Blogs
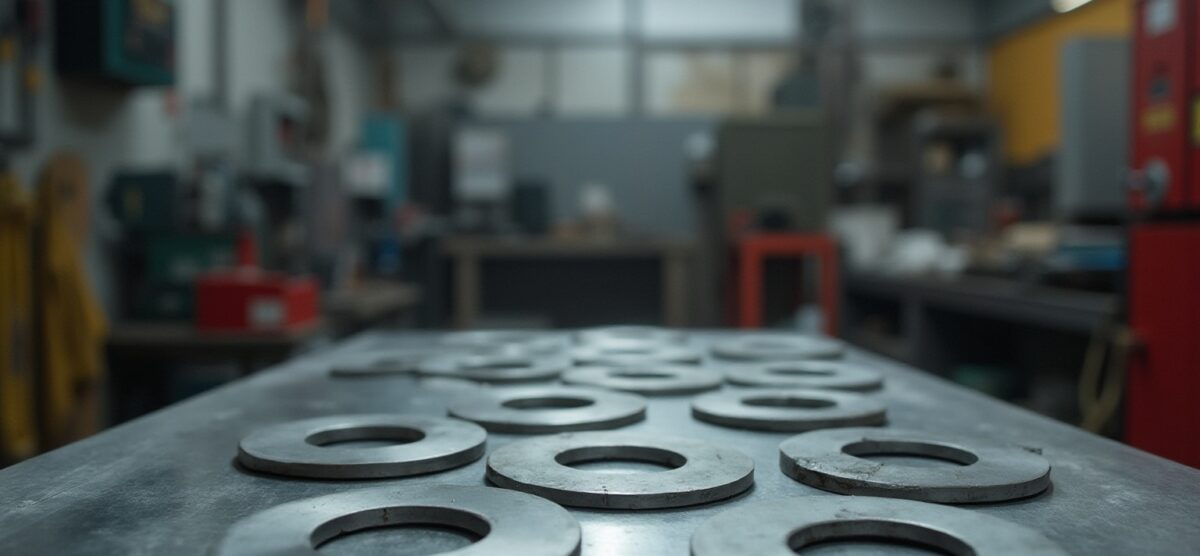
Understanding Monel Washers: A Complete Tutorial on Properties and Applications
Overview
Monel washers, specifically made from alloy 400, are highly valued for their exceptional corrosion resistance, strength, and thermal stability, making them ideal for demanding applications in industries such as marine engineering, chemical processing, and aerospace. The article supports this by detailing the alloy’s composition, mechanical properties, and extensive applications, illustrating its superiority over other materials like stainless steel in harsh environments.
Introduction
In the realm of high-performance materials, Monel washers stand out as a critical component across various industries, thanks to their unique properties and exceptional durability. Crafted from the nickel-copper alloy Monel 400, these washers offer unparalleled resistance to corrosion and remarkable mechanical strength, making them indispensable in challenging environments such as:
- Marine engineering
- Chemical processing
- Aerospace applications
As procurement managers navigate the complexities of material selection, understanding the advantages and applications of Monel washers becomes essential. This article delves into the properties, benefits, and diverse uses of Monel washers, providing insights that can inform strategic decision-making and enhance operational efficiency in demanding industrial settings.
Introduction to Monel Washers: Understanding Monel 400
Washers made from the nickel-copper alloy known as alloy 400 are renowned for their outstanding resistance to corrosion and remarkable strength. This alloy, comprising approximately 67% nickel and 30% copper, is enhanced with trace amounts of iron, manganese, and silicon. These characteristics make alloy 400 particularly effective in demanding environments where durability is critical.
Incorporated in 1983, alloy 400 has established a strong reputation in various applications, including:
- Marine engineering
- Chemical processing
- Oil refining
This exemplifies its superior performance when exposed to corrosive substances. Manoj Phagare, a Senior Research Analyst at Cognitive Market Research, emphasizes the significance of alloy 400 in shaping evidence-based strategies for industries that rely on high-performance materials. For instance, alloy 400 wood screws—designed specifically for high corrosion resistance—have proven their reliability in marine and architectural structures, meeting international standards and ensuring longevity even in harsh conditions.
This emphasizes the wider selection of copper nickel alloys offered at Domadia, which serve different purposes in marine engineering and electronics. Understanding the properties and applications of alloy 400 and Monel washers, along with other copper nickel alloys, becomes essential for procurement managers. These materials not only influence product selection but also play a critical role in decision-making processes aimed at leveraging their exceptional qualities in diverse industries.
