Blogs
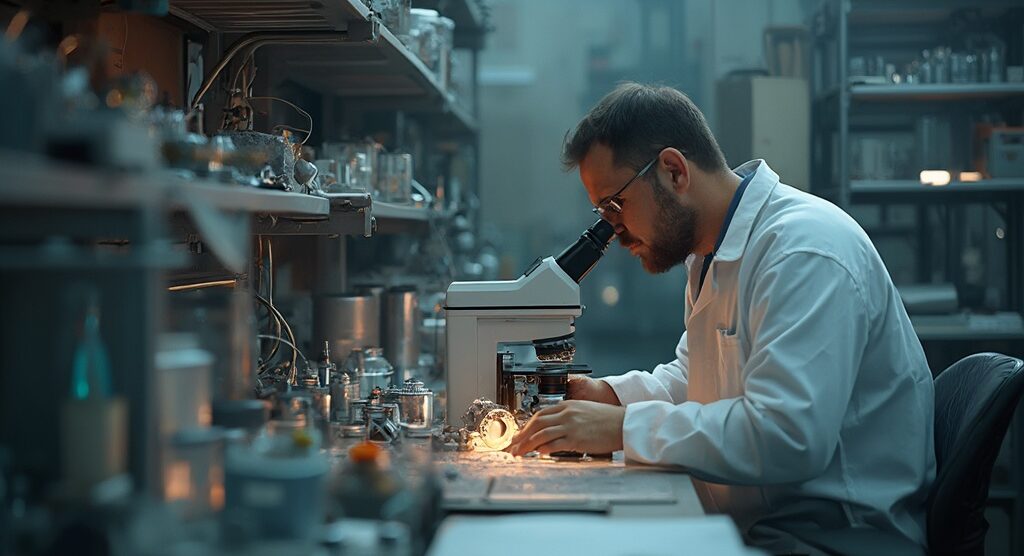
Understanding Inconel 625 Temperature Limits: A Complete Tutorial
Introduction
Inconel 625 stands out as a premier choice for industries that operate under extreme conditions, thanks to its unique composition and exceptional properties. This nickel-chromium alloy not only excels in corrosion resistance but also maintains impressive mechanical stability at high temperatures, making it indispensable in applications ranging from aerospace to chemical processing.
With a careful balance of nickel, chromium, and molybdenum, Inconel 625 has earned its reputation as a “superalloy,” capable of withstanding the rigors of demanding environments. As industries increasingly seek materials that ensure reliability and durability, understanding the nuances of Inconel 625—from its fabrication techniques to its performance characteristics—becomes essential for procurement managers and engineers alike.
This article delves into the key attributes of Inconel 625, exploring its composition, temperature limits, corrosion resistance, and optimal applications, providing valuable insights for those navigating the complexities of material selection in high-stakes environments.
Overview of Inconel 625: Composition and Key Properties
Inconel 625 is a highly regarded nickel-chromium alloy, celebrated for its outstanding mechanical properties and exceptional durability against oxidation and corrosion. Its composition typically comprises:
- 58% nickel
- 20% chromium
- 8% molybdenum
- Trace amounts of iron, niobium, and other elements
This strategic combination significantly enhances the alloy’s strength, enabling it to perform exceptionally well within the inconel 625 temperature limits in extreme conditions.
Significantly, the alloy’s ability to withstand wear and fatigue under high-stress environments is vital for industries such as aerospace and chemical processing, particularly when considering the inconel 625 temperature limits for ensuring reliability and durability. Similarly, DOMADIA’s Nickel Molybdenum Iron Alloy, which contains approximately:
- 65% nickel
- 15% molybdenum
- 20% iron
offers superior corrosion protection, excellent mechanical properties, and high-temperature stability, making it an ideal choice for demanding applications. Curtis Bligh, Head of Marketing at Excell Metal Spinning Ltd., effectively conveys the essence of the alloy 625, mentioning that it has justly earned its reputation as a ‘superalloy.’ Recent advancements in its composition, especially the rise in chromium and molybdenum levels during the 1960s to 22% and 9%, respectively, have greatly enhanced its ability to withstand corrosion, confirming its status as one of the most adaptable alloys worldwide.
