Blogs
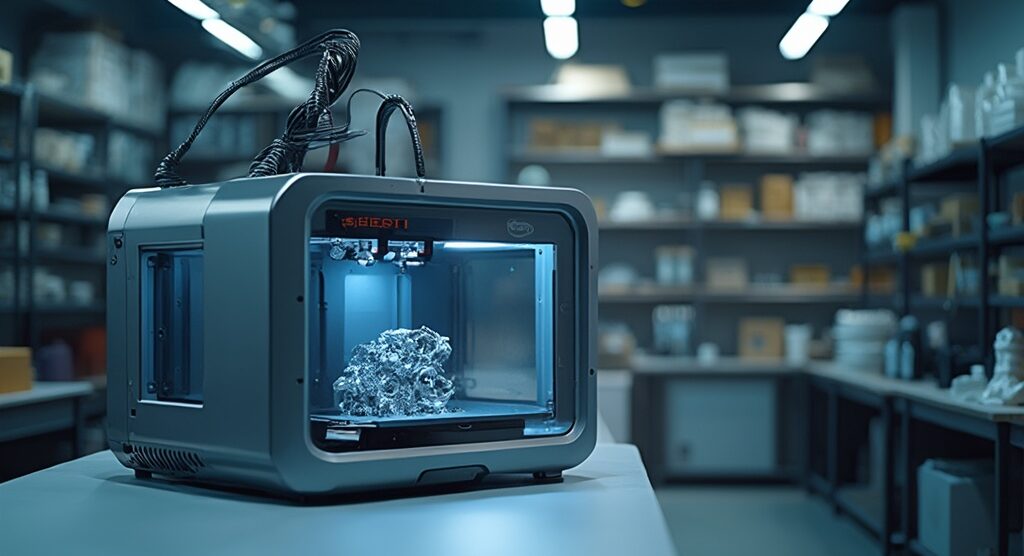
How to Choose and Use an Inconel 3D Printer: A Comprehensive Guide
Introduction
The advent of additive manufacturing has revolutionized the way industries approach production, particularly with high-performance materials like Inconel. As procurement managers navigate the complexities of selecting the right 3D printing technology, understanding the distinct methods available for Inconel printing becomes imperative. From Powder Bed Fusion to Binder Jetting, each technique offers unique advantages tailored to specific production needs.
This article delves into the various types of Inconel 3D printers, operational guidelines for optimal performance, and the selection of appropriate Inconel materials, alongside essential post-processing techniques. By exploring these facets, procurement professionals can make informed decisions that drive efficiency and enhance the quality of their manufacturing processes, ultimately positioning their organizations for success in a competitive landscape.
Exploring Different Types of Inconel 3D Printers
When selecting an Inconel 3D printer, it is crucial to consider different technologies that cater to diverse production requirements:
Powder Bed Fusion (PBF): This advanced method employs a laser to fuse layers of powdered substances, making it particularly effective for creating complex geometries and high-density components. Noteworthy models in this category include the EOS M 290 and Renishaw AM 400, both of which are recognized for their precision and reliability in producing intricate parts. According to SmarTech Analysis, the market for 3D printing is predicted to grow by a factor of 2 every three years, underscoring the increasing adoption of technologies like PBF.
Directed Energy Deposition (DED): DED technology employs concentrated thermal energy to melt materials during deposition, making it an excellent option for scenarios involving the repair or enhancement of existing components. Prominent examples include the Optomec LENS and DMG MORI Lasertec, which are well-regarded for their capability to manage complex repair tasks efficiently. As noted in recent industry reports, 65% of engineering companies utilized 3D printing in 2020, highlighting the relevance of DED in contemporary manufacturing.
Binder Jetting: This method involves applying a binding agent to layers of powder, allowing for a faster production process compared to PBF. However, it may require additional post-processing to enhance the strength of the final product. Significant systems in this category comprise the ExOne X1 and HP Metal Jet, which are intended for high-throughput uses. The growth of the 3D printing market for metals, expected to increase annually by around 32.4%, positions Binder Jetting as a viable option for manufacturers looking to scale.
Material Extrusion: Although less frequent for this alloy, this technique entails extruding a filament made of the material. It’s suitable for more straightforward uses where high precision is not the primary concern. The Markforged Metal X is a prominent option for those considering this approach. However, industry experts caution that while this method is more accessible, it may not meet the stringent requirements often associated with certain high-performance alloy applications.
