Blogs
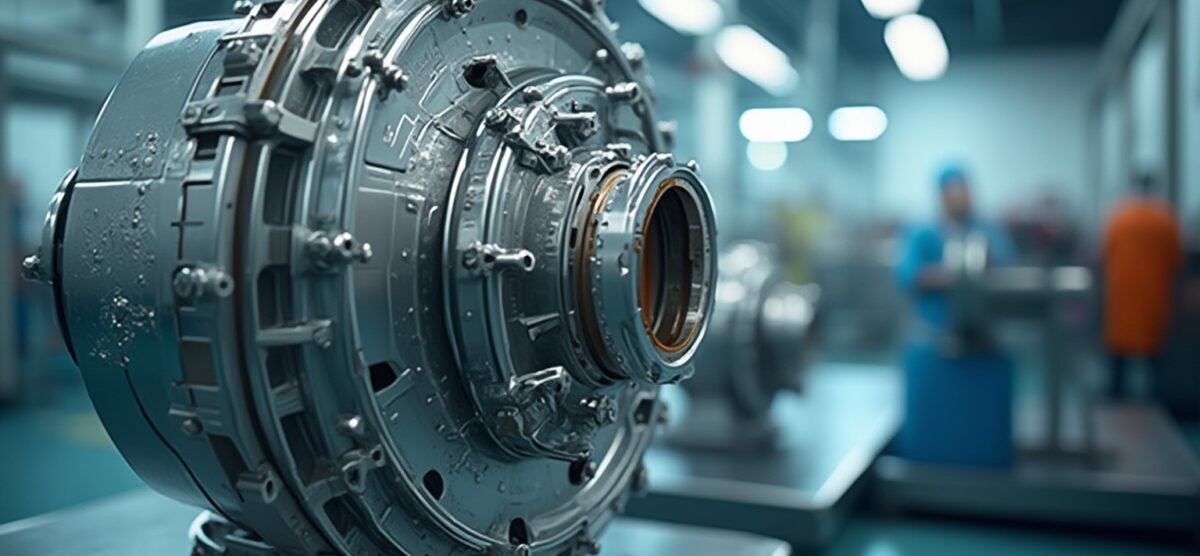
Understanding Monel Reactors: An In-Depth Tutorial on Types and Applications
Overview
Monel reactors are specialized processing units made from a nickel-copper alloy known for its exceptional corrosion resistance and durability, making them suitable for harsh industrial environments. The article outlines their various types and applications across industries like aerospace, marine, and chemical processing, emphasizing their advantages in operational efficiency, safety, and longevity, supported by statistical evidence of their performance benefits.
Introduction
Monel reactors stand at the forefront of modern chemical processing, offering unparalleled durability and resilience in some of the most challenging environments. Crafted from a unique nickel-copper alloy, Monel not only excels in corrosion resistance but also thrives under high temperatures and pressures, making it a preferred choice across industries such as aerospace, marine, and chemical processing.
As procurement managers navigate the complexities of material selection, understanding the distinct types of Monel reactors and their specific applications becomes essential. This article delves into the characteristics, advantages, and maintenance strategies of Monel reactors, providing insights that empower decision-makers to optimize operational efficiency while ensuring safety and sustainability in their processes.
Introduction to Monel Reactors: Definition and Characteristics
These processing units are sophisticated structures made from a highly regarded nickel-copper alloy recognized for its outstanding resistance to corrosion and durability at high temperatures. With the ability to endure harsh environments, this alloy is particularly beneficial in industries where materials face aggressive conditions, such as exposure to acids and saltwater. Statistically, the monel reactor is widely utilized in processing vessels, demonstrating the favored status of these alloys among producers for their durability and resilience.
In fact, this material was widely used for firebox stays in steam locomotive boilers, highlighting its historical significance and versatility. The distinct mixture of this alloy enables the monel reactor and other systems to function effectively in both elevated-temperature and high-pressure situations, rendering them suitable for various uses in processing substances and marine settings. Additionally, the diverse range of copper nickel alloys available at Domadia provides exceptional properties suited for marine engineering and electronics, enhancing their utility in similar harsh conditions.