Furthermore, machining this alloy presents moderate to difficult challenges due to its rapid work hardening and high shear strengths. Recommendations for effective processing include:
- Using rigid machines
- Sharp tools
- Appropriate lubricants
with a typical milling feed of 0.005-0.008 inches to enhance tool life and maintain cutting efficiency. In environments where sparking poses a risk, incorporating Non-Sparking Tools becomes crucial for safety, providing reliable alternatives designed for explosive potential scenarios.
Additionally, DOMADIA offers Mica Tape products that provide high-temperature resistance and electrical insulation, further enhancing safety and performance in various industrial uses.
Temperature Limits and Performance of Inconel 625 in High-Temperature Applications
Alloy 625 demonstrates impressive mechanical stability at elevated temperatures, maintaining its properties up to approximately 1,800°F (982°C). However, exceeding the inconel 625 temperature limits may compromise its strength and creep resistance, which are two essential characteristics for applications that demand high performance under extreme conditions. The significance of operational environments cannot be overstated; understanding the inconel 625 temperature limits is crucial as prolonged exposure to high temperatures can adversely affect the alloy’s performance.
Recent studies underscore these challenges, revealing that at 650 °C and 500 MPa, the time to rupture for Inconel 625 is about 23.6 hours, indicating the alloy’s limitations under sustained stress. Notably, dynamic recrystallization has been observed in specimens tested at 800 °C, leading to smaller equiaxial grains and the absence of carbides at grain boundaries, which further influences its performance. In uses such as gas turbine components and heat exchangers, a thorough understanding of the inconel 625 temperature limits is crucial for ensuring both safety and efficiency.
Furthermore, Mica Tape products from Domadia provide exceptional high-temperature durability and electrical insulation, rendering them perfect for essential uses in sectors such as aerospace and automotive. Their superior insulation properties ensure reliability and durability, enhancing the performance of components exposed to extreme conditions. Specifically, these Mica Tapes are utilized in the production of fire-resistant cables and other essential electrical insulation systems, offering outstanding flame protection and dielectric strength.
Furthermore, DOMADIA’s Nickel Molybdenum Iron Alloy stands out with exceptional strength, corrosion resistance, and thermal stability, making it a favored selection for critical uses. A case study titled ‘High-Temperature Tensile and High Cycle Fatigue Properties of Alloy 625’ reveals that hot isostatic pressed LPBF Alloy 625 has a lower high-cycle fatigue limit of 500 MPa compared to 550 MPa for wrought 625, attributed to higher sulfur content affecting its fatigue endurance at 650 °C. As Renato Baldan observes in his research, ‘Recognizing the inconel 625 temperature limits and thermal performance characteristics is vital for its effective use in demanding environments.
Corrosion Resistance and Thermal Stability of Inconel 625
Alloy 625 is famous for its remarkable ability to withstand corrosion, especially in tough conditions that involve acids, saltwater, and different corrosive substances. The alloy’s unique composition enables it to withstand pitting and crevice corrosion effectively, making it an ideal material for marine and chemical processing uses. Based on recent discoveries, alloy 625 exhibits remarkable corrosion protection capabilities, which are essential for durability in challenging environments.
Notably, it can be fabricated to a minimum detail size of 0.4 mm, enhancing its applicability in precision environments. Furthermore, its thermal stability is noteworthy; the alloy retains its structural integrity even when subjected to high temperatures and reactive substances, which are within the inconel 625 temperature limits, making it suitable for use in extreme conditions. This combination of properties not only highlights its effectiveness but also shows its reliability in practical uses, such as in offshore platforms and chemical processing equipment, where durability is paramount.
Additionally, customization options such as hand polished or electropolished finishes are available on request, allowing for tailored solutions to meet specific project requirements. Specialist views on the corrosion durability of alloy 625 further confirm its excellence, with practical instances demonstrating its effectiveness in marine uses and chemical processing machinery.
Fabrication Techniques and Heat Treatment for Optimal Inconel 625 Performance
To achieve optimal performance from this alloy, it is crucial to employ specific fabrication techniques, particularly in welding and machining. Utilizing the appropriate filler materials and welding methods is vital for preserving the alloy’s integrity. Significantly, the welding of Alloy 625 can be effectively performed using gas-shielded processes with tungsten or consumable electrodes, eliminating the need for post-weld heat treatment to preserve corrosion durability.
