 80% nickel and 20% iron, noted for its exceptional magnetic properties, which make permalloy 80 for cryogenic shields ideal for low-temperature shielding applications. Its high magnetic permeability enables effective channeling of magnetic fields, thereby optimizing performance in environments that require precise magnetic control. Furthermore, the alloy 80 possesses low coercivity, allowing it to be easily magnetized and demagnetized.
This quality is crucial in minimizing energy losses within cryogenic systems that incorporate permalloy 80 for cryogenic shields, ensuring operational efficiency. Recent advancements indicate that the flux density for Square Alloy 80 ranges from 0.66 to 0.82 Tesla, confirming its effectiveness in challenging uses. The coating color of Square 80 is red, which is an important detail for identification and specifications.
Furthermore, Round Alloy 80 acts as a practical illustration of the material’s capabilities; it is a non-oriented 80% nickel-iron alloy that has been processed to achieve high initial permeability and low coercive force, making it especially efficient in uses with extremely low signals and minimal losses, ensuring high accuracy in current transformers.
For procurement managers and engineers, a thorough understanding of these properties, including the minimum for part number 806191R080000 being 800, is vital for making informed decisions regarding substance selection for low-temperature environments, ultimately leading to enhanced system reliability and performance.
Applications of Permalloy 80 in Cryogenic Shielding
Permalloy 80 for cryogenic shields has established itself as a cornerstone material in cryogenic applications, particularly within the realms of superconducting magnets and particle accelerators. In superconducting magnets, it plays a crucial role in shielding sensitive components from external magnetic fields, which are known to disrupt performance and contribute to energy losses. The saturation magnetization of composites comprising 80 wt% of a specific alloy has been reported to reach 50.9 emu/g, making it exceptionally effective in these demanding environments.
Furthermore, in particle accelerators, Permalloy 80 is utilized to mitigate magnetic interference, thereby ensuring precise control over particle beams. As mentioned by Jeffrey Ambs, “The 5014iQ and 5030iQ monitors from Thermo Fisher provide precise particulate measurements, improving air quality management in urban and industrial environments,” which emphasizes the significance of sustaining optimal environmental conditions in low-temperature processes. The strategic use of permalloy 80 for cryogenic shields not only enhances the operational efficiency of particle accelerators but also underscores its status as a premier choice for cooling shielding solutions.
Furthermore, findings from recent research on magnetoresistance emphasize that phase-based transducers can greatly enhance sensitivity in contexts related to a specific alloy, rendering them appropriate for miniaturization. As progress in low-temperature technologies continues to evolve, the application of permalloy 80 for cryogenic shields remains crucial in ensuring optimal performance and reliability in high-stakes scenarios.
Step-by-Step Guide to Implementing Permalloy 80 for Cryogenic Shields
- Identify Requirements: Begin by thoroughly assessing the specific cryogenic conditions and shielding requirements relevant to your use case. Key factors to evaluate include the operational temperature range, magnetic field strength, and the physical dimensions of the components that need protection. Given the essential role of substances in high-temperature environments, consider using Mica Insulation Tape for its exceptional thermal and electrical insulation properties, ensuring reliability in diverse applications. It’s crucial to consider the sustainability of your resources, especially since five elements, including hafnium and neodymium, have a high alloy use (over 70%) but low functional recycling (under 30%). Emphasizing the importance of selecting suppliers who provide certifications that meet international standards can further enhance the reliability of your sourcing decisions.
- Engage with reputable suppliers specializing in high-performance metals, including Permalloy 80 for cryogenic shields and Mica products that enhance electrical insulation. Ensure these suppliers can provide the necessary certifications that meet international standards. It’s essential to verify that they have a proven track record in delivering quality resources suitable for permalloy 80 for cryogenic shields. As highlighted by T. E. Graedel, “it is crucial to acknowledge that, in general, the minor alloying elements are not extracted for their own sake,” which emphasizes the significance of obtaining resources that align with both performance and sustainability.
- Material Preparation: After obtaining the alloy 80, prepare the material by cutting it to the specified dimensions required for your shielding design. Additionally, consider the use of Mica Sheet Tape for insulating large flat surfaces, which can complement your shielding strategy. Ensure that all surfaces are meticulously cleaned to eliminate any contaminants, as this is vital for maintaining the alloy’s performance under low-temperature conditions.
- Shield Design: Carefully design the layout of the cryogenic shield with particular attention to the positioning of permalloy 80 for cryogenic shields. The shield should effectively encompass sensitive components while minimizing any gaps that could permit magnetic interference, ensuring optimal protection. Incorporating Mica Tape products can enhance the shield’s effectiveness by providing reliable insulation against electrical hazards. Each type of Mica Tape offers specific benefits, such as flame resistance and dielectric strength, which are crucial for ensuring safety in electrical applications.
- Implementation: Proceed with the installation of the permalloy 80 for cryogenic shields, ensuring that it is securely mounted and properly aligned to the designated specifications. Conduct thorough tests to verify the effectiveness of the shielding under operational conditions, confirming its ability to perform as intended.
