Blogs
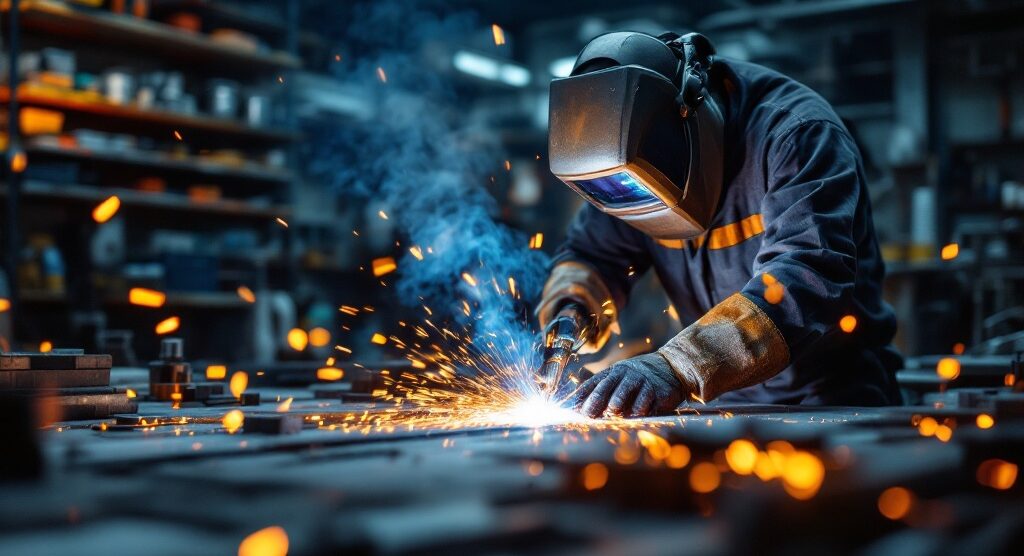
How to Weld Inconel: A Comprehensive Step-by-Step Guide
Introduction
Inconel, a family of austenitic nickel-chromium-based superalloys, stands at the forefront of materials engineering, particularly due to its exceptional resistance to heat and corrosion. With a composition that typically includes over 50% nickel and 20% chromium, Inconel alloys are indispensable in high-temperature applications across industries such as aerospace, chemical processing, and nuclear energy.
Understanding the properties, treatment processes, and welding techniques associated with Inconel is crucial for procurement managers and engineers who seek to optimize performance and ensure longevity in demanding environments. This article delves into the intricacies of Inconel, exploring its applications, the preferred TIG welding methods, essential preparation steps, challenges faced during welding, and the importance of post-welding inspections.
Through a strategic approach, organizations can harness the full potential of Inconel, ensuring that their components not only meet but exceed performance expectations.
Understanding Inconel: Properties and Applications
This material represents a distinguished family of austenitic nickel-chromium-based superalloys, characterized by their remarkable resistance to heat and corrosion. Generally containing at least 50% nickel and 20% chromium, these alloys excel in high-temperature environments, making them particularly valuable for aerospace, chemical processing, and nuclear reactor applications. Their exceptional ability to retain tensile strength and oxidation resistance under extreme temperature fluctuations is crucial for components such as gas turbine engines and heat exchangers.
Recent advancements in the application of nickel-chromium alloy, particularly in aerospace contexts, have further solidified its role as a critical material. For instance, the tensile properties of this alloy can be significantly enhanced through specific treatment processes, including:
- Solution treatment at 1800°F (982°C) for 1 hour
- Precipitation treatment at 1325°F (718°C) for 8 hours
This comprehension of the alloy’s characteristics and treatment methods is crucial for enhancing joining techniques and material choice, ensuring that components fulfill performance standards and durability needs in challenging operational environments.
Additionally, Mica Tape products, such as Mica Insulation Tape and Mica Tape for Electrical, provide essential solutions for high-temperature resistance and electrical insulation across diverse applications. These tapes offer excellent flame resistance and dielectric strength, making them indispensable in the manufacture of fire-resistant cables and other critical electrical insulation systems. The high mechanical strength of Mica Sheet Tape also makes it suitable for insulating large flat surfaces in challenging environments, such as those found in the aerospace and automotive industries.