Furthermore, Domadia’s mica tape products offer high-temperature resistance and excellent electrical insulation, making them essential for critical applications in electrical engineering. These tapes are specifically designed to withstand extreme conditions, ensuring reliability in applications such as fire-resistant cables and insulation systems. As highlighted by Huaxiaometal:
- “Versatility: Easily fabricated, welded, and machined, making it a top choice for manufacturers.”
Recent advancements in corrosion-resistant materials further highlight the significance of the monel reactor, ensuring that it continues to be a competitive choice for contemporary process vessels.
Exploring the Different Types of Monel Reactors
The monel reactor systems encompass a variety of types, each tailored for specific operational requirements. Significantly, batch systems are preferred for smaller-scale operations because of their versatility in managing various chemical compositions. This flexibility allows for experimental approaches and efficient production of small batches, making them ideal for niche applications and ensuring the successful execution of small batch orders.
The operational capabilities of these systems, including their ability to quickly adjust to different formulations, directly contribute to the proven execution of both small and large batch orders. Conversely, continuous flow systems are engineered for larger production capacities, optimizing operational efficiency and consistency, thus enabling the proven execution of large batch orders. This design is especially advantageous for high-volume manufacturing processes, where sustaining product quality over long durations is vital.
Furthermore, specialized vessels have emerged, incorporating advanced features such as enhanced mixing capabilities and integrated heat exchangers, essential for unique chemical processes. These innovations not only improve reaction rates but also ensure that the materials processed are compatible with the specific demands of the application. Comprehending these differences is essential for procurement managers aiming to optimize production lines and align system types with strategic operational goals.
In terms of safety and efficiency, it is crucial to reflect on the consequences of operational mistakes, such as the 1999 incident in Tokai Mura, Japan, which underscored the critical nature of system safety. As procurement managers evaluate their options, insights from industry experts can provide valuable guidance. Furthermore, the competitive environment of the market for processing units, marked by fierce rivalry among established firms and newcomers, emphasizes the significance of approaches such as mergers and ongoing R&D investment.
Staying informed on the efficiency statistics and expert opinions regarding batch versus continuous flow systems will be instrumental in making informed procurement decisions.
Applications of Monel Reactors in Industry
These vessels are essential to the aerospace, marine, and chemical processing sectors because of their distinctive characteristics. In the aerospace sector, these reactors are essential for producing components that demand a high strength-to-weight ratio coupled with outstanding corrosion resistance. According to industry experts, its superior performance under extreme conditions is critical for maintaining the integrity of aircraft systems.
As highlighted by Schwan and Sher (1969), ‘In a gradient field, the pearl chains protrude from the electrode surface,’ stressing the significance of properties in operational efficiency. Likewise, in marine uses, its exceptional resistance to saltwater corrosion renders it the preferred option for systems employed in shipbuilding and offshore structures. This is particularly vital in environments where durability is paramount.
In the chemical processing sector, these vessels exhibit their dependability and strength when handling aggressive substances, improving both safety and efficiency in production procedures. Recent statistics suggest that the application of a nickel-copper alloy in system setups results in a 25% increase in lifespan compared to conventional materials. The versatility of this material in diverse applications is a significant asset, ensuring that operational demands are met without compromising on sustainability.
A case study titled ‘Balancing Sustainability with Operational Demands in Airlines’ illustrates how specific vessels contribute to fuel efficiency and eco-friendly technology investments, promoting sustainable practices while maintaining operational efficiency. Additionally, recent advancements emphasize the significance of material performance, with reports suggesting that grinding cracks, which can impact hard substances, are less of a worry when employing a specific nickel-copper alloy in system applications, thus strengthening its industrial relevance.
Advantages of Monel Reactors: Why Choose Monel?
