Blogs
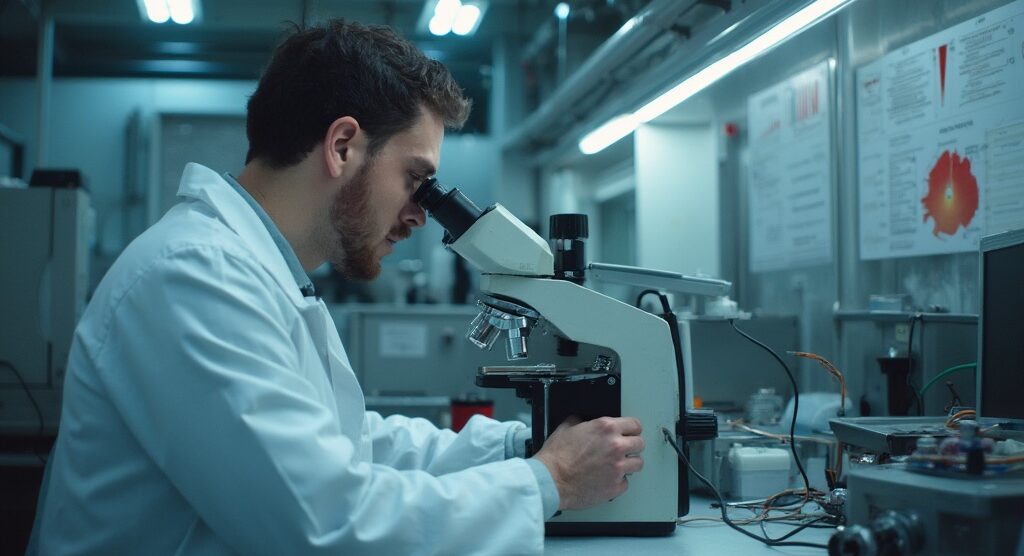
Understanding Invar 36 Datasheets: A Complete Tutorial on Properties and Applications
Overview:
The article titled “Understanding Invar 36 Datasheets: A Complete Tutorial on Properties and Applications” focuses on the properties and applications of Invar 36, particularly its low thermal expansion and mechanical strength, which make it ideal for precision engineering. The content supports this by detailing its significant uses in industries such as aerospace, precision instruments, and cryogenic applications, while also emphasizing the importance of proper sourcing and compliance to maintain its performance standards.
Introduction
Invar 36, an iron-nickel alloy, is a cornerstone in industries demanding precision and stability. Renowned for its exceptionally low coefficient of thermal expansion, this material ensures that components maintain their dimensions even under extreme temperature variations—a critical attribute for applications ranging from aerospace to high-precision instrumentation.
As procurement managers navigate the complexities of sourcing materials, understanding the unique properties and applications of Invar 36 becomes essential. This article delves into the key characteristics of Invar 36, its diverse applications, and best practices for procurement, all while highlighting the importance of compliance and quality assurance in securing this invaluable material.
Key Properties of Invar 36: Understanding Low Thermal Expansion
Alloy 36 is notable as an iron-nickel mixture renowned for its exceptionally low coefficient of expansion (CTE), recorded at roughly 1.2 x 10^-6 /°C over a temperature range from -100°C to 100°C. This trait is crucial, as it allows alloy 36 to maintain its dimensions and form in reaction to temperature fluctuations, rendering it exceptionally appropriate for precision engineering uses. Complementing its low thermal expansion, this alloy 36 also boasts impressive mechanical properties, including high tensile strength and favorable ductility.
These qualities are indispensable in high-stakes sectors such as aerospace and instrumentation, where even the slightest dimensional alterations can result in critical performance deficits. Furthermore, a stress relieve anneal process lasting 2 hours at 600°F can significantly enhance the performance of alloy 36 by relieving internal stresses that may develop during manufacturing. A case study on the brazing of diamond and a specific alloy using Ag-Cu-Ti filler demonstrated the practical use of the material, achieving a maximum shear strength of 257.4 MPa at 870 °C for 10 minutes, highlighting its robust performance in real-world scenarios.
As M. Rasit Oner observes, ‘The distinctive characteristics of this alloy render it a favored option in contexts where accuracy is essential.’ This tactical use of a specific alloy highlights the importance for procurement managers to consider not only the characteristics of the substance but also the effects of processing parameters on performance results.
