Blog
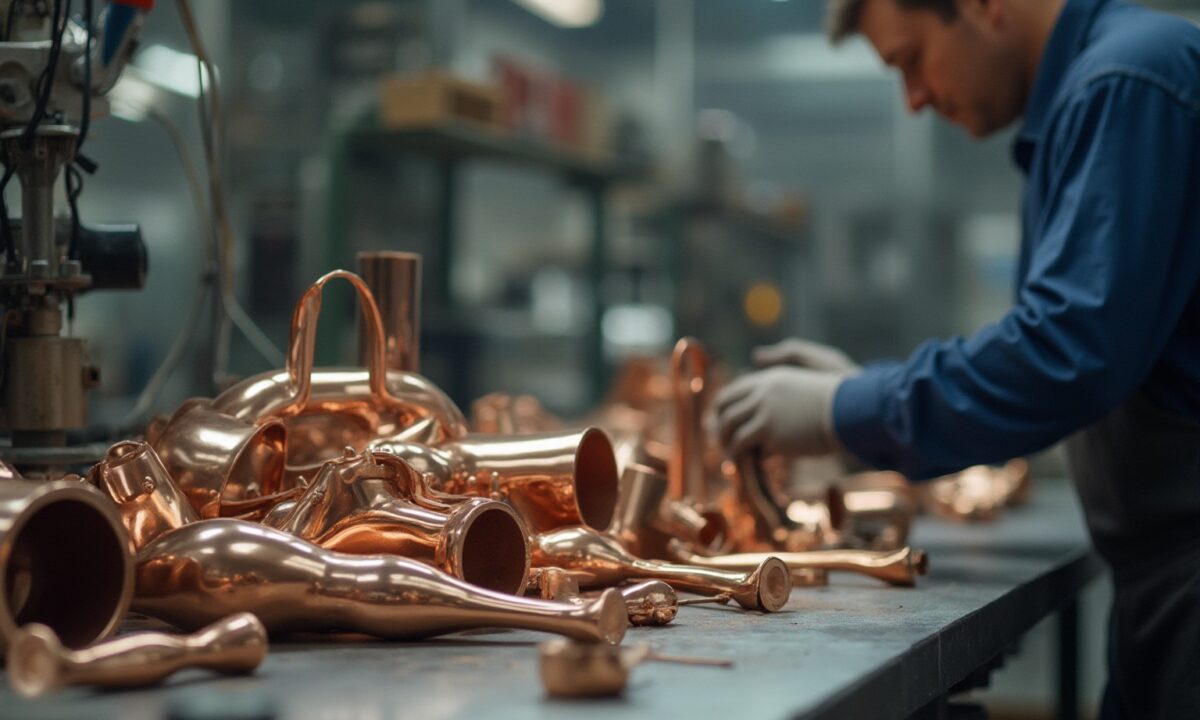
Understanding Non-Sparking Properties of Beryllium Copper: A Complete Tutorial for Bearings in Low Wear & Tear Applications
Overview
The article focuses on the significance of beryllium copper’s non-sparking properties for bearings in low wear and tear applications, particularly in environments where safety from ignition is critical. It supports this focus by detailing how these properties enhance operational safety in explosive settings, backed by industry standards, case studies, and the alloy’s exceptional mechanical characteristics, which make it a preferred choice for various industrial applications.
Introduction
In the realm of industrial materials, beryllium copper stands out not only for its remarkable strength and electrical conductivity but also for its critical non-sparking properties. This unique alloy has become a cornerstone in environments where safety is paramount, such as oil rigs and chemical plants, where the risk of ignition can have catastrophic consequences.
As procurement managers navigate the complexities of sourcing materials, understanding the multifaceted applications and benefits of beryllium copper is essential. From its superior performance in low wear and tear environments to its compliance with stringent safety standards, this material is poised to meet the demands of various high-stakes industries.
With an eye on future trends and innovations, the strategic selection of beryllium copper can significantly enhance operational safety and efficiency, making it a vital consideration for any procurement strategy.
Exploring the Non-Sparking Properties of Beryllium Copper
The alloy is renowned for its remarkable strength and electrical conductivity, and its non-sparking property of beryllium copper for bearings in low wear & tear applications makes it an essential material in settings where combustible gases or vapors exist, such as oil rigs and chemical facilities. The significance of the non-sparking property of beryllium copper for bearings in low wear & tear applications cannot be overstated; it plays a critical role in preventing accidental ignitions during operations. The non-sparking property of beryllium copper for bearings in low wear & tear applications is engineered to prevent sparks when subjected to friction or impact, making it the preferred choice for tools and components used in sensitive applications.
A spokesperson from an international consulting firm stated, ‘Our organization has been utilizing beryllium-bronze tools for some years now and we are very pleased with the quality and safety they offer in hazardous environments.’ Furthermore, case studies have demonstrated that the use of specific metal tools in chemical facilities has resulted in enhanced operational safety and fewer instances of ignition. Domadia is committed to supplying high-quality, tailored Copper Plates, ensuring that your projects gain from exceptional corrosion resistance and reliability in various environmental conditions.