Properties of Monel Washers: Chemical Composition and Mechanical Strength
Alloy 400 fasteners are celebrated for their exceptional mechanical strength, featuring a tensile strength of roughly 100,000 psi and a yield strength near 45,000 psi. This remarkable strength is primarily attributed to their specific chemical composition, which includes about 67% nickel and 30% copper, enhancing their durability and significantly improving their resistance to corrosion, particularly in challenging environments such as seawater, acids, and alkalis. Recent studies have shown that alloy 400 washers maintain their structural integrity and performance even under high thermal stress, demonstrating excellent thermal stability.
For example, this alloy has a thermal conductivity of 21 W/m·K, in contrast to titanium’s 6.7 W/m·K, making it especially appropriate for heat transfer uses. In contrast, copper nickel alloys are widely employed in marine engineering for components like:
- Ship hulls
- Offshore platforms
- Seawater piping systems
These applications showcase their superior corrosion resistance compared to stainless steel in these environments. Their uses also extend to automotive systems for:
- Brake lines
- Hydraulic systems
As well as in:
- Electronics
- Heat exchangers
- Coinage
As highlighted by industry expert Kat de Naoum, ‘The unique properties of monel washers underscore their versatility across diverse industries.’ These characteristics render the 400 alloy fasteners an excellent choice for uses where dependability and longevity are crucial, especially in settings where copper nickel alloys thrive. Their capability to withstand extreme conditions ensures that they remain a preferred choice among engineers for critical installations.
Applications of Monel Washers Across Industries
Certain alloys are essential elements in various crucial sectors, characterized by their distinctive attributes that provide considerable benefits. Their applications include:
Marine Industry: Nickel-copper alloys are extensively utilized in shipbuilding and offshore oil drilling operations, primarily due to their exceptional corrosion resistance. This renders them essential in locations where contact with saltwater and severe conditions is common.
Chemical Processing: In contexts where equipment frequently encounters corrosive substances, monel washers are suitable fasteners for use in valves, pumps, and fittings. Their durability guarantees dependable performance, reducing the risk of failure in crucial applications.
Aerospace: The aerospace industry utilizes nickel-copper alloy fasteners in aircraft engine components, where high strength and temperature resistance are essential. These fasteners contribute to the overall safety and efficiency of aircraft operations, proving vital in high-stress environments.
Electronics: Beyond these industries, these components also find uses in various electrical connectors and parts, where their conductivity and durability enhance performance and reliability.
The versatility of monel washers as fasteners underscores their importance in providing effective engineering solutions across multiple sectors, reinforcing their status as a preferred material for procurement managers seeking reliable, high-performance components. Notably, a standard practice in company procedures manuals references a statistic of 5,138, highlighting the importance of adhering to industry standards. Furthermore, as noted by an expert, Tunalover, ‘What if the bolt is being used essentially as a pin, such that it can drop to near zero clamping force and still be effective?’
This prompts reflections on the performance of specific fasteners in different uses. Moreover, the case study named ‘Need for Standard Part Numbers for Serrated Fasteners’ demonstrates the difficulties encountered in the sector concerning standardization and sourcing, highlighting the essential function of specific components in addressing these requirements.
Advantages of Monel Washers: Why Choose Monel Over Other Materials
These monel washers provide unique benefits compared to other materials, especially stainless steel, making them an excellent option for various challenging uses. Key benefits include:
- Corrosion Resistance: Monel exhibits exceptional performance in harsh environments, especially in saltwater and acidic conditions, far surpassing that of stainless steel. According to industry experts, this property is essential for uses in marine and chemical processing sectors.
- Strength: With higher tensile and yield strength compared to many common materials, this alloy ensures superior performance under stress, making it suitable for high-load uses. This strength is crucial in scenarios where material failure could lead to significant operational disruptions.
- Thermal Stability: Monel maintains its integrity at elevated temperatures, offering reliable performance in extreme conditions. Significantly, stainless steel has a coefficient of thermal expansion of 16.0 µm/m·K, which can influence its performance in high-heat uses. This stability is particularly beneficial for uses that involve exposure to heat, where material degradation could compromise functionality.
- Longevity: The resistance of this material to wear and tear translates to a greater lifespan, ultimately reducing replacement costs and downtime. This longevity is particularly evident in high-stress environments where the durability of components is paramount.
Furthermore, as noted by Kat de Naoum, stainless steel, often referred to as ‘inox’ or rustless steel, is composed of around 70–80% iron and at least 10.5% chromium, which provides a protective oxide layer. However, the non-magnetic characteristics of this alloy, as demonstrated in the case study titled “Magnetic Properties of this Alloy and Stainless Steel,” render it especially appropriate for electronic uses, where magnetic interference could be harmful.
