Blogs
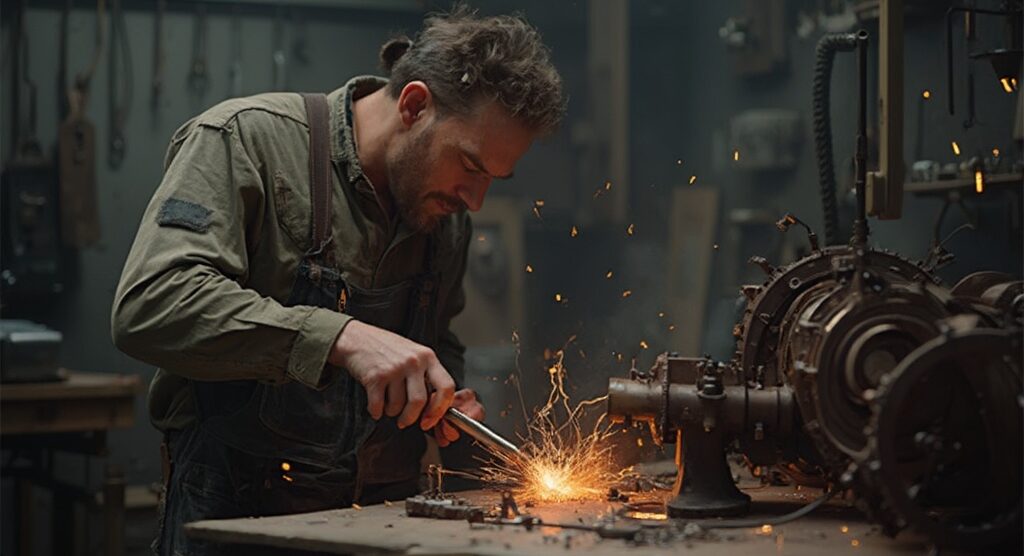
Understanding Beryllium Copper Non-Sparking Tools: A Complete Tutorial
Introduction
In industries where the stakes are high and safety is non-negotiable, the choice of tools can mean the difference between smooth operations and catastrophic incidents. Beryllium copper non-sparking tools emerge as a vital solution in environments fraught with the risk of fire and explosion, such as oil and gas, mining, and chemical processing. This advanced alloy not only offers remarkable strength and durability but also effectively mitigates the risk of ignition, making it an indispensable asset for procurement managers focused on safety and efficiency.
As the demand for innovative safety solutions grows, understanding the unique benefits and applications of beryllium copper tools becomes essential for professionals tasked with ensuring operational integrity in hazardous settings.
This article delves into the critical role these tools play, their advantages, maintenance practices, and the safety protocols necessary to maximize their effectiveness in high-stakes environments.
Introduction to Non-Sparking Tools: The Role of Beryllium Copper
In high-risk environments such as oil and gas, mining, and chemical processing, the use of non-sparking equipment is paramount to minimizing the risk of fire and explosion. Non-Sparking Tools, especially those crafted from a specific alloy, merge the outstanding electrical conductivity of the metal with the improved strength and hardness offered by another element. This unique composition results in implements that not only resist sparking but also demonstrate remarkable performance under demanding conditions.
The capability of beryllium instruments to absorb heat rapidly greatly decreases the chance of ignition, rendering them particularly effective in scenarios where safety is essential. While non-sparking implements can be several times more expensive than standard ones, this cost is an important consideration for procurement managers. A pertinent case study named ‘Copper and Sparks’ demonstrates that while this metal can generate cold sparks, its main use is in non-sparking implements because of its efficient heat absorption, which reduces ignition hazards.
As sectors progressively emphasize protection and effectiveness, the need for beryllium-based instruments is acknowledged as a strategic investment, as they represent the optimal substitute for non-sparking usage in explosive risk settings. Moreover, Emerson’s recent purchase of NI for $8.2 billion underscores the increasing significance of innovative solutions in the sector, further emphasizing the importance of beryllium instruments in improving safety measures.
Benefits of Beryllium Copper in Non-Sparking Tool Production
Beryllium copper presents a range of advantages for non-sparking tools, making it an ideal choice for various applications in hazardous environments:
- High Strength and Durability: This alloy exhibits considerable strength in comparison to pure metal, ensuring instruments can withstand extensive use without warping or losing integrity. Domadia’s dedication to quality ensures you receive instruments that endure over time.
- Corrosion Resistance: Beryllium alloy’s inherent resistance to corrosion extends the lifespan of instruments, even in the most challenging conditions, thereby reducing replacement costs.
