Blogs
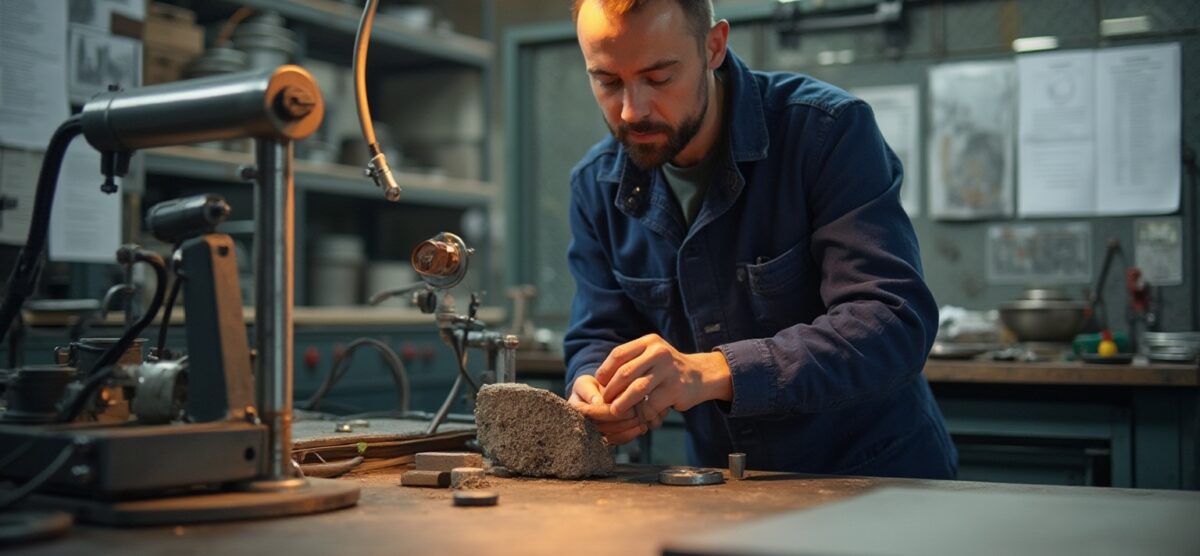
How to Choose the Right Monel K500 Equivalent: A Step-by-Step Guide
Overview
To choose the right Monel K500 equivalent, procurement managers should follow a structured approach that includes defining application requirements, researching equivalent alloys, and evaluating compliance standards. The article supports this by outlining specific steps such as conducting supplier assessments and testing for mechanical and corrosion resistance, ensuring that the selected material meets both performance and industry standards for various applications.
Introduction
In the realm of advanced materials, Monel K500 stands out as a formidable nickel-copper alloy, celebrated for its exceptional strength and remarkable resistance to corrosion, particularly in harsh marine environments. Its unique properties, such as high tensile strength and thermal stability, make it an essential choice for industries ranging from aerospace to chemical processing.
However, the challenge for procurement managers lies in navigating the complexities of selecting the right equivalent materials that can match or exceed the performance of Monel K500. This article delves into the critical properties of Monel K500, outlines a systematic approach for identifying suitable equivalents, and explores the diverse applications where these materials excel.
By understanding the nuances of procurement and testing protocols, professionals can ensure that their selections not only meet stringent industry standards but also enhance operational efficiency and longevity in demanding environments.
Understanding Monel K500: Properties and Specifications
This nickel-copper alloy is distinguished by its remarkable strength and superior corrosion resistance, particularly in marine environments. Its key characteristics that render it essential in various sectors include:
- Corrosion Resistance: This alloy displays exceptional resistance to seawater and a broad range of acids, making it an ideal selection for marine engineering and chemical processing.
- Mechanical Strength: With a yield strength that can surpass 690 MPa (100,000 PSI) when age-hardened, it provides high tensile strength, positioning it as suitable for demanding uses in oil and gas production and aerospace.
