Blogs
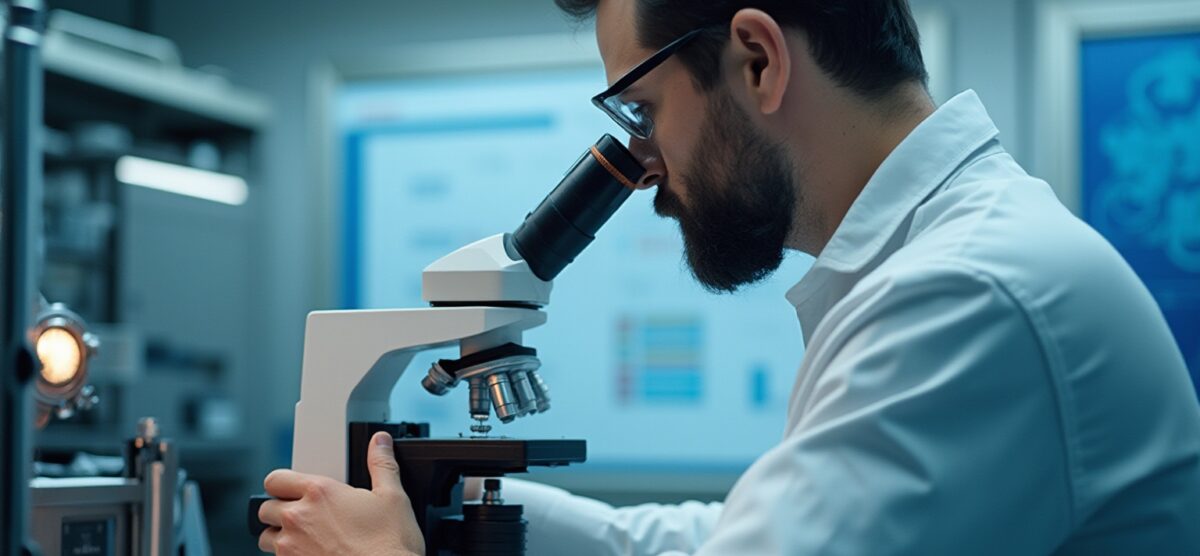
What Are Monel Specifications? A Comprehensive Overview
Overview
Monel specifications refer to the defined standards and properties of nickel-copper alloys, particularly emphasizing their composition, mechanical properties, and corrosion resistance, which make them suitable for demanding environments like marine and chemical processing applications. The article supports this by detailing the composition of Monel alloys, such as Alloy 400, and highlighting their advantages over other materials, including superior corrosion resistance and strength, thereby underscoring their significance in various industrial sectors.
Introduction
In the realm of advanced materials, Monel alloys emerge as a formidable choice, particularly for industries that demand exceptional performance in challenging environments. Renowned for their outstanding corrosion resistance and strength, these nickel-copper alloys are engineered to excel in applications ranging from marine engineering to chemical processing.
With a composition that typically includes a significant percentage of nickel and copper, Monel alloys not only withstand harsh conditions but also maintain their integrity and performance under extreme temperatures. As industries continue to evolve, understanding the distinct properties and applications of Monel alloys becomes crucial for procurement managers seeking to optimize their material selections.
This article delves into the composition, key types, and diverse applications of Monel alloys, providing insights into their compliance with industry standards and the advantages they offer over traditional materials.
Introduction to Monel: Composition and Properties
This well-known nickel-copper mixture is celebrated for its exceptional resistance to corrosion and outstanding strength. Consisting of roughly 67% nickel and 28% copper, this mixture also contains trace amounts of iron, manganese, carbon, and silicon, which collectively improve its overall performance. This alloy’s unique properties render it particularly effective in harsh environments, especially where it faces exposure to seawater or acidic conditions.
