Blogs
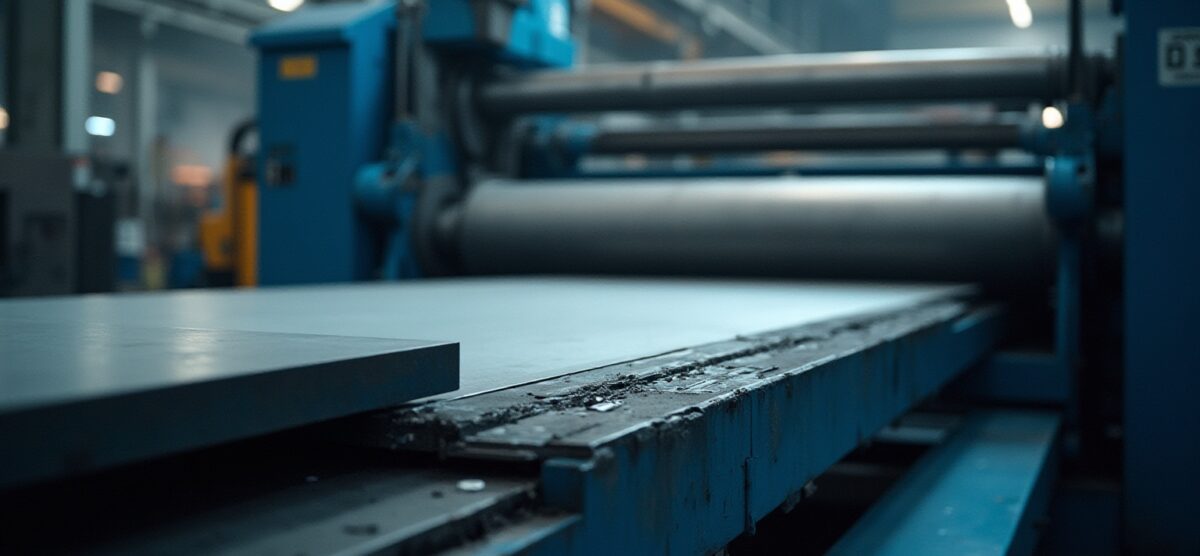
Understanding Types of Rolling: A Complete Tutorial for Manufacturers
Overview
The article titled “Understanding Types of Rolling: A Complete Tutorial for Manufacturers” focuses on the various types of rolling processes used in manufacturing metals, specifically distinguishing between hot, cold, and warm rolling methods. It explains that these processes are essential for optimizing material properties, production efficiency, and cost-effectiveness, supported by insights into the operational advantages and applications of different rolling mills and techniques in the industry.
Introduction
In the realm of manufacturing, the rolling process stands as a cornerstone technique, shaping metals into forms that meet the diverse needs of various industries. This method not only reduces the thickness of materials but also enhances their mechanical properties and surface finish, making it indispensable for producing sheets, plates, and structural components.
With the ongoing evolution of technology and fluctuating market demands, understanding the nuances of rolling—be it hot, cold, or warm—is crucial for procurement managers tasked with making informed sourcing decisions.
As the landscape shifts, innovations in rolling technology promise to improve efficiency and sustainability, while the strategic selection of rolling mills can significantly impact production outcomes.
This article delves into the intricacies of rolling in manufacturing, exploring its types, processes, and the benefits it brings to modern production environments.
Introduction to Rolling in Manufacturing
The process of passing metal through a pair of rolls is one of the types of rolling that is essential for forming metals, as it reduces thickness, enhances surface finish, and improves mechanical properties. This method is essential in the manufacturing of sheets, plates, and structural components, particularly for strips with a thickness of less than 6 mm and a width of less than 600 mm. The process of deformation is primarily classified into two types of rolling: hot and cold.
- Hot processing occurs above the material’s recrystallization temperature, enabling significant deformation and enhancing ductility. This process is particularly advantageous for producing large quantities of metal shapes efficiently.
- Cold processing is performed at room temperature, which not only enhances the surface finish but also improves dimensional accuracy.
