Blogs
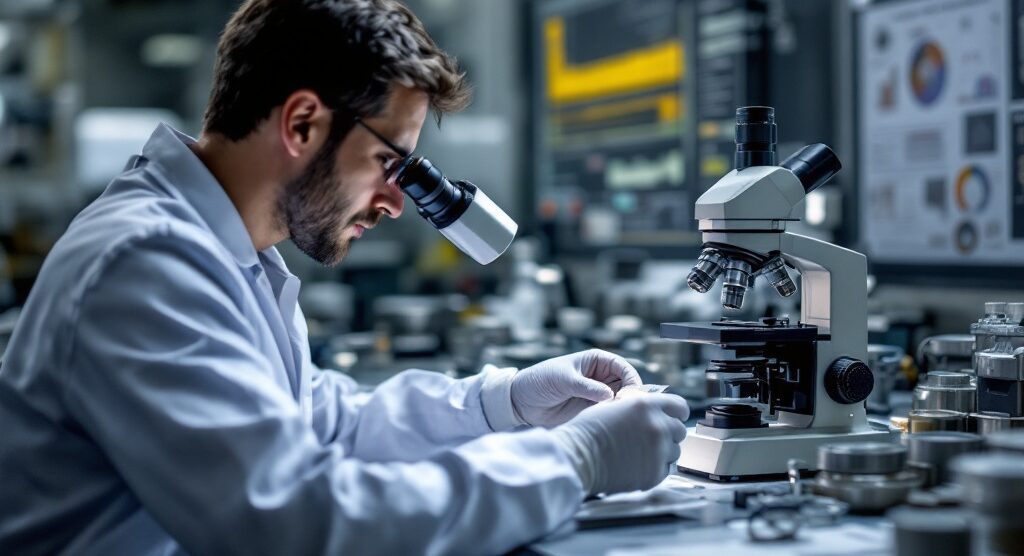
What is Monel K400? Understanding Its Properties and Applications
Introduction
In the realm of advanced materials, Monel K400 stands out as a premier nickel-copper alloy, celebrated for its remarkable properties that cater to a wide array of demanding applications. With a composition rich in nickel and copper, this alloy boasts exceptional corrosion resistance and mechanical strength, making it an indispensable choice in industries ranging from marine engineering to aerospace. As organizations seek materials that can withstand extreme environments and aggressive chemicals, Monel K400’s versatility is increasingly recognized.
From its impressive tensile strength to its adaptability in machining processes, this alloy not only meets but exceeds the rigorous demands of modern manufacturing and engineering. By delving into the characteristics, applications, and comparative advantages of Monel K400, procurement managers can make informed decisions that enhance operational efficiency and ensure the longevity of critical components.
Introduction to Monel K400: Definition and Characteristics
The monel k400, which is a nickel-copper alloy, is famous for its remarkable resistance to corrosion and notable mechanical durability, making it a flexible option for a range of uses. This alloy typically comprises approximately 67% nickel and 28% copper, along with trace amounts of iron, manganese, carbon, and silicon. This distinctive composition grants the alloy with superior properties, including formidable mechanical strength with a tensile strength (annealed) of 517-620 MPa, yield strength of 172-345 MPa, and a modulus of elasticity of 179 GPA.
Its high melting point, coupled with excellent weldability, further solidifies its status as a preferred choice in critical sectors such as marine engineering, oil refining, and chemical manufacturing, where its robustness is essential for maintaining performance integrity under challenging conditions. Recent advancements in additive manufacturing also emphasize the evolving adaptability of nickel-copper alloys, as noted by Prof. Bo Chen:
‘Learn how additive manufacturing is revolutionizing structural integrity in safety-critical industries.’
Additionally, case studies on machining monel k400 demonstrate that carbide tools are required, with specific suggested starting rates for various processes, ensuring optimal machining performance and quality in manufacturing processes.
With its exceptional corrosion resistance and high conductivity, this alloy is an excellent choice for demanding applications. Explore our extensive product catalog at Domadia to discover the perfect copper nickel alloy for your project needs.
Key Properties of Monel K400: Composition and Mechanical Attributes
The mechanical characteristics of this alloy are heavily influenced by its chemical composition. This alloy demonstrates impressive mechanical strength, with a tensile strength of approximately 70,000 psi (about 480 MPa) and a yield strength of 25,000 psi (approximately 170 MPa) for annealed bars. Such characteristics underline its durability and ability to resist deformation under stress.
Furthermore, this alloy boasts an elongation percentage ranging from 40% to 50%, indicating significant ductility, which is crucial for uses requiring flexibility. Notably, this alloy exhibits exceptional resistance to pitting and stress corrosion cracking, making it particularly valuable in marine environments and other corrosive conditions. In comparison, copper nickel alloys excel in marine engineering, where their corrosion resistance surpasses that of stainless steel, particularly in seawater uses, making them ideal for components such as ship hulls and offshore platforms.
Additionally, copper nickel alloys are preferred in automotive systems for brake lines and hydraulic systems due to their durability and reliability. They also find use in electronics, heat exchangers, and coinage, where their resistance to corrosion and wear is essential. Prof. Bo Chen highlights the relevance of these properties, stating, ‘Learn how additive manufacturing is revolutionizing structural integrity in safety-critical industries.’
This combination of properties positions this alloy as a favored option for uses that require materials able to endure both extreme temperatures and harsh chemical exposure, as demonstrated by its usage in the case study on additive manufacturing and structural integrity.
