Blogs
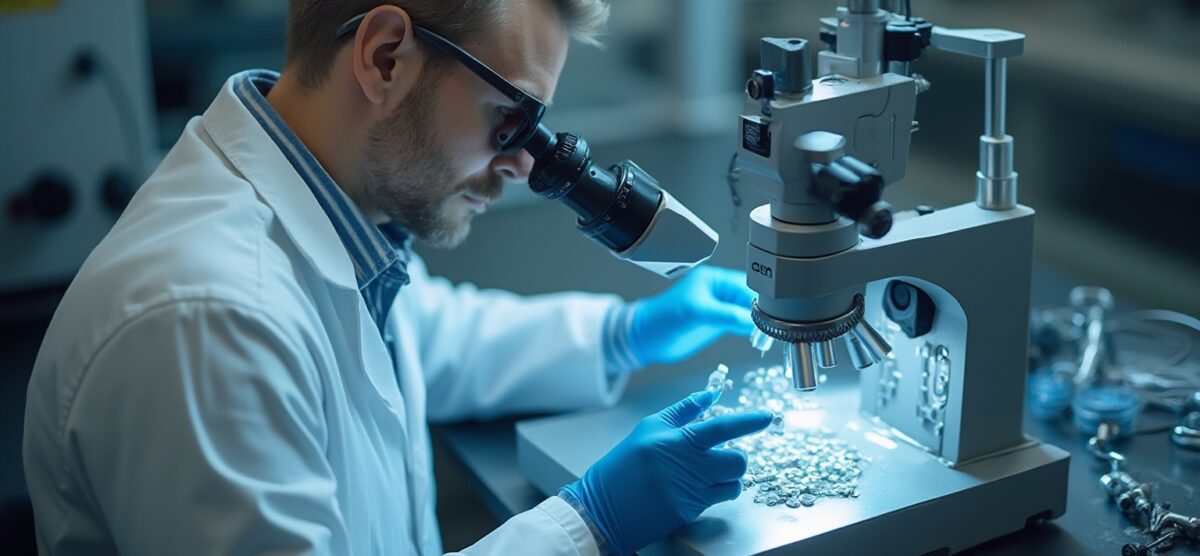
Understanding the Laves Phase in Inconel 718: An In-Depth Tutorial
Overview:
The article focuses on understanding the Laves phase in Inconel 718, highlighting its significant impact on the alloy’s microstructure and mechanical properties. It emphasizes that controlling the formation and distribution of this intermetallic compound through precise processing parameters is crucial for optimizing the strength and ductility of Inconel 718, as evidenced by various studies linking these factors to improved performance in high-temperature applications.
Introduction
The Laves phase in Inconel 718 is more than just a structural curiosity; it is a pivotal element that significantly influences the performance and reliability of this renowned nickel-chromium superalloy. As industries increasingly demand materials capable of withstanding extreme temperatures and mechanical stress, understanding the intricacies of the Laves phase becomes essential.
This article delves into the following topics:
- Formation mechanisms
- Impact on mechanical properties
- Critical control measures during manufacturing
By providing procurement managers and engineers with valuable insights, readers will explore recent research findings and practical applications. This will enable them to gain a comprehensive understanding of how to optimize the performance of Inconel 718, ensuring it meets the rigorous demands of modern engineering challenges.
Introduction to the Laves Phase in Inconel 718
This structure signifies an important intermetallic compound that appears in certain metal alloys, particularly in a specific nickel-chromium alloy. Characterized by its unique crystal arrangement, this material plays a crucial role in affecting the overall performance of the alloy. Inconel 718, a prominent nickel-chromium superalloy, finds extensive application in high-temperature environments, such as jet engines and gas turbines.
Therefore, a thorough comprehension of its state behaviors, particularly this specific structure, is crucial for enhancing material characteristics. Recent studies have indicated that the processing parameters, including:
– B: E: 939 J/mm
– TTS: 230 mm/min
– WFS: 2.5 m/min
– DR: 1.39 kg/h
significantly influence the development of the intermetallic compound and its effect on the alloy’s microstructure. Studies show that the existence of this particular variant can greatly alter the alloy’s microstructure, directly influencing its mechanical properties.