This method ensures that the mechanical properties of the welds align with those of the base metal, provided that standard welding practices are adhered to. Furthermore, heat treatment processes such as solution annealing play a significant role in enhancing the mechanical properties of this alloy, particularly its strength and resistance to stress corrosion cracking. The typical rupture strength of alloy 625 at 1600°F (871°C) for 10 hours is 12 ksi (83 Mpa), which underscores its strong performance within the inconel 625 temperature limits for high-temperature applications.
Additionally, the use of Non-Sparking Tools, such as brass or aluminum wrenches and non-sparking hammers, during fabrication is essential in explosive environments, ensuring safety while working with certain materials. Non-destructive testing methods, such as magnetic particle flaw detection and ultrasonic flaw detection, are essential for identifying defects or cracks in the alloy, ensuring its integrity. Furthermore, obtaining high-quality electrical insulation materials, including high-temperature fabrics and papers from trusted providers like 3M, Dupont, and Insulflex, enhances the performance of certain alloys in crucial uses.
Adopting best practices during fabrication, as demonstrated in the case study on the weldability of Alloy 625, is essential to ensure that the alloy meets the stringent performance standards required.
Applications of Inconel 625: From Aerospace to Chemical Processing
Inconel 625 is a vital material in high-temperature uses, adhering to specific inconel 625 temperature limits, across various sectors, especially in aerospace and chemical processing. In aerospace, its remarkable properties make it ideal for components such as turbine blades and combustion chambers, where resistance to extreme thermal conditions is paramount. The alloy’s excellent weldability, attributed to its low carbon and high nickel content, facilitates the creation of complex geometries essential for these applications.
According to aerospace engineers, the use of alloy 625 has significantly enhanced the performance and reliability of engine components under demanding operational conditions. Notably, Alloy 625 contains niobium in a range of 3.15-4.15%, which contributes to its strength and corrosion resistance. In the chemical processing sector, this alloy excels in environments characterized by corrosive agents and high temperatures, within the inconel 625 temperature limits.
It is commonly employed in heat exchangers, reactors, and piping systems, where understanding inconel 625 temperature limits ensures its resilience, longevity, and safety. The chemical composition of Alloy 625 can vary slightly depending on the specific grade and manufacturer, which is an important consideration for engineers specifying materials for projects. Recent studies have highlighted the alloy’s adaptability, providing real-world examples of its successful application in chemical processing systems that require reliable and durable materials.
For example, the case study titled ‘Influence of Tools and Cutting Strategy on Milling Conditions’ explores how various tools and strategies impact milling conditions and quality, providing valuable insights into optimizing processes involving a specific alloy. With its unique properties, this alloy remains a preferred choice for industries that demand materials capable of performing consistently under pressure. As Witold Brostow observed in his assessment of variations for horizontal thin walls constructed from Nickel Alloy 625, the material’s performance in different uses remains a central theme of research and development.
It’s important to note that while Inconel 625 is widely used, Mica Tape products provide exceptional high-temperature resistance and electrical insulation, making them ideal for critical applications in electrical engineering and other high-temperature environments.
Conclusion
Inconel 625 proves to be an invaluable asset across a multitude of industries due to its exceptional composition and properties. With a strategic blend of nickel, chromium, and molybdenum, this superalloy excels in high-temperature environments, showcasing remarkable mechanical stability and corrosion resistance. Its ability to withstand extreme conditions makes it indispensable for applications ranging from aerospace components to chemical processing equipment.
The alloy’s resistance to oxidation and corrosion, coupled with its impressive thermal stability, highlights its reliability in demanding settings. Understanding the specific temperature limits and the importance of proper fabrication techniques is essential for maximizing the performance of Inconel 625. The insights on welding methods and machining practices further reinforce the need for strategic approaches in material handling to ensure the integrity and longevity of components made from this alloy.
As industries continue to prioritize safety, durability, and efficiency, Inconel 625 stands out as a premier choice. Its proven track record in high-stress environments, complemented by effective fabrication methods, positions it as a leading material for engineers and procurement managers alike. By leveraging the unique properties of Inconel 625, organizations can enhance their operational capabilities, ensuring that their applications meet the rigorous demands of today’s industrial landscape.