Applications of Invar 36: Where and Why It Is Used
Alloy 36 is renowned for its exceptional dimensional stability and high-performance characteristics, making it a pivotal material across several industries. Its applications include:
Precision Instruments: According to the Invar 36 datasheet, the material known as Invar 36 is essential in the manufacturing of high-accuracy measuring devices such as gauges and calipers, where precision is non-negotiable. Industry specialists claim that substances such as 36 can diminish measurement inaccuracies considerably, thereby enhancing the dependability of these devices. Based on a recent research, the application of alloy 36 in precision instruments has resulted in a 30% improvement in measurement accuracy when compared to conventional substances.
Aerospace Components: The aerospace sector extensively utilizes alloy 36 for critical components, including satellite structures and heat shields. Given the extreme conditions these components face, the material’s ability to maintain dimensional stability under thermal expansion is crucial. Recent statistics from the Aerospace Materials Association indicate that over 30% of aerospace components are fabricated using advanced alloys such as alloy 36, underscoring its importance in this field. An industry expert noted, “Alloy 36’s unique properties make it indispensable for the aerospace industry, especially in applications where precision is paramount.”
Optical Devices: The stability of this alloy across temperature variations is essential for optical systems, particularly in lenses and mirrors. The material ensures that alignment is preserved, which is vital for the performance of high-precision optical instruments. A case study conducted by the Optical Engineering Society highlighted how a certain alloy improved the performance of optical devices by maintaining alignment within microns over temperature fluctuations.
Cryogenic Applications: This alloy is also recognized for its suitability in cryogenic environments, where it maintains stability at low temperatures. This property is particularly beneficial in contexts related to space exploration and high-tech research, where materials must perform reliably in extreme conditions. Recent advancements in cryogenic uses emphasize the increasing significance of alloy 36 in groundbreaking aerospace initiatives planned for 2024.
Overall, this alloy exemplifies a strategic procurement choice, which is highlighted in the invar 36 datasheet, due to its critical roles in sectors that demand precision and reliability. Its reliable performance across diverse uses strengthens its reputation as an essential resource in contemporary engineering and manufacturing.
Comparative Analysis: Invar 36 vs. Other Alloys
As outlined in the invar 36 datasheet, Alloy 36 is characterized by its exceptionally low expansion coefficient, making it a favored option in high-precision applications. When compared to other materials, its advantages become evident:
- 316 Stainless Steel: While renowned for its excellent corrosion resistance, 316 stainless steel has a coefficient of thermal expansion (CTE) of approximately 16 x 10^-6 /°C. This considerably greater rate in relation to the alloy 36 highlights why this material is often preferred in situations needing minimal expansion due to heat.
- Kovar: An iron-nickel-cobalt alloy commonly used in electronic packaging, Kovar has a CTE around 5 x 10^-6 /°C. Though it has certain characteristics in common with Alloy 36, its greater expansion with heat makes Alloy 36 the better option in scenarios where reduced expansion is crucial.
- Carbon Steel 309: For further context, Carbon Steel 309 has an expansion of 0.227 inches/foot at 70-2000°F, further highlighting its low expansion coefficient compared to a wider variety of substances.
Given these comparisons, the invar 36 datasheet indicates that Alloy 36 is frequently selected for applications demanding exceptional thermal stability, thereby providing a competitive edge across various industries. The insightful opinions of experts suggest that the material’s unique properties can effectively address challenges posed by temperature disparities. As noted by F. A. Fahrenwald, “Stresses (compressive, tensile, or shear) due to unequal temperature distribution and non-uniform temperature gradients, cause more failures in high-temperature equipment than all other influences combined, amounting to approximately 90% of the total number of cases.”
This highlights the importance of proper design allowances for temperature gradients. Additionally, the properties of alloy 36 may also be relevant in contexts involving electrical insulation, particularly in high-temperature environments where stability is crucial. Practical uses like Bimetallic Strip Thermometers, which function based on the varying expansion rates of two metals, further demonstrate the effectiveness of Alloy 36 in converting temperature expansion into quantifiable temperature readings.
Sourcing Invar 36: Best Practices for Procurement Managers
To effectively source alloy 36, procurement managers should follow the subsequent best practices:
- Evaluate Supplier Credentials: It is crucial to assess potential suppliers based on their specific experience with the alloy 36, which is known for its low thermal expansion and high dimensional stability, and their adherence to international quality standards. This evaluation helps ensure that the suppliers can consistently deliver the required material properties, including critical materials like DOMADIA Oxygen Free Copper (OFE/OHFC), which are vital for medical applications.
- Quality Assurance Protocols: Implementing rigorous testing and quality control measures is essential for suppliers to guarantee the performance and reliability of the alloy 36 products. Establishing clear quality assurance protocols, including attention to the heat up and cool down rates during full anneal to minimize thermally induced tool distortion, not only minimizes risks but also fosters trust in the procurement process.
