Blogs
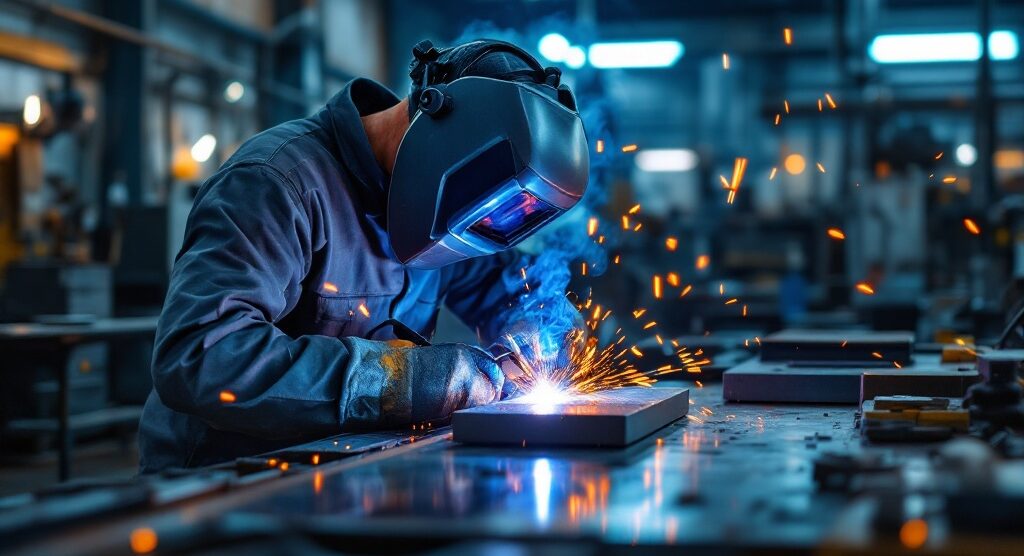
Inconel Metal Welding Tutorial: Techniques and Best Practices Explained
Introduction
Inconel alloys represent a remarkable category of superalloys that are engineered to perform under the most demanding conditions. Their unique composition, characterized by a blend of nickel and chromium, bestows them with unparalleled resistance to corrosion and high-temperature stability, making them essential in industries ranging from aerospace to chemical processing.
As procurement managers navigate the complexities of sourcing these specialized materials, understanding their properties and applications becomes crucial. This article delves into the intricacies of Inconel alloys, exploring effective welding techniques, best practices, and the challenges faced during the welding process.
It also highlights innovative trends shaping the future of Inconel welding, providing valuable insights for professionals committed to optimizing performance and ensuring compliance in their operations.
Understanding Inconel Alloys: Properties and Applications
Certain alloys are a sophisticated family of austenitic nickel-chromium-based superalloys, recognized for their exceptional performance in extreme environments. Their unique mechanical properties, including superior corrosion resistance and high-temperature stability, make them indispensable in critical industries such as aerospace, chemical processing, and power generation. For instance, this alloy is esteemed for its outstanding fatigue and thermal-fatigue strength, boasting a tensile strength of 690 MPa and a yield strength of 276 MPa, qualities that render it particularly suitable for aerospace components where reliability is paramount.
Dean McClements, a B. Eng Honors graduate in Mechanical Engineering, emphasizes the importance of understanding these properties as they guide the inconel metal welding process and are crucial for aligning with strategic sourcing considerations in procurement. Moreover, the composition of these alloys—including nickel (Ni), molybdenum (Mo), and iron (Fe)—ensures precision manufacturing, which is critical for achieving exceptional mechanical performance and enhancing structural integrity and longevity. Additionally, in environments with explosive potential, the use of non-sparking tools is critical, providing a safe alternative for applications where risk mitigation is essential.
By choosing the suitable mixture tailored to specific applications, procurement managers can enhance performance outcomes while ensuring compliance with industry standards. Insights from consumer analysis of the flange market indicate that factors such as supplier reputation and sustainability practices significantly influence purchasing decisions, underscoring the real-world implications of these substances in procurement.
