Blogs
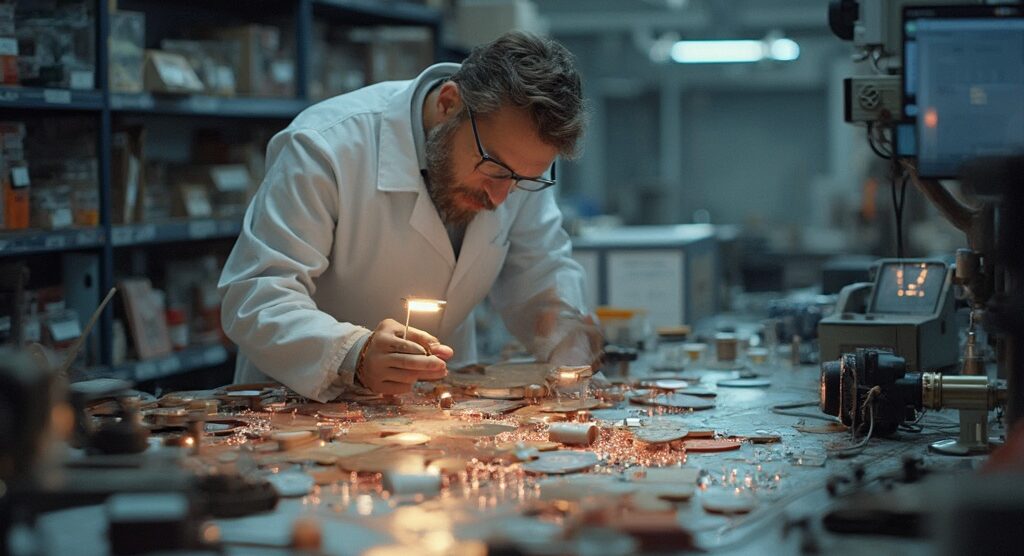
Understanding CDA 172 Thermal Conductivity: A Complete Tutorial for Microwave Component Design
Introduction
In the realm of advanced material selection, CDA 172 copper stands out for its exceptional thermal conductivity and versatility, particularly in the demanding field of microwave component design. As industries continue to innovate, the need for materials that not only meet but exceed performance expectations has never been greater. CDA 172, with its impressive ability to facilitate efficient heat dissipation and maintain electrical integrity, is becoming a go-to choice for engineers and procurement managers alike.
This article delves into the fundamental properties of CDA 172 copper, its applications in microwave technology, a comparative analysis with other copper alloys, strategic procurement considerations, and future trends that underscore its significance in evolving design landscapes. Understanding these elements is crucial for making informed decisions that drive operational excellence and competitive advantage in an ever-changing market.
Fundamental Properties of CDA 172 Copper: Thermal Conductivity Insights
CDA 172, a high-conductivity copper alloy, is distinguished by its remarkable thermal conductivity, ranging from 400 to 4000 W/m·K, depending on specific temper and processing methods. The CDA 172 thermal conductivity for microwave components makes CDA 172 copper an ideal option for uses that require efficient heat dissipation. By facilitating effective heat transfer, the CDA 172 thermal conductivity for microwave components minimizes thermal losses, optimizing the performance of microwave devices and ensuring superior operational efficiency.
Furthermore, this alloy boasts impressive ductility and notable resistance to corrosion, making it particularly advantageous in challenging environments. With a minimum electrical conductivity of 22% IACS, CDA 172 supports a variety of uses, including aerospace and precision engineering, where Beryllium Copper (CuBe2, C17200) excels due to its exceptional strength and fatigue resistance. At Domadia, we take pride in our leadership role in supplying and manufacturing high-performance Beryllium Copper Plates, ensuring that our clients receive the best solutions tailored to their needs.
Additionally, our commitment to quality and customer satisfaction extends to Oxygen Free Copper (OFE/OHFC), essential for critical medical components. A satisfied customer remarked, ‘Thank you for your quick response,’ showcasing the ease of procurement associated with CDA 172’s diverse availability in forms such as sheet, plate, and bar. By comprehending these essential properties, engineers can strategically design components that fully utilize the CDA 172 thermal conductivity for microwave components, ensuring longevity and performance in their uses.
Applications of CDA 172 Copper in Microwave Component Design
CDA 172 thermal conductivity for microwave components has made CDA 172 copper a critical material in their design, primarily due to its exceptional thermal and electrical properties. Its primary use lies in the manufacturing of heat sinks, where effective heat dissipation is imperative for maintaining performance and reliability. This alloy’s ability to withstand elevated temperatures while ensuring consistent performance is crucial for engineers engaged in CDA 172 thermal conductivity for microwave components.
Furthermore, CDA 172 is extensively utilized in connectors and transmission lines, where minimizing losses and maximizing conductivity are essential for signal integrity. In antenna design, the superior CDA 172 thermal conductivity for microwave components of the alloy significantly enhances overall efficiency, making it a preferred choice among professionals in the field. Recent industry reports highlight the increasing significance of these solutions, as acquisition strategies must adjust to the latest requirements for high-performance materials.
Additionally, with the Occupational Safety and Health Administration establishing a permissible exposure limit for copper dust at 1 mg/m³ and an IDLH value of 100 mg/m³, understanding the safe handling of this material becomes paramount for purchasing managers. As industries keep advancing microwave technology, remaining knowledgeable about CDA 172 thermal conductivity for microwave components and its performance metrics is essential for strategic procurement decisions. As Michael from Michael Talks Metals stated, ‘This is Michael with Michael Talks Metal, see you next Thursday, same time, same place,’ emphasizing the importance of continuous learning and adaptation in this evolving field.
