Blogs
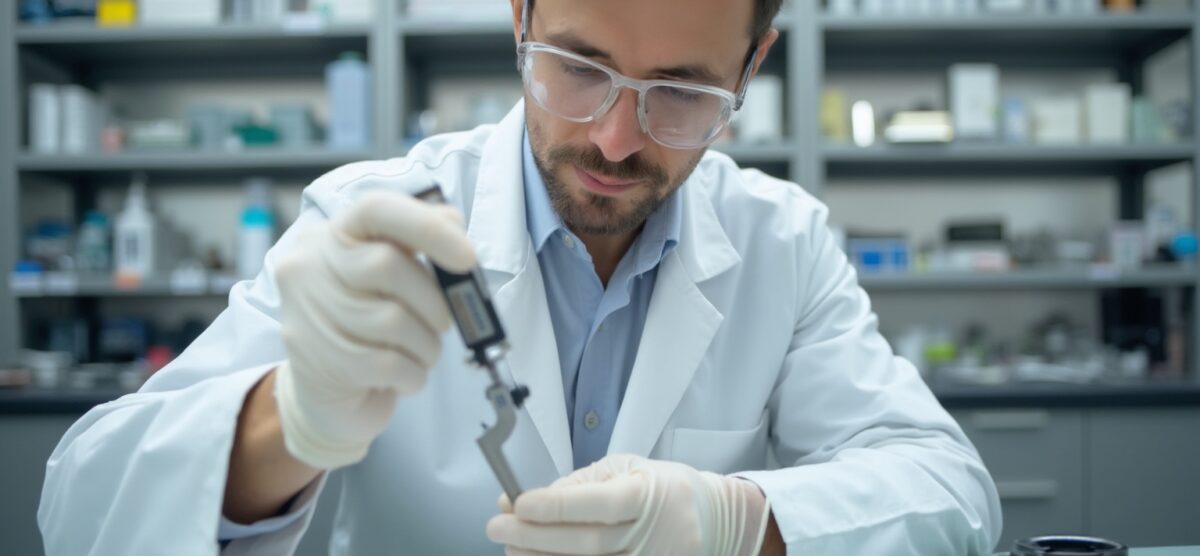
Understanding Invar Young’s Modulus: A Complete Tutorial on Properties and Applications
Overview:
Understanding Invar Young’s modulus is essential as it measures the rigidity of Invar alloys, which exhibit low thermal expansion and are crucial for precision applications in sectors like automotive and aerospace. The article discusses how specific compositions of Invar alloys, such as Alloy 36, demonstrate Young’s modulus values between 140 to 180 GPA, highlighting their importance in high-precision contexts where dimensional stability and mechanical properties are paramount.
Introduction
In the realm of advanced materials, Invar alloys stand out for their remarkable properties, particularly their exceptional dimensional stability and minimal thermal expansion. These characteristics make them indispensable in high-precision applications across various industries, including aerospace, automotive, and electronics.
As procurement managers navigate the complexities of material selection, understanding the nuances of Young’s modulus and the performance attributes of Invar alloys becomes crucial. From evaluating the mechanical properties to implementing effective sourcing strategies, this article delves into the critical aspects that influence the successful procurement of Invar alloys.
By exploring their applications, comparing them with other materials, and outlining best practices for sourcing, it provides valuable insights that can enhance decision-making and optimize supply chain efficiency in demanding environments.
Understanding Young’s Modulus in Invar Alloys
Invar young’s modulus, often denoted as E, measures the rigidity of solid substances and is particularly important in relation to certain materials, which are known for their low thermal expansion characteristics. These alloys typically exhibit an invar young’s modulus within the range of 140 to 180 GPA, influenced by their specific compositions. Alloy 36, for example, has a diameter range from Ø 3 mm up to 280 mm, demonstrating its adaptability in different uses.
Comprehending the precise values of invar young’s modulus is essential for use in sectors like automotive and electronics, where exact dimensional stability is paramount. Recent research has highlighted the directional Young’s moduli of specific alloys fabricated through laser powder-bed fusion, demonstrating variations of up to 20 GPA, with the highest stiffness found in orientations parallel to the fabrication process. The case study titled ‘Thermal Expansion and Invar Young’s Modulus’ found that the coefficient of thermal expansion is nearly orientation-independent, which is crucial for high-precision applications.
Procurement managers must consider these characteristics to select materials that align with performance requirements, thereby optimizing both quality and cost. As Wido Glombitza, Business Unit Manager for Medical, Aerospace, and Industry, observes,
This nickel iron mixture is tough, versatile and retains good strength at cryogenic temperatures.
Furthermore, as Sergej Baričević highlights, the advancement of calibration techniques is essential for guaranteeing accuracy in uses involving specialized metals.
This statement emphasizes the significance of invar young’s modulus in material selection, especially in high-precision contexts where performance under various loads is essential.
Applications of Invar Alloys
These materials are essential for uses that require outstanding dimensional stability, especially in precision instruments, aerospace parts, and electronics. Their unique property of minimal thermal expansion makes them ideal for manufacturing measuring devices such as gauges and thermometers, which must operate accurately under fluctuating temperatures. In aerospace, the properties of this alloy are crucial in the fabrication of satellite components, where maintaining structural integrity amid temperature variations is imperative.