As Muralidhara Reddy inquired about the feasibility of cold working the alloy 718 for the production of hex bolts, it highlights the ongoing exploration of its versatility in various applications, reaffirming its indispensable role in modern engineering.
Welding Techniques for Inconel: The Role of TIG Welding
TIG (Tungsten Inert Gas) processes stand out as the preferred technique on how to weld inconel alloys, renowned for its ability to produce high-quality, precise joints. By employing a non-consumable tungsten electrode coupled with an inert gas—predominantly argon—this technique is crucial for understanding how to weld inconel while effectively safeguarding the weld area from atmospheric contamination. Successful TIG fusion is essential for understanding how to weld inconel, as it relies on keeping a stable arc and carefully managing heat input to prevent warping and guarantee consistent penetration across the connection.
When learning how to weld inconel, it is essential to choose a filler substance that corresponds with the specific alloy grade being welded, as this decision directly affects the integrity of the connection.
Recent advancements in TIG welding methods have further optimized the process. For instance, studies have demonstrated that the prediction error for hardness in Inconel 600 welded connections ranges from 0.6% to 1.9%, indicating a high level of precision achievable through careful technique. A significant case study, titled ‘Temperature Measurement and Hardness Correlation,’ established a robust relationship between temperature in the heat-affected zone (HAZ) and hardness in welded joints.
This research discovered that as linear energy input rises, so does hardness in the joint area, highlighting the significance of effective temperature regulation during the joining process. It is also significant that the width of the HAZ differs with various current settings, which can greatly impact the overall joint quality. Moreover, the study contains comprehensive tables of chemical compositions and joining parameters for different superalloys, providing valuable insights into how to weld inconel and the factors affecting TIG processes for specific alloys.
Expert insights are invaluable in understanding these advancements. Chunfu Guo observes the ‘Effect of Fast-Frequency Pulsed Current Parameters on FFP-TIG Arc Behavior and Its Implications for Alloy 718 Joining,’ emphasizing how innovative methods can improve the quality of joints. By concentrating on these best practices, including careful selection of welding parameters and monitoring of HAZ width, procurement managers can ensure superior results in their welding operations, making TIG welding the optimal choice for high-quality nickel-chromium alloys.
Preparation Steps for Successful Inconel Welding
Thorough preparation of alloy workpieces is essential for attaining high-quality joints. Begin the process by meticulously cleaning the surfaces to eliminate contaminants such as oil, dirt, and oxidation—common culprits in joint defects. While some may suggest wire brushing, LC—a veteran in welding this special alloy—advises utilizing a roto file to ensure the removal of oxidation effectively, stating, ‘This material has a lot of oxidation on the surface… by wire brushing it all you are doing is shining the surface.’
This emphasizes the significance of employing the appropriate cleaning technique for the best outcomes. After cleaning, ensure proper alignment of the components, minimizing gaps to avoid irregular joints. Preheating the alloy to a temperature between 300°F and 500°F is advised, as it helps to relieve thermal stresses and improve joint quality.
After joining, polishing the joint surface using a buffing wheel or sanding disc is essential for achieving a smooth and uniform finish, further enhancing the quality of the connection. Lastly, confirm that the equipment is properly set up: sharpen the tungsten electrode and prepare the correct filler material. For joining nickel-chromium alloys, it is important to understand how to weld inconel using Inconel 625 as the top filler metal, which guarantees compatibility and performance throughout the joining procedure.
A case study demonstrates these challenges: Matt shares his experience of struggling to connect a tee structure in nickel-chromium during a test, expressing frustration over the material’s behavior and his lack of access to practice tools. Veteran welders offered insights into common pitfalls and recommended techniques to improve his chances of success, such as fusing the joint first and using small tack welds to stabilize the weld area.
