Blogs
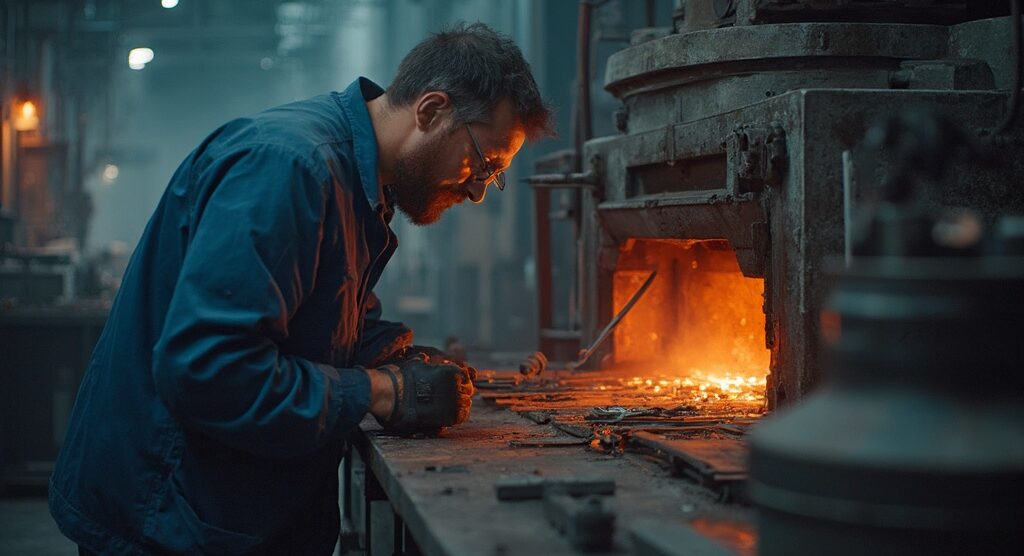
How to Perform Heat Treatment on Invar 36: A Step-by-Step Guide
Overview:
The article provides a detailed step-by-step guide on performing heat treatment on Invar 36, emphasizing the importance of each stage—from preparation and heating to quenching, tempering, and inspection. This guide is supported by explanations of how each step optimizes the alloy’s mechanical properties, such as tensile strength and dimensional stability, which are crucial for its applications in precision instruments and aerospace components.
Introduction
Invar 36, a unique nickel-iron alloy, stands out in the realm of precision engineering due to its exceptional low thermal expansion properties. Comprising 36% nickel and 64% iron, this alloy is indispensable in industries where dimensional stability is paramount, such as aerospace and electronics. The ability to maintain performance under fluctuating temperatures makes Invar 36 a preferred choice for critical applications, from precision instruments to cryogenic systems.
As the demand for high-quality materials intensifies, understanding the intricacies of heat treatment processes becomes crucial for enhancing the mechanical properties of Invar 36. This article delves into the essential aspects of Invar 36, including its properties, heat treatment techniques, challenges, and diverse applications, providing procurement managers with the insights needed to make informed material selections that meet stringent industry standards.
Understanding Invar 36: Properties and Applications
The nickel-iron alloy known as 36, which consists of 36% nickel and 64% iron, is celebrated for its exceptional low thermal expansion characteristics, featuring a Modulus of Elasticity of 21.0 psi x 10. This characteristic makes it particularly advantageous for precision instruments and components utilized within the aerospace and electronics sectors. The alloy’s stability under fluctuating temperatures allows its use in critical environments, such as precision gauges, optical instruments, and cryogenic systems.
Comprehending the fundamental characteristics of alloy 36 is crucial, as they directly affect its invar 36 heat treatment response and overall performance in practical uses. Recent advancements highlight its growing importance in aerospace, where precision and reliability are paramount. The DOMADIA Group, a trusted supplier of Nickel Molybdenum Iron Alloy and special metals such as Copper, Titanium, and Rare Earths since 1952, ensures that you have access to high-quality materials that embody superior corrosion resistance, excellent mechanical properties, and high-temperature stability.
Our commitment to customer satisfaction means we prioritize your needs and provide detailed specifications, lead times, and pricing upon request. Additionally, effective handling techniques, such as those outlined in the case study ‘Tapping Techniques,’ recommend using a slightly larger tap drill than standard to accommodate metal flow, which can prevent binding and enhance thread quality when working with a specific alloy.
