Blogs
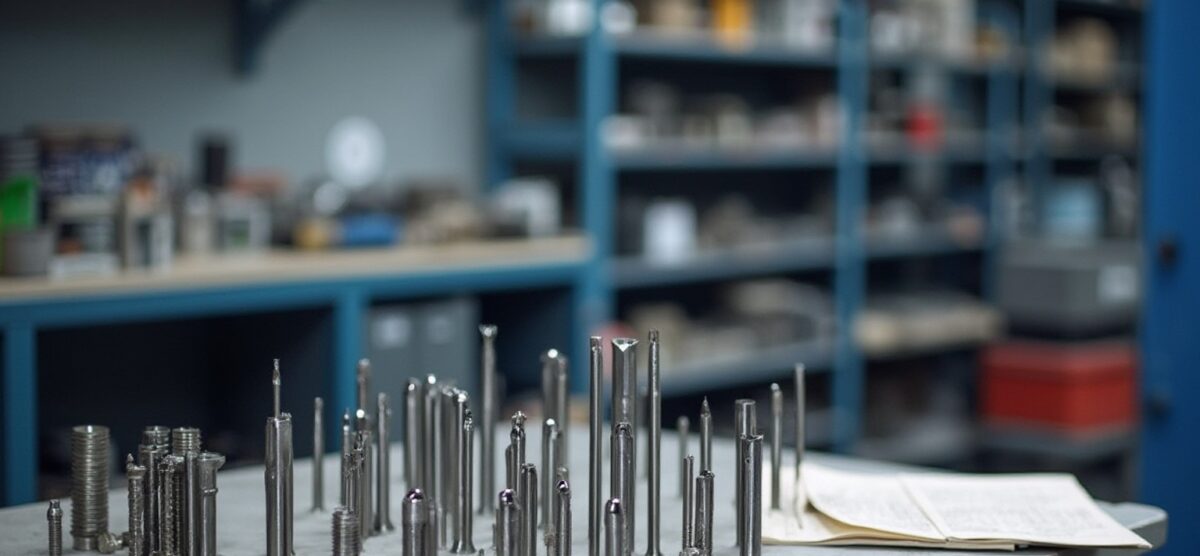
Understanding Monel Cotter Pins: A Complete Tutorial on Selection and Application
Overview
The article focuses on the selection and application of Monel cotter pins, highlighting their properties, benefits, and best practices for use in various industries. It emphasizes the importance of understanding the unique characteristics of these fasteners, such as their corrosion resistance and strength, while providing practical guidelines for selecting the right pins based on load requirements, environmental conditions, and installation methods to ensure reliability and safety in demanding applications.
Introduction
In the realm of fasteners, Monel cotter pins have emerged as a paramount choice for industries demanding exceptional durability and reliability. Crafted from a nickel-copper alloy, these fasteners are engineered to withstand the harshest environments, including marine, aerospace, and chemical applications. Their impressive corrosion resistance, coupled with the ability to endure extreme temperatures, positions them as a superior alternative to traditional materials.
This article delves into the properties and benefits of Monel cotter pins, offering a comprehensive guide to their selection, application, and maintenance. By exploring common applications and cost considerations, procurement managers can make informed decisions that enhance operational efficiency and reduce long-term expenses.
Understanding the nuances of Monel cotter pins is not merely an academic exercise; it is a strategic imperative for organizations aiming to optimize their fastening solutions in an increasingly competitive landscape.
Introduction to Monel Cotter Pins: Properties and Benefits
Nickel-copper alloy fasteners, designed for their exceptional corrosion resistance and high strength, are especially well-suited for demanding environments, particularly in marine and chemical uses. These cotter pins exhibit an impressive ability to endure temperatures ranging from cryogenic conditions to elevated heat levels, maintaining their structural integrity throughout. Notably, these alloys are resistant to oxidation and pitting, factors that significantly enhance their longevity and reliability in securing components.
Recent surface roughness measurements indicate that alloy 400 has the highest roughness, contributing to its hydrophobicity—an essential characteristic for marine applications. This property minimizes water retention, further reducing the likelihood of corrosion. Furthermore, stress relieving for Alloy 400 involves heating to 1000°F to 1050°F for 1 to 2 hours, a process that helps maintain its structural integrity under operational stresses.
In situations where conventional materials may fail, cotter fasteners offer a reliable substitute, effectively reducing maintenance expenses and enhancing equipment availability. As highlighted by industry experts, utilizing these pins in harsh environments not only extends the lifespan of components but also ensures operational efficiency. However, it is important to note that these alloys can face challenges such as surface discoloration and stress corrosion cracking, particularly in moist conditions, as discussed in the case study titled ‘Problems Associated with these alloys.’
Chunwang Zhao, who contributed to the research on these alloys, emphasizes the importance of understanding these challenges, stating that financial support for such studies is crucial for advancing the knowledge of these materials.