- Monitoring and Maintenance: Establish a routine for observing the performance of the cooling shield, coupled with a maintenance plan to address any necessary upkeep. Regular assessments are essential to ensure the ongoing effectiveness of the shield in protecting critical components from magnetic interference.
Case Study Reference: Consider looking into Sekonic Metals Technology Co., Ltd., established in 1996, which specializes in anti-corrosion and high-temperature alloys for industrial applications. Their knowledge in creating high-performance alloys, along with Mica Tape products, can be a valuable asset when procuring resources for your shielding requirements. Emphasizing the sustainability of your selections, particularly regarding the recycling rates of critical elements, can further enhance the overall efficiency and environmental impact of your project.
Challenges and Considerations in Using Permalloy 80 for Cryogenic Applications
Employing alloy 80 for low-temperature shielding presents several distinct challenges that procurement managers must navigate:
- Temperature Effects: The magnetic properties of alloy 80 can significantly change at low temperatures. Research indicates that remanence can increase by 8.93% at 140 °C compared to room temperature (25 °C). This variation requires thorough verification of the magnetic properties of permalloy 80 for cryogenic shields to ensure consistent performance in low-temperature applications. Furthermore, the reinforcement and hardening characteristics of the alloy in low-temperature conditions are associated with microstructure evolution during deformation, which is essential for comprehending its performance.
- Substance Handling: Proper handling and installation of the alloy 80 are crucial to prevent damage and maintain integrity. Educating your team in specialized best practices is crucial to alleviate any potential problems during installation, especially when operating in extremely low temperature environments. As Waeckerlé Demier Godard Fraisse notes, certain alloy grades, such as permalloy 80 for cryogenic shields, exhibit remarkable magnetic properties across a wide temperature range, which can be harnessed effectively if handled correctly.
- Real-World Applications: Insights from case studies, such as the research on tensile properties and a modified s-Johnson-Cook model for AA7075 sheets at extremely low temperatures, illustrate the challenges faced with materials in such environments. These examples can offer valuable context for understanding the performance of this alloy 80 under similar conditions.
- Cost Management: While the high-performance attributes of this alloy 80 come at a premium, it is imperative for procurement managers to conduct a comprehensive cost analysis. This should encompass the total lifecycle costs, including sourcing, installation, and ongoing maintenance. By adopting a strategic approach to budget allocation, organizations can optimize their expenses while utilizing permalloy 80 for cryogenic shields in low-temperature applications. The credibility of these findings is further supported by the research funded by the National Natural Science Foundation of China, emphasizing the relevance of ongoing inquiries into the properties.
Future Trends in Cryogenic Shielding with Permalloy 80
The future of cryogenic shielding is set to be revolutionized by permalloy 80 for cryogenic shields, driven by advancements in materials science and engineering. Ongoing research aims to enhance the magnetic properties of an alloy 80, with the potential for [maximum permeability](https://espimetals.com/index.php/technical-data/175-Permalloy 80) reaching up to 300,000. Such improvements could lead to greater efficiency in shielding uses, particularly in demanding environments like photon energy and linac machines, with the application of permalloy 80 for cryogenic shields.
Furthermore, the integration of smart technologies into low-temperature systems is likely to inspire new designs that capitalize on the unique characteristics of permalloy 80 for cryogenic shields. With the oxygen content in electron beam additive manufactured specimens being remarkably low at just 0.0042%, the integrity remains robust, further solidifying its role in future applications. For procurement managers, staying informed about these evolving trends is essential to maintain a competitive edge in the dynamic landscape of refrigeration shielding technologies.
A recent publication in Additive Manufacturing highlights the significance of emerging materials, such as the Co47.5Fe28.5Ni19Si3.4Al1.6 high-entropy alloy, which reflects the ongoing evolution of microstructures and properties relevant to the field. As Binggang Zhang notes, ‘The advancements in high-entropy alloys are paving the way for innovative applications in cryogenic environments.’ Engaging with these innovations will be critical for strategic decision-making in procurement.
Conclusion
In summary, Permalloy 80 emerges as a vital material in the realm of cryogenic applications, distinguished by its unique composition and outstanding magnetic properties. Its high magnetic permeability and low coercivity make it particularly effective for shielding sensitive components in superconducting magnets and particle accelerators, ensuring optimal performance in environments where precision is critical. The detailed exploration of its properties, applications, and implementation strategies underscores the significance of understanding Permalloy 80 for procurement managers aiming to enhance system reliability and operational efficiency.
As advancements in materials science continue to evolve, the potential for Permalloy 80 is further expanded by emerging trends and technologies. Future innovations may lead to enhanced magnetic characteristics, thereby improving the effectiveness of cryogenic shielding solutions. Staying informed about these developments is essential for procurement professionals, enabling them to make strategic decisions that align with the latest advancements in the field.
Ultimately, the strategic application of Permalloy 80 not only addresses the challenges associated with cryogenic environments but also positions organizations to leverage its capabilities for future growth. By prioritizing informed sourcing and implementation practices, decision-makers can ensure that their systems remain at the forefront of technological advancements, securing a competitive edge in the dynamic landscape of cryogenic applications.