Blogs
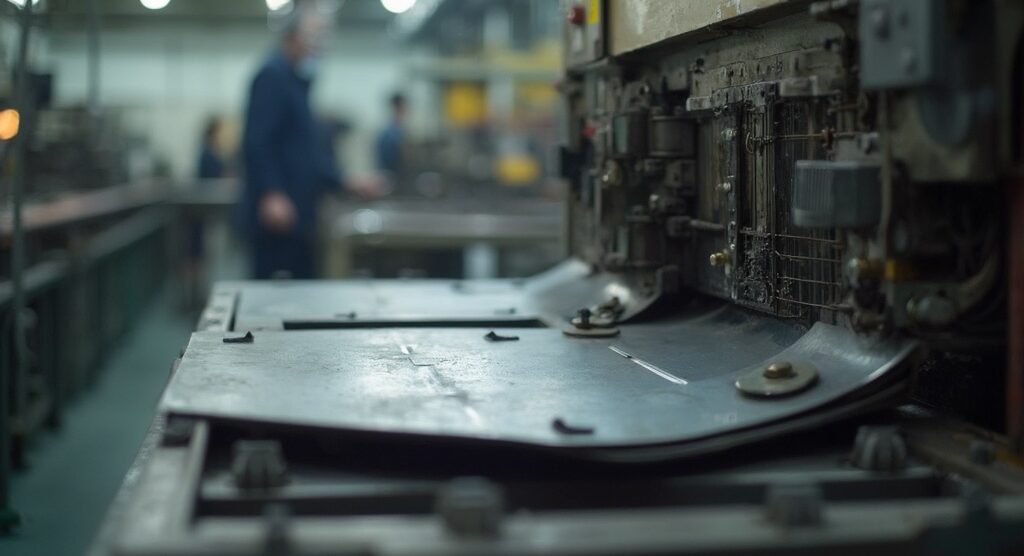
Case Study: Effective Techniques for Creating Stamping Drawings
Introduction
Metal stamping is a cornerstone of modern manufacturing, offering precision and efficiency across various industries. This article delves into the specialized techniques of metal stamping, including progressive die stamping, deep draw stamping, and fourslide stamping, each tailored to meet distinct manufacturing requirements. It explores the detailed processes and benefits of progressive die stamping, highlighting its role in high-volume production and the importance of consistent quality and reduced waste.
The article further examines critical design considerations for metal stamping, emphasizing the meticulous alignment of material specifications with design requirements to ensure optimal performance and reliability. Additionally, it discusses secondary processing techniques, such as heat treating and surface finishing, which enhance the strength and quality of stamped parts. By maintaining stringent quality control and integrating advanced technologies, manufacturers can achieve the high standards demanded by industries such as automotive and electronics, ensuring reliability and consistency in the final product.
Types of Metal Stamping Techniques
Metal shaping involves several specialized techniques, each tailored to meet distinct manufacturing requirements. Key methods include progressive die pressing, deep draw pressing, and fourslide pressing. Progressive die forming is frequently utilized in high-volume manufacturing to produce complex parts with strict tolerances. Deep draw forming, vital for creating components with considerable depth, is critical in sectors such as automotive, where parts must withstand harsh conditions, including vibrations and temperature changes. Metrics such as fatigue resistance and impact strength are vital in this sector. Fourslide forming, recognized for its flexibility, enables intricate bends and configurations, making it perfect for the electronics sector where accuracy and miniaturization are crucial. Comprehending these methods ensures that the chosen billet bars and metal specifications match perfectly with the intended pressing process, thereby guaranteeing reliability and consistency in the final product. Ongoing quality management and the embrace of contemporary technologies, such as robotics and automation, further improve the effectiveness and accuracy of metal forming processes, fulfilling the high expectations prevalent across different sectors.
