Blogs
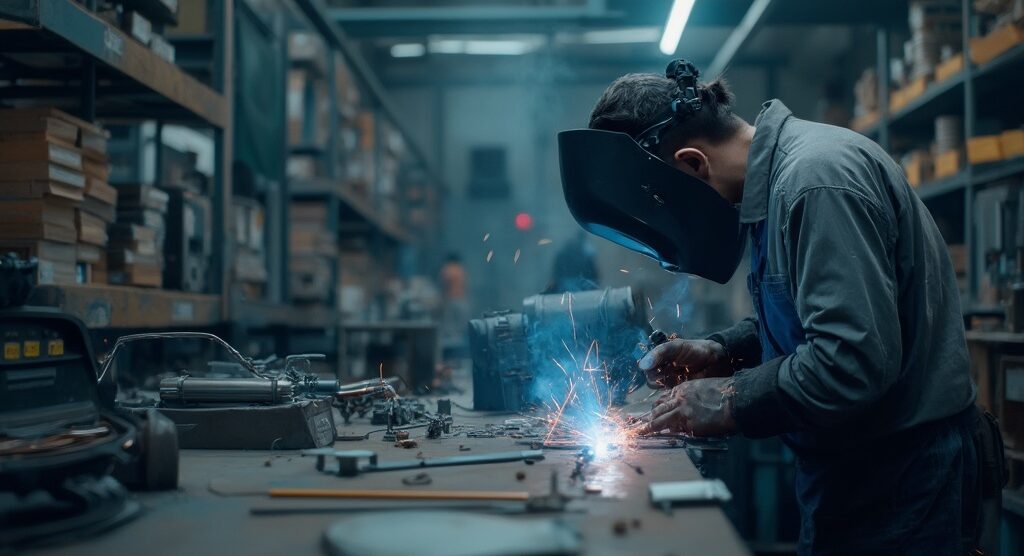
Understanding and Preventing Tungsten Inclusion in Welding: A Complete Tutorial
Introduction
In the intricate world of welding, maintaining the integrity of welds is paramount, especially in industries where safety and performance are non-negotiable. One of the most insidious threats to weld quality is tungsten inclusion, an issue that can stem from seemingly minor oversights in electrode maintenance or shielding gas application.
This article delves into the multifaceted challenges posed by tungsten inclusion, exploring its definitions, implications, and the critical need for effective prevention strategies. By understanding the underlying causes and adopting best practices, professionals can safeguard the quality of their welds, ensuring compliance with industry standards and enhancing the performance of welded components.
With insights drawn from recent studies and expert recommendations, this comprehensive guide equips welding professionals with the knowledge necessary to navigate and mitigate the risks associated with tungsten inclusion.
Understanding Tungsten Inclusion in Welding: Definition and Importance
The presence of metal particles in the joint, often referred to as tungsten inclusion in welding, occurs due to the unintended occurrence of these particles within the bead, typically resulting from insufficient cleaning of the electrode or inadequate shielding gas coverage. Based on recent data, defects in the material can arise in as much as 5% of joints, greatly affecting overall joint integrity. This contamination can lead to significant defects, including porosity and a reduction in ductility, which are often a result of tungsten inclusion in welding, ultimately compromising the mechanical properties of the weld.
Such defects are particularly concerning in high-stakes industries, such as automotive and aerospace, where material integrity is critical for safety and performance. For example, in aerospace applications, the presence of this element can negatively influence the reliability of structural components, resulting in possible failures under stress. As noted by Sandler et al. (2019), ‘The presence of metallic particles can drastically reduce the fatigue life of welded joints, making proper electrode maintenance essential.’ Grasping the effects of tungsten inclusion in welding is essential for welders and engineers alike, as it directly affects the quality and dependability of welded structures. A case study titled ‘Analysis of Optimizer Performances Across Models’ emphasizes that proper cleaning and shielding practices can minimize metal contamination defects, thereby improving overall joint quality.
By adopting best practices—such as ensuring thorough cleaning of electrodes and optimal shielding gas application—professionals can effectively minimize the occurrence of foreign material, thereby enhancing overall weld quality.
