Blogs
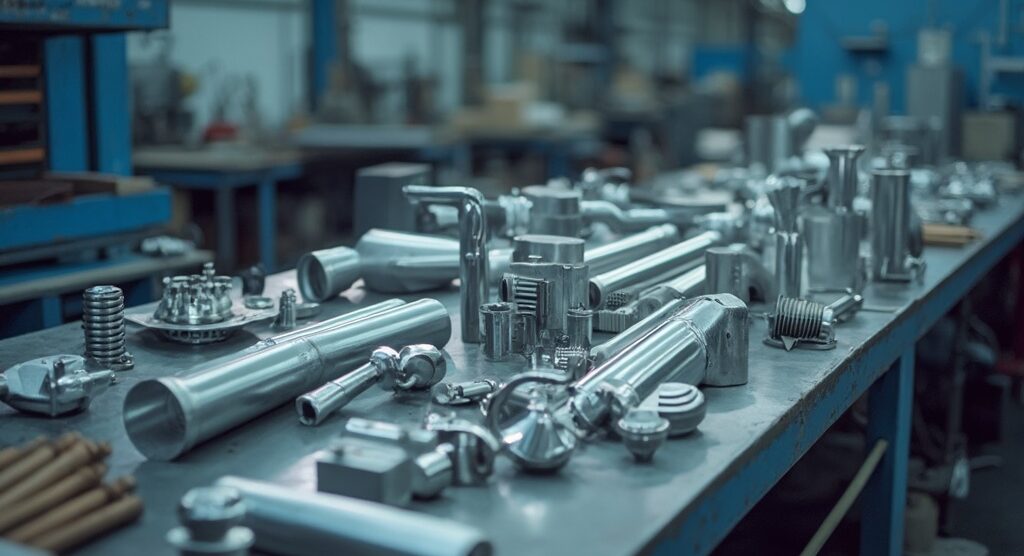
Exploring the Role of Alloy Nickel in Modern Manufacturing Processes
Introduction
Nickel alloys are pivotal in modern engineering, renowned for their exceptional properties and versatile applications. Combining nickel with elements such as chromium, molybdenum, and iron, these alloys offer unparalleled corrosion resistance, high-temperature stability, and mechanical strength. These characteristics make them indispensable in industries ranging from aerospace to automotive and chemical processing.
As global demand for more efficient and sustainable solutions escalates, the need for robust materials like nickel alloys becomes increasingly critical. This article delves into the properties, applications, advantages, industry-specific uses, and fabrication processes of nickel alloys, shedding light on their vital role in advancing technology and industrial performance.
Properties of Nickel Alloys
Nickel mixtures stand out for their superior corrosion resistance, remarkable high-temperature stability, and impressive mechanical strength. By merging elements such as chromium, molybdenum, and iron, these materials attain improved characteristics that are crucial for demanding conditions. Their excellent fatigue strength and consistent performance across a wide temperature range make them indispensable in industries such as aerospace, automotive, and chemical processing. The aerospace industry, especially, has experienced an increase in need for metal mixtures because of their crucial function in aircraft parts, fueled by substantial orders from Boeing and Airbus. This heightened demand emphasizes the essential requirement for nickel mixtures in aiding the worldwide movement towards sustainable energy options, such as electric cars and renewable energy frameworks.
Applications of Nickel Alloys
Nickel mixtures play a critical role across diverse industries due to their unique properties. The aerospace industry depends significantly on these materials for parts like turbine blades and exhaust systems, owing to their outstanding heat resistance and durability. This demand is set to rise further with significant new orders from Boeing and Airbus, driving up prices and potentially impacting supply chains.
In the automotive sector, nickel-based mixtures are essential for producing fuel cells and battery parts, in line with worldwide efforts for sustainable energy and electric vehicles. The chemical sector also gains advantages from these materials, employing them in piping and valves where resistance to corrosion and chemical assaults is crucial.
‘The growing need for nickel in aerospace, along with its application in energy infrastructure such as LNG terminals, highlights the material’s importance.’. However, this increased need could lead to scarcity, affecting availability and pricing, and posing challenges for industries reliant on this critical material.
Advantages of Nickel Alloys in Manufacturing
Nickel alloys present numerous benefits in manufacturing. Their exceptional strength-to-weight ratio allows for lightweight designs without sacrificing structural integrity. This is especially vital in areas like aerospace, where the need for high-performance materials is skyrocketing. According to recent reports, the global aerospace industry’s recovery has boosted the need for this metal, driven by massive new orders from major airlines and aircraft manufacturers. This demand is expected to increase by around 65% by the decade’s end, partly due to the transition towards clean energy technologies.
Furthermore, certain metal mixtures show exceptional durability against high temperatures and harsh conditions. This attribute significantly reduces maintenance costs and prolongs the lifespan of components, making them an economical choice despite initial higher costs. Their ability to withstand harsh conditions is being tested rigorously in high-temperature oxidation environments, aiming for applications in nuclear fusion reactors, hypersonic flights, and high-temperature jet engines.
