Blogs
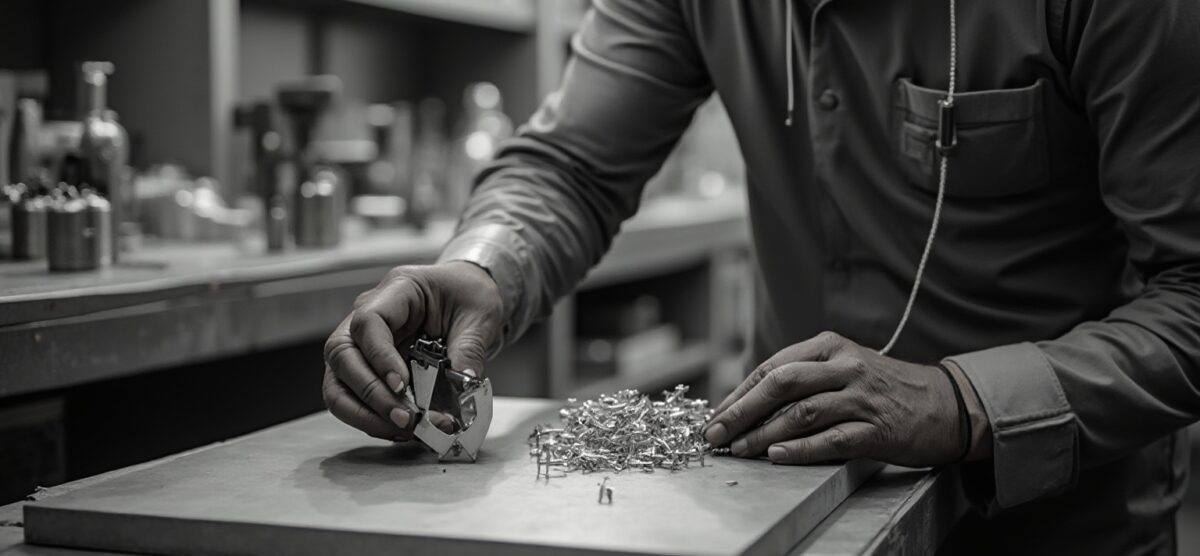
Understanding Monel K500 Yield Strength: An In-Depth Tutorial for Engineers
Overview
Monel K500 exhibits a yield strength of approximately 70 ksi (480 MPa), making it a highly durable and corrosion-resistant alloy suitable for demanding applications in industries such as marine, chemical processing, and oil and gas. The article supports this by detailing how heat treatment processes enhance its mechanical properties, particularly yield strength, while also emphasizing its exceptional performance characteristics in harsh environments, which are critical for engineering applications.
Introduction
In the realm of advanced materials, Monel K500 emerges as a powerful nickel-copper alloy, distinguished by its remarkable strength and exceptional resistance to corrosion. This alloy is not merely a choice but a strategic solution for industries that demand reliability in extreme conditions, such as:
- Marine
- Chemical processing
- Oil and gas sectors
With a yield strength that can reach up to 70 ksi (480 MPa) in its age-hardened state, Monel K500 is engineered to withstand the rigors of high-stress environments while maintaining structural integrity. As organizations seek to optimize their material selection, understanding the unique properties, heat treatment techniques, and diverse applications of Monel K500 becomes paramount. This article delves into the intricate characteristics of Monel K500, offering insights into its performance, corrosion resistance, and the best practices for leveraging its capabilities across various engineering applications.
Introduction to Monel K500: Properties and Applications
The nickel-copper alloy, a powerful material, is praised for its outstanding durability and resistance to corrosion, rendering it a perfect option for challenging uses. Notably, Nickelvac K-500™ contains 0.01% sulfur, which can influence its performance characteristics. In its age-hardened condition, this alloy demonstrates a monel k500 yield strength of approximately 70 ksi (480 MPa), which is instrumental in environments such as marine, chemical processing, and oil and gas industries.
Its resilience under harsh conditions ensures that the alloy maintains structural integrity, thus providing engineers with a dependable material for demanding uses. However, it is important to note that while this alloy is generally free from chloride stress corrosion cracking, only annealed material resists stress cracking in the presence of mercury or mercury salts, and it should not be used for nitric acid service. Furthermore, the exceptional mechanical characteristics of this alloy are further improved by its weldability and formability, enabling diverse uses in various engineering designs.