Effective Strategies for Preventing Tungsten Inclusion in Welding
To effectively prevent metal inclusion in welding, consider the following strategies:
Proper Cleaning of the Electrode: Ensure that the electrode is free of contaminants before use. Use a dedicated grinder for tungsten and avoid using the same grinder for other materials to prevent cross-contamination.
Optimizing Shielding Gas Coverage: Maintain proper gas flow rates and ensure that the shielding gas encompasses the entire joint area. This is particularly important in orbital joining, where the gas coverage can be challenging due to the geometry of the weld joint.
Managing Joining Parameters: Adjust joining parameters such as current and voltage to appropriate levels. Overheating can lead to excessive melting of the metal and potential inclusion.
Regular Equipment Maintenance: Conduct routine inspections and maintenance of joining equipment to ensure proper function. This includes checking for leaks in the gas delivery system and ensuring that the torch is in good condition.
Training and Best Practices: Offer continuous education for metal workers on optimal techniques and the effects of contamination on joint quality. This guarantees that all staff are informed of the problems and understand how to alleviate them efficiently.
By applying these techniques, welding experts can greatly diminish the likelihood of foreign material contamination, resulting in superior joints and enhanced functionality of joined components.
Identifying Signs of Tungsten Inclusion in Welds
Welds affected by metal inclusion often show several recognizable signs that experts should observe closely:
- Visual Inspection: Irregularities on the surface of the bead, such as pitting, craters, or rough textures, may indicate tungsten inclusion in welding. Employing consistent visual inspection techniques is crucial, as studies show that systematic visual checks can effectively identify anomalies, reinforcing the integrity of the welding process. As articulated by J.H. Jack in the J. Iron Steel Inst., maintaining rigorous inspection protocols is imperative for achieving optimal joint integrity.
- Microstructural Analysis: Conducting metallographic examinations allows for a detailed assessment of the joint’s microstructure. Sophisticated microscopy methods can uncover metal particles, thereby clarifying their influence on mechanical characteristics. Significantly, studies employing artificial neural networks (ANN) for estimating geometry and mechanical characteristics of bead joints have demonstrated consistent error ranges with results associated with metallic particles, highlighting the dependability of such evaluations. The recent X-ray Diffraction (XRD) analysis of weld regions demonstrated significant differences in phase composition and grain structure between the fusion zone and heat-affected zones, providing deeper insights into the microstructural changes associated with metal inclusions.
- Mechanical Testing: Implementing tensile and impact tests on welded samples can provide critical insights. A decrease in ductility or toughness often signifies the existence of metallic particles, which are recognized stress concentrators that undermine material integrity.
- Non-Destructive Testing (NDT): Utilizing NDT methods, such as ultrasonic testing or X-ray inspection, is essential for detecting internal flaws related to tungsten inclusion in welding. The recent analysis of bead-on-plate short-circuiting GMA joints has shown that these techniques are effective in evaluating the microstructural features, contributing to enhanced joint quality. In particular, the SHAZ measurement for Sample 2 was recorded at 793 μm, highlighting the significance of these evaluations in maintaining joint integrity.
In explosive environments, the use of Non-Sparking Tools is critical to prevent ignition risks. These tools serve as the best alternative for non-sparking applications, ensuring safety while performing tasks that could potentially cause explosions. For instance, using Non-Sparking Tools during welding operations minimizes the risk of igniting flammable materials in the vicinity. Additionally, it is essential for procurement managers to consider suppliers and manufacturers of high-temperature materials, such as electrical insulation papers and fabrics, to complement their safety protocols in hazardous environments. By being vigilant and employing these identification techniques, procurement managers can proactively manage the quality of their welds, ensuring compliance with industry standards and significantly enhancing overall performance.
The Role of Material Selection in Preventing Tungsten Inclusion
Selecting the appropriate substances is crucial in avoiding contamination. Consider the following factors:
Compatibility: Ensure that the filler material is compatible with the base metals being welded.
Mismatches can lead to increased risk of entries and defects.Cleanliness: Select materials that are free of contaminants such as oils, dirt, or oxides.