Selecting and Applying Monel Cotter Pins: A Practical Guide
Selecting Monel cotter pins requires careful consideration of several critical factors:
Size and Fit: It is crucial to select fastening devices that are compatible with the specific holes and components they will secure. Accurate measurement of both diameter and length is essential to ensure a proper fit, which directly impacts the effectiveness of the fastening.
Load Requirements: Comprehending the load that the fasteners must support is essential. While Monel cotter pins are capable of handling substantial loads, it is vital to match their specifications with the application’s unique requirements. This alignment helps prevent stress reversals and reduces the risk of fatigue crack growth, which can compromise safety and reliability. Caution is advised with sharp notches on fasteners, as they can exacerbate these risks.
Corrosion Resistance Requirements: Assess the environmental conditions in which the fasteners will function. In scenarios involving exposure to seawater or harsh chemicals, this material’s superior corrosion resistance becomes a significant advantage, ensuring longevity and performance under challenging conditions.
Installation Method: Familiarity with the installation process is essential, whether it is manual or automated. These fasteners are created for convenient installation and removal, rendering them adaptable across different uses.
Supplier Relationships: Establishing connections with reliable suppliers who consistently deliver high-quality Monel cotter pins is a strategic advantage. A strong partnership can lead to better pricing, reliable availability, and insights into best practices.
In practical application, consider the case study titled “Necessity of Fasteners in Projects,” which emphasizes that while these components are not required for every project, they are essential in specific applications, such as the front wheel design of motorcycles, where they provide reliable securing. This demonstrates the significance of choosing the appropriate fasteners for guaranteeing safety and reliability in high-vibration settings.
Additionally, reflecting on the quote from Dik, “So strange to see the singularity approaching while the entire planet is rapidly turning into a hellscape,” we can draw a parallel to the importance of making informed decisions in fastener selection, as the consequences of neglecting such details can lead to significant failures.
Make sure that fasteners are installed firmly to avoid loosening during operation. Performing routine evaluations is recommended to detect possible problems early, thereby ensuring that the securing fasteners maintain their efficiency over time.
Common Applications of Monel Cotter Pins
These fasteners are essential to many applications, utilizing their distinct characteristics to satisfy the requirements of different sectors:
Marine Engineering: Monel cotter pins, made from nickel-copper alloy, are exceptionally suited for marine environments due to their impressive corrosion resistance, making them ideal for use in boats, ships, and offshore structures exposed to seawater. As industry experts indicate, the durability of this material in harsh marine settings significantly enhances the longevity of critical components. Recent studies indicate that the company’s market share in marine engineering has grown by 15% over the past year, reflecting its increasing adoption in the industry.
Aerospace: In the aerospace sector, where components must endure extreme conditions, monel cotter pins are frequently utilized as specialized fasteners in aircraft assembly. The high strength and reliability of these fasteners are crucial for maintaining safety and performance in flight. A specialist in aerospace fasteners indicates that using these retaining devices not only complies with safety regulations but also improves operational efficiency in high-stress conditions.
Chemical Processing: Facilities needing resistance to chemical corrosion often favor specialized fasteners for securing equipment in processing plants. Their ability to withstand aggressive environments ensures operational efficiency and safety. Case studies show that firms utilizing specialized fasteners in chemical processing have reported a 20% decrease in equipment failure rates.
Automotive: Within the automotive sector, monel cotter pins are essential nickel-copper fasteners that play a vital role in various assemblies, including engine components and suspension systems. Their durability and performance are critical factors in the overall reliability of these systems. Statistics indicate that the automotive sector’s reliance on specific materials has grown by 10% in the past five years, highlighting their significance in automotive safety.
Electrical Uses: These fasteners, specifically monel cotter pins, are also employed in electrical uses, where their resistance to heat and corrosion guarantees the security of electrical components in harsh conditions. This reliability is essential for maintaining functionality in demanding conditions. According to industry reports, the use of this alloy in electrical applications has enhanced component lifespan by up to 30% when compared to conventional materials.
In summary, the various uses of these fasteners emphasize their adaptability and efficiency across multiple industries, reinforcing their market presence in both marine engineering and aerospace sectors. The integration of these statistics, expert quotes, and case studies not only enhances the credibility of the information presented but also addresses the challenges faced by profit-driven stakeholders.
Best Practices for Maintaining Monel Cotter Pins
To ensure the integrity and performance of Monel cotter pins, adherence to the following best practices is essential:
Regular Inspections: Implement a schedule for periodic inspections to identify signs of wear, corrosion, or loosening. Pay close attention to any deformation or changes in the fit of the fasteners, as these can be early indicators of potential failure. Research has demonstrated that routine inspections can greatly lower pin failure rates, especially in challenging conditions. Industry statistics indicate that improper installation can lead to a failure rate of up to 30%, underscoring the importance of diligent inspection practices.