As a result, cold processing is often the preferred choice for applications requiring tight tolerances and superior surface quality. According to industry insights, the total apparent steel use worldwide saw a slight decline from 1,779.3 million tons in 2019 to 1,763.0 million tons in 2023, reflecting shifting dynamics in metal demand and production methods. As noted by IBISWorld, ‘strong demand for precious metals enabled them to pass down cost increases to buyers, boosting revenue and supporting profitability.’
Grasping the differences and uses of these techniques is essential for procurement managers as they make informed choices regarding sourcing and optimization. Furthermore, insights from the ‘Machinery Leasing Global Market Report 2025’ emphasize the significance of machinery leasing in acquiring necessary equipment for processing activities, highlighting practical implications for procurement strategies.
Exploring the Four Main Types of Rolling Mills
Metal mills are fundamental in metal processing, and understanding the various types is crucial for procurement managers aiming to optimize production efficiency. The four primary types of mill processes are:
- Two-High Mill: This design incorporates two horizontal rolls and is widely utilized in different types of rolling, including both hot and cold processing. Its simplicity and efficiency make it an excellent choice for producing sheets and plates, catering to diverse industrial applications.
- Three-High Mill: This is one of the types of rolling mills, arranged vertically and consisting of three rolls that enable multiple passes of the substance. This configuration not only enhances productivity but also effectively reduces the thickness of the substance, making it a preferred option in high-volume operations.
- Four-High Mill: This is one of the types of rolling composed of four rolls, where two smaller rolls are positioned between two larger ones, and it excels at producing thin sheets with superior surface quality. Its design permits better control over the substance, ensuring high precision in production.
- Cluster Mill: Often referred to as a Sendzimir mill, this type is one of the various types of rolling that employs multiple rolls to achieve significant thickness reductions. It is especially beneficial for handling materials that require precise thickness regulation and superior finishes.
Chitranshi Jaiswal emphasizes the significance of quality in this field, stating,
NSSMC stands as a formidable entity in the Mill Machine Market, with a reputation established on providing exceptional product quality and technological leadership.
This insight underscores the competitive landscape where efficiency and innovation are paramount.
Moreover, the Nigeria Rolling Mill and Other Metalworking Machinery Market is projected to experience significant growth, with a focus on capacity segmentation and forecasts extending to 2034.
As the machinery leasing market develops, as outlined in the Machinery Leasing Global Market Report 2025, understanding the specifications and uses of these mills becomes increasingly essential for strategic procurement decisions. Recent trends suggest that procurement managers must evaluate the efficiency comparisons between two-high and three-high mills, along with the specific applications that match their operational needs.
Understanding Different Rolling Processes in Manufacturing
Manufacturing utilizes different deformation techniques, each with unique advantages and applications:
Hot Deformation: This method involves shaping at elevated temperatures, allowing significant alteration without the risk of fracture. Commonly utilized for structural steel and heavy plates, it allows for the efficient production of components that can withstand significant stresses. In fact, the production of hot rolled steel products in the U.S. reached 56.4 million metric tons in 2009, reflecting its critical role in the industry.
Cold Rolling: Executed at room temperature, cold rolling enhances both surface finish and dimensional accuracy. The process is particularly valuable in automotive and appliance manufacturing, where precise specifications are crucial. Recent discussions in the industry highlight that cold working can significantly enhance the physical properties of substances, making them more suitable for demanding applications. This improvement is critical for procurement managers when selecting materials that must meet stringent performance standards. If cold rolled steel is not available, considering higher carbon alloys can be an effective alternative to maintain desired physical properties in finished products.
Warm Processing: Positioned between hot and cold processing, this method occurs at temperatures lower than those used in hot processing but higher than room temperature. It offers a favorable balance of ductility and strength, making it ideal for specialized applications, as various types of rolling techniques have distinct implications for the mechanical properties of the finished products. For instance, the limitations of hot rolled 1215 steel highlight the need for careful consideration of properties in procurement decisions, especially given that this steel may not respond effectively to heat treatment due to its low carbon content. Grasping these procedures is vital for making informed choices regarding material specifications and suitability for various manufacturing applications.