Notably, this alloy can be finish-machined to close tolerances, with best practices recommending that components be machined oversize prior to aging to optimize performance. Conventional plasma arc cutting systems can be effectively used for cutting a specific nickel-copper alloy, with a mixture of argon and hydrogen gases yielding the best results while avoiding oxygen-bearing gases to ensure better cut quality. In 2024, advancements in nickel-copper alloy applications continue to emerge, particularly in the chemical processing sector, where its resistance to stress corrosion cracking plays a pivotal role.
This alloy is particularly valued in marine environments, where its durability and resistance to corrosion from seawater are critical. The strategic application of this alloy in these sectors highlights its significance in modern engineering solutions.
Understanding the Mechanical Properties: Yield Strength of Monel K500
Yield resistance is a crucial mechanical characteristic that defines the maximum stress that this alloy can withstand without experiencing permanent deformation. Typically, when subjected to suitable aging treatments, the Monel K500 yield strength attains a resistance of approximately 70 ksi (480 MPa). This remarkable yield capacity, specifically the Monel K500 yield strength, makes it perfect for uses requiring materials able to endure high stress without the threat of failure.
Comprehending the numerous factors that affect yield capacity, including temperature, alloying elements, and heat treatment processes, is essential for engineers and procurement managers alike. Importantly, aging processes contribute greatly to improving yield durability, which is essential for optimizing the alloy’s Monel K500 yield strength for specific uses. Additionally, Monel alloy can be cold rolled to attain specific temper characteristics, further improving its performance in different uses.
In machining processes, the yield capacity directly affects parameters such as:
- Feed (0.13 mm/rev)
- Cutting speed (35 m/min)
- Depth of cut (1.02 mm)
These parameters are essential for effective material removal and tool longevity. Moreover, case studies illustrate that Alloy 500 is employed in various applications, such as chains, cables, pump parts, and marine instruments, highlighting its durability and resistance to corrosion. It is also essential to consider how Monel K500 yield strength interrelates with other mechanical properties, such as ductility and toughness, ensuring a comprehensive approach to material selection that meets specific operational requirements.
Importantly, according to NACE MR0175 / ISO 15156, Monel K500 can be used without restrictions on temperature, pH2S, Cl−, or in situ pH in production environments, reinforcing its practical implications in various industries.
Corrosion Resistance of Monel K500: Key Considerations
Q1. What are the typical uses of copper nickel alloys?
Copper nickel alloys are widely utilized in marine engineering for parts such as ship hulls, offshore platforms, and seawater piping systems.
They are also utilized in the automotive industry for brake lines and hydraulic systems due to their excellent corrosion resistance. Additionally, copper nickel alloys are utilized in electronics, heat exchangers, and coinage.
How does the alloy compare to copper nickel alloys regarding corrosion resistance?
The alloy is renowned for its superior resistance to a variety of corrosive environments, including seawater and acidic conditions. The alloy’s high nickel content plays a critical role in its resistance to stress corrosion cracking, while the addition of copper significantly enhances its resistance to pitting and crevice corrosion. When assessing the alloy for particular uses, a comprehensive analysis of the working environment is crucial, particularly in maritime contexts where the material’s capacity to endure the severe impacts of saltwater corrosion is critical.
What are the machining capabilities of this alloy?
This material can be effectively machined using plasma arc cutting, with argon and hydrogen gases providing the best cut quality. Recommended machining parameters include utilizing carbide tools and maintaining positive cutting action to prevent work hardening.
Q4. In which sectors is this alloy commonly utilized?
This material finds applications across various fields such as chemical processing, oil and gas, pulp and paper, pharmaceuticals, food processing, and electronics, particularly in uses requiring high durability and hardness, including fasteners, springs, chains, pump and valve components, and other elements in highly corrosive environments. For procurement managers, understanding these applications alongside the specifications of copper nickel alloys—such as their widespread use in automotive systems for brake lines and hydraulic systems, and in electronics and heat exchangers—will facilitate informed material selection suited to diverse operational needs.
