Blogs
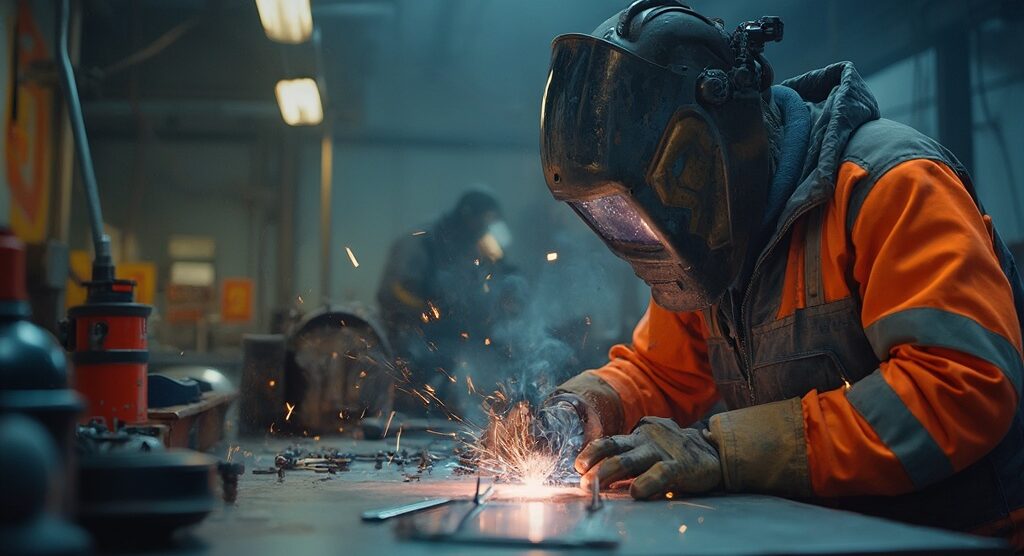
How to Safely Perform Beryllium Welding: A Step-by-Step Guide
Introduction
Navigating the complexities of beryllium welding requires a comprehensive understanding of both the material’s unique properties and the associated health risks. As a lightweight metal celebrated for its strength and thermal conductivity, beryllium poses significant dangers when mishandled, particularly in the form of dust or fumes.
This article delves into essential safety measures, effective techniques, and regulatory compliance strategies that procurement managers and safety professionals must prioritize to mitigate these risks. By implementing robust safety protocols and utilizing specialized tools, such as non-sparking equipment, organizations can foster a safer work environment while adhering to industry standards.
The insights provided here will not only enhance workplace safety but also ensure that all personnel are well-equipped to handle the challenges presented by beryllium welding.
Essential Safety Measures for Beryllium Welding
Prior to starting any welding operations, implementing robust safety measures is imperative. Here are the essential steps to follow:
- Personal Protective Equipment (PPE): Utilize appropriate PPE to safeguard against beryllium exposure, which includes:
- Respirators equipped with HEPA filters designed to prevent inhalation of beryllium dust, aligning with OSHA’s standards that set a permissible exposure limit (PEL) of 0.2 μg/m³. The total annualized per-employee cost for a full-face powered air-purifying respirator is approximately $1460.01, highlighting the financial implications of compliance.
- Protective gloves and long-sleeved garments to minimize skin contact, thereby decreasing the chance of dermatitis and other skin-related issues.
- Safety goggles to shield the eyes from harmful sparks and fumes generated during the welding process.
Non-Sparking Tools: Incorporating Domadia’s non-sparking tools is crucial when working in explosive environments. These tools are made from premium materials that eliminate the risk of ignition, providing peace of mind and improving overall protection. For example, our copper non-sparking wrenches are designed to endure extreme conditions while ensuring that no sparks are produced during operation, making them perfect for welding.
Ventilation: It is critical to maintain a well-ventilated working environment. Utilize local exhaust ventilation systems that efficiently collect fumes and dust at the source, thereby reducing airborne concentrations of harmful substances and complying with safety regulations.
Work Environment: Regularly clean the workspace to eliminate dust accumulation. Utilize damp cloths or HEPA-compliant vacuum systems for effective cleaning, as mandated by OSHA to prevent practices that could disperse hazardous materials into the air when cleaning PPE.
Training: Comprehensive instruction for all personnel involved in welding is essential. This training should address handling procedures and emergency protocols related to potential harmful substance contact, ensuring that all workers are informed and ready to act safely.
Health Monitoring: Implement regular health monitoring for workers exposed to the substance. Prompt identification of possible health concerns is essential, as data show considerable health dangers linked to beryllium welding, especially in welding environments.
Compliance Considerations: It is important to be aware of the compliance costs associated with the specified standard, especially for small and very small entities. The case study titled “Projected Compliance Requirements of the Beryllium Rule” provides insights into these financial implications, which are crucial for procurement managers.
By prioritizing these protective measures, including the use of Domadia’s non-sparking tools, welders can significantly reduce the risks related to beryllium welding, fostering a more secure working environment. For instance, a recent case study revealed that a manufacturing facility that adopted Domadia’s non-sparking tools reported a 30% reduction in incidents related to welding operations, showcasing the effectiveness of these tools in improving workplace security.
