Blogs
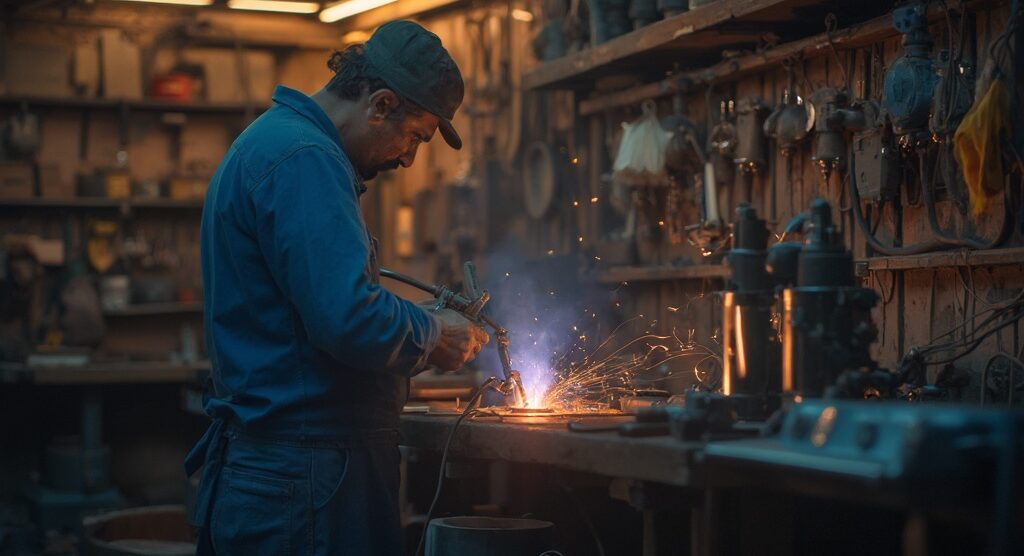
What Temperature is Brazing Done At? A Comprehensive Overview
Introduction
Brazing is a critical process in metal joining that demands precision and expertise, particularly when it comes to temperature control. With temperature ranges typically spanning from 450°C (842°F) to 1200°C (2192°F), understanding the nuances of brazing temperatures is essential for professionals in various industries, including:
- Automotive
- Electronics
- Aerospace
Each brazing technique—whether torch, furnace, dip, or induction—has its unique temperature requirements that influence the quality and strength of the joint. Additionally, factors such as:
- Material composition
- Joint design
- Filler metal properties
play pivotal roles in determining the ideal brazing temperature. As technology advances, the integration of high-performance materials like Mica Tape not only enhances safety and reliability during the brazing process but also addresses the challenges posed by thermal and electrical hazards. This article delves into the intricacies of brazing temperatures, exploring best practices and industry applications that ensure optimal results in metal joining.
Understanding Brazing Temperatures: What You Need to Know
Brazing is a crucial joining technique that involves the application of heat to melt a filler substance, creating a strong bond between two or more base materials. To understand what temperature is brazing done at, one should note that the brazing heat generally ranges from 450°C (842°F) to 1200°C (2192°F), with specific intervals like BCo-1’s 2050-2100°F (1120-1149°C) and 2100-2250°F (1150-1230°C) being crucial based on the base alloys and filler materials used. Achieving the correct temperature, which raises the question of what temperature is brazing done at, is crucial as it ensures that the filler metal adequately flows into the connection without compromising the structural integrity of the base metals.
This precision is especially crucial in sectors such as automotive and electronics, where the strength of the connection directly impacts performance and safety. Furthermore, the use of Mica Tape products, including Mica Sheet Tape and Insulating Mica Tapes, known for their high-temperature resistance and excellent electrical insulation properties, can complement joining processes, particularly in applications requiring additional safety measures against thermal and electrical hazards. Recent progress in joining technology, including research on flow properties of filler metals, emphasizes the importance of optimizing heat levels to improve connection strength and reduce voids in larger openings.
As noted in a case study, better flowing alloys can penetrate smaller gaps, but excessive flow in larger gaps may lead to voids, emphasizing the need for a balance in flow characteristics. Such insights are reflected in the work of researchers like Zhang et al., who studied the joining mechanisms pertinent to diamond wire saws, highlighting the complex relationship between heat and the resulting mechanical properties of the bonds created. Dalton O’Brien of Johnson Matthey Metal Joining highlights the significance of these discussions, stating, ‘Understanding the flow characteristics and their connection to brazing levels is crucial for attaining optimal bond strength.’
For procurement managers, integrating Mica Tape solutions not only enhances the reliability of these applications but also provides effective materials that can be evaluated based on their specific properties, ensuring safety and performance in critical applications.
Brazing Techniques and Their Temperature Requirements
Brazing includes a range of techniques, each defined by particular heat requirements, leading to the inquiry of what temperature is brazing done at to achieve optimal joint quality. The primary methods include:
- Torch Brazing: This commonly utilized technique uses a flame to heat the components, and it typically operates at what temperature is brazing done at, which ranges from 850°C (1562°F) to 1200°C (2192°F). Its versatility makes it suitable for a diverse array of metals.