In addition to these advantages, monel washers are an essential component of non-sparking tools, which are critical in explosive environments. The use of non-sparking tools, like those crafted from a specific alloy, enhances safety and operational efficiency, highlighting the significance of choosing suitable materials for particular uses. For procurement managers, it is also crucial to consider suppliers and manufacturers of electrical insulation and high-temperature materials, including other alloys, to ensure access to quality products that meet industry standards.
These suppliers play a crucial role in providing the necessary materials for applications where performance and safety are paramount.
Frequently Asked Questions About Monel Washers
- What is the difference between alloy 400 and alloy 500?
Monel 400 is characterized by its higher nickel content, which enhances its corrosion resistance, making it particularly effective in marine and chemical environments. In contrast, alloy 500 boasts a greater copper content, offering improved machinability without significantly sacrificing corrosion resistance. This distinction makes alloy 400 the preferred option for uses requiring superior toughness and durability. As noted by AEETHER CO., LIMITED, if your product has higher requirements for toughness, alloy 400 should be given priority.
Can nickel-copper alloy spacers be utilized in high-temperature settings?
Absolutely. These fasteners are designed to withstand high-temperature environments, demonstrating outstanding thermal stability. This capacity renders them ideal for critical applications in aerospace, oil and gas, and chemical processing industries, where reliability under heat stress is paramount.
How do I ascertain the appropriate size of metal disc for my project?
To accurately determine the appropriate size of a Monel washer, it’s essential to collaborate with your engineering team. They should evaluate the specific requirements of your application, including load-bearing capacities and pressure factors, to ensure optimal fit and performance.
Are these fasteners more expensive than stainless steel?
While the initial procurement cost of Monel washers is indeed higher—approximately Rs 2000 per kg compared to stainless steel—their durability and resistance to corrosion in hostile environments often translate into lower long-term maintenance expenses. According to the case study titled “Long-term Cost Analysis of Monel and Stainless Steel,” the superior corrosion resistance of this material can lead to lower long-term maintenance expenses in harsh environments. Therefore, in situations where longevity and performance are critical, using Monel washers can serve as a more economical solution over time. It is also important to note that stainless steel remains a cost-effective option for less corrosive conditions, making it popular across various industries.
What are the typical uses of copper nickel alloys?
Copper nickel alloys are widely used in marine engineering for components such as ship hulls, offshore platforms, and seawater piping systems. They are also utilized in the automotive industry for brake lines and hydraulic systems due to their excellent corrosion resistance. Furthermore, copper nickel alloys are utilized in electronics, heat exchangers, and coinage.
Why are Non-Sparking Tools essential in explosive environments?
- Non-Sparking Tools are the best alternative for non-sparking application purposes in explosive potential environments, ensuring safety and reliability during operations. Their design minimizes the risk of ignition, making them crucial for workplaces where flammable materials are present. For procurement managers, investing in Non-Sparking Tools not only enhances workplace safety but also ensures compliance with safety regulations, reducing liability risks associated with accidents. Examples of their applications include use in oil rigs, chemical plants, and mining operations, where the potential for explosive atmospheres is significant.
Conclusion
Monel washers, crafted from the resilient Monel 400 alloy, embody a synthesis of strength, longevity, and unparalleled resistance to corrosion. Their unique chemical composition, which includes a high percentage of nickel and copper, positions them as the material of choice in demanding environments such as:
- Marine engineering
- Chemical processing
- Aerospace applications
The mechanical properties of Monel washers, including their impressive tensile and yield strength, coupled with their thermal stability, ensure reliable performance even under extreme conditions.
The versatility of Monel washers extends across multiple industries, where their applications range from:
- Shipbuilding
- Oil drilling
- Critical aerospace components
- Electronic connectors
This broad applicability underscores their significance as essential components in engineering solutions that prioritize durability and reliability. Procurement managers must recognize the distinct advantages Monel washers offer over alternative materials, particularly in environments prone to corrosion and high stress, thereby making informed decisions that enhance operational efficiency and safety.
In summary, the strategic selection of Monel washers not only provides robust performance but also translates to long-term economic benefits. As industries continue to navigate the challenges of material selection, Monel washers emerge as a pivotal solution, reinforcing their status as indispensable components that drive success in high-performance applications. The emphasis on quality and reliability in procurement practices will undoubtedly lead to improved outcomes and sustained operational excellence.