Blogs
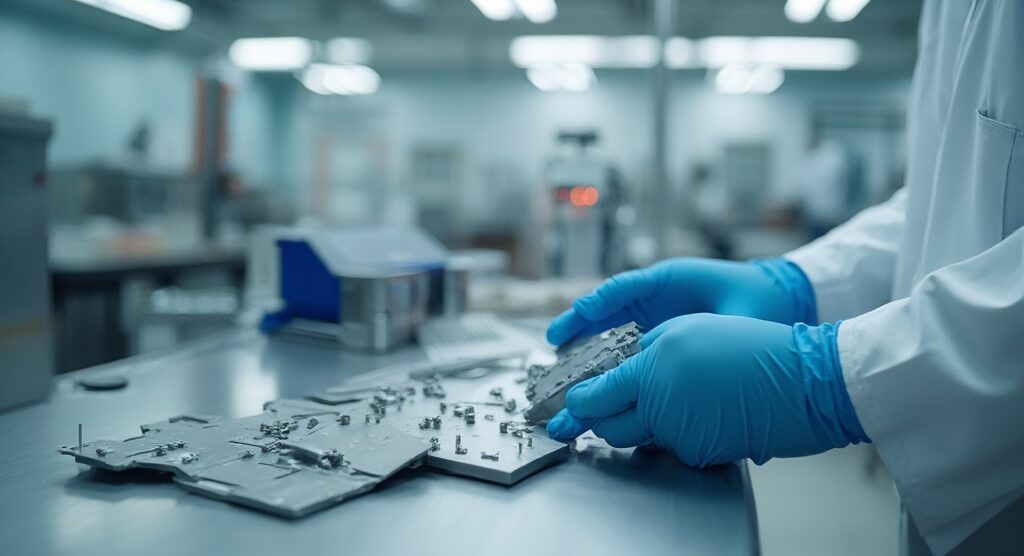
Exploring the Comprehensive Properties of Titanium Metal in Engineering
Introduction
Titanium stands as a paragon of advanced materials in modern engineering, renowned for its remarkable physical, chemical, and mechanical properties. With an exceptional strength-to-weight ratio, high corrosion resistance, and the ability to withstand extreme temperatures, titanium has secured its place in critical industries such as aerospace, automotive, medical, and military. This article delves into the multifaceted attributes of titanium, exploring its diverse applications, the various grades tailored for specific industrial needs, and the benefits it bestows upon engineering endeavors.
Additionally, it addresses the inherent challenges and limitations associated with titanium, offering a comprehensive understanding of why this material remains indispensable despite its complexities.
Physical Properties of Titanium
Titanium is renowned for its extraordinary physical characteristics, notably its high strength-to-weight ratio. With a density of approximately 4.5 g/cm³, it is significantly lighter than steel while maintaining comparable strength, making it an indispensable material in industries requiring high performance. High-strength metal forgings, created through a meticulous process, exemplify this property, providing outstanding mechanical traits suitable for aerospace, automotive, medical, and military uses.
Titanium’s excellent corrosion resistance is another key attribute, attributed to the formation of a protective oxide layer that enables it to endure harsh environments, including seawater and acidic conditions. Studies on Ti-Al-V alloys produced through spark plasma sintering emphasize this durability, rendering them appropriate for essential uses in various sectors.
Furthermore, the metal’s high melting point of approximately 1,668 °C (3,034 °F) aids its application in elevated temperature situations. This asset is especially valuable in sectors such as aerospace, where materials are subjected to extreme thermal conditions. The blend of these characteristics highlights the usefulness and adaptability of this metal, establishing it as a preferred material for contemporary engineering challenges.
Chemical Properties of Titanium
Titanium, a transition metal, is renowned for its high reactivity, particularly with oxygen, nitrogen, and hydrogen. This characteristic leads to the formation of various alloys, which can significantly influence the metal’s properties. For instance, this metal’s high affinity for oxygen necessitates meticulous handling during fabrication processes to prevent contamination and embrittlement. This reactivity presents both challenges and opportunities in processing this metal. High-strength metal forgings, recognized for their outstanding mechanical characteristics, are created through rigorous manufacturing processes to guarantee optimal performance in sectors such as aerospace, automotive, medical, and military. The careful management of this metal’s reactivity is crucial in maintaining the integrity and superior qualities of these advanced materials.
Mechanical Properties of Titanium
Titanium is renowned for its exceptional mechanical properties, making it a preferred choice in high-performance applications. With a tensile strength that can range from 240 MPa to an impressive 1,200 MPa, depending on the alloy and treatment, this metal stands out for its strength and durability. The modulus of elasticity for this metal is approximately 110 GPA, which, while lower than that of steel, contributes to its lightweight nature and ease of use in various industries.
‘High-strength metal forgings, produced through stringent manufacturing processes, offer unparalleled strength and are vital in sectors such as aerospace, automotive, medical, and military.’. These forgings are made from the highest quality of metal, ensuring both lightweight and strong performance. This makes them ideal for applications where both strength and efficiency are paramount.
Moreover, the metal’s ability to maintain its strength at elevated temperatures underscores its suitability for environments where thermal stability is crucial. This is especially pertinent in the aviation sector, which has encountered considerable supply chain difficulties due to shortages of a certain metal. The aerospace sector’s dependence on the metal for essential components emphasizes its significance, particularly in light of recent disruptions in global supply chains.