Effective Welding Techniques for Inconel: The Role of TIG Welding
TIG welding is acknowledged as the top method for joining specific metals, mainly because of its ability to produce clean, precise, and strong joints. This technique utilizes a non-consumable tungsten electrode, which aids the joining process, supplemented by the inclusion of filler substance when required. Critical to the success of inconel metal welding through TIG joining is the meticulous control of heat input; improper management can lead to warping or the compromise of the alloy’s inherent properties.
To achieve optimal results, utilizing a direct current (DC) with reverse polarity is recommended, as it enhances arc stability and allows for better control over heat input. For applications involving thicker materials, the adoption of pulsed TIG technique is advisable. This method not only improves heat control but also enhances penetration, ensuring a strong and durable bond.
Significantly, the as-welded joint strength attains 60% of that of the base metal, highlighting the effectiveness of this joining technique. Additionally, a case study titled ‘Characterization of Interfacial Microstructure in Friction Welds Between Inconel 718 and SM45C Steel’ emphasizes the challenges associated with inconel metal welding and highlights the successful results attained through meticulous parameter control. As Chunfu Guo aptly notes in his research on welding parameters, ‘Effect of Fast-Frequency Pulsed Current Parameters on FFP-TIG Arc Behavior and Its Implications for a Specific Metal 718 Joining,’ understanding these parameters is key to mastering the intricacies of joining these materials effectively.
Best Practices for Welding Inconel: Tips and Techniques
To attain optimal outcomes during inconel metal welding, following best practices is crucial. Key recommendations include:
- Select appropriate filler substances: It is critical to choose a filler substance that is compatible with the alloy type to ensure optimal weld strength and integrity. For example, utilizing the filler for the base alloy significantly improves performance and longevity. Utilizing a filler substance is essential to successfully bond metal components without fracturing. As mentioned in a recent case study, inconel metal welding with the right filler substance, such as Inconel 625, ensures the durability and effectiveness of the welds in high-temperature applications.
- Implement preheating techniques: Preheating the material not only minimizes the risk of cracking but also enhances the flow characteristics of the weld pool, leading to a more uniform weld. Experts recommend considering the specific characteristics of the alloy when determining the preheating temperature.
- Control heat input: It is advisable to utilize lower amperage settings to prevent overheating, which can cause distortion and diminish corrosion resistance. Maintaining precise control over heat input is vital for achieving high-quality welds.
- Maintain a clean workspace: Ensuring that work surfaces are free from contaminants such as oil, rust, or dirt is crucial, as these impurities can significantly impact weld quality. Recent guidelines emphasize that a clean environment is a fundamental aspect of successful fabrication practices.
- Stay updated on best practices: According to industry experts, regularly reviewing and adapting joining techniques is necessary to align with the latest advancements. While the quote from Phoebe Han,
What is API 5L X70 PSL2 specification?
highlights the need for ongoing education, it would be more impactful to focus on quotes from specialists specifically addressing metal practices. Furthermore, it is important to highlight that GTAW is acknowledged as the optimal technique for joining Monel®, another nickel material, offering useful context for the techniques suitable for nickel materials. The changing characteristics of inconel metal welding require a dedication to comprehending and applying optimal methods as they progress.
Challenges in Inconel Welding: Overcoming Common Issues
Welding specialized metal mixtures, including inconel metal welding, presents multiple complex challenges that necessitate a strategic method to guarantee successful results. Key issues include:
High Thermal Expansion: Certain metal mixtures exhibit significant thermal expansion, which can result in warping if not managed effectively. This necessitates advanced heat management techniques to maintain dimensional integrity during the welding process.
Sensitivity to Cracking: This material is particularly susceptible to hot cracking, especially if preheating is inadequate or if the heat input exceeds recommended levels. To mitigate this risk, it is crucial to maintain a consistent travel speed and avoid overheating. Expert insights emphasize that careful control of these parameters during inconel metal welding can significantly reduce the likelihood of cracking, ensuring the integrity of the weld. As pointed out by A. Lingenfelter, the introduction of Inconel grade 718 represented a major advancement in the nickel-base superalloy category, particularly enhancing its applications in inconel metal welding due to its lack of sensitivity to strain-age.