Moreover, a case study titled ‘Copper in Electronics’ highlights CDA 172’s use in integrated circuits and printed circuit boards, showcasing its significant contributions to enhancing performance and efficiency in various electronic devices.
Comparative Analysis of CDA 172 with Other Copper Alloys
When assessing CDA 172 thermal conductivity for microwave components in comparison to other alloys such as C11000 and C19400, CDA 172 consistently demonstrates superior performance. Specifically, CDA 172 boasts a thermal conductivity significantly higher than C11000, which measures at 390 W/m-K, and C19400 at 260 W/m-K. While C11000 is recognized for its exceptional electrical conductivity, it does not match the CDA 172 thermal conductivity for microwave components, which is essential for effective heat dissipation.
Conversely, C19400, although noted for its mechanical strength, falls short in thermal management capabilities. The chemical composition of CDA 172 copper includes a minimum copper content of 99.90%, ensuring material quality and compliance with industry standards, as highlighted in case studies that define acceptable ranges for various chemical elements. This comprehensive evaluation enables engineers and purchasing managers to strategically select the most appropriate material, effectively balancing performance requirements with cost considerations.
In real-world scenarios, the use of CDA 172 thermal conductivity for microwave components can lead to improved thermal efficiency and overall system performance. Additionally, purchasing managers are encouraged to request samples or inquire further about Fisk products suited for their applications to make informed decisions.
Cost Considerations and Procurement Strategies for CDA 172 Copper
Procurement managers navigating the complexities of CDA 172 copper must remain vigilant to the volatile nature of market prices, driven by global supply and demand trends. Creating a strong sourcing strategy is essential, one that nurtures long-term partnerships with suppliers like Domadia, recognized for their high-quality Oxygen Free Copper (OFE/OHFC) designed for critical medical components. This ensures not only favorable pricing but also consistent quality.
As emphasized by specialists, the tensile strength of high-strength cast Cu-Ni alloys can achieve up to 850 N/mm when heat treated, underscoring the significance of material quality in purchasing choices. Additionally, leveraging bulk purchasing agreements can significantly mitigate costs, particularly in fluctuating markets. Michael, host of Michael Talks Metals, emphasizes, ‘This is Michael with Michael Talks Metal, see you next Thursday, same time, same place,’ reminding us of the importance of expert insights in shaping purchasing strategies.
Regular evaluations of supplier performance, along with careful observation of market conditions, enable organizations to make timely adjustments to their purchasing strategies. Furthermore, Domadia’s dedication to supplying tailored Beryllium Copper Plates enhances value to purchasing choices. A recent client stated, ‘Domadia’s Beryllium Copper Plates exceeded our expectations in both quality and customization, significantly enhancing our project outcomes.’
This proactive approach not only enhances competitiveness but also optimizes material costs, ensuring that procurement managers are equipped to navigate the intricacies of the copper alloy market effectively. Pricing details for Beryllium Copper Strips are competitive, with inventory readily available to meet urgent project demands, further solidifying Domadia’s position as a reliable supplier.
Future Trends in Microwave Component Design Using CDA 172 Copper
The evolution of microwave technology positions CDA 172 copper as a pivotal material in the advancement of component design, particularly when paired with high-quality insulation solutions such as Domadia’s Mica Tapes. With the U.S. Department of Energy forecasting that updated energy efficiency standards for microwave ovens will save consumers $1.6 billion over the next decade, the demand for materials capable of handling higher frequencies and temperatures is on the rise. Domadia’s Mica Insulation Tape, comprising Mica Sheet Tape and Insulating Mica Tapes, is recognized for its excellent thermal and electrical insulation characteristics, rendering it perfectly appropriate for essential uses in this domain.
As sectors like automotive, chemicals, consumer electronics, and energy strive for enhanced energy-efficient designs, the demand for superior thermal management capabilities will stimulate further interest in CDA 172 uses. The global microwave oven market is growing due to demand for convenience and technological advancements, solidifying microwaves as kitchen staples and reflecting the increasing ownership rates in developed markets. Innovations in manufacturing techniques are anticipated to enhance the performance characteristics of both CDA 172 and Domadia’s Mica Tapes, positioning them at the forefront of research in advanced microwave applications.
For procurement managers, it is essential to stay informed about these trends and consider how high-temperature electrical insulation solutions can complement CDA 172 copper in future designs. To learn more about our range of Mica Tapes and how they can benefit your business, we invite you to contact our expert team or visit our website today.
Conclusion
CDA 172 copper emerges as an indispensable asset in the evolving landscape of microwave technology, characterized by its outstanding thermal conductivity and versatility. The exploration of its fundamental properties reveals a material that not only excels in heat dissipation but also offers significant advantages in terms of ductility and corrosion resistance. These attributes make CDA 172 a prime candidate for critical applications, such as:
- Heat sinks
- Connectors
- Transmission lines
where optimal performance is paramount.
When compared to other copper alloys, CDA 172 consistently outperforms its counterparts, showcasing superior thermal efficiency essential for high-performance microwave applications. This comparative analysis empowers engineers and procurement managers to make informed choices, balancing performance requirements with cost considerations effectively. Moreover, strategic procurement practices, including:
- Fostering long-term supplier relationships
- Leveraging bulk purchasing agreements
can mitigate costs in a fluctuating market, further enhancing the value derived from CDA 172 copper.
Looking ahead, the future trends in microwave component design suggest a growing reliance on CDA 172 copper, particularly as industries push for more energy-efficient solutions. The integration of high-quality insulation materials, such as Mica Tapes, alongside CDA 172 will be crucial in meeting the demands of advanced microwave applications. Staying abreast of these developments will enable procurement managers to secure a competitive edge, ensuring that they are well-equipped to navigate the complexities of material selection and procurement in an ever-evolving market.