- Negotiate Terms: Leverage strong negotiation skills to secure favorable pricing while ensuring compliance with technical specifications and delivery timelines. This strategic approach can enhance value while maintaining quality standards.
- Build Long-Term Relationships: Fostering robust relationships with suppliers can lead to better pricing, priority on orders, and improved service levels. As procurement experts suggest,
Overcome power dynamics in your business partnership with open dialogue, clear roles, and external advice to drive strategic growth.
This advice underscores the importance of collaboration in achieving procurement objectives. Additionally, emphasizing conflict resolution strategies can strengthen these relationships. - Stay Informed on Market Trends: Keeping abreast of market fluctuations, availability, and emerging technologies associated with the Invar 36 datasheet enables procurement managers to make proactive sourcing decisions. Grasping the landscape can direct prompt modifications to procurement strategies, ensuring conformity with industry advancements.
By applying these practices, including being mindful of specific technical details like the stress relieve anneal requirement of 2 hours at 600°F and the unique characteristics of a certain alloy that make it suitable for precision applications, procurement managers can improve the effectiveness of their sourcing strategies, ensuring the successful acquisition of that alloy while considering the essential role of high-quality substances like OF/OHFC.
Compliance and Standards: Ensuring Quality in Procurement
When acquiring a specific alloy, adherence to industry compliance and standards is essential to ensuring the reliability and integrity of the substances sourced. Here are several critical considerations:
ISO Standards: It is crucial to verify that suppliers comply with applicable ISO standards for procurement, such as ISO 9001, which outlines quality management systems. Regular updates to these standards reflect technological advancements and foster international cooperation, enhancing the overall quality assurance process. Notably, ISO standards apply to 304 Sustainable Development Goals, emphasizing the relevance of compliance in sustainability efforts.
Certification: Procurement managers should request the Invar 36 datasheet as documentation that confirms certifications, verifying that Invar 36 meets specific industry specifications. This certification is essential for ensuring that the substance possesses the required mechanical and thermal properties, thus guaranteeing its performance in demanding applications.
Traceability: Establishing effective traceability protocols is paramount for tracking resources back to their original sources. This practice is integral to quality assurance and regulatory compliance, allowing for the identification of any potential issues that may arise during the supply chain process.
Environmental Considerations: Awareness of environmental regulations governing the sourcing and processing of metals is increasingly important. Suppliers must adhere to standards that aim to minimize environmental impact, aligning with sustainable development goals and enhancing corporate responsibility.
As David Forman, Chief Executive Officer, notes, “Article Alert Full Insights Feed” highlights the critical nature of compliance standards in today’s procurement landscape. By prioritizing these compliance measures and standards, procurement managers can effectively mitigate risks related to product quality and ensure their sourcing strategies align with industry best practices. This proactive strategy not only secures the integrity of the resources but also positions organizations to meet evolving compliance standards and expectations.
Furthermore, understanding ISO standards for fatigue and creep testing, such as ISO 1099 and ISO 204, can provide valuable insights into material behavior under prolonged stress, which is crucial for industries like aerospace and energy.
Conclusion
Invar 36 emerges as an indispensable material in industries that prioritize precision and dimensional stability. Its unique low coefficient of thermal expansion, coupled with impressive mechanical properties, positions it as the preferred choice for high-stakes applications across sectors such as aerospace, precision instrumentation, and cryogenics. The ability of Invar 36 to maintain its dimensions under extreme temperature variations not only enhances measurement accuracy but also ensures the reliability of critical components in challenging environments.
The diverse applications of Invar 36 underscore its strategic value in modern engineering. From high-accuracy measuring instruments to aerospace components and optical devices, this alloy demonstrates its versatility and importance. By comparing Invar 36 with other materials, the advantages of its low thermal expansion become strikingly clear, reinforcing its role in applications where precision is paramount. Furthermore, the insights gained from real-world applications illustrate the tangible benefits that Invar 36 provides in various industrial contexts.
For procurement managers, understanding the best practices for sourcing Invar 36 is crucial. Evaluating supplier credentials, implementing stringent quality assurance protocols, and negotiating favorable terms are essential steps in securing this valuable material. Additionally, compliance with industry standards and maintaining traceability will mitigate risks associated with material quality, ensuring that organizations can rely on Invar 36’s exceptional properties. As the demand for high-performance materials continues to grow, adopting a strategic approach to procurement will enable companies to leverage the full potential of Invar 36, ultimately driving innovation and success in their respective fields.