Porosity: The presence of gas porosity is a common issue, often arising from contamination in the weld area. To combat this, rigorous attention to shielding gas coverage and the cleanliness of the base material is essential. Utilizing Weld Purge Monitors®, which can measure oxygen levels as low as 10 ppm, can provide the necessary control over the environment to prevent porosity, thereby enhancing weld quality. A case study on managing purge gas oxygen levels emphasizes how monitors such as the PurgEye® series guarantee low oxygen levels, which is essential for attaining high-quality nickel welds.
Tackling these challenges requires a combination of skill, experience, and appropriate equipment. Recent studies have highlighted the importance of meticulous preparation and execution in inconel metal welding, reinforcing that this process of joining nickel alloys is a sophisticated endeavor that benefits from strategic oversight and expert guidance.
Innovations in Inconel Welding: Future Trends and Technologies
The metal fabrication sector is in a phase of ongoing progress, especially in its methods for working with specialized alloys. Key innovations include:
- Ultrasonic Welding: This technique employs ultrasonic vibrations to generate frictional heat, allowing for high-quality welds without the need for filler metals. This method is gaining traction in inconel metal welding due to its ability to produce strong joints with minimal thermal distortion, making it an attractive option for Inconel applications.
- Automation and Robotics: The incorporation of automated joining systems is transforming the industry by improving precision and repeatability. These systems significantly reduce human error, leading to improvements in production efficiency and weld quality. As noted by industry expert Ahmed Abotaleb, the strategic implementation of these controls is anticipated to substantially improve the quality and consistency of joint outcomes.
- Advanced Filler Materials: The development of new filler alloys tailored for specific Inconel applications is another noteworthy trend. These advanced substances are designed to provide exceptional performance and compatibility, which is essential for attaining optimal outcomes in intricate joining situations. For instance, a recent case study titled “Estimating the Strengthening Contributions” quantified the various strengthening mechanisms at play in welded materials, providing a comprehensive understanding of their mechanical behavior.
- Real-Time Monitoring: The adoption of real-time monitoring technologies enables professionals to oversee joining parameters continuously. This capability is essential for maintaining optimal conditions throughout the fabrication process and for early detection of potential issues, thereby enhancing overall weld quality.
- Safety Features in Modern Machines: Modern machines, such as the YesWelder MIG205DS-B, are equipped with automatic shut-off systems that prevent overheating and reduce the risk of fire or explosion, showcasing advancements in safety technology.
Incorporating these innovations not only helps professionals keep pace with industry standards but also positions them to maintain a competitive edge in the market. Staying informed about the latest trends, such as the implementation of Model Predictive Control (MPC) for optimizing welding processes, is vital for procurement managers aiming for excellence in their operations.
Conclusion
Inconel alloys stand as a testament to engineering excellence, offering unmatched performance in extreme environments. Their unique properties, including remarkable corrosion resistance and high-temperature stability, make them indispensable across various industries, from aerospace to chemical processing. Understanding these attributes, alongside effective welding techniques like TIG welding, is essential for procurement managers seeking to optimize their operations. The careful selection of filler materials, control of heat input, and adherence to best practices are critical for achieving high-quality welds that meet rigorous industry standards.
However, the journey of welding Inconel is not without its challenges. Issues such as:
- High thermal expansion
- Susceptibility to cracking
- Gas porosity
require a strategic approach and skilled execution. By addressing these complexities with meticulous preparation and the right equipment, professionals can enhance the integrity of their welds, ensuring reliable performance in demanding applications.
Looking ahead, the welding landscape is evolving with innovative techniques and technologies that promise to further improve Inconel welding processes. From ultrasonic welding to real-time monitoring systems, these advancements are set to enhance precision, safety, and efficiency. As the industry continues to progress, staying abreast of these trends is crucial for procurement managers aiming to maintain a competitive edge and ensure compliance in their operations. Embracing these insights and innovations will ultimately lead to superior performance and sustainable success in the realm of Inconel welding.