Furthermore, the adaptability of nickel mixtures in enduring various environmental pressures results in improved performance and efficiency in production methods. This reliability is increasingly vital as industries strive for more sustainable and cost-effective solutions. Researchers and engineers continue to innovate, developing multi-principal element materials to meet stringent design goals for strength, toughness, and corrosion resistance.
These factors collectively make nickel mixtures a preferred choice for engineers and designers who seek to balance performance, durability, and cost-efficiency in their projects.
Industry-Specific Uses of Nickel Alloys
Nickel blends are essential in numerous sectors, each utilizing their distinct characteristics for particular uses. In the oil and gas sector, these materials are essential for downhole tubing and drilling equipment, thanks to their exceptional resistance to sour environments. This is particularly critical as the worldwide need for energy continues to rise, and the durability of materials used in extraction processes becomes even more crucial.
In the electronics sector, nickel-based mixtures are employed for connectors and circuit boards because of their outstanding conductive characteristics. Their reliability and efficiency in transferring electrical signals make them a preferred choice in high-performance electronic devices. With the ongoing advancements in technology, the need for such robust materials is set to increase.
The aerospace sector is another major user of these metal mixtures, motivated by their high strength, resistance to corrosion, and mechanical characteristics. The resurgence in global travel has led to a surge in aircraft orders, with Boeing and Airbus receiving over 2,400 new orders combined. This heightened need is driving up the costs of alloy materials, which could affect other industries such as renewable energy and electric vehicles that also depend significantly on this adaptable metal.
Nickel’s role in the energy transition cannot be overstated. As clean energy technologies rapidly emerge, there is a growing need for a specific metal in energy storage solutions. The International Energy Agency forecasts a 65% rise in consumption by the end of the decade. This surge in demand highlights the significance of sustainable practices in metal production to satisfy future requirements without jeopardizing environmental integrity.
The adaptability of certain metal mixtures enables them to be customized for specific uses, improving their function in various production methods. At Morgan Advanced Materials, our goal is to use advanced materials to solve complex problems and improve the quality of life. By concentrating on application engineering and ongoing development, we guarantee that these metal mixtures stay at the cutting edge of innovation and efficiency across various sectors.
Fabrication Processes for Nickel Alloys
‘The creation of nickel mixtures employs advanced methods to preserve their integrity and improve performance.’. Methods like forging, welding, and casting are carefully customized to the particular thermal and mechanical characteristics of each metal mixture. Precision machining is crucial, ensuring components meet exacting tolerances. Surface treatments, including advanced corrosion resistance enhancements, are often applied to meet stringent sector standards.
Seco, a leader in metal cutting solutions, exemplifies excellence in high-precision machining, leveraging over 80 years of experience to address the challenges in manufacturing. Similarly, the Department of Energy’s AMMT program promotes advancements in materials and manufacturing technologies, crucial for reliable and economical energy solutions.
‘The aerospace sector’s increasing need for nickel-based materials, fueled by fresh requests from Boeing and Airbus, underscores the significance of these manufacturing methods.’. ‘This request not only impacts energy applications but also emphasizes the need for sustainable manufacturing practices, as demonstrated by Sandvik Coromant’s significant progress in reducing carbon emissions.’.
Through a combination of traditional techniques and modern innovations like 3D printing and data-driven optimization, the fabrication of nickel alloys continues to evolve, ensuring high-quality outputs that meet the demands of various high-stakes industries.
Conclusion
Nickel alloys are essential across various industries, valued for their outstanding corrosion resistance, high-temperature stability, and mechanical strength. By combining nickel with elements like chromium and molybdenum, these alloys play a critical role in sectors such as aerospace, automotive, and chemical processing. The rising demand for sustainable energy solutions, especially in electric vehicles and renewable energy, further highlights their significance.
In aerospace, nickel alloys are crucial for components that endure extreme conditions, while in automotive applications, they are vital for efficient fuel cells and battery systems. This growing demand may lead to supply chain challenges, stressing the need for strategic procurement and resource management.
The benefits of nickel alloys extend beyond their basic properties. Their impressive strength-to-weight ratio and resistance to harsh environments enhance performance and reduce long-term maintenance costs, making them a preferred choice for engineers. Continuous innovations in alloy development reflect a commitment to meeting stringent design requirements.
Advanced fabrication processes, including precision machining and surface treatments, ensure that nickel alloys meet high industry standards. The evolving manufacturing landscape underscores the importance of these materials in achieving both performance and sustainability goals.
In conclusion, nickel alloys are critical components driving innovation across multiple sectors. Their unique properties and applications position them as vital to pursuing sustainable solutions and advanced manufacturing practices. Strategic use of nickel alloys will be essential for future industry success.
Explore our range of high-performance nickel alloys today to meet your sustainable energy needs!