By understanding these distinctive technologies and their respective market trends, procurement managers can make informed decisions that align with their production needs and budget constraints, ultimately optimizing their operational efficiency. Additionally, case studies such as the UK’s 3D printing market expansion, which is expected to grow at a rate of 10% CAGR between 2021 and 2026, provide insights into the practical applications and benefits of these technologies.
Operational Guidelines for Inconel 3D Printers
To effectively operate your Inconel 3D printer, adhere to the following guidelines:
Installation: Set up your printer in a controlled environment to minimize exposure to dust and temperature fluctuations. Follow the manufacturer’s instructions carefully regarding placement, power supply, and connectivity to ensure optimal performance. Recent guidelines emphasize that proper installation is crucial for achieving the desired print quality and consistency.
Calibration: Regular calibration is essential for achieving precise layer alignment and consistent substance flow. This involves checking the build plate level and adjusting the nozzle height. Calibration significantly impacts printing accuracy; scans of molds printed for technical studies reveal that over 75% of parts show a variation smaller than ±0.05 mm. As emphasized by Mk4User, an eminent member in the field,
To add to material shrinkage: the moment your model warps on your print bed, it’s over, concerning accuracy.
To illustrate effective calibration techniques, consider real-world examples such as the use of laser leveling tools to ensure optimal build plate alignment. Hence, maintaining calibration is critical.Material Handling: Store alloy powder in a dry, cool location to prevent moisture absorption, which can affect print quality. When handling materials, always use appropriate personal protective equipment (PPE) to ensure safety and compliance with industry standards.
Maintenance: Schedule routine maintenance checks, including thorough cleaning of the print head and timely replacement of worn components. Keeping a detailed log of maintenance activities allows for effective tracking of performance and early identification of potential issues. Case studies on installation best practices for nickel-chromium alloy 3D printers have shown that regular maintenance can significantly extend the lifespan of the equipment and improve overall print quality.
Monitoring: Leverage advanced monitoring software to oversee print jobs and quickly identify any emerging problems. This proactive approach enables timely adjustments during the printing process, significantly reducing the risk of failures.
By adhering to these operational guidelines, you can significantly enhance the performance and reliability of your 3D printer, which in turn leads to improved production outcomes. Additionally, Formlabs provides resources, including a white paper on optimizing design for functional 3D printed assemblies, offering valuable insights into materials and tolerances that can further inform your practices.
Selecting the Right Inconel Material for Your Project
Superalloys are offered in different grades, each designed for particular uses, making them a flexible option in challenging settings.
625 alloy: Renowned for its exceptional corrosion resistance and high strength, this material is particularly well-suited for marine and chemical processing uses. Its lightweight nature—boasting a density of 8.08 g/cm³—further enhances its appeal in industries where weight is a critical factor. When comparing densities, Incoloy 925, with a density of 8.08 g/cm³, demonstrates that certain alloys are generally lighter, which can be a significant consideration for procurement managers.
Mica Insulation Tape: Recognized for its high-temperature resistance and electrical insulation features, enhances certain applications by offering extra safety measures in electrical engineering scenarios. Mica Insulation Tape is especially effective in settings where heat and electrical insulation are crucial, rendering it essential in uses like transformers and motors.
Grade 718: Highly regarded for its remarkable high-temperature strength and oxidation resistance, making it an optimal choice for aerospace components and gas turbine engines. Its attributes contribute to enhanced performance and reliability in critical aerospace applications, reflecting the latest advancements in aerospace technology. For instance, a recent case study highlighted the successful implementation of Inconel 718 in a leading aerospace company’s turbine components, showcasing its effectiveness in high-stress environments. The case study revealed a 15% increase in operational efficiency and a significant reduction in maintenance costs, underscoring its value.
Mica Tape for Electrical uses: Invaluable in the production of fire-resistant cables and insulation systems, ensuring safety in high-temperature settings.
X-750: With excellent resistance to stress corrosion cracking, X-750 is frequently utilized in high-temperature applications, including gas turbines and nuclear reactors, where integrity is paramount.
When selecting a nickel-chromium alloy, it is essential to evaluate the specific environmental conditions and mechanical requirements of your project. Moreover, welding nickel-chromium alloys is advised to be carried out with automated machines using alloy 625 as filler substance to ensure compatibility and uphold structural integrity. Engaging in collaboration with suppliers of high-temperature materials, including Mica Tape products, such as Mica Sheet Tape and Insulating Mica Tapes, can help ensure that you choose the appropriate grade that aligns with your production goals, ultimately enhancing the success of your projects.
