Blogs
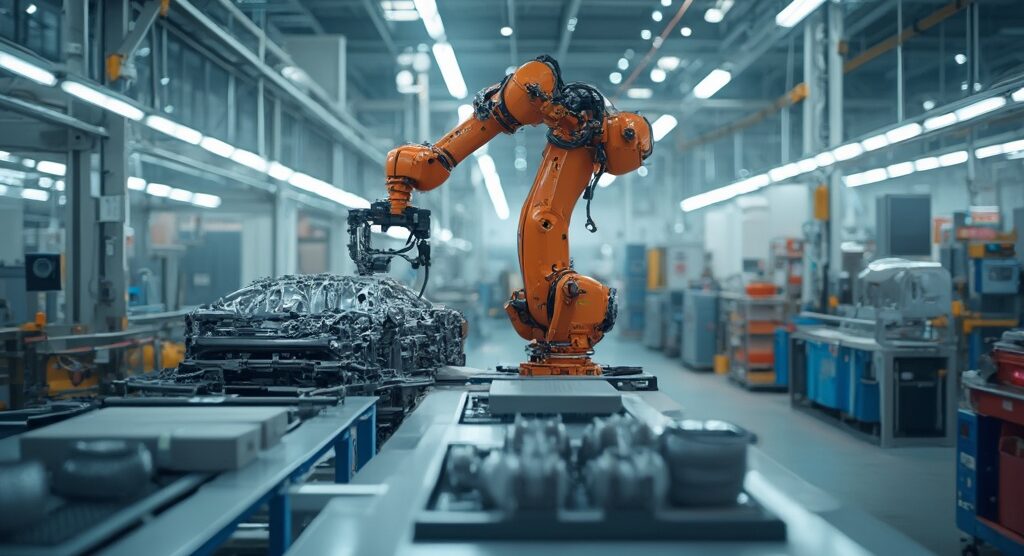
Best Practices in Manufacturing Automotive Metal Components
Introduction
The automotive industry is undergoing a profound metamorphosis, driven by rapid technological advancements and evolving consumer preferences. Key trends reshaping automotive component manufacturing include the adoption of lightweight materials, the integration of smart technologies, and the rise of electric vehicles (EVs). Lightweight materials are pivotal for enhancing fuel efficiency and meeting stringent regulatory standards, with the Asia-Pacific region leading this change.
The global lightweight materials market for EVs is projected to witness exponential growth, reaching $50.78 billion by 2031.
Furthermore, smart manufacturing technologies are revolutionizing production processes, offering real-time insights and optimization to improve efficiency and reduce waste. The increasing demand for EVs is driving manufacturers to utilize lightweight materials for various components to enhance performance and sustainability. By aligning production strategies with these trends, manufacturers can stay competitive, meet market demands, and adhere to regulatory standards.
Trends Shaping Automotive Component Manufacturing
The automotive industry is undergoing significant transformation driven by technological advancements and shifting consumer preferences. One of the most notable trends is the adoption of lightweight substances, crucial for enhancing fuel efficiency and meeting stringent regulatory requirements. The Asia-Pacific area, especially China and India, is driving this transformation because of its swiftly growing economies and substantial production base. The global lightweight materials market for electric vehicles, valued at $3.36 billion in 2020, is projected to reach $50.78 billion by 2031, growing at a compound annual growth rate (CAGR) of 25.4%.
Moreover, the integration of smart technologies into automotive components is revolutionizing production processes. These advancements allow for real-time insights and optimization, significantly enhancing efficiency and reducing waste. For example, the use of high-performance substances (HPMS) and industrial IoT in manufacturing processes is becoming increasingly common, facilitating the development of flexible production systems that can quickly adjust to market demands.
The rise of electric vehicles (EVs) is another major trend reshaping the industry. The demand for lightweight substances in EVs is driven by the need for longer battery life and adherence to environmental regulations. Producers are progressively employing lightweight substances for battery packs, exterior trims, and interior components to improve vehicle performance and lower expenses. This shift not only contributes to sustainability but also aligns with global efforts to reduce carbon emissions.
In summary, remaining competitive in the automotive sector necessitates adopting these essential trends: the use of lightweight substances, intelligent production technologies, and the increase of electric vehicles. By aligning production strategies with these developments, manufacturers can ensure they meet evolving market demands and regulatory standards.
Advanced Materials Integration
Incorporating advanced substances such as high-strength steels, aluminum alloys, and composites is crucial in the production of automotive components. These substances not only enhance performance but also significantly decrease weight and improve durability. For instance, press hardening technology transforms boron steel into ultra high strength steel, which is three times more stable than its original form. This makes it extremely strong relative to its weight, thereby contributing to the production of lighter and more fuel-efficient vehicles.
Producers must evaluate the particular advantages of each substance and take into account application requirements for elements such as pistons, trims, and wipers. The transition towards Industry 4.0 and the adoption of virtual assembly techniques enable manufacturers to reduce the number of physical prototypes, cutting down on time and costs. This is essential as the conventional vehicle development cycle, which lasts three to five years, can be improved by utilizing advanced substances and technologies.