Recent findings from Mossbauer experiments at 4.2 K have demonstrated high-spin to low-spin transitions in Fe–Ni and Fe–Pt compositions, showcasing their unique properties. Additionally, the typical hardness for ½ hard alloy material ranges from 84 to 88 on the Rockwell B scale, indicating their robustness. As mentioned in recent discussions on precision instruments, the adoption of effective sourcing strategies is essential for procurement managers to secure high-quality metal mixtures tailored to project specifications.
Significantly, progress in precipitation-hardened Invar alloys, such as Fe–Ni–Co–Ti, has resulted in improved mechanical properties, further reinforcing the importance of invar young’s modulus in challenging uses. The insights offered by specialists, including Yong’s observation that the most commonly utilized tool substances in the aerospace sector were summarized in Section 3.1, emphasize the significance of comprehending these uses. This knowledge enables procurement professionals to strategically source materials that align with their operational needs and enhance supply chain efficiency.
Additionally, hybrid tools employing specialized alloys and composites are emerging as promising solutions, achieving a balance between service life, movability, and efficiency, especially in future aerospace uses.
Comparing Invar with Other Alloys
When assessing this material in relation to other alloys like stainless steel and aluminum, it is essential to examine several key properties:
- Thermal expansion coefficients
- Mechanical strength
- Corrosion resistance
This alloy, known for its remarkably low thermal expansion, excels in scenarios requiring high precision and dimensional stability. This feature minimizes the risks of distortion in sensitive instruments, a hallmark of Charles Guillaume’s Nobel Prize-winning discovery in 1920, which enabled the creation of extremely accurate scientific instruments.
Furthermore, the low magnetic permeability of this alloy restricts its use in magnetic fields, as it does not hold significant magnetism when subjected to an external field, emphasizing an important factor for particular purposes. While stainless steel demonstrates superior corrosion resistance, Invar’s thermal stability can outweigh this advantage in precision environments. Conversely, copper nickel alloys provide remarkable corrosion resistance, particularly in marine environments, along with excellent thermal and electrical conductivity, good ductility, and antimicrobial properties—rendering them ideal for uses where hygiene is paramount.
Additionally, their ease of fabrication further enhances their appeal for various applications. Mechanical strength statistics reveal that this alloy typically exhibits a yield strength of around 280 MPa, compared to stainless steel’s 250 MPa and aluminum’s 70 MPa, which highlights its robust nature in the context of invar young’s modulus. On the other hand, aluminum offers a lighter and more malleable option; however, it lacks the dimensional stability that this material is recognized for.
Grasping these distinct properties—alongside the unique features of copper nickel alloys—is essential for procurement managers, as it allows them to evaluate the trade-offs and choose the most appropriate options tailored to their specific application needs.
Sourcing Invar Alloys: Best Practices
Effectively obtaining specific metals requires a systematic and tactical approach. Recent innovations include modified Invar alloys with enhanced mechanical properties and corrosion resistance, emphasizing the relevance of invar young’s modulus and the importance of staying updated with advancements in substances. Essential to this process is the assessment of suppliers according to their certifications and adherence to international standards, which guarantees that products meet the necessary quality benchmarks.
Establishing long-term relationships with dependable suppliers not only enhances pricing negotiations but also fosters mutual trust, leading to improved quality assurance over time. In this context, Mica Tape products play a significant role, particularly for applications requiring high-temperature resistance and electrical insulation, making them essential for procurement managers to consider. Regular audits of suppliers serve as a critical practice to verify that they uphold high standards consistently.
Furthermore, leveraging technology, such as advanced procurement software, can significantly streamline the sourcing process. This technology enables better tracking of supplier performance and material quality, ultimately enhancing forecasting efficiency. By following these best practices, procurement managers can ensure a robust supply chain that takes into account invar young’s modulus for Invar alloys and Mica Tape products, setting the foundation for successful long-term partnerships.
Additionally, the complexities involved in supplier evaluation can be illustrated by exploring strategies like those mentioned in the case study on balancing utility and privacy in machine learning, emphasizing the need for a balanced approach in procurement practices.
Conclusion
Invar alloys are indispensable in high-precision applications due to their remarkable properties, including exceptional dimensional stability and minimal thermal expansion. Understanding Young’s modulus is crucial for procurement managers, as it directly impacts the performance of Invar alloys in sectors such as aerospace and electronics. The ability to evaluate mechanical properties, alongside the latest advancements in material technology, empowers professionals to make informed decisions that optimize both quality and cost.
The diverse applications of Invar alloys highlight their significance in precision instruments and aerospace components, where maintaining structural integrity under varying temperatures is paramount. As industries continue to evolve, the development of new alloy formulations demonstrates the ongoing innovation within this field, reinforcing the need for strategic sourcing practices. By comparing Invar with other materials, such as stainless steel and aluminum, procurement managers can better understand the unique advantages that Invar offers, particularly in terms of thermal stability and mechanical strength.
Ultimately, effective sourcing strategies are essential for securing high-quality Invar alloys tailored to specific project requirements. Establishing strong relationships with reliable suppliers and leveraging technology for tracking and quality assurance can greatly enhance supply chain efficiency. By adopting these best practices, procurement professionals can navigate the complexities of material selection with confidence, ensuring that their operations are well-equipped to meet the demands of high-precision environments.