- Furnace Brazing: In this method, components are heated in a controlled furnace environment, ensuring uniform heat distribution. The usual heat range for this process raises the question of what temperature is brazing done at, which is between 600°C (1112°F) and 1100°C (2012°F).
- Dip Brazing: This method entails submerging components in a liquid bath of filler substance, requiring elevated heat levels frequently surpassing 1000°C (1832°F). This method is particularly effective for complex geometries and large assemblies.
- Induction Brazing: Utilizing electromagnetic induction, this technique enables rapid heating, efficiently reaching levels between 600°C (1112°F) and 1200°C (2192°F), prompting the inquiry of what temperature is brazing done at.
Understanding what temperature is brazing done at is essential, as it guarantees the filler substance melts and flows correctly while avoiding harm to the base materials. Factors such as the type of filler metal, the size, and thickness of the parts significantly influence what temperature is brazing done at, as highlighted in the case study titled ‘Factors Affecting Copper Brazing Temperature.’ For instance, the assembly brazed at 900 °C for 5 minutes achieved a maximum shear strength of 27 MPa, illustrating what temperature is brazing done at and underscoring the importance of precise temperature control in enhancing the quality of the connection.
As noted, “according to the mechanical property tests, the joint brazed at what temperature is brazing done at 900 °C for 5 min obtains the maximum shear strength of 27 MPa.” In applications where high-temperature resistance and electrical insulation are critical, Mica Tape products can play a significant role. Their excellent thermal properties make them suitable for use in environments where joining occurs, providing additional insulation and protection against heat.
By recognizing these variations and their implications, professionals can make informed choices regarding the most suitable joining method for specific materials and applications, as well as the integration of Mica Tape for enhanced performance.
Factors Influencing Brazing Temperature Selection
Choosing the suitable joining heat is essential for obtaining robust and dependable connections, and several important aspects must be taken into account:
Material Composition: The kinds of alloys being fused have a crucial influence on establishing the required joining heat levels. For example, high-strength alloys tend to require higher temperatures, prompting the inquiry of what temperature is brazing done at compared to softer materials. The influence of material selection is underscored by research conducted by Zhang et al., who examined the brazing mechanisms and machining performance of a Cu-Sn-Ti alloy, highlighting how composition directly affects thermal requirements.
Combined Design: The arrangement of the connection, including gap size and surface area, has a profound impact on heat transfer and filler alloy flow. A good rule of thumb for lap connection length is to make it three times the thickness of the thinner member, as this can significantly affect the strength and integrity of the assembly. When considering tighter gaps, one might ask what temperature is brazing done at to ensure adequate penetration of the material. As noted by metallurgist Gray, the drop in strength at tighter joint clearances is attributed to flux inclusions, which underscores the importance of careful joint design.
Filler Material Properties: The melting points of various filler substances must align with the base materials to create a successful bond. Copper-phosphorus alloys are frequently used in automotive applications due to their ability to join pure copper without flux, although they can be brittle when used with nickel or iron alloys. The development of the OKC600 copper-based filler substance exemplifies how tailored compositions can enhance performance in modern applications like copper-brass heat exchangers, enabling them to compete effectively with aluminum systems.
Heating Method: The technique of heat application—whether through torch, furnace, or induction—can help identify what temperature is brazing done at for effective joining. Recent research suggests that the enhancement in strength of fused connections compared to the filler substance alone is due to connection shape preventing necking, thus allowing for greater nominal loads.
Furthermore, it is essential to consider the use of Non-Sparking Tools during the fusion process, particularly in settings with explosive potential. These tools enhance safety by minimizing the risk of sparks that could ignite flammable materials. By understanding these factors and their interplay, professionals can customize their joining processes to achieve optimal results, ensuring the integrity and durability of metal joints in various applications.
Common Applications of Brazing and Their Temperature Considerations
Brazing acts as a key joining method in multiple sectors, with particular heat considerations adapted to each application:
Automotive Industry: In this sector, joining is crucial for connecting components such as radiator cores and exhaust systems. The usual melting point varies from 600°C (1112°F) to 1000°C (1832°F), which raises the question of what temperature is brazing done at, ensuring the connections can withstand high-stress situations without sacrificing integrity. Residual stresses in these joints can reach several hundred megaPascals, highlighting the critical need for precise temperature control. Domadia’s Mica Tapes, recognized for their outstanding flame resistance and dielectric strength, can offer extra insulation in these applications, safeguarding delicate components from thermal harm during the joining process.
Electronics: The electronics sector depends on welding for connecting heat exchangers and circuit boards. In this context, heat regulation is essential; joining is typically carried out at reduced levels between 450°C (842°F) and 600°C (1112°F) to protect delicate components from possible thermal harm. Utilizing Mica Insulation Tape in electronic assemblies can further enhance safety by providing electrical insulation and flame resistance, ensuring long-lasting performance.