- Thermal Stability: This alloy retains its strength even at high temperatures, which is crucial for uses such as heat exchangers in energy sectors.
- Weldability: Although this alloy can be welded using conventional methods, it is advisable to conduct pre- and post-weld heat treatments to enhance performance and prevent issues.
- Magnetic Properties: While this alloy is not entirely non-magnetic, it demonstrates very low magnetic permeability, making it virtually non-magnetic in most conditions.
Understanding these characteristics is vital for procurement managers when evaluating potential equivalents, particularly the Monel K500 equivalent, as they significantly influence the suitability of the alloy for specific uses across diverse industries, including automotive, electronics, and pulp and paper production. At Domadia, we provide a wide variety of copper nickel alloys customized to fulfill different usage requirements, guaranteeing you have access to outstanding products like Monel. We encourage you to explore our extensive product catalog to find the perfect solution for your project needs.
Furthermore, insights from machining factors for this alloy indicate that while machining is easier in its annealed state, post-age-hardening, the material becomes harder, making machining more challenging. Proper techniques are essential to accommodate dimensional changes and prevent stress corrosion cracking. These machining factors are essential for procurement choices, as they can influence the selection of alloys in real-world uses.
Real-world applications of this alloy highlight its effectiveness in environments where durability and corrosion resistance are paramount.
Selecting the Right Equivalent: A Step-by-Step Approach
To select the most appropriate equivalent to Monel K500, procurement managers should adhere to the following structured steps:
Define Application Requirements: Clearly identify the specific operational conditions for the material, including temperature ranges, pressure levels, and potential exposure to corrosive environments. This foundational understanding is crucial for making informed decisions.
Research Equivalent Alloys: Investigate alloys that match or surpass the characteristics of Monel K500. Notable equivalents include Inconel 625, Hastelloy C-276, and Monel K500 equivalent, all of which provide comparable corrosion resistance and mechanical strength, making them suitable alternatives. Additionally, consider the Coefficient of Thermal Expansion for Alloy K500, which is 13.4 x 10^-6 μm/m·K, to ensure compatibility with thermal conditions in your projects.
Evaluate Compliance Standards: Confirm that the selected equivalent alloy complies with relevant industry standards and certifications such as ASTM or ISO. Adherence to these standards ensures the quality and reliability of various applications.
Conduct Supplier Assessments: Thoroughly evaluate potential suppliers by considering their market reputation, reliability, and ability to provide comprehensive documentation for the products offered. Establishing long-term partnerships with trusted suppliers can significantly enhance procurement efficiency and reduce risks.
Request Samples: Prior to committing to a bulk order, it is prudent to request samples of the equivalent alloy. This step allows for performance testing and validation, ensuring that the material meets your specific performance criteria.
Analyze Cost vs. Quality: Assess the total cost of ownership, which includes procurement, processing, and lifecycle costs. This analysis enables a balanced decision that weighs cost against quality, ultimately supporting long-term project success.
Consider Magnetic Properties: Be aware that while most alloys of this type are non-magnetic, they may become slightly magnetic in certain environments after long-term use or cold working. This consideration may affect the selection process based on the intended use.
Reference Case Studies: Utilize insights from relevant case studies, such as the one titled “Hydro-abrasive Disintegration of Alloy K-500,” which analyzes how various technological and abrasive factors impact the surface quality of K-500. Such information can provide valuable context for understanding the performance and processing of the alloy.
In addition to these steps, it’s essential to consider the advantages of copper nickel alloys, particularly their high resistance to corrosion in marine environments and their excellent thermal and electrical conductivity. These properties, along with good ductility and ease of fabrication, make copper nickel alloys a superior option over stainless steel for certain uses. Specifically, their corrosion resistance outperforms that of stainless steel in harsh environments, while their thermal and electrical conductivity is unmatched.