The Benefits and Applications of Rolling in Manufacturing
The process of deformation offers numerous benefits within the manufacturing sector, including:
- Enhanced Material Properties: This technique effectively improves the mechanical characteristics of metals, such as strength and ductility. For instance, research has shown that the AZ31 Mg alloy with a thickness of 1.6 mm exhibited a reduction in yield strength while demonstrating improved elongation with an increase in the number of passes. This demonstrates how controlled deformation, which combines heat treating and regulated shaping, can optimize material performance and enhance mechanical properties.
- Cost Efficiency: The procedure greatly aids in cost savings by optimizing production methods. By minimizing waste and reducing energy consumption, manufacturers can achieve lower operational costs. Recent updates in 2024 highlight that optimization strategies within the types of rolling process have resulted in heightened cost efficiency, reflecting the industry’s ongoing commitment to financial prudence.
- Versatility: The types of rolling are adaptable to a wide variety of substances, ranging from aluminum to various steel grades, thus providing a flexible manufacturing solution. It produces a variety of shaped products, including angles, channels, beams, and hexagons, which are essential in many industries. Its widespread applications include automotive components, structural materials, and consumer electronics, where quality and performance are critical. The significance of lubrication during hot processing further highlights the necessity for optimized strategies, as improper lubrication can lead to sheet adherence, negatively impacting product quality. A case study emphasizes that inadequate lubrication at elevated temperatures can elevate the chances of sheet adherence, highlighting the crucial importance of control in achieving successful outcomes while maximizing formability.
Innovations in Rolling Technology for Modern Manufacturing
Recent advancements in information technology are transforming the landscape of the manufacturing sector, particularly within the cold mill market, which is crucial for the global steel industry. Key innovations include:
Automation and Smart Manufacturing: The integration of IoT technologies has revolutionized operations by enabling real-time monitoring and data analytics. This facilitates predictive maintenance, significantly enhancing operational efficiency. Erin Thompson, an industry expert, emphasizes this shift, stating, “Learn how automated solutions can enhance efficiency, reduce costs, and improve accuracy in warehouse operations.” By adopting these technologies, manufacturers streamline processes and mitigate the risk of costly downtime.
Advanced Materials: Ongoing development of new alloys and composites is pushing the boundaries of forming capabilities. These advancements result in the development of lighter and stronger substances suitable for a variety of applications, meeting the demands of modern manufacturing.
Eco-Friendly Practices: With the construction sector accountable for a staggering 37% of global emissions, innovations aimed at reducing the environmental footprint of processing methods are gaining momentum. Energy-efficient mills and sustainable sourcing of materials are becoming pivotal practices for manufacturers committed to eco-friendly operations. The cold rolling mill market is actively innovating with different types of rolling to meet these environmental challenges, reflecting a broader industry trend towards sustainability.
Furthermore, insights from the case study titled “Recent Trends in the Cold Rolling Mill Market” reveal that the market is dynamically adapting to these innovations, highlighting ongoing efforts to innovate and effectively meet the evolving demands of the steel industry.
Staying abreast of these developments is essential for manufacturers seeking to optimize their processes and maintain a competitive edge in a rapidly evolving market.
Conclusion
The rolling process in manufacturing is not just a fundamental technique; it is a driving force behind the production of high-quality metal products that meet industry standards. Understanding the various types of rolling—hot, cold, and warm—along with their unique applications, allows procurement managers to make informed decisions that directly affect production efficiency and product quality. Each rolling method offers distinct advantages, from the substantial deformation capabilities of hot rolling to the precision and surface finish achieved through cold rolling, highlighting the importance of selecting the right process for specific manufacturing needs.
Equally crucial is the knowledge of different rolling mills and their configurations. The choice between two-high, three-high, four-high, and cluster rolling mills can significantly impact output and operational efficiency. As industries evolve, staying updated on advancements in rolling technology—such as automation, innovative materials, and eco-friendly practices—will empower procurement managers to optimize sourcing strategies and enhance production capabilities.
In conclusion, the rolling process stands as a vital pillar in manufacturing, offering enhanced material properties, cost efficiency, and versatility. By embracing the latest innovations and understanding the intricacies of rolling techniques, procurement managers can not only address current market demands but also position their organizations for future success in a competitive landscape. The strategic selection of rolling processes and mills is essential for driving efficiency, sustainability, and quality in manufacturing operations.