Dr. SGK Manikandan from the Indian Space Research Organization observed,
The results indicate improved fusion zone microstructure, decreased quantity of certain compounds, minimal niobium segregation, and a softer fusion zone in the as-welded state.
This insight highlights the significance of closely observing the relevant structure during processing to reduce potential negative impacts, such as liquidation cracking, which can result from heat accumulation in specific welding techniques. Additionally, a case study titled ‘Microstructural Characterization of Fusion Zone’ revealed that higher cooling rates lead to finer equiaxed dendritic structures and reduced microsegregation of niobium, enhancing the mechanical properties of the weldments.
Understanding the development and effects of this specific structure, including the laves phase in inconel 718, is not merely an academic task; it holds practical significance for engineers and procurement managers, ensuring that alloy 718 meets the rigorous performance standards of challenging applications.
Mechanisms of Laves Phase Formation in Inconel 718
The creation of the specific structure in alloy 718 is significantly affected by elements like temperature, composition, and cooling rates. During the solidification process, as the alloy transitions from a liquid to a solid state, diffusion mechanisms play a pivotal role in the aggregation of specific elements. This aggregation is fundamental to the nucleation of the specific structure, which is characterized by a rich concentration of molybdenum and niobium that often segregates during solidification.
Recent statistics indicate that the homogenization time for Inconel 718 superalloys fabricated by LPBF is:
- 45 minutes at 1080 °C
- 2 hours at 1050 °C
- Significantly longer for casting methods, which can take up to 165 hours at the same temperature
Comprehending these mechanisms is crucial as they directly influence the volume fraction and distribution of the intermetallic compound, leading to considerable consequences for the alloy’s mechanical characteristics. Studies, including a case analysis titled ‘Yield Strength and Ductility of Specific Structures,’ have offered understanding into how processing parameters can be modified to effectively control the development of the alloy structure, thereby improving the material’s performance traits.
The research determined that granular structures are more favorable to ductility than their long-striped equivalents, with differences in yield strength mainly linked to the γ” component. As Han D. noted, the effect of Mo addition on grain growth is critical, emphasizing the need for precise control over temperature and composition to optimize the mechanical properties of alloy 718 in various applications.
Impact of Laves Phase on Mechanical Properties
This structure plays a crucial part in influencing the mechanical characteristics associated with the laves phase in Inconel 718, especially regarding its strength and ductility. While this intermetallic structure can enhance strength, excessive amounts can lead to embrittlement, which diminishes impact toughness. Recent findings suggest that a meticulously balanced existence of the intermetallic compound is crucial; maintaining an optimal volume fraction can enhance high-temperature strength while ensuring sufficient ductility for practical applications.
For example, the hardness of specimen SA was recorded at 439.273 HV, which is 30.2% greater than that of specimen AR, demonstrating the quantitative effect of the specific structure on mechanical properties. Engineers must understand the complex connection between the specific structure and mechanical characteristics to make informed choices when selecting materials for essential components. Research, including the case study titled ‘Effect of Intermetallic Compound on Mechanical Properties of Inconel 718,’ has shown that the laves phase in inconel 718, when present in different quantities in wrought and cast + HIP Inconel 718, considerably influences its mechanical performance.
The existence of the intermetallic compound may serve as a favored location for crack initiation and growth, resulting in decreased tensile ductility and ultimate tensile strength. Dr. SGK Manikandan emphasizes this point, stating, ‘Thus, can predict that the post welding aging pulse current with helium sample provides better strength than the other cases.’ This emphasizes the importance of comprehending the effects of variations in compositional structures to enhance both strength and ductility in superalloys.
Controlling Laves Phase During Manufacturing of Inconel 718
Efficient management of the laves phase in Inconel 718 during production is essential for enhancing the material’s mechanical characteristics. This control begins with the management of heat treatment and cooling processes. Applying methods like controlled cooling rates and optimized heat treatment cycles can greatly affect the formation of the intermetallic compound.