Step-by-Step Guide to Heat Treatment of Invar 36
Preparation: Begin by thoroughly cleaning the Invar 36 components to eliminate any contaminants that may affect the Invar 36 heat treatment process. Utilize an appropriate solvent or cleaning solution to ensure a pristine surface, which is critical for achieving optimal results.
Heating: Preheat the furnace to a temperature range of 900-1100°C (1652-2012°F). This specific range is crucial for developing the desired microstructure of the alloy, contributing to its unique characteristics, including a Modulus of Elasticity (Annealed) of 21.0 psi x 10.
Soaking: Once the furnace reaches the target temperature, introduce the components and allow them to soak for 1-2 hours. The exact duration should be adjusted based on the thickness of the substance to ensure uniform temperature distribution throughout the components.
Quenching: After the soaking period, swiftly remove the components from the furnace and quench them in a suitable medium, such as oil or water. This swift cooling method is crucial for securing the preferred characteristics of 36. Metallurgist Markus Merkel emphasizes that effective quenching techniques are vital for achieving a minimum and stable coefficient of thermal expansion, which enhances the material’s performance in various applications.
Tempering: The next step involves tempering the components at a lower temperature, ideally between 300-500°C (572-932°F), for approximately one hour. This step is crucial for relieving internal stresses and enhancing the toughness of the alloy, making it more resilient in its applications.
Cooling: Allow the components to cool gradually to room temperature. Controlled cooling is important to maintain dimensional stability and prevent any warping or distortion.
Inspection: Once the components have cooled, conduct a thorough inspection to identify any signs of distortion or defects. This quality assessment is essential to confirm that the components fulfill the necessary specifications and are prepared for their intended uses.
Recent developments in Invar 36 heat treatment methods suggest that utilizing a three-step heat treatment greatly enhances the soft magnetic characteristics of alloy 36, including reduced coercivity and heightened saturation magnetization. Case studies on heat treatment processes for specific alloys demonstrate the effectiveness of various temperature settings and cooling rates, reinforcing the importance of following these guidelines to achieve optimal stability.
The Role of Heat Treatment in Enhancing Mechanical Properties
Invar 36 heat treatment is pivotal in optimizing the mechanical properties of alloy 36, yielding significant enhancements in tensile strength, hardness, ductility, and toughness. This process begins a transformation in the microstructure of alloy 36, enhancing a more uniform grain distribution that is crucial for performance. Specifically, during heating, the alloy undergoes structural changes that are locked in through quenching, while tempering effectively alleviates any residual stresses that may arise.
Notably, the selenium content in Free-Cut ’36’ Alloy is 0.20%, which plays a role in its performance characteristics. Furthermore, the modulus of elasticity for Free-Cut Invar ’36’ Alloy is recorded at 20.5 ksi, offering a clearer understanding of the substance’s mechanical characteristics. The result is a substance that not only demonstrates remarkable dimensional stability in the face of temperature variations but is also well-suited for high-precision applications.
Recent studies corroborate these findings, demonstrating that invar 36 heat treatment can lead to substantial improvements in tensile strength and ductility, which are vital for industries requiring exacting standards. As expressed by engineer Daining Fang, comprehending these mechanical properties is vital for procurement managers assigned with choosing substances suited to particular operational requirements. Furthermore, case studies, such as the one titled ‘Programmable Poisson’s Ratio in Mechanical Metamaterials,’ highlight the tangible benefits of invar 36 heat treatment, showcasing how such processes have led to enhancements in tensile strength and overall alloy performance, thereby reinforcing the strategic importance of this knowledge in material selection.
Challenges and Considerations in Heat Treating Invar 36
Heat treating alloy 36 presents a range of challenges, notably the risks of warping or cracking that can stem from rapid temperature fluctuations. These issues are particularly concerning given that warping rates in heat-treated alloy 36 can reach alarming levels if not properly managed. To effectively mitigate these risks, it is vital to maintain a consistent heating rate and to avoid any thermal shock during the process.