Clean materials assist in minimizing the likelihood of metallic contaminants during the welding process.Alloy Composition: Understand the alloying elements present in the materials, as certain elements can affect the probability of specific metal presence.
For instance, high carbon content can worsen incorporation issues.Supplier Quality Assurance: Work with suppliers like DOMADIA, which offers Beryllium Copper and Oxygen Free Copper (OFE/OHFC) that comply with international standards (UNS, ASTM).
DOMADIA employs rigorous testing and inspection processes to ensure that each product meets the highest industry standards.
Their dedication to quality ensures that the materials provided are dependable and function outstandingly, thus lowering the chance of tungsten inclusion in welding.
By emphasizing material choice and partnering with trustworthy suppliers who follow rigorous quality control standards, professionals can lessen the risk of tungsten inclusion in welding and improve the overall quality of their welded items. Additionally, consider related products such as electrical insulation papers and high-temperature fabrics, which can further support the integrity of the joining process.
Continuous Improvement and Quality Assurance Practices
To cultivate a robust culture of quality and continuous improvement within joining processes, organizations should consider the following strategic practices:
Implement Quality Management Systems (QMS): Establish a comprehensive QMS that incorporates detailed procedures for monitoring joining processes, ensuring compliance with industry standards, and diligently documenting occurrences of tungsten inclusion in welding. This structured approach not only enhances operational efficiency but also facilitates compliance with regulatory requirements. According to recent statistics, organizations that implement effective QMS can see a reduction in defect rates by up to 30%, showcasing the impact of structured quality management.
Conduct Regular Audits: Engage in systematic internal audits of fabrication practices and supplier performance. These audits are essential for identifying potential areas for improvement and ensuring strict adherence to established quality standards. Consistent evaluation helps to uncover inefficiencies and fosters a culture geared towards excellence. For instance, a case study from a leading fabrication firm demonstrated that regular audits led to a 25% improvement in compliance with quality standards over a year.
Encourage Feedback and Reporting: Foster a transparent atmosphere where welders can communicate concerns related to metal contamination or other flaws without fear of retaliation. This proactive approach encourages problem-solving and knowledge sharing, enabling teams to address challenges swiftly and effectively, thereby enhancing overall process quality. A recent survey highlighted that companies with strong feedback mechanisms reported a 40% increase in defect resolution speed.
Invest in Training and Development: Offer ongoing education for fabrication staff centered on the most recent methods, technologies, and best practices intended to avoid material contamination and maintain quality standards. This investment not only elevates workforce competency but also reinforces a commitment to quality assurance throughout the organization. Recent advancements in training tools, as reported by Durable’s news on AI tools, can significantly enhance the learning experience for professionals in the field.
By integrating these continuous improvement practices, organizations can significantly reduce the incidence of tungsten inclusion in welding and enhance the overall quality and reliability of their operations. The implementation of effective quality management strategies is critical in navigating the complexities of modern welding environments.
Conclusion
Understanding and addressing tungsten inclusion is crucial for maintaining the integrity and performance of welds across various high-stakes industries. This article has explored the definition and implications of tungsten inclusion, revealing its potential to compromise mechanical properties and safety standards. By implementing effective strategies such as:
- Proper electrode cleaning
- Optimizing shielding gas applications
- Controlling welding parameters
professionals can significantly mitigate the risks associated with this defect.
Identifying the signs of tungsten inclusion through:
- Visual inspection
- Microstructural analysis
- Non-destructive testing
is essential for ensuring weld quality. Coupled with careful material selection and robust quality assurance practices, these measures create a comprehensive approach to preventing tungsten inclusion. The emphasis on continuous improvement and training further empowers welding teams to uphold high standards of quality, thereby enhancing the reliability of welded components.
Ultimately, a proactive stance on tungsten inclusion not only ensures compliance with industry standards but also bolsters the overall performance of welded structures. By prioritizing best practices and fostering a culture of quality, organizations can safeguard their operations against the risks posed by tungsten inclusion, paving the way for safer and more effective welding outcomes.