Our expert support is available to help you choose the right specifications for your needs. This commitment to excellence reinforces the non-sparking property of beryllium copper for bearings in low wear & tear applications, establishing its reputation as a safe material for industrial use and ensuring operational integrity where safety is paramount.
Applications of Beryllium Copper in Low Wear & Tear Environments
Beryllium alloy is renowned for its exceptional performance in environments that demand low wear and tear, particularly because of the non-sparking property of beryllium copper for bearings in low wear & tear applications. This alloy, compliant with international standards such as UNS and ASTM, boasts impressive fatigue resistance and low thermal expansion, making it a prime choice for precision applications in both aerospace and automotive sectors. For example, a specific alloy can withstand high loads while maintaining dimensional stability, which greatly prolongs the lifespan of essential components such as bearings, particularly due to the non-sparking property of beryllium copper for bearings in low wear & tear applications.
This durability not only contributes to reduced maintenance costs but also enhances operational efficiency. The manufacturing and electronics sectors further leverage the non-sparking characteristics of this alloy, which are crucial for safety in connectors and switches, especially in explosion-risk settings. By utilizing beryllium copper from Domadia, organizations can achieve optimal performance while adhering to stringent safety standards.
Domadia’s dedication to high-quality Copper solutions through innovative manufacturing and stringent quality control reinforces its leadership in providing high-performance Copper Plates for industrial uses. Particular uses of Copper tools include their role in electrical connectors, precision instruments, and mold tooling, where the unique blend of strength, conductivity, and corrosion resistance is essential. As highlighted by recent market analysis, the copper alloy market was valued at approximately USD 1,825.48 million in 2024, underscoring its significance and growing demand across various high-stakes industries.
Additionally, procurement managers should consider pricing factors when evaluating copper solutions, especially in light of recent research exploring alternatives to harmful bronzes, such as the Cu–7.4Ni–1.3Si–1.2Cr alloy, which demonstrates high tensile strength and good thermal conductivity for mold tooling applications. Furthermore, it is essential to consider that beryllium may act as a hapten, triggering immune responses through interactions with proteins or peptides, a crucial consideration for procurement managers evaluating material safety.
Mechanical Properties of Beryllium Copper
Beryllium alloy is renowned for its exceptional mechanical properties, boasting a tensile strength that can reach up to 1,400 MPa and a shear modulus of 50.0 GPA. Combined with outstanding fatigue resistance and a hardness generally ranging from 40-45 HRC, this alloy stands out in contexts that require durability and resilience under stress. Notably, beryllium alloy maintains its mechanical integrity across a broad temperature spectrum, making it particularly advantageous in environments subject to thermal fluctuations.
The non-sparking property of beryllium copper for bearings in low wear & tear applications, along with its corrosion-resistant properties, enhances safety, especially in explosive environments, while its excellent thermal and electrical conductivity makes it ideal for electrical contacts. Recent studies highlight that these high conductivity alloys have thermal conductivity surpassing aluminum and marginally lower than pure metal, emphasizing their appropriateness for essential uses. As procurement managers navigate material selection, understanding these mechanical properties is crucial for ensuring optimal performance and longevity in various applications.
Furthermore, noted experts in the field, Matt Germscheid and John Hauck, have remarked on the transformative impact of new technologies in metallographic sample preparation, indicating a continuous evolution in the understanding of material properties. This insight is especially pertinent when examining the consequences of exposure to this element; however, alloys containing less than 2.5% of it are not categorized as carcinogenic, thereby supporting their safe application in different settings. At Domadia, we are dedicated to delivering premium alloy solutions, featuring a varied selection of products like foils, sheets, rods, and wires, in addition to custom fabrication options designed to meet your requirements.
Our exceptional customer service supports your project success, ensuring you have access to the best solutions available.
Cost Considerations in Sourcing Beryllium Copper
When obtaining the alloy, procurement managers must navigate various cost factors, including fluctuating raw material prices, processing expenses, and the reliability of suppliers. The cost of alloy scrap is affected by market demand, purity, and current metal prices. At Domadia, we are dedicated to providing fair and transparent pricing for all metal scrap transactions, ensuring competitive and appealing rates through robust supplier relationships and market trend insights.
The worldwide alloy market, valued at USD 1.51 billion in 2023 and expected to attain USD 2.53 billion by 2032, shows a compound annual growth rate (CAGR) of 6.1%, signifying strong demand fueled by the material’s exceptional physical characteristics. While beryllium bronze typically incurs higher costs than standard alloys due to its specialized manufacturing processes, this investment is often justified by its extended lifespan and lower maintenance requirements in critical applications, particularly due to the non-sparking property of beryllium copper for bearings in low wear & tear applications. The non-sparking property of beryllium copper for bearings in low wear & tear applications makes copper suitable for use in dangerous environments, minimizing the risk of ignition in flammable settings, which is essential for safety in sectors like oil and gas.
