Blogs
