Blogs
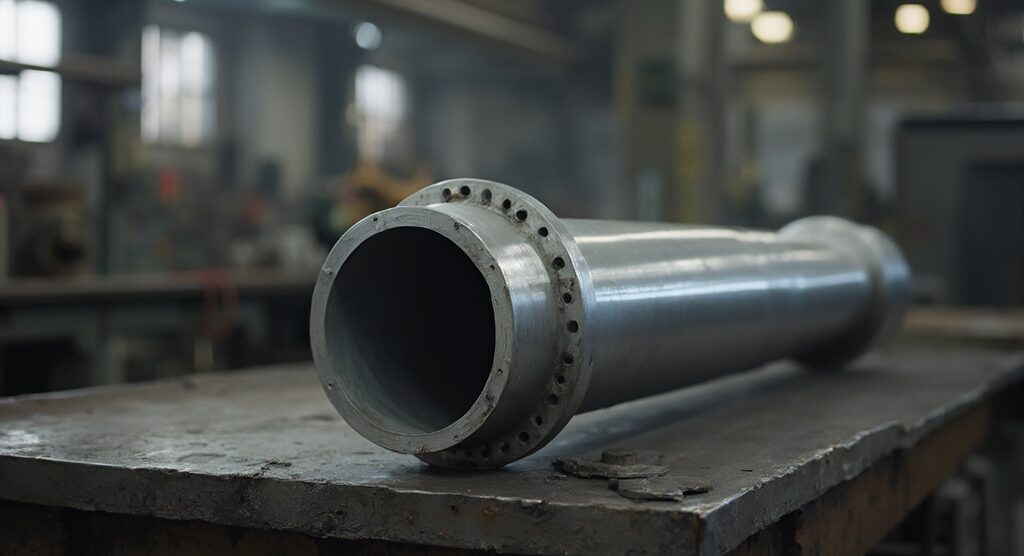
Understanding the Versatile Applications of C-276 Hastelloy in Industry
Introduction
Hastelloy C-276, a nickel-molybdenum-chromium alloy, is a paragon of engineering excellence due to its unparalleled resistance to corrosion and oxidation. This alloy, composed of approximately 57% nickel, 16% molybdenum, and 15% chromium, with minor amounts of tungsten and iron, is indispensable for industries facing harsh environments. Its remarkable ability to withstand aggressive chemicals and maintain structural integrity under extreme conditions makes it a preferred choice for critical applications.
In industrial settings, Hastelloy C-276 demonstrates exceptional corrosion resistance, particularly in reducing environments where pitting, crevice corrosion, and stress corrosion cracking are common threats. Its performance remains robust even at elevated temperatures, ensuring reliability in high-temperature industrial processes. The alloy’s resilience is crucial for sectors such as chemical processing and petrochemicals, where both temperature and corrosive elements present significant challenges.
The chemical processing industry relies heavily on Hastelloy C-276 for constructing reactors, heat exchangers, and pipelines that handle corrosive substances like sulfuric and hydrochloric acids. Its durability and adaptability are also vital for pharmaceutical and petrochemical sectors, supporting processes involving aggressive media. Furthermore, the trend towards energy-efficient manufacturing underscores the importance of materials that ensure longevity and minimize downtime, a role well-suited to Hastelloy C-276.
Proper fabrication and welding of Hastelloy C-276 require meticulous attention to maintain its superior properties. Incorporating pre-heat and post-weld heat treatments, alongside stringent quality control, is essential to preserving its corrosion resistance and mechanical integrity. These considerations are particularly critical in high-end manufacturing applications, such as the marine industry and advanced air mobility markets, where maintaining high standards is paramount for optimal performance.
Composition and Properties of Hastelloy C-276
The nickel-molybdenum-chromium alloy is notable for its exceptional resistance to corrosion and oxidation. ‘The exact composition typically features around 57% nickel, 16% molybdenum, and 15% chromium, with minor additions of tungsten and iron.’. This unique amalgamation of elements endows it with exceptional performance attributes, making it indispensable for numerous demanding industrial applications. Famous for its capacity to withstand severe surroundings, this alloy stands out in opposing chlorides and other hostile substances, guaranteeing durability and dependability in the toughest circumstances.