- Excellent Conductivity: While preserving its non-sparking characteristics, this alloy also demonstrates notable electrical conductivity, with thermal conductivity surpassing aluminum and marginally below that of pure metal. This makes them suitable for applications where electrical interaction is necessary.
- Lightweight Composition: These instruments are notably lighter than many other non-sparking materials, minimizing user fatigue during prolonged use—an essential factor for efficiency in demanding tasks.
- Versatile Applications: The unique characteristics of beryllium copper make it adaptable across multiple industries, including aerospace and automotive sectors. As pointed out by Lothar Wagner, Chair of Applied Materials Science and Engineering at TU Clausthal, the microstructure-property relationships of this alloy significantly enhance its fatigue performance and surface treatment capabilities, emphasizing its reliability in manufacturing.
Additionally, the use of beryllium copper non-sparking tools is essential for ensuring protection in potentially explosive environments such as petrochemical plants and oil refineries. They help in preventing ignition that could lead to fires or explosions, ensuring the safety of personnel and property. A case study titled “Health and Safety Considerations of Beryllium Alloys” indicates that while inhalation of airborne particles poses health risks, these alloys in solid form do not present the same hazards.
This renders alloys safe for utilization and disposal without specific hazardous waste protocols, emphasizing their eco-friendliness—an essential factor for procurement managers focused on sustainability.
In summary, specialized instruments merge strength, durability, and versatility, making them a favored choice for professionals overseeing procurement in high-stakes situations. Domadia stands at the forefront of this technology, ensuring you receive the best solutions tailored to your needs. We invite you to explore our range of Beryllium Copper products and discover how they can enhance your operations.
Types of Beryllium Copper Non-Sparking Tools
Beryllium copper non-sparking tools are essential for safe operations in hazardous environments, significantly reducing the risk of ignition in sensitive settings. It is essential to recognize that contacts with beryllium can happen during the handling of beryllium-containing substances, emphasizing the significance of precautions in equipment usage. The following types are commonly utilized:
- Wrenches: Designed for assembly and maintenance tasks, these tools are vital in preventing accidental sparking around flammable materials, ensuring adherence to standards like UNS and ASTM in sensitive environments. Their design improves protection by minimizing the risk of ignition during use.
- Hammers: In explosive settings, beryllium copper non-sparking tools, such as hammers, deliver reliable striking power without generating sparks, making them indispensable for safe handling and assembly. Their compliance with international standards further ensures their reliability in critical applications.
- Screwdrivers: These precision tools facilitate detailed work while improving protection in hazardous locations, thus significantly reducing ignition risks during operation. Their non-sparking characteristics conform to strict regulations.
- Pliers: Known for their versatility, alloy pliers are widely utilized in tasks requiring secure gripping and manipulation, providing a safe alternative in environments where sparks could lead to serious incidents. Their adherence to UNS and ASTM standards strengthens their security profile.
- Chisels: Beryllium copper non-sparking tools, like chisels, are ideal for cutting and shaping materials, blending durability with security, making them suitable for sensitive applications where conventional instruments could pose a risk.
According to Cezary Palczynski in the Handbook on the Toxicology of Metals, the properties of beryllium copper make it a valuable asset across industries such as petrochemicals, pharmaceuticals, oil and gas, aerospace, and automotive. These instruments exemplify innovation in non-sparking technology, aligning with market demands for improved security and reliability in these sectors while adhering to stringent international standards. The adherence to US and ASTM standards not only guarantees the quality of these instruments but also strengthens their role in enhancing safety in hazardous environments.
Maintenance and Care for Beryllium Copper Non-Sparking Tools
Proper maintenance and care of beryllium copper non sparking tools are crucial in ensuring their longevity and effectiveness, particularly in hazardous environments. Beryllium copper non sparking tools are recognized for their corrosion-resistant and highly durable properties, making them ideal for use in explosive environments. Here are key practices to follow:
Cleaning: Utilize a mild soap solution and water for regular cleaning. Avoid abrasive cleaners, as they can scratch the surface and compromise the integrity of the implements. Notably, magnesium hydroxide’s insolubility in water makes it a suitable cleaning agent in specific contexts without contributing to corrosion.
Drying: After cleaning, thoroughly dry the equipment to prevent moisture-related corrosion, which can significantly affect performance and lifespan.
Storage: Keep equipment in a dry setting, preferably inside protective cases to guard them against environmental pollutants and physical harm. This practice not only preserves their condition but also enhances workplace safety.