Post-Processing Techniques for Inconel Parts
After the additive manufacturing process is complete, consider the following essential post-processing techniques to optimize nickel-chromium superalloy components:
Heat Treatment: This critical process serves to relieve residual stresses inherent in printed parts and significantly enhances mechanical properties. Choosing the suitable heat treatment cycle is essential and should be customized to the specific alloy grade used. As noted by Jing Shi from the University of Cincinnati, the influence of post-heat treatment on microstructure and tensile properties can be profound, particularly in nano-TiC reinforced Inconel 718 produced through selective laser melting.
Surface Finishing: Utilizing surface finishing methods such as shot peening, grinding, or polishing can markedly enhance surface quality and fatigue resistance. The choice of method should be informed by the specific application requirements and desired surface characteristics. Real-world instances of effective surface finishing methods demonstrate that these processes can lead to enhanced performance in demanding environments.
Machining: For components that require precise tolerances or specific features, machining becomes an essential step. It is essential to ensure that the machining methods correspond with Inconel’s characteristics to reduce tool wear and uphold component integrity.
Cost Analysis: Conducting a thorough cost examination of post-processing methods is essential for procurement managers. Understanding the financial implications of each method allows for informed decision-making, ensuring that the selected processes align with budgetary constraints while maximizing performance.
Recent Trends: Keeping up with current developments in post-processing methods for nickel-chromium alloys is essential. Innovations in technologies and methodologies are continuously emerging, which can lead to improved efficiencies and cost savings. For instance, advancements in automated surface finishing and enhanced heat treatment processes are gaining traction in the industry.
By adopting these post-processing techniques, procurement managers can enhance the performance and longevity of specific metal components, ensuring they meet the rigorous demands of various applications. Recent studies, such as those published in Materials Characterization, highlight the significant effects of production parameters on the properties of IN 718, underscoring the importance of a well-structured post-processing approach.
Cost Considerations in Inconel 3D Printing
When creating a budget for 3D printing with that material, it is essential to consider various cost factors that significantly influence the overall expenditure:
- Substance Expenses: The cost of this powder is significantly greater than that of traditional substances, with current prices indicating an average of $47 per kilogram for alloy 718. Understanding the specific resource requirements for your project will aid in accurately estimating total costs.
- Printer Operation: This includes expenses related to energy consumption, equipment maintenance, and labor associated with operating the 3D printer. With the complexities of these materials, operational efficiency becomes crucial, impacting overall production costs.
- Post-Processing: Post-processing techniques such as heat treatment, machining, and surface finishing add to the budget. These processes are essential for attaining the desired mechanical characteristics and surface quality, which are crucial for applications involving nickel-chromium alloys.
- Supplier Relationships: Establishing and maintaining long-term relationships with suppliers can yield better pricing and terms. Interacting with your suppliers to secure advantageous terms can greatly lower total expenses, offering a competitive advantage in financial planning for specific projects. For instance, you can request a custom quote for specific products by reaching out to your suppliers, providing details about the items and quantities you need for an accurate quote.
- Case Studies: Reviewing case studies on cost analysis of Inconel 3D printing can provide valuable insights and real-world examples that aid in developing effective budgeting strategies.
By meticulously evaluating these cost factors, procurement managers can create a robust budget that aligns with production objectives while ensuring the necessary quality and performance standards are met.
Conclusion
The exploration of Inconel 3D printing technologies reveals a complex landscape that procurement managers must navigate to optimize production efficiency. By understanding the distinct printing methods—such as Powder Bed Fusion, Directed Energy Deposition, Binder Jetting, and Material Extrusion—professionals can select the technology that best aligns with their specific production needs and budget constraints. Each method offers unique advantages, underscoring the importance of a tailored approach to additive manufacturing.
Operational guidelines are equally critical in ensuring the effective use of Inconel 3D printers. From proper installation and calibration to diligent material handling and maintenance, adherence to best practices significantly enhances printing accuracy and component quality. Moreover, selecting the appropriate Inconel material—whether it be Inconel 625, 718, or X-750—requires a careful evaluation of application-specific requirements, emphasizing the need for informed decision-making in material procurement.
Post-processing techniques play a pivotal role in refining the performance of Inconel components. Methods such as heat treatment, surface finishing, and machining are essential for achieving the desired mechanical properties and surface integrity. Additionally, conducting thorough cost analyses that factor in material costs, operational expenses, and supplier relationships will empower procurement managers to develop effective budgeting strategies.
In conclusion, the strategic selection of Inconel 3D printing technologies, combined with meticulous operational practices and post-processing techniques, positions organizations to harness the full potential of additive manufacturing. By prioritizing these elements, procurement professionals can drive operational excellence, enhance product quality, and ensure their organizations remain competitive in an evolving industrial landscape.