Corrosion Resistance and High-Temperature Performance
Hastelloy C-276 stands out for its exceptional corrosion resistance, particularly in reducing environments. This alloy is highly effective against pitting, crevice corrosion, and stress corrosion cracking, which are prevalent issues in industrial applications. For instance, geothermal power plants deal with highly corrosive steam containing chemicals like hydrogen sulfide, which can severely damage equipment. This alloy reduces such risks, rendering it essential in these environments.
Furthermore, this alloy preserves its mechanical characteristics at high temperatures, guaranteeing dependable operation in elevated thermal environments. This capability is crucial in industries such as chemical processing and petrochemicals, where both temperature and corrosive elements pose significant threats. A case from the Australian manufacturing industry emphasizes the significance of high-performance substances such as a specific alloy. Researchers are continuously exploring metal mixtures that can withstand extreme environments, including high-temperature oxidation, to meet the rigorous demands of modern industrial applications.
Applications in Chemical Processing
Hastelloy C-276 is an essential material in the processing industries, renowned for its exceptional resistance to substances and durability. This nickel-molybdenum-chromium mixture is extensively used in manufacturing reactors, heat exchangers, and pipelines that handle highly corrosive substances such as sulfuric acid and hydrochloric acid. Its robust properties ensure longevity and reliability, making it invaluable in environments where harsh chemicals are present.
The alloy’s versatility extends to its application in various sectors, including pharmaceuticals and petrochemicals, where it supports processes involving aggressive media. ‘For example, HRS, a prominent provider of heat exchangers, focuses on utilizing substances similar to the alloy for effective thermal transfers in demanding materials, including those with high viscosity or fouling potential.’. They have seen significant global sales growth, with a 60% increase in turnover in 2022, driven by the demand for robust and reliable thermal processing solutions.
Furthermore, the rising focus on energy efficiency in production has emphasized the significance of materials such as a certain corrosion-resistant alloy. Its durability contributes to the longevity of systems, reducing the need for frequent replacements and associated downtime. As the industry moves towards more sustainable practices, the material’s ability to withstand extreme conditions without degradation is proving to be a significant advantage.
In essence, the exceptional chemical resistance and adaptability of this alloy make it an indispensable asset in the chemical processing industry, ensuring both operational efficiency and long-term reliability.
Fabrication and Welding Considerations
Hastelloy C-276 offers excellent performance characteristics, but its fabrication and welding require specific considerations. The mixture can be welded using traditional techniques, though it is often advised to include pre-heat and post-weld heat treatment processes to reduce residual stresses and avoid distortion. As Dr. Griffiths noted in his research, understanding the dynamics of thin oxide films that form on alloys during the casting process is crucial. This knowledge can significantly impact the welding and fabrication approach, ensuring optimal performance.
Proper handling during fabrication is essential to maintain Hastelloy C-276’s corrosion-resistant properties. Contamination or exposure to certain environments can degrade these properties, making stringent quality control vital. As seen in the automation and assembly sectors, continuous monitoring and analysis of production data help identify trends or potential areas for improvement, ensuring reliability and consistency in end products.
In the context of high-end manufacturing, such as the marine industry or advanced air mobility markets, these considerations become even more critical. For example, Smoker Craft’s long-standing commitment to innovation and quality underscores the importance of maintaining high standards in material handling and fabrication. Thus, understanding these considerations is essential for engineers and manufacturers to ensure optimal performance in end applications.
Conclusion
Hastelloy C-276 is essential for industries that demand exceptional corrosion resistance and high-temperature performance. Its unique composition, with significant nickel, molybdenum, and chromium content, allows it to effectively combat pitting and stress corrosion cracking, making it invaluable in sectors such as chemical processing, pharmaceuticals, and petrochemicals.
The alloy’s ability to maintain mechanical integrity under extreme conditions enhances operational efficiency and aligns with the industry’s focus on energy-efficient manufacturing. As the demand for reliable materials grows, Hastelloy C-276 stands out for its durability, minimizing downtime and ensuring long-term reliability in critical applications.
To fully leverage its advantages, meticulous fabrication and welding practices are crucial. Implementing pre-heat and post-weld heat treatments helps preserve its superior properties, while stringent quality control measures prevent contamination. These considerations are particularly vital in high-stakes industries like marine and advanced air mobility, where optimal performance and safety are paramount.
In summary, Hastelloy C-276 exemplifies engineering excellence, meeting the rigorous demands of various industrial applications. Its remarkable resistance to corrosion and high temperatures, combined with proper handling techniques, solidifies its role as a strategic choice for procurement managers focused on operational efficiency and sustainability in critical processes.