HVAC Systems: In HVAC applications, soldering is indispensable for assembling systems that must function reliably under varying thermal conditions. To understand what temperature is brazing done at, it’s important to note that the necessary brazing heat levels generally vary from 800°C (1472°F) to 1100°C (2012°F), ensuring that joints can endure thermal cycling without failure. Mica Sheet Tape from Domadia can be valuable in these systems, ensuring robust insulation against high heat, which is essential for maintaining system efficiency.
Aerospace: The aerospace industry demands the highest standards of performance and reliability. Brazing is employed to join critical components, often necessitating precise temperature control above 1000°C (1832°F), leading to the question of what temperature is brazing done at to ensure the integrity and performance of high-performance materials used in this field. An example of the technique’s effectiveness is seen in its application to connect thin sections, such as honeycomb cores in sandwich panels, which can be challenging for other joining methods. The brazed connection area is often stronger than the core itself due to lower stresses, making it advantageous in high-performance applications. In this context, Insulating Mica Tapes can improve the overall safety and dependability of these joints.
A thorough understanding of these applications and their respective heat requirements is essential for professionals aiming to optimize welding processes. According to mechanical property tests, the joint brazed at 900 °C for 5 min obtains the maximum shear strength of 27 MPa. By aligning these considerations with industry-specific needs and leveraging high-temperature insulation solutions like Domadia’s Mica Tapes, procurement managers can enhance safety, reliability, and overall performance in their projects.
To explore our range of Mica Tapes and learn more about how they can benefit your business, visit our website or contact our expert team today.
Best Practices for Managing Brazing Temperatures
Achieving optimal joining results necessitates a strategic approach to managing temperatures effectively. Here are several best practices that can significantly enhance the quality and reliability of joining operations:
- Preheat Components: Implementing preheating techniques can mitigate thermal shock and facilitate better filler substance flow, particularly in thicker materials. This practice not only readies the base metals for joining but also improves connection integrity.
- Monitor Heat Accurately: Utilizing precise heat measurement tools, such as thermocouples or infrared thermometers, ensures that the brazing process adheres to the desired ranges. Accurate monitoring is crucial, especially when considering what temperature is brazing done at, as even slight deviations can adversely affect overall performance.
- Control Heating Rate: A slow rise in warmth is crucial to avoid warping or distortion of base materials. This is particularly critical in sensitive applications where maintaining dimensional accuracy is paramount.
- Use Appropriate Flux: Choosing the right flux is essential to enhancing the flow of the filler metal, thereby improving bond strength. This is particularly relevant at reduced heating levels, where the flux can play a crucial role in achieving a strong connection.
- Conduct Post-Process Inspections: Routine evaluations of connections after the process are essential for detecting any problems associated with heat control. These evaluations allow for timely adjustments in future processes, ultimately contributing to improved outcomes.
These practices not only align with the latest insights from industry research but also reflect the findings of notable studies. For example, a recent study on the melting heat and duration effects on TiC cermet/Ag–Cu–Zn/steel connections revealed that ideal conditions, specifically what temperature is brazing done at—850 °C for 15 minutes—achieved a maximum shear strength of 95.7 MPa. However, surpassing the parameters related to what temperature is brazing done at led to harmful performance of the connections, highlighting the essential importance of careful heat management. Song et al. speculated that elevated joining temperatures could harm the properties of joints, further emphasizing the necessity of sustaining optimal conditions. Additionally, the preparation of 7075 aluminum alloys involved cutting them into specified dimensions and removing the oxide film through Ar ions bombardment, a crucial step that improves the joining process. This research was supported by the National Natural Science Foundation of China and the Key Research & Development program of Shandong Province, underscoring the significance of the findings. By implementing these best practices, professionals can significantly boost the performance of their brazing applications, ensuring they meet the increasingly stringent demands of 2024.
Conclusion
Understanding the intricacies of brazing temperatures is essential for achieving strong, reliable metal joints across various industries. The article highlights the critical temperature ranges for different brazing techniques—torch, furnace, dip, and induction—and emphasizes the importance of precise temperature control. Factors such as material composition, joint design, and filler metal properties significantly influence the selection of the optimal brazing temperature.
Moreover, the integration of high-performance materials like Mica Tape not only enhances safety and reliability but also addresses thermal and electrical hazards that can arise during the brazing process. As demonstrated through case studies and expert insights, achieving the ideal brazing temperature is paramount in ensuring joint strength and performance while mitigating risks associated with overheating or inadequate bonding.
In conclusion, professionals in the field must prioritize a thorough understanding of brazing temperatures and the associated best practices. By leveraging the latest advancements in technology and materials, along with a strategic approach to temperature management, procurement managers can enhance the quality and durability of their brazed joints. This commitment to excellence will ensure optimal performance in critical applications, paving the way for safer and more reliable metal joining solutions in the future.