Heat Treatment Techniques for Enhancing Monel K500 Properties
Heat treatment plays a critical role in optimizing the mechanical properties of Monel K500, with two primary techniques: solution annealing and aging. The solution annealing process involves heating the alloy to approximately 1900°F (1040°C) followed by a rapid cooling phase. This method effectively dissolves precipitates, thereby enhancing ductility and overall workability.
Conversely, aging is usually performed at temperatures between 1200°F (650°C) and 1400°F (760°C), promoting precipitation hardening that significantly enhances the Monel K500 yield strength. Recent studies indicate that the yield strengths of Monel K500 are 296 and 298 MPa at 0 hours of aging, escalating to 556 and 558 MPa after 2 hours. These findings underscore the importance of processing technology in influencing the Monel K500 yield strength.
Additionally, microhardness and compression testing conducted on cylindrical specimens further validate these mechanical properties, providing a deeper understanding of the alloy’s performance. In practical uses, heavy machining of Alloy K-500 is best conducted in the annealed or hot-worked and quenched condition. Age-hardened material can also be machined to close tolerances, with the recommended practice being to machine slightly oversize, age-harden, and then finish to size, which results in minimal warpage due to low temperatures and slow cooling rates.
Engineers and procurement managers alike must carefully choose the suitable heat treatment processes to achieve a balance between durability and ductility tailored to specific applications. As A. G. Kostryzhev noted, ‘No ethical approval was required for this research as it did not involve human tissue or any other parts of living organisms.’ By comprehending the intricate relationship between heat treatment and mechanical properties, stakeholders can achieve remarkable enhancements in material performance and longevity in demanding service conditions.
Applications of Monel K500: Where and Why It Is Used
The alloy stands out as a material of choice across various industries, attributed to its exceptional blend of properties. In the marine sector, it is extensively utilized in critical components such as propeller shafts and pump shafts, where its unmatched durability and corrosion resistance are essential. Furthermore, in the aerospace sector, this alloy is favored for its excellent high strength-to-weight ratio, making it suitable for uses such as fasteners and valve bodies.
Its performance in elevated temperature environments makes it particularly suitable for chemical processing equipment, encompassing valves and fittings. Significantly, the alloy achieves roughly three times the Monel K500 yield strength and twice the tensile strength of its predecessor, the alloy 400, further reinforcing its position as a dependable option for engineers. The alloy’s ability to maintain its integrity under extreme conditions renders it an invaluable resource for those seeking durable solutions.
Additionally, this alloy exhibits very low magnetic permeability, making it virtually non-magnetic in most conditions; however, processing can lead to a magnetic nickel-rich film. Proactive measures, such as controlled atmosphere heating and minimizing cold work, are crucial for preserving its non-magnetic characteristics. These best practices, as highlighted in the case study titled ‘Maintaining Non-Magnetic Properties of Monel Alloy K-500‘, ensure that Monel K500 remains effective in high-performance applications.
As noted by Kun Zhou, these methodologies are essential for maintaining the material’s integrity and performance.
Conclusion
Monel K500 stands as a benchmark in the world of nickel-copper alloys, showcasing exceptional strength and corrosion resistance that make it indispensable across various demanding industries. Its yield strength of up to 70 ksi (480 MPa) and remarkable resilience in harsh environments underline its suitability for applications in marine, chemical processing, and oil and gas sectors. The strategic advantages of Monel K500 are further amplified by its excellent weldability and formability, allowing for versatile engineering solutions tailored to specific operational needs.
The alloy’s superior resistance to stress corrosion cracking, particularly in marine environments, highlights the importance of thorough evaluation when selecting materials for critical applications. Coupled with effective heat treatment techniques such as solution annealing and aging, Monel K500’s properties can be optimized to meet the rigorous demands of modern engineering challenges. Understanding the interplay between yield strength, corrosion resistance, and machining capabilities enables procurement managers to make informed decisions that enhance performance and longevity in their projects.
As industries continue to evolve, the role of Monel K500 remains pivotal, reinforcing its status as a strategic material choice. By leveraging its unique properties and adhering to best practices in machining and heat treatment, stakeholders can ensure that their applications not only meet but exceed the expectations set by the most challenging environments. The ongoing advancements and applications of Monel K500 will undoubtedly shape the future of engineering solutions, solidifying its place at the forefront of material innovation.