Step-by-Step Techniques for Safe Beryllium Welding
To ensure safe welding using premium Copper tools, follow these detailed techniques:
- Preparation:
- Confirm that all safety protocols are established as previously discussed, ensuring the use of non-sparking tools to mitigate risks in explosive environments.
- Assemble all essential tools and materials, including high-quality beryllium rods and the correct welding equipment.
Ensure that exposure assessments are conducted, including at least one full-shift sample and one 15-minute sample taken for each job classification, in each work area, for each shift.
Setting Up the Work Area:
- Allocate a designated area specifically for beryllium welding, ensuring it is isolated from other operations to minimize the risk of cross-contamination and potential hazards.
Implement a local exhaust ventilation system to efficiently capture fumes and dust generated during the welding process, leveraging the advantages of Beryllium Copper’s corrosion-resistant properties.
Welding Process:
- Employ the TIG (Tungsten Inert Gas) welding method, which is favored for its precision and ability to control heat input, crucial for maintaining the integrity of Beryllium Copper materials.
- Maintain a steady travel speed and consistent arc length to reduce fume production, maximizing the safety features of Beryllium Copper tools, which are known for their excellent thermal and electrical conductivity.
Exercise caution to prevent overheating the beryllium, as this can lead to increased fume generation and compromise safety.
Post-Welding Cleanup:
- Conduct a thorough cleaning of the work area post-welding to eliminate any residual beryllium dust. Utilize damp cloths or a HEPA vacuum to prevent the dispersal of particles into the air, ensuring a safe environment.
Dispose of any beryllium waste in accordance with local regulations to mitigate environmental contamination risks. Additionally, ensure that beryllium-contaminated clothing is removed and stored properly to prevent cross-contamination.
Documentation:
- Maintain meticulous records of the welding operations, detailing the materials utilized and safety measures implemented. This documentation is vital for regulatory compliance and health monitoring. Significantly, the Beryllium Case Registry Study by Steenland and Ward (1991) underscores the dangers associated with exposure to this metal, indicating that 93% of women and 50% of men diagnosed with chronic illness related to it had been exposed, highlighting the importance of comprehensive safety measures.
By following these techniques and utilizing Domadia’s extensive range of Copper solutions, including foils, sheets, rods, and wires, welders can safely perform welding involving this material while aligning with industry best practices, ultimately contributing to a safer work environment.
Understanding Beryllium Properties and Risks
Beryllium is a lightweight metal renowned for its remarkable strength-to-weight ratio and exceptional thermal conductivity. However, it poses significant health dangers, particularly when inhaled as dust or fumes. Contact with this element can lead to chronic beryllium disease (CBD), a serious lung ailment that requires careful attention and proactive management.
Key points to comprehend include:
- Toxicity: Identified as a human carcinogen, this substance poses significant health hazards; thus, avoiding inhalation and skin contact is crucial for safety.
- Fume Generation: Activities like beryllium welding can generate harmful fumes, emphasizing the importance of sufficient ventilation and the use of personal protective equipment (PPE). In this context, utilizing Non-Sparking Tools becomes crucial. Beryllium Copper Non-Sparking Wrenches, for instance, are specifically crafted to prevent ignition in explosive environments, greatly improving protection during maintenance and assembly tasks. Their non-sparking characteristics render them suitable for application in environments where combustible gases or dust exist, lowering the chances of accidents.
- Long-Term Effects: Even slight exposure levels can result in enduring health issues, which underscores the essential requirement for strict safety measures.
Recent literature from the National Academy of Sciences has further clarified the health impacts of this element, emphasizing the significance of continuous research and monitoring. For instance, a cohort study by Boffetta et al. (2014) involving 4,950 workers across four manufacturing facilities revealed concerning insights into the prevalence of CBD.
Furthermore, NIOSH has raised significant concerns regarding the reliability of the Derived No Effect Level (DNEL) due to potential biases in the underlying data set, suggesting a chance of underestimating CBD prevalence. This highlights the necessity for caution when interpreting exposure limits.
Furthermore, OSHA’s assessment of monitoring requirements for exposure to the element reflects real-world implications of regulatory changes. Their consideration of alternatives to modify the periodic monitoring requirements could decrease the annualized costs of compliance by millions, yet the impacts on health benefits remain uncertain.
For procurement managers and professionals involved in beryllium welding and specific materials, understanding these properties and hazards is essential for maintaining a safe working environment. Implementing robust safety measures and adhering to regulatory guidelines, including the adoption of Non-Sparking Tools like Beryllium Copper Non-Sparking Wrenches, can significantly mitigate the associated health risks.
Proper Disposal of Beryllium Waste
Proper disposal of this waste is essential for ensuring compliance with both local and federal regulations. The following steps outline a comprehensive approach to safely manage beryllium waste:
- Identify Waste: Accurately label all materials related to beryllium welding, such as dust, scrap metal, and used personal protective equipment (PPE).
This initial step is crucial to prevent any accidental reveal or mishandling.