These alloy systems offer numerous benefits, mainly distinguished by their outstanding resistance to corrosion and impressive strength, rendering them perfect for harsh conditions. These attributes not only prolong the lifespan of the monel reactor but also significantly lower maintenance costs and minimize downtime. Recent findings indicate that alloy K-500 benefits from enhanced strength through aging processes, reinforcing its reliability in demanding applications and contributing to overall cost-effectiveness.
However, it is essential to manage the material’s disadvantages, such as its high cost and poor machinability. Strategies encompass:
- Using different resources where practical
- Enhancing the application of specific alloys in particular situations
In explosive environments, integrating Non-Sparking Tools becomes crucial; these tools provide an essential safety measure, ensuring compliance with industry standards while working with certain alloys.
Suppliers such as [Supplier Name] and [Supplier Name] offer a range of Non-Sparking Tools specifically designed for use in hazardous environments, including wrenches, screwdrivers, and hammers made from materials like aluminum and brass. A case study titled ‘Managing Disadvantages of a Nickel-Copper Alloy’ illustrates how companies have successfully navigated these challenges by investing in specialized machining tools and training, which can enhance machining efficiency and reduce costs. Furthermore, this material’s compatibility with a diverse array of chemicals renders it a versatile choice across various industrial sectors.
As noted by expert Mayuly Rodríguez, ‘This treatment significantly improves resistance to stress corrosion cracking, which is a crucial property for applications in high-pressure, highly corrosive environments like those found in a monel reactor.’ By choosing specialized containers alongside suitable Non-Sparking Tools from trusted providers, companies position themselves to improve operational efficiency while ensuring compliance with strict industry standards, especially in areas where safety adherence is essential.
Maintenance and Care for Monel Reactors
To maximize the longevity and operational efficiency of these reactors, implementing a rigorous maintenance routine is imperative. The exceptional properties of this material make it highly valuable in marine, chemical processing, and aerospace industries, emphasizing the importance of proper care. Regular inspections should be conducted to identify any early indications of corrosion or wear, ensuring that all seals and connections remain secure.
The selection of cleaning solvents is essential; using alternatives that do not compromise the integrity of the material is vital for sustaining its performance. As noted by Huaxiao Metal, ‘the versatility of this alloy allows for easy fabrication and maintenance,’ which solidifies its position as a preferred material in various industries. Following manufacturer-recommended maintenance schedules will further enhance system reliability, while meticulous record-keeping of maintenance activities is essential for tracking equipment health.
For instance, a case study involving coated heat exchangers in a chemical processing facility demonstrated that using this material improved thermal efficiency and reduced energy consumption, ultimately increasing equipment lifespan and lowering replacement costs. By adopting a proactive maintenance strategy, procurement managers can significantly reduce the risk of costly downtimes and extend the service life of the Monel reactor.
Conclusion
Monel reactors represent a pinnacle in chemical processing technology, characterized by their exceptional durability and resistance to extreme conditions. The unique nickel-copper alloy composition not only renders them highly resilient against corrosion but also enables efficient operation in high-temperature and high-pressure environments. This versatility makes Monel reactors indispensable across critical industries such as aerospace, marine, and chemical processing.
Understanding the various types of Monel reactors—batch, continuous flow, and specialized configurations—equips procurement managers with the insights necessary to make informed decisions tailored to specific operational needs. By recognizing the advantages and applications of Monel reactors, including their ability to enhance safety and efficiency, stakeholders can strategically align their material choices with long-term operational goals.
Moreover, the importance of rigorous maintenance cannot be overstated. Implementing a comprehensive care routine ensures the longevity and reliability of Monel reactors, allowing organizations to maximize their investments while minimizing downtime and costs. As industries continue to evolve, the integration of Monel reactors into production processes not only supports operational efficiency but also aligns with sustainability initiatives, reinforcing their value in modern chemical processing.
In conclusion, Monel reactors stand as a testament to innovation in material science, providing robust solutions that address the complexities of contemporary industrial demands. By leveraging their unique properties and understanding their applications, procurement managers can confidently navigate the landscape of chemical processing and make choices that drive both performance and sustainability.