Significantly, these metal mixtures maintain their strength even at high temperatures, and their exceptional weldability makes them highly desired in scenarios where dependability is essential. Alloy 400, for instance, boasts a thermal conductivity of 21.8 W/m·K. As highlighted by metallurgical experts Matt Germscheid and John Hauck, ‘Discover how new technologies are drastically reimagining metallographic sample preparation.’
Ongoing developments are influencing the future of nickel-copper applications across various industries, including:
- Marine engineering
- Automotive
- Electrical sectors
At Domadia, we provide a comprehensive product catalog showcasing a varied selection of nickel-copper materials that adhere to the monel specification to fulfill your particular project requirements. Most nickel-copper materials are non-magnetic, making them suitable for electronic equipment and marine fields, although they may display slight magnetism under certain conditions.
Furthermore, in environments with explosive potential, incorporating non-sparking tools becomes essential to enhance safety. Despite the high performance of the metal mixtures, it is important to consider their limitations, including high costs due to their nickel and copper composition and processing difficulties that require specialized equipment.
Monel Alloys: Key Types and Their Properties
Among the most notable Monel materials, Monel 400 stands out for its exceptional corrosion resistance and remarkable strength, which meet the monel specification, making it a preferred choice in marine environments where exposure to seawater is prevalent. The electrical resistivity of this material is notable as well, measured at 0.511 Microhm-cm at 21°C and 307 Microhm-in at 70°C, further indicating its robust performance under varying conditions. However, it is crucial to note that oxidizing impurities such as:
- Ferric chloride
- Ferric sulfate
- Chromates
can cause significant attack in environments that would otherwise be mild for alloy 400.
Variants such as 404 and K-500 enhance the properties of 400, with K-500 being particularly distinguished by its age-hardening capability, which aligns with the monel specification, resulting in superior strength and hardness. Real-world applications demonstrate the effectiveness of K-500 in extreme conditions, solidifying its position as a reliable material for demanding environments. Furthermore, alloy 400’s adaptability is exemplified in case studies on its hot working; operating within a temperature range of 1200°F to 2150°F allows for the formation of various shapes while enhancing mechanical properties and reducing grain sizes.
This versatility emphasizes the significance of comprehending the unique attributes of these materials, as highlighted in the key points, enabling procurement managers to choose the most appropriate option tailored to specific project requirements.
Applications of Monel Alloys in Industry
Certain metal mixtures are essential to various industries, especially in marine, chemical processing, and petrochemical sectors, because of their distinctive characteristics. In marine environments, Model is widely utilized for components such as propeller shafts and seawater valves, thanks to its exceptional corrosion resistance, which is crucial for longevity in harsh conditions. However, copper metal mixtures also play a significant role in marine engineering, being extensively utilized in ship hulls, offshore platforms, and seawater piping systems.
Their excellent corrosion resistance makes them a superior choice in these applications compared to stainless steel. Moreover, copper mixed metals are extensively utilized in electronics, heat exchangers, and coinage, demonstrating their adaptability. In the automotive sector, both copper and similar materials are preferred for hydraulic systems and brake lines, utilizing their durability against corrosion.
Furthermore, in the chemical processing sector, its strong capacity to endure harsh chemicals renders it a perfect selection for piping systems and storage tanks, similar to copper and its mixtures. Recent insights indicate that the nickel content in these materials can significantly affect their performance, with experimental studies highlighting a reduction from 66.5 wt% to 17.6 wt% in dealloyed layers, underscoring the importance of precise monel specification. Expert evaluations, like those from Chintakindi, highlight the essential role of proper heat annealing and parametric optimization in maximizing the efficiency of drilling components that adhere to the monel specification for Monel-400 material.
Additionally, a case study on Multi-objective Particle Swarm Optimization (MOPSO) illustrates how optimization techniques can enhance machining parameters for specific metals, leading to improved performance outcomes. The experimental configuration involved heating the 400 metal in a furnace to specific temperatures over a defined cycle, which is crucial for understanding the material’s performance and monel specification. These varied uses demonstrate the importance of strict compliance with both specific copper and copper nickel standards to guarantee optimal performance across all industrial functions.