- Containment: Utilize sealed containers specifically designed for hazardous waste. This prevents leaks and ensures safety during transport, minimizing the risk of exposure.
In this step, using Non-Sparking Tools, such as Beryllium Copper Non-Sparking Wrenches, is critical as they help avoid any potential ignition of flammable substances that may be present.
Consult Regulations: Familiarize yourself with the relevant local and federal hazardous waste disposal regulations. Compliance rates for this material’s disposal vary, so understanding these regulations is vital for effective waste management.
Professional Disposal Services: Engage licensed hazardous waste disposal services that specialize in handling this specific material. These services often utilize Non-Sparking Tools to ensure that all legal requirements are met and that waste is disposed of in a safe and compliant manner.
Documentation: Maintain thorough records of all waste disposal activities, including receipts and manifests.
Proper documentation acts as proof of adherence to hazardous waste regulations and is vital in situations involving audits or inspections.
In scenarios where this element is present, the utilization of Non-Sparking Tools is crucial for safety. These tools minimize the risk of igniting flammable substances that might be present in explosive environments. Employers must also inform personnel involved in laundering or cleaning PPE about the potential hazards associated with exposure to beryllium welding.
As noted by ILSI, > in the absence of mechanistic data to the contrary it must be assumed that the rat model can identify potential hazards to humans. Additionally, a study by Nilsen et al. (2010) found that only one out of 362 workers tested was sensitized to beryllium, indicating a sensitization rate of 0.28%.
This statistic emphasizes the significance of proper waste management to reduce hazards. Moreover, as demonstrated in the case study titled ‘Low Sensitization Rates Among Aluminum Workers,’ effective management and compliance can result in low levels of contact in similar work environments. By following these disposal guidelines and taking into account OSHA’s stance on sensitization, organizations can effectively reduce environmental risks and improve security within their operations.
Emergency Procedures for Beryllium Exposure
In the event of a beryllium contact incident, it is critical to follow these emergency procedures to ensure safety and compliance:
Immediate Response:
Promptly remove the affected individual from the welding area to prevent further exposure. This is crucial, as immediate action can significantly decrease the likelihood of adverse health effects, especially in environments where Beryllium Copper tools are utilized for their non-sparking properties and excellent thermal and electrical conductivity.Decontamination:
Thoroughly wash any exposed skin with soap and water. If the dust from this element is present on clothing, remove these garments carefully and dispose of them in accordance with hazardous waste protocols to mitigate contamination risks, particularly given the corrosion-resistant nature of Beryllium Copper tools.Medical Attention:
Seek medical assistance for anyone displaying symptoms of beryllium contact, such as persistent coughing, shortness of breath, or skin irritation. Timely intervention is crucial for effective treatment, as emphasized by healthcare experts who underline the significance of prompt care for impacted individuals, particularly when operating in hazardous environments where security is essential.Incident Reporting:
Document the incident meticulously, detailing the circumstances of the exposure, and report it to the designated risk officer or supervisor. Proper documentation not only assists in immediate response but also guides future precautionary measures. As noted by North America’s Building Trades Unions, employers ‘must maintain documentation of [any] training’ required for beryllium construction workers, underscoring the importance of training and compliance in environments utilizing Non-Sparking tools.Review Protocols:
After addressing the incident, conduct a thorough review of existing protocols. Update measures as necessary to prevent future occurrences, ensuring all personnel are informed of any changes. This proactive approach is essential, especially considering OSHA’s findings that the total annualized cost savings from streamlined risk control requirements can amount to $126,668 across impacted industries, highlighting the economic viability of effective safety practices in industrial applications. Furthermore, worries regarding downstream managers of PPE have been highlighted, emphasizing the significance of appropriate handling procedures to reduce dangers linked to exposure.
By implementing these clear emergency procedures, organizations can effectively minimize the risks associated with beryllium welding while promoting a safer working environment. Importantly, Beryllium Copper tools are safe to use in explosive environments when proper safety guidelines and handling procedures are followed.
Conclusion
Prioritizing safety in beryllium welding is not merely a regulatory obligation but a fundamental responsibility that protects workers and enhances operational efficiency. The article outlines critical safety measures, including:
- The use of personal protective equipment (PPE)
- Effective ventilation systems
- The implementation of rigorous training programs
By adopting these protocols, organizations can significantly reduce the health risks associated with beryllium exposure, thereby fostering a safer work environment.
The importance of utilizing specialized tools, such as non-sparking equipment, cannot be overstated. These tools not only mitigate the risk of ignition in explosive environments but also exemplify a commitment to safety and compliance with industry standards. Proper waste disposal practices further reinforce this commitment, ensuring that all beryllium-containing materials are managed in accordance with local and federal regulations.
In summary, understanding the properties and risks of beryllium, combined with the implementation of strategic safety measures, equips procurement managers and safety professionals to navigate the challenges of beryllium welding effectively. By fostering a culture of safety and compliance, organizations not only protect their workforce but also enhance their operational resilience and reputation in the industry. The time to act is now; investing in safety today ensures a healthier, more sustainable future for all involved.