Challenges and Best Practices in Welding Inconel
Welding nickel-chromium alloys, particularly alloy 718, poses notable challenges, primarily due to their inherent susceptibility to cracking and distortion, which is crucial to understand when learning how to weld inconel. Alloy 718 is extensively used in critical applications within the aerospace, nuclear power, and petrochemical industries, making it essential to adopt a strategic approach to mitigate these issues. Controlling heat input is paramount, as excessive heat can induce warping and compromise weld integrity.
Choosing the suitable filler material that aligns precisely with the alloy grade is essential when considering how to weld inconel to avoid issues like hot cracking. A case study titled ‘Conclusions on Inconel 718 Welds’ reveals that metallurgical issues, including hot cracking and Laves phase formation, can be mitigated by employing low heat input joining processes and high Mo content fillers. Recent studies on multi-pass welding techniques have shown promise in distributing heat more evenly across the joint, thus minimizing the risk of thermal distortion.
Furthermore, employing post-weld heat treatments is essential for relieving residual stresses and enhancing the mechanical properties of the weld. Notably, E. Thompson, a specialist in Materials Science and Engineering, emphasizes the importance of these practices:
- ‘Hot ductility tests, gas-tungsten-arc filler fusion tests, and circle patch-weld-restraint tests were conducted on a specific alloy to better understand and correlate the weldability/resistance to cracking.’
Such insights emphasize the necessity of adopting meticulous welding practices, especially in understanding how to weld inconel, to address the challenges posed by these alloys.
Post-Welding Inspection and Testing for Inconel Joints
Post-welding inspections of Inconel connections are crucial for those learning how to weld Inconel to ensure structural integrity and reliability in operational environments. The inspection process should commence with a visual assessment aimed at identifying surface imperfections such as cracks or porosity. Following this initial check, non-destructive testing (NDT) methods—such as ultrasonic testing (UT) and radiographic testing (RT)—offer profound insights into the internal quality of the joints, mitigating the risk of undetected flaws.
Recent advancements in NDT have significantly enhanced detection capabilities, underscoring its vital role in the quality assurance of welded joints. For instance, statistics indicate that the concentration of nickel in the joining metal near the interface is measured lower than that in the metal itself (51.45%). This discrepancy could potentially affect the joint’s performance under stress, making it imperative to monitor and control this parameter during the welding process.
Additionally, mechanical testing, including tensile and Charpy impact tests, assesses the performance of the welded connections under realistic operational conditions. Notably, as reported by Amit Kumar Chandan Pandey, in Charpy impact testing of NVG and DVG welded connections, specimens failed in two parts with a small amount of plastic deformation, yielding impact energies of 99 ± 4 J for NVG welds and 91 ± 3 J for DVG welds. This emphasizes the critical nature of mechanical testing in evaluating the reliability of welded connections.
Furthermore, case studies on how to weld Inconel joints, including those that explore various laser welding techniques for Inconel 718, reveal that specific NDT methods significantly reduce failure rates in real-world applications. These findings emphasize the essential role these technologies play in safeguarding operational integrity and ensuring compliance with industry standards.
Conclusion
Inconel’s exceptional properties make it a cornerstone material in high-temperature and high-stress applications across various industries, including aerospace, chemical processing, and nuclear energy. Understanding its composition, treatment processes, and the specific welding techniques required—particularly TIG welding—ensures that components can withstand the rigors of demanding operational environments. The meticulous preparation steps, which include effective cleaning, proper fit-up, and appropriate preheating, are essential in preventing defects and ensuring the integrity of welds.
Despite the advantages of Inconel, challenges such as susceptibility to cracking and distortion underscore the importance of strategic welding practices. Employing low heat input and selecting the right filler materials are crucial to mitigating these issues. Moreover, post-welding inspections and testing, including non-destructive testing methods, play an invaluable role in ensuring the reliability and structural integrity of Inconel joints.
Ultimately, organizations that adopt a comprehensive approach to working with Inconel—ranging from careful material selection and welding practices to thorough inspection processes—will not only optimize performance but also extend the longevity of their components. As the industry continues to evolve, leveraging the full potential of Inconel will be paramount in meeting and exceeding performance expectations in challenging environments.