Furthermore, the increase in demand for lightweight and durable substances across various sectors has spurred innovation in the science of materials. For example, using a laser to melt magnesium wire under a shielding gas can create lighter and stronger components than those made of steel or aluminum. This method is not only more energy-efficient but also environmentally friendly, making it a promising alternative for automotive applications.
In conclusion, the strategic incorporation of advanced materials and innovative processes will enable automotive manufacturers to meet evolving performance and sustainability standards while maintaining cost-effectiveness.
Quality Assurance and Control
Ensuring the integrity of automotive components requires robust quality assurance and control mechanisms. ‘Implementing stringent testing protocols and leveraging advanced inspection technologies are critical steps in identifying defects early in the manufacturing process.’. For instance, the use of automated visual inspection systems has been demonstrated to improve quality control, increase productivity, and reduce waste. A continuous improvement approach, incorporating operator notes and images of defective parts stored in an ERP system, can guide trend analysis initiatives and help maintain high-quality standards.
As emphasized by industry specialists, the merging of technologies such as the Industrial Internet of Things (IIoT) and artificial intelligence creates new opportunities for productivity and competitiveness. However, realizing this potential demands a strategic and holistic approach to digital transformation. Quality is now a boardroom agenda, impacting focus areas such as sustainability. In this context, adopting best practices in quality engineering, including the integration of generative AI, can significantly enhance engineering skills and productivity.
For example, recent industry reports have shown that customer satisfaction with automotive service quality remains a key metric, with longer appointment wait times driving more customers to aftermarket service facilities. This underscores the importance of maintaining high standards in quality control to enhance customer satisfaction and trust.
Cost-Effective Production Strategies
To maintain a competitive edge, manufacturers must prioritize optimizing operations to reduce costs while upholding high quality standards. Adopting lean manufacturing principles can significantly streamline operations by minimizing waste and enhancing efficiency. For example, Jubilant Ingrevia’s execution of digital transformation strategies in their Acetic Anhydride manufacturing facility led to a decrease in output losses by over 30% and an increase in workforce efficiency by more than 20%.
Incorporating just-in-time inventory management further refines the production process by ensuring that materials and components are available exactly when needed, thereby reducing inventory costs and minimizing storage space requirements. Additionally, automation technologies play a crucial role in enhancing operational performance. ‘Despite recent economic challenges, the demand for robotics in sectors like automotive production has seen notable growth, with a 14.4 percent increase in orders during the first half of 2024.’.
Investing in workforce training and development is another critical strategy for boosting productivity and efficiency. As the manufacturing landscape continues to evolve, equipping employees with the necessary skills to handle advanced technologies is essential. This approach not only improves production outcomes but also fosters a more adaptable and resilient workforce. By focusing on these strategies, manufacturers can navigate the complexities of the modern market and achieve sustained growth and competitiveness.
Common Challenges and Solutions in Automotive Sheet Metal Fabrication
Automotive sheet metal fabrication faces significant challenges such as material deformation, precision alignment, and surface finish issues. Tackling these complexities demands advanced fabrication techniques and a skilled workforce. For example, Lantek’s new software, Lantek v43, provides an improvement in process speed and productivity by introducing automatic and intelligent tools that simplify daily tasks in sheet metal production. ‘As stated by Juan José Colás, Chief Sales and Marketing Officer of Lantek, the software improves machinery and equipment usage while promoting the digital transformation of production processes, ensuring agility, productivity, and long-term business sustainability.’.
Simulation software plays a pivotal role in anticipating potential issues before they arise, allowing for preemptive adjustments. Additionally, regular training programs are essential to equip workers with the necessary skills to handle these challenges effectively. Derek Hammer, president of Hammer MetalWerks, emphasizes the importance of technology in making operators’ jobs easier and helping them get up to speed faster, which is crucial given the shortage of highly skilled operators. As the automotive industry evolves towards Industry 4.0, integrating these advanced techniques and tools can significantly enhance production efficiency and sustainability, aligning with the broader shift towards more optimal and sustainable vehicle manufacturing.
Conclusion
The automotive industry is at a pivotal juncture, driven by the integration of lightweight materials, smart technologies, and the surging demand for electric vehicles. The strategic adoption of lightweight materials not only enhances fuel efficiency but also plays a crucial role in meeting stringent regulatory standards. The Asia-Pacific region is at the forefront of this transformation, with the global lightweight materials market for EVs projected to experience exponential growth in the coming years.
Incorporating advanced materials such as high-strength steels and aluminum alloys is essential for manufacturers aiming to improve performance and durability while reducing vehicle weight. The transition to Industry 4.0, along with innovative production techniques, allows for a more agile manufacturing process, ultimately reducing costs and timeframes. Additionally, the importance of robust quality assurance and control mechanisms cannot be overstated, as they ensure product integrity and customer satisfaction, which are vital for maintaining competitiveness in a rapidly evolving market.
Cost-effective production strategies, including lean manufacturing and just-in-time inventory management, further refine operations, allowing manufacturers to navigate economic challenges efficiently. Emphasizing workforce training and development equips employees with the skills necessary to manage advanced technologies, fostering a more resilient and adaptable workforce.
Ultimately, aligning production strategies with these key trends and innovations is essential for automotive manufacturers. By embracing lightweight materials, advanced technologies, and effective operational strategies, manufacturers can not only meet current market demands but also position themselves for sustained growth and success in the future.