Furthermore, organizations should systematically evaluate multiple suppliers to ensure competitive pricing and uphold quality standards. Establishing long-term partnerships with dependable vendors can result in improved pricing structures and a consistent supply chain, ultimately enhancing the organization’s profitability. As mentioned by a Senior Analyst at Cognitive Market Research, ‘This will assist you in grasping the overall optimistic, pessimistic, and neutral effects of the coronavirus pandemic on the Copper market.’
Furthermore, the recent introduction of beryllium copper-based materials by Smiths Metal Centers for military uses has driven a 20% rise in demand, highlighting current market trends. It is also important to note that the Copper market is expected to witness significant growth, particularly in the Rod segment and the Plastic Molds & Tooling sector, providing further insights into the material’s diverse uses. Understanding these dynamics and the anticipated 10-15% cost increases due to regulatory measures will empower procurement managers to make informed decisions.
Compliance and Standards for Beryllium Copper
Beryllium copper tools, particularly those that leverage the non-sparking property of beryllium copper for bearings in low wear & tear applications, must comply with strict industry standards and regulations, including ASTM B194 and ISO 9001, ensuring that the materials used are of outstanding quality and suitable for hazardous uses. Non-sparking tools leverage the non-sparking property of beryllium copper for bearings in low wear & tear applications, making them the best alternative for non-sparking application purposes in explosive potential environments, as they mitigate ignition risks and provide a safe solution where flammable materials are present. Considering the potential health risks linked to exposure to this substance, organizations must stay alert about adherence to regulations governing its handling.
As Maureen Ruskin from the Occupational Safety and Health Administration (OSHA) states, ‘General information and technical inquiries should always prioritize compliance to safeguard worker health.’ This underscores the importance of these standards, as non-compliance can have significant health implications for workers. A pertinent case study on the dissolution and cytotoxicity of certain compounds highlights that the uptake and toxicity vary based on solubility, indicating that organizations must be aware of the health risks associated with different forms of this element.
Furthermore, OSHA concluded that the rule will not impose a federal mandate on the private sector in excess of $100 million in expenditures in any one year, providing context on the regulatory environment. Procurement managers play a pivotal role in this process by ensuring that suppliers not only meet these regulations but also possess relevant certifications that demonstrate adherence to both legal and industry standards. By prioritizing adherence and certification, procurement experts can protect safety and quality throughout production processes, ultimately reducing health risks linked to exposure and ensuring the efficient use of the non-sparking property of beryllium copper for bearings in low wear & tear applications in explosive environments.
Future Trends in the Use of Beryllium Copper
The forecast for this metal alloy is becoming more promising, especially as its uses in advanced technologies such as electric vehicles and renewable energy systems gain momentum. As industries seek materials that excel in performance while emphasizing safety, the non-sparking property of beryllium copper for bearings in low wear & tear applications positions this alloy as a crucial element for future innovations. Non-sparking tools made from this alloy demonstrate the non-sparking property of beryllium copper for bearings in low wear & tear applications, making them the best alternative for use in explosive environments while offering essential safety features such as spark resistance and reduced static electricity risks.
Ongoing research is focused on enhancing the alloy’s characteristics, which could lead to breakthroughs that further optimize performance and reduce production costs. With North America projected to capture a substantial 35.8% market share by 2024, procurement managers must remain vigilant about these evolving trends. This awareness will empower them to make well-informed, strategic decisions that align with the dynamic demands of the market and the rapid advancements in technology.
To ensure exceptional quality in sourcing alloy tools, procurement managers should:
- Organize significant events with a small group, promoting collaboration and transparent communication to balance individual sales targets with team goals.
- Understand real-world applications through case studies, such as effective management strategies that meet client expectations in repair jobs, which can provide valuable insights into the challenges faced in sourcing decisions.
For instance, a recent case study highlighted how a company successfully utilized the non-sparking property of beryllium copper for bearings in low wear & tear applications to mitigate risks during a critical repair operation in a high-stakes environment.
Conclusion
Beryllium copper emerges as a critical material across various high-stakes industries, underscoring its exceptional strength, electrical conductivity, and vital non-sparking properties. Its ability to prevent accidental ignitions in flammable environments, such as oil rigs and chemical plants, positions it as an indispensable asset for ensuring operational safety. The unique characteristics of this alloy not only enhance performance in low wear and tear applications but also comply with stringent industry standards, reinforcing its reputation as a reliable choice for procurement managers.
As the demand for beryllium copper continues to grow, understanding the mechanical properties, cost considerations, and compliance requirements is essential for making informed sourcing decisions. The potential for significant advancements in its applications, particularly in innovative technologies like electric vehicles and renewable energy systems, further highlights the strategic importance of this material. By staying abreast of market trends and evolving regulations, procurement professionals can optimize their strategies, ensuring that their selections align with both safety and operational efficiency.
In conclusion, the strategic selection of beryllium copper is not merely a matter of material choice but a pivotal decision that can drive safety and efficiency in industrial operations. By prioritizing this alloy, procurement managers can significantly enhance their organization’s resilience against operational risks, ultimately leading to improved outcomes in critical environments. Embracing the benefits of beryllium copper is a forward-thinking approach that promises to yield substantial dividends in safety and performance.