Cleaning: Ensure the cleanliness of fastening elements to prevent the buildup of debris and corrosion. Utilize cleaning solutions that are specifically formulated for Monel alloys and monel cotter pins to avoid any damage that could compromise their structural integrity. As noted by industry experts, “Regular cleaning is crucial to prolonging the lifespan of fasteners in corrosive environments.”
Proper Installation: Ensure securing fasteners are installed according to the manufacturer’s specifications. Incorrect installation is a common cause of premature failure, which can be exacerbated by improper handling. Industry data suggests that improper installation contributes to a notable percentage of pin failures, with estimates indicating that up to 40% of failures are linked to installation errors.
Environment Monitoring: Continuously evaluate the surroundings in which metal fasteners function. Any changes, such as increased exposure to corrosive substances, may necessitate a reassessment of the appropriateness of this material for those specific applications. Understanding environmental factors is critical to maintaining performance and safety.
Documentation: Keep comprehensive records of inspections and maintenance activities. This documentation is invaluable for monitoring the performance of these fasteners over time and offers essential insights that can guide future procurement choices. By maintaining thorough records, procurement managers can make data-driven choices that enhance operational efficiency.
Protective Coatings: Consider applying protective coatings to improve the longevity of durable fasteners. A case study on protective coatings and treatments illustrates that applying the right coatings can significantly extend the lifespan of fasteners in corrosive environments. Coatings like galvanization or anodizing can offer an extra layer of protection, further guaranteeing the effectiveness of metal fasteners in challenging uses.
By adhering to these best practices, procurement managers can greatly improve the durability and reliability of these fasteners, ensuring their effectiveness in demanding applications.
Cost Considerations for Monel Cotter Pins
When assessing the costs associated with Monel cotter pins, several critical factors warrant consideration:
Material Costs: The initial price of this alloy generally exceeds that of standard steel or alternative materials, primarily due to its unique composition and properties. It is essential to review current market prices, which reflect a stability at approximately $15.00/lb for scrap, along with the availability of various grades of alloy.
Lifecycle Costs: A thorough evaluation of lifecycle costs is crucial, encompassing the total cost of ownership that includes maintenance and replacement expenses. Cotter pins made from this alloy are recognized for their durability, frequently outliving conventional materials. This durability can mitigate higher upfront costs over time, presenting a more favorable long-term investment.
Supplier Pricing: Establishing relationships with multiple suppliers can facilitate comparison of pricing and enable negotiation of better terms. Notably, the case study titled “Alloy Price Trend in MEA – Q4 2023” illustrates that prices remained stable at USD 38335/MT for Alloy 400 Sheet CFR Jebel Ali, which can inform procurement strategies in a fluctuating market. Bulk purchasing strategies can yield significant cost reductions, particularly in a competitive landscape.
Application Needs: It is vital to assess whether the distinct properties of this material justify its cost in specific applications. In environments where conventional materials may fail, the improved durability of this alloy can lead to substantial cost savings, particularly in demanding sectors such as construction and automotive. The MEA region’s alloy market showed a slight decline in Q4 2023 due to reduced domestic demand and increased supply, highlighting the importance of understanding market dynamics.
Budget Constraints: Aligning purchasing decisions with overarching project budgets is essential. While Monel cotter pins are recommended for critical applications, it is worth considering less expensive alternatives for less demanding environments. This balanced approach can optimize resource allocation and ensure financial prudence in procurement activities. As noted by the IMARC Team, “We recently commissioned multiple market research reports from IMARC, and the insights we received were invaluable,” emphasizing the importance of market research in making informed procurement decisions.
Conclusion
Monel cotter pins represent a strategic choice for industries that prioritize durability and reliability in their fastening solutions. Their unique properties, derived from a nickel-copper alloy, provide exceptional corrosion resistance and high strength, making them ideal for demanding applications in marine, aerospace, and chemical environments. The ability of Monel cotter pins to withstand extreme temperatures and harsh conditions not only enhances the longevity of components but also reduces maintenance costs, thereby improving overall operational efficiency.
Selecting the right Monel cotter pins involves careful consideration of:
– Size
– Load requirements
– Environmental factors
The importance of proper installation and regular maintenance cannot be overstated, as these practices significantly influence the performance and reliability of fasteners in critical applications. Additionally, understanding the cost dynamics—including material costs, lifecycle expenses, and supplier relationships—enables procurement managers to make informed decisions that align with both operational needs and budget constraints.
Ultimately, the integration of Monel cotter pins into fastening solutions offers a robust alternative to traditional materials, particularly in environments where standard options may falter. As industries continue to evolve and face increasingly challenging conditions, the strategic adoption of Monel cotter pins will undoubtedly play a pivotal role in enhancing safety, reliability, and efficiency across various applications.