The lasting need for this metal in advanced air mobility and other innovative uses further highlights its vital importance in contemporary engineering. As sectors keep advancing and looking for sustainable alternatives, titanium stays at the forefront because of its outstanding characteristics and adaptable uses.
Applications of Titanium in Engineering
Titanium’s unique properties make it indispensable in various engineering applications. In the aerospace industry, its high strength-to-weight ratio and resistance to extreme temperatures and corrosion make it ideal for airframes and engine components. Despite recent supply chain challenges, including a shortage of the metal exacerbated by geopolitical issues in Ukraine, the material remains crucial for maintaining the integrity and performance of aircraft. Boeing’s dependence on this metal highlights its significance, with continuous efforts to diversify supply sources to reduce risks.
In the medical field, the biocompatibility and durability of this metal make it a preferred material for implants and prosthetics. Its ability to integrate well with human tissue reduces the likelihood of rejection and extends the lifespan of medical devices, contributing significantly to patient care and outcomes. The demand for advanced materials in medical applications is driven by the need for innovative solutions to meet evolving regulatory standards and healthcare needs.
The automotive sector also benefits from the characteristics of this metal. Components manufactured from a lightweight metal assist in lowering vehicle mass, resulting in better fuel economy and increased performance. This is particularly important as the industry seeks to meet stringent environmental regulations and consumer demand for high-performance vehicles.
In chemical processing, the remarkable resistance to corrosion of this metal makes it suitable for use in harsh environments. The metal’s ability to withstand aggressive chemicals and high temperatures ensures the longevity and reliability of processing equipment, thereby reducing maintenance costs and downtime.
Overall, the adaptable uses of this metal across these sectors underscore its essential role in progressing technology and enhancing efficiency, safety, and performance.
Grades of Titanium and Their Uses
Titanium’s versatility is best illustrated through its various grades, each designed for specific uses. Grade 1 titanium, renowned for its outstanding corrosion resistance, is frequently employed in chemical processing environments. Grade 2 strikes a balance between strength and ductility, making it a popular choice for industrial applications. For high-performance demands, such as those in aviation, Grade 5 (Ti-6Al-4V) stands out due to its exceptional strength and toughness, ideal for critical engineering tasks. Choosing the suitable grade of this metal is crucial to utilize its characteristics efficiently for particular industrial requirements.
Benefits of Using Titanium in Engineering
Titanium offers numerous advantages in engineering, making it a highly sought-after material. Its remarkable strength-to-weight ratio allows for lighter designs without compromising structural integrity, an essential aspect in sectors such as aviation and automotive. Titanium’s remarkable corrosion resistance extends the lifespan of components, significantly reducing maintenance costs. ‘This is especially advantageous in the aerospace industry, which has been struggling with supply chain issues, particularly due to the recent shortages of a certain metal caused by geopolitical tensions in Ukraine.’.
Furthermore, this metal’s biocompatibility makes it indispensable in medical applications, from surgical instruments to implants, ensuring safety and reliability. Original Equipment Manufacturers (OEMs) in the medical device sector heavily depend on a certain metal to meet stringent regulatory standards, such as ISO 13485 and FDA requirements. Its ability to withstand high temperatures also makes it invaluable in aerospace engineering, where it contributes to the performance and reliability of critical components.
In essence, this metal’s distinct characteristics improve performance and reliability across various high-performance applications, reinforcing its significance in both current and future technological advancements.
Challenges and Limitations of Titanium
Titanium, despite its numerous advantages, does not come without its set of challenges. One of the primary barriers to its widespread adoption is its high cost relative to other metals. This financial hurdle can be particularly daunting for industries operating under stringent budget constraints. Furthermore, the machining and welding of this metal require specialized techniques and equipment, which adds layers of complexity to production processes. The risks of embrittlement and contamination during processing are also significant concerns that need to be meticulously managed to preserve the metal’s desirable properties.
The aerospace sector, for example, has been notably impacted by these challenges. According to Toma Matutyte, CEO of Locatory.com, the shortage of this metal has sent shockwaves through the Maintenance, Repair, and Overhaul (MRO) sector, emphasizing the urgent need for agile supply chain solutions. This shortage is partly due to geopolitical factors, such as the disruption of supply from Ukraine, historically a major producer.
Furthermore, the reliance on data-driven approaches in manufacturing, such as those used in cutting and grinding operations, can help mitigate some of these challenges by optimizing production efficiency and reducing costs. Nevertheless, understanding and addressing these challenges is crucial for effective titanium procurement and application across various sectors.
Conclusion
Titanium’s remarkable properties and diverse applications underscore its significance in modern engineering. Its high strength-to-weight ratio, excellent corrosion resistance, and ability to withstand extreme temperatures make it an essential material across critical industries, including aerospace, automotive, medical, and military sectors. The various grades of titanium, each tailored for specific applications, further enhance its versatility, allowing for optimal performance in demanding environments.
However, the advantages of titanium are tempered by challenges such as high costs, specialized machining requirements, and risks of embrittlement during processing. Recent geopolitical events have exacerbated supply chain issues, highlighting the need for strategic procurement practices and agile supply solutions. As industries continue to innovate and evolve, understanding both the benefits and limitations of titanium is crucial for effective application and maximizing its potential.
In summary, titanium remains an indispensable material in engineering, driving advancements and improving efficiencies across various sectors. Its unique characteristics not only enhance performance but also contribute to the sustainability of engineering solutions in the face of modern challenges. Recognizing and addressing the complexities associated with titanium will ensure its continued relevance and utility in future technological developments.