Applications of Monel K400: Where and Why It Is Used
This versatile alloy, monel k400, is used widely across numerous sectors, including marine, chemical processing, and aerospace. Its exceptional corrosion resistance makes it particularly effective for components exposed to seawater, such as pumps and valves, which are critical in marine environments. Recent studies indicate a growing market demand for monel k400 in marine applications, driven by its reliability in harsh conditions.
In the realm of chemical processing, monel k400 is favored for its superior ability to withstand aggressive chemicals, making it ideal for heat exchangers and piping systems. Significantly, thrust force under cryogenic conditions is roughly 8% greater than under dry cutting, emphasizing the material’s performance in extreme environments. Moreover, the aerospace industry employs monel k400, a nickel-copper alloy, in components that necessitate both high strength and resistance to extreme conditions, including engine parts and exhaust systems.
The case study titled ‘Optimal Machining Parameters for 400 Superalloy’ demonstrates the practical uses of this alloy, employing finite element analysis to determine optimal machining parameters while focusing on minimizing carbon emissions. The strategic advantages of this alloy underscore its value, as highlighted by Murat Sarikaya from Sinop University, who states that its unique properties make it indispensable for critical applications. Furthermore, recent advancements in machining processes for nickel-based superalloys, including a specific type, have been investigated through three-dimensional thermo-mechanical FEM analyses using AdvantEdge® software.
As sectors keep advancing in 2024, this alloy remains a highly desired substance, highlighting its significance in preserving operational efficiency and safety.
Comparative Analysis: Monel K400 vs. Monel K500
Both types K400 and K500 are acknowledged for their nickel-copper composition; however, they have unique traits that affect their uses. K500, with its added aluminum and titanium, is engineered to provide improved strength and hardness, making it a perfect selection for challenging environments, such as aerospace uses where extreme strength is essential. In contrast, monel K400 is recognized for its ductility and ease of machining, making monel K400 more appropriate for uses that require complex fabrication and weldability.
Its specific heat capacity is 430 J/kg-K, while K500 has a slightly higher specific heat capacity of 440 J/kg-K, highlighting their thermal properties.
This alloy is particularly advantageous in marine settings due to its remarkable corrosion resistance and flexibility during processing. Current trends suggest that monel K400 is increasingly being employed in particular applications such as pump shafts and impellers, leveraging its durability characteristics. However, AEETHER CO., LIMITED advises, “If the performance is sufficient, it is recommended to select alloy 400 to reduce costs.”
This viewpoint corresponds with the results from the case study titled ‘Cost Considerations for Alloys,’ which demonstrates how the simpler manufacturing process of one variant compared to the more expensive alternative makes it a more cost-effective option for uses that do not require the enhanced durability of its equivalent. Therefore, grasping the comparative characteristics of the alloy K500 and its counterpart is crucial for procurement managers seeking to enhance material selection based on performance, cost, and usage requirements.
Advantages of Monel K400: Benefits in Various Applications
Monel K400 is celebrated for its exceptional characteristics, including superb corrosion resistance, high strength, and excellent weldability, making it a perfect choice for diverse applications across numerous sectors. Its superior performance in harsh environments significantly reduces maintenance costs, contributing to a longer service life for components and ultimately enhancing overall operational efficiency. For instance, in aerospace applications during the 1960s, a particular alloy was pivotal in the construction of experimental rocket planes like the North American X-15, where its ability to endure extreme heat was critical.
This historical context underscores the effectiveness in demanding conditions. Additionally, RotoSound’s introduction of a special alloy for electric bass strings in 1962 highlights its versatility and adaptability in different manufacturing processes. As Sam Bush of Gibson Guitar Corporation observed, ‘These strings provide a distinct sound quality that improves performance,’ further reinforcing the alloy’s reputation in both musical and industrial uses.
Significantly, the attributes of this alloy, including its non-sparking features, render it appropriate for application in explosive settings, conforming to the standards for Non-Sparking Tools. This adaptability not only streamlines operations but also supports existing systems. Cumulatively, these advantages lead to a reduced total cost of ownership, making Monel K400 a compelling choice for industries that prioritize durability, reliability, and cost-effectiveness.
Conclusion
Monel K400 emerges as a leading choice in the landscape of advanced materials, celebrated for its exceptional properties that cater to a diverse array of industrial applications. With its impressive composition of nickel and copper, Monel K400 delivers unparalleled corrosion resistance and mechanical strength, making it indispensable in sectors such as:
- Marine engineering
- Chemical processing
- Aerospace
The alloy’s ability to withstand extreme environments while maintaining operational integrity reinforces its value across critical applications.
The comparative analysis with Monel K500 further highlights Monel K400’s unique advantages, particularly in terms of:
- Ductility
- Ease of machining
- Cost-effectiveness
As procurement managers evaluate material options, understanding these distinctions is crucial for optimizing performance while balancing budgetary considerations. Monel K400’s adaptability in machining processes and compatibility with additive manufacturing further underscore its relevance in modern manufacturing practices.
Ultimately, the strategic advantages of Monel K400 not only enhance operational efficiency but also ensure the longevity of components in demanding environments. As industries evolve, the continued recognition of Monel K400’s properties positions it as a vital material for the future, meeting the rigorous demands of today and tomorrow’s engineering challenges.