Specifically, the recommended solution followed by double aging heat treatment process includes:
- A solution treatment at 1150°C for 2 hours, followed by water cooling.
Recent advancements have shown that raising the solution treatment temperature from 950 °C to 1150 °C results in a significant reduction in the volume fraction of Nb-rich structure, leading to improved tensile strength and elongation. As Tiago Falcade, an editor, observes, ‘The heat treatment procedure used in this paper was developed based on the precipitation temperature and dissolution temperature of the precipitated component and the time-temperature transformation (TTT) curve created by Brooks and Bridges.’
Producers should contemplate implementing a multi-step heat treatment process to alleviate the negative impacts linked to the intermetallic compound while enhancing overall material performance. A case study examining the direct aging of L-PBF Inconel 718 illustrates that the laves phase in Inconel 718, when solid solution heat treatment is bypassed, can lead to suboptimal mechanical properties. The study highlights that direct aging samples exhibit a microstructure fraught with defects and lack the beneficial hardening precipitates formed during proper heat treatment, leading to inferior hardness and microstructural integrity compared to those that underwent solid solution heat treatment.
As a result, teams are urged to perform comprehensive metallurgical evaluations and utilize sophisticated simulation tools to anticipate behavior under different processing conditions. This proactive approach enables tailored adjustments to properties, ensuring that the final product meets stringent performance requirements.
Future Directions in Laves Phase Research for Inconel 718
Current studies on the structure in Inconel 718 are uncovering essential information about its impact on fatigue resistance and oxidation characteristics at high temperatures. The interpass cooling temperature for ICS is established at 300 °C, a factor that significantly influences processing conditions and performance. As the demand for advanced components increases, upcoming research is set to investigate novel alloying techniques that enhance the interaction between specific structures and critical mechanical characteristics.
Significantly, progress in additive manufacturing methods is anticipated to enable a greater comprehension of how the specific structure can be created and managed, especially in intricate shapes. This is reflected in the findings of M. Kamaraj, who observes that,
These effects reduce the size of laves phase in inconel 718 particles which can be dissolved during the conventional double aging treatment, suggesting a pathway for enhancing performance. Moreover, recent studies on high-entropy alloys emphasize the potential of merging these substances with the laves phase in inconel 718 structures, indicating promise for attaining an ideal balance of strength and ductility.
The results from this research suggest new possibilities for developing high-temperature structural substances. Additionally, the COS strategy has been shown to reduce manufacturing times significantly while allowing for greater segregation of alloying elements, which leads to the formation of the δ phase and increased brittleness in the microstructure. Staying informed about these developments is imperative for procurement managers and materials engineers, allowing them to adapt their strategies and leverage cutting-edge findings in material science.
Conclusion
Understanding the Laves phase in Inconel 718 is crucial for optimizing the performance and reliability of this superalloy in demanding applications. The formation mechanisms, influenced by processing parameters, play a significant role in determining the microstructure and mechanical properties of the alloy. As discussed, the careful management of temperature, composition, and cooling rates is essential to control the Laves phase, which can enhance strength but may also lead to embrittlement if present in excessive amounts.
The relationship between the Laves phase and the alloy’s mechanical properties underscores the necessity for engineers and procurement managers to approach material selection with a keen understanding of these dynamics. By maintaining an optimal volume fraction of the Laves phase, it is possible to achieve a balance between high-temperature strength and adequate ductility, essential for critical components in aerospace and industrial applications.
As research continues to evolve, the exploration of innovative manufacturing techniques and alloying strategies will further illuminate the complexities of the Laves phase. Proactive monitoring and control during the manufacturing process will enable teams to mitigate potential adverse effects and enhance the overall material performance. Staying abreast of these advancements will empower procurement managers and engineers to make informed decisions, ensuring that Inconel 718 meets the rigorous demands of modern engineering challenges and continues to excel in high-stakes environments.