Progressive Die Stamping: Detailed Process and Benefits
Progressive die stamping is a highly efficient technique for high-volume production, where material is fed through a series of dies that incrementally shape the part. This method ensures consistent quality and reduces waste, making it ideal for industries with strict reliability requirements. For instance, in the automotive sector, components must endure extreme conditions such as vibrations, temperature fluctuations, and long-term wear. ‘Metrics such as fatigue resistance and impact strength are essential, with guidelines like ISO/TS 16949 dictating quality criteria to ensure safety and durability.’. The choice of billet bars is critical in this process, as they must withstand repetitive mechanical stresses, thus enhancing the overall durability of the final product. Continuous monitoring and quality assurance practices are essential to identify trends and implement corrective actions, ensuring that stamped products meet the high standards expected by clients and end-users.
Design Considerations for Metal Stamping
When producing imprint drawings, several critical design considerations must be taken into account to ensure optimal performance and reliability. These include material thickness, bend radii, and features such as holes and notches. The specifications of the billet bars must be meticulously aligned with these design requirements to optimize the stamping process. For instance, the automotive industry demands components that can endure extreme conditions, such as vibrations and temperature fluctuations. Measurements such as fatigue resistance and impact strength are essential, as detailed in specifications like ISO/TS 16949, which impose strict quality requirements for safety and durability.
Well-crafted illustrations not only aid in efficient production but also guarantee that the final product fulfills the required performance criteria. By maintaining stringent quality control and assurance practices, manufacturers can ensure that their stamped products are reliable and consistent. Continuous monitoring and analysis of production data help identify trends or potential areas of improvement, allowing for the implementation of corrective actions when necessary. This holistic approach guarantees that the final product fulfills the high expectations held by clients and end-users across various industries.
Secondary Processing: Enhancing Part Strength and Surface Quality
Secondary processing techniques, like heat treating or surface finishing, play a crucial role in enhancing the strength and surface quality of stamped parts. To ensure optimal outcomes, the specifications of the initial billet bars must align with the intended secondary processes. Certain materials, such as high-strength steels, exhibit superior responses to these treatments, making them ideal choices for demanding applications.
A comprehensive method for choosing and handling materials is crucial, concentrating on industry-specific reliability requirements and expectations. For instance, the automotive industry prioritizes safety and durability, with components required to withstand extreme conditions such as vibrations, temperature fluctuations, and long-term wear and tear. Measurements such as fatigue resistance and impact strength are essential in this sector, as emphasized by automotive criteria such as ISO/TS 16949.
Implementing stringent quality control and assurance practices throughout the production process is imperative. Continuous monitoring and analysis of production data help identify trends and areas for improvement, ensuring that stamped products consistently meet high standards. As noted by experts, maintaining reliability and consistency in production is vital for meeting client and end-user expectations.
‘Incorporating advanced technology and innovative solutions, as demonstrated by leading companies like Seco, can further optimize the manufacturing journey.’. By leveraging decades of toolmaking experience, manufacturers can achieve high-precision machining and superior output quality, thus fulfilling the stringent requirements of modern industries.
Conclusion
Metal stamping is an essential process in modern manufacturing, characterized by a variety of specialized techniques that cater to distinct industry needs. Progressive die stamping, deep draw stamping, and fourslide stamping each offer unique advantages, from high-volume production capabilities to intricate design flexibility. Understanding the nuances of these methods ensures that manufacturers can select the appropriate materials and processes, ultimately leading to reliable and consistent products.
The benefits of progressive die stamping are particularly noteworthy, emphasizing efficiency and waste reduction. This technique is vital in sectors like automotive, where components must meet rigorous standards for strength and durability. Consistent quality control and adherence to industry benchmarks, such as ISO/TS 16949, are crucial to achieving the desired performance, especially in challenging environments.
Design considerations play a pivotal role in the success of metal stamping operations. Proper alignment of material specifications with design requirements is imperative to optimize the stamping process and ensure that final products can withstand extreme conditions. The integration of secondary processing techniques, such as heat treating and surface finishing, further enhances the strength and quality of stamped parts, reinforcing the importance of meticulous planning and execution.
By leveraging advanced technologies and maintaining stringent quality assurance practices, manufacturers can meet the high standards demanded by various industries. A strategic approach to metal stamping not only ensures the reliability and consistency of products but also positions manufacturers to excel in a competitive landscape.