Inspection: Conduct periodic inspections to identify signs of wear or damage. Substitute any compromised equipment swiftly to uphold standards and maintain operational efficiency.
Lubrication: For instruments with moving components, apply appropriate lubricants to minimize friction and optimize performance.
In addition to these maintenance practices, it is essential to follow safety guidelines when using beryllium copper non sparking tools. This includes proper handling procedures to minimize exposure risks, as Beryllium can pose health hazards if not managed correctly. In industrial practice, the disposal and recycling of contaminated materials underscore the critical need for proper management of Beryllium-containing equipment.
Employers must label and handle these materials with care to ensure safe transport and disposal, significantly reducing the risk of exposure. As highlighted in the Handbook on the Toxicology of Metals by Cezary Palczynski, proper maintenance of equipment is essential not only for performance but also for minimizing health risks associated with Beryllium exposure. Understanding that Beryllium can distribute to the liver, kidney, and bone, primarily eliminated through urine, underscores the health risks associated with improper maintenance and handling.
Safety Protocols for Using Beryllium Copper Non-Sparking Tools
When using beryllium copper non-sparking tools made from a specific alloy, following strict safety protocols is essential to reduce risks linked to dangerous environments. Beryllium copper non-sparking tools serve as essential alternatives in explosive potential applications where traditional implements pose significant hazards. These beryllium copper non-sparking tools are designed not only to provide non-sparking properties but also to exhibit non-magnetic characteristics, making them ideal for environments where magnetic interference could pose additional risks.
Consider the following essential guidelines:
Personal Protective Equipment (PPE): It is imperative to don appropriate PPE, including gloves and protective glasses, to provide a barrier against potential hazards. The correct use of PPE can significantly reduce the chances of injury.
Training: Comprehensive training for all users is critical in the proper handling and operation of non-sparking tools. This training reduces risks and ensures that all personnel are well-versed in protective practices.
Environment Assessment: Conduct a thorough assessment of the work environment prior to commencing tasks. Identifying potential hazards, such as flammable materials or unstable surfaces, is crucial for maintaining safety. The use of explosimeters to monitor hazardous environments is essential for ensuring that conditions are safe for equipment usage. Regular inspections of equipment for damage or wear are essential. Ensuring that equipment is in optimal working condition before use can prevent accidents and enhance operational efficiency.
Emergency Procedures: Familiarize all users with established emergency procedures to ensure a swift and effective response in the event of an accident. Comprehending these protocols can greatly enhance security results.
Practical uses of beryllium copper non-sparking tools include their application in the oil and gas sector, where combustible gases are found, and in chemical facilities, where reactive substances are managed. Recent incidents, such as the fatalities of Vixon Louis and Miguel Angel Amador Olvera, underscore the dire consequences of insufficient protective measures. These tragedies emphasize the necessity of proactive measures and a culture of protection, particularly when using non-sparking tools in potentially hazardous environments.
As pointed out by expert Jim Loud, ‘Incident rates do not measure security.’ They assess the lack of security. Furthermore, the case study regarding pedestrian safety raises awareness about the importance of adhering to safety protocols in all environments.
Conclusion
In high-risk industries where safety is paramount, the adoption of beryllium copper non-sparking tools is not just a recommendation but a necessity. These tools provide a unique blend of strength, durability, and non-sparking properties, making them indispensable in environments such as:
- Oil and gas
- Mining
- Chemical processing
Their ability to minimize ignition risks while maintaining excellent conductivity and lightweight characteristics positions them as the optimal choice for procurement managers focused on safety and operational efficiency.
The benefits of beryllium copper extend beyond mere functionality; they include:
- Corrosion resistance
- Versatility across various applications
From wrenches and hammers to pliers and chisels, these tools are designed to meet stringent safety standards while enhancing productivity. However, the effectiveness of beryllium copper tools is greatly influenced by proper maintenance and adherence to safety protocols. Regular cleaning, inspection, and responsible handling practices are crucial in ensuring their longevity and minimizing health risks associated with beryllium exposure.
Ultimately, the strategic investment in beryllium copper non-sparking tools represents a commitment to operational integrity and safety. As industries continue to prioritize innovative solutions for hazardous environments, understanding and implementing the unique advantages of these tools will be vital in preventing catastrophic incidents. By integrating these practices, procurement managers can ensure that their teams operate safely and efficiently, reinforcing a culture of safety that protects both personnel and assets in challenging conditions.