Moreover, their antimicrobial properties enhance their suitability for environments where hygiene is paramount. By following this systematic approach, procurement managers can confidently choose the most appropriate alternative to the specified alloy, including the Monel K500 equivalent, ensuring that their projects meet both performance and compliance standards. As noted by industry experts,
Versatility: Easily fabricated, welded, and machined, making it a top choice for manufacturers
a testament to the adaptability of these alloys.
Furthermore, the advantages discussed are sourced from the FAQ context, reinforcing the credibility of the information presented.
Identifying Applications for Monel K500 Equivalents
Monel K500 equivalents are integral to several critical applications due to their exceptional properties, particularly in the following sectors:
Marine Engineering: These alloys excel in environments exposed to seawater, making them ideal for components such as pumps, valves, and fittings. Their superior corrosion resistance ensures longevity and reliability in marine applications, where material degradation can lead to costly failures.
Aerospace: In the aerospace sector, a specific alloy is employed in components that require high strength and durability against severe operating conditions. This alloy’s tensile strength reaches up to 110 ksi, with a yield strength of 50 ksi and an elongation of 20% in 2 inches. The aging process, conducted at temperatures between 900°F and 1050°F after solution annealing, further enhances these properties. As noted by Hejun Hu, “the increase in hardness and tensile strength of the heat-treated samples is attributed to the precipitation hardening effect,” making this alloy a preferred choice for aerospace engineers.
Oil and Gas: The alloy is well-suited for downhole tubing and valves, essential for withstanding high pressures and corrosive environments typical in oil and gas extraction. Its ability to resist stress corrosion cracking, particularly when properly heat-treated, further enhances its suitability for these applications.
Chemical Processing: The Monel K500 equivalent is used in equipment that interacts with aggressive chemicals, ensuring durability and reliability in processes that would otherwise pose significant risks to less resilient substances. However, it is important to note that only annealed material resists stress cracking in the presence of mercury or mercury salts, and the alloy should not be used for nitric acid service.
Understanding these applications allows procurement managers to make informed decisions that align with specific industry requirements. The recent study titled ‘Hydro-abrasive Disintegration of Alloy K-500’ underscores the importance of technological and abrasive factors in enhancing surface quality, providing valuable insights for improving manufacturing processes. Ultimately, choosing the appropriate resources is crucial for optimizing performance and ensuring longevity in demanding environments.
Testing and Validation of Equivalent Materials
To ensure that the chosen substance equivalent to Monel K500 meets stringent performance standards, particularly in applications where high-temperature resistance and electrical insulation are critical, it is imperative to implement a comprehensive testing and validation protocol:
- Mechanical Testing:
- Initiate a series of mechanical tests, including tensile tests, yield strength tests, and hardness assessments.
These evaluations will confirm that the substance satisfies the requisite mechanical properties, essential for its intended use in environments where Mica Tape products are utilized.
Corrosion Testing:
- Conduct accelerated corrosion tests to assess the substance’s resistance in specific corrosive environments.
This step is crucial to ensure compatibility with system requirements, especially in industries prone to corrosive challenges, similar to those faced by Mica Tape in electrical insulation scenarios.
Thermal Testing:
- Assess the substance’s performance at elevated temperatures to verify its stability and strength retention under high-temperature conditions.
This testing is vital for applications where thermal exposure is a factor, paralleling the high-temperature resistance offered by Mica Tape products.
Documentation Review:
- Ensure that all testing results are meticulously documented and compliant with relevant industry standards, such as ASTM B 865 and NACE MR 0103.
This practice facilitates traceability and accountability, which are critical in selection processes, including those involving Mica Tape.
Field Testing:
- Whenever feasible, conduct field tests in real-world conditions to validate the performance of the chosen equivalent substance in situ.
This practical approach offers invaluable insights into how the substance behaves under actual operating conditions, similar to the performance of Mica Tape in electrical insulation applications and the Monel K500 equivalent materials.
Machining Considerations:
- It is important to note that machining is best performed on annealed or hot-worked substances, with age-hardened items also being finish-machined to close tolerances.