Overall, the benefits of copper nickel mixtures over stainless steel, especially in marine and electrical fields, further emphasize their importance in various sectors.
Compliance and Standards for Monel Specifications
Certain alloys are governed by a range of industry standards, notably including the monel specification, which dictate their composition, mechanical properties, and testing methods. Adherence to these stringent standards is crucial for guaranteeing that the 400 alloy products fulfill vital performance requirements for safety and reliability in challenging environments. For instance, ASTM B164 specifically outlines the requirements for alloy 400, mandating a chemical composition containing at least 63% nickel and 28-34% copper, along with defined mechanical properties.
Thorough testing and quality assurance procedures, including tension assessments and hydrostatic evaluations, are performed to ensure that the 400 alloy pipes and tubes meet high standards, guaranteeing the integrity and performance of the materials in challenging environments. This adherence not only enhances product quality but also promotes international trade, as it guarantees these materials can effectively support industries, especially in marine sectors, chemical processing, and oil and gas, where corrosion resistance and durability are crucial. Industry expert Sato from the J Research Institute emphasizes the significance of these specifications, stating:
The inflammability ranking is as follows (from the lowest flammability): copper, alloy 400, nickel, tin-bronze (BC 3).
By ensuring compliance with ASTM standards, the performance and integrity of these materials are significantly enhanced, enabling their deployment in a wide array of applications worldwide.
Advantages of Monel Alloys Compared to Other Materials
These alloys stand out for their exceptional properties, particularly in environments where corrosion resistance and durability are paramount, as outlined in the monel specification. Significantly, this material is harder than many varieties of stainless steel, including 316 stainless steel, which further emphasizes its superior performance. In scenarios involving chloride exposure, this alloy meets the monel specification, exhibiting a level of corrosion resistance that surpasses that of stainless steel, which can be prone to pitting.
This alloy meets the monel specification, making it a favored material in chemical and marine uses where exposure to harsh conditions is common. Moreover, the strength-to-weight ratio of these materials is especially beneficial in aerospace fields, where reducing weight without sacrificing strength is essential. Their excellent weldability facilitates easier fabrication and assembly, a feature that engineers and procurement managers highly value.
The case study titled ‘Strength Comparison of Monel and Stainless Steel‘ highlights that while both materials are strong, the monel specification demonstrates high tensile strength and toughness in extreme temperatures, making it ideal for chemical and marine environments. As HXM Anna aptly stated,
Suppliers are important because they help clients choose the most suitable metal materials for their projects by providing advice on a particular alloy’s properties and applications.
Consulting with experts like Wieland Diversified can provide valuable insights for procurement professionals, helping them make strategic material choices that meet specific project needs.
Conclusion
Monel alloys represent a pivotal choice in advanced materials, particularly for industries that face demanding environmental challenges. With their unique composition, characterized by high nickel and copper content, these alloys deliver remarkable strength and corrosion resistance, making them invaluable in applications ranging from marine engineering to chemical processing. Understanding the distinct properties of key variants like Monel 400 and Monel K-500 allows procurement managers to make informed decisions that align with project requirements.
The diverse applications of Monel alloys underscore their versatility and reliability. From marine components that withstand harsh seawater conditions to critical elements in chemical processing, the performance of Monel in extreme environments is well-documented. Moreover, adherence to stringent industry standards, such as ASTM specifications, ensures that these materials meet the highest performance criteria, thereby enhancing safety and reliability across various sectors.
Ultimately, the advantages of Monel alloys over traditional materials, particularly in terms of corrosion resistance, strength, and weldability, position them as a superior choice for procurement professionals. As industries continue to evolve and demand materials that can withstand increasingly challenging conditions, Monel alloys will remain at the forefront, offering strategic solutions that enhance operational efficiency and longevity. Embracing these materials not only meets current industry needs but also paves the way for innovation and excellence in future applications.