The selection of quenching medium is another essential factor that can affect the final characteristics of the alloy; for example, oil quenching is typically less aggressive than water quenching, thereby decreasing the potential for distortion. Markus Merkel emphasizes that the ‘Minimum and Stable Coefficient of Thermal Expansion by Three-Step Heat Treatment of Invar 36‘ indicates that careful invar 36 heat treatment can lead to more stable characteristics. The material displays minimal fluctuations in its coefficient of thermal expansion (CTE) value between 0.5 and 0.6 × 10 /°C up to 150 °C, underscoring its stability during invar 36 heat treatment.
Close temperature monitoring is crucial during invar 36 heat treatment, as even minor deviations can compromise mechanical characteristics. Furthermore, a thorough post-treatment inspection is recommended to detect any issues early, allowing for corrective measures to be implemented promptly. Recent case studies, such as the evaluation of the magnetic characteristics of a specific alloy 36, highlight the consequences of neglecting these precautions.
The study demonstrated that insufficient heat treatment can result in considerable performance issues, including a saturation magnetization increase to 130 emu/g and coercivity values from 20 One to 25 One, which are essential for aerospace uses demanding high precision. Furthermore, utilizing high-quality insulating materials, such as Mica Tape products, can enhance the overall performance of Invar 36 heat treatment in high-temperature applications. These tapes offer superior electrical insulation and thermal resistance, making them vital in uses such as fire-resistant cables and other critical electrical insulation systems.
Their distinctive characteristics, such as outstanding flame resistance and dielectric strength, guarantee that the integrity of the alloy is preserved during processing and operational use, especially in electrical engineering contexts.
Applications of Heat-Treated Invar 36 in Industry
The invar 36 heat treatment of alloy 36 is a critical process in industries requiring exceptional dimensional stability and minimal thermal expansion, achieving a low coefficient of thermal expansion (CTE) of 0.331 × 10 /°C through cold rolling. In the aerospace sector, its applications include:
- Engine mounts
- Precision instruments
where reliability and performance are non-negotiable. Recent innovations underscore its role in the electronics industry as well, where invar 36 heat treatment is commonly utilized in:
- Connectors
- Circuit boards
enhancing the functionality of sensitive devices.
Additionally, in environments with explosive potential, the use of Non-Sparking Tools becomes crucial, as they prevent ignition risks during operations involving certain alloys. Furthermore, Domadia’s Mica Tapes offer high-temperature electrical insulation solutions that can be advantageous alongside specific uses, while their Oxygen Free Copper (OFE/OHFC) is crucial for critical medical components, ensuring high conductivity and reliability. As noted by H.L., ‘All authors have read and agreed to the published version of the manuscript,’ which underscores the collaborative effort in advancing the understanding of Invar 36.
Furthermore, a comparative analysis can be drawn from the case study on the decomposition of cellular structure in selective laser melted Cu–Zn–Si silicon brass, which emphasizes the significance of material properties in diverse usages. By understanding these diverse applications and the importance of Non-Sparking Tools, procurement managers can make strategic sourcing decisions that align with industry standards and operational needs.
Conclusion
Invar 36, with its distinctive low thermal expansion properties, emerges as an invaluable asset in precision engineering across various critical industries. Its composition of 36% nickel and 64% iron not only bestows exceptional stability under temperature fluctuations but also enhances its suitability for high-stakes applications in aerospace, electronics, and cryogenic systems. The article underscores the significance of understanding Invar 36’s properties and the meticulous heat treatment processes that optimize its mechanical performance, including tensile strength, ductility, and toughness.
The step-by-step guide to heat treatment highlights the careful preparation, heating, soaking, quenching, tempering, and inspection required to achieve the desired characteristics. It is evident that addressing the challenges associated with heat treatment—such as warping and cracking—is crucial for maintaining the integrity of Invar 36. By adhering to stringent guidelines and employing effective techniques, procurement managers can ensure that the alloy meets the rigorous demands of its applications.
Ultimately, the strategic selection of Invar 36, bolstered by an understanding of its properties and heat treatment processes, empowers industries to achieve unparalleled precision and reliability. As the landscape of technology continues to evolve, the importance of high-quality materials like Invar 36 remains paramount, reinforcing its role as a cornerstone in the pursuit of excellence in engineering and manufacturing.