For instance, when finishing in the hardened condition, a feed of 0.13 mm/rev, cutting speed of 35 m/min, and depth of cut of 1.02 mm are recommended for optimal results, similar to machining considerations for Mica Tape products.
Case Study Reference:
- A pertinent case study on Grade K heat exchanger tube coating varieties demonstrates the use of these testing methods.
- This study emphasizes various advanced coating solutions that enhance the longevity and efficiency of heat exchangers in industrial environments, drawing parallels with the durability and reliability of Mica Tape in similar uses.
By following these rigorous testing protocols and incorporating these considerations, procurement managers can confidently choose substances that will perform reliably in their specific applications, including those involving Mica Tape, thereby reducing the risk of failure and minimizing associated costs.
Building Strong Supplier Relationships
To cultivate robust relationships with suppliers of Monel K500 equivalents, particularly in the context of mica tape procurement, procurement managers should adopt the following strategic approaches:
Open Communication: Establishing transparent and consistent channels of communication with mica tape suppliers is essential. This allows for the clear discussion of expectations, quality standards, and timely identification of potential issues, thereby fostering trust and collaboration.
Collaborative Problem Solving: Engaging in joint problem-solving initiatives with mica tape suppliers can significantly enhance partnerships. By collaborating to tackle challenges unique to high-temperature substances, both parties can discover mutually advantageous solutions that strengthen their cooperative spirit.
Long-Term Agreements: Establishing long-term agreements with mica tape suppliers can be beneficial in obtaining favorable pricing and ensuring a stable supply of resources. Such agreements not only provide predictability in procurement but also strengthen the supplier relationship by demonstrating commitment. In fact, the best SRM teams drive 39% more supplier innovation by leveraging supplier innovation events consistently.
Performance Reviews: Regular assessments of mica tape supplier performance are crucial. Assessing key metrics such as quality, delivery timelines, and responsiveness enables procurement managers to guarantee that suppliers consistently fulfill their operational requirements and expectations, particularly for specialized products like mica tape.
Feedback Mechanism: Instituting a feedback system encourages a culture of continuous improvement. By sharing insights with mica tape suppliers about their performance and potential areas for enhancement, procurement managers can foster an environment that values growth and responsiveness.
As Kodiak Hub emphasizes, “as Procurement Teams around the world start to understand the massive value SRM can bring, our guess is that the SRM software category will soon be included in all of CRM’s.” By prioritizing these strategies, procurement managers can significantly bolster their supply chain efficiency and secure consistent access to high-quality mica tape materials, ultimately enhancing their overall procurement effectiveness. Furthermore, the case study titled “Reinforcing supplier relationship management best practices” illustrates how strategic supplier relationships are tested amid economic disruptions, necessitating a focus on best practices in supplier relationship management.
Conclusion
Monel K500 is a remarkable nickel-copper alloy that excels in both strength and corrosion resistance, making it indispensable across various industries, especially in marine, aerospace, and chemical processing applications. Its unique properties, such as exceptional mechanical strength and thermal stability, are critical for ensuring durability in harsh environments. However, the challenge for procurement managers lies in identifying suitable equivalent materials that can deliver comparable performance while adhering to industry standards.
A systematic approach to selecting appropriate alternatives involves:
- Defining application requirements
- Researching equivalent alloys like Inconel 625 and Hastelloy C-276
- Evaluating compliance with industry standards
Additionally, conducting thorough supplier assessments and requesting material samples are essential steps to ensure the selected alloys meet specific performance criteria. Implementing rigorous testing and validation protocols further guarantees that the chosen materials will perform reliably in demanding applications.
Ultimately, understanding the properties and applications of Monel K500 and its equivalents empowers procurement professionals to make informed decisions that enhance operational efficiency and material longevity. By fostering strong supplier relationships and leveraging strategic procurement practices, managers can secure high-quality materials that not only meet but exceed the rigorous demands of their industries. This comprehensive approach ensures that projects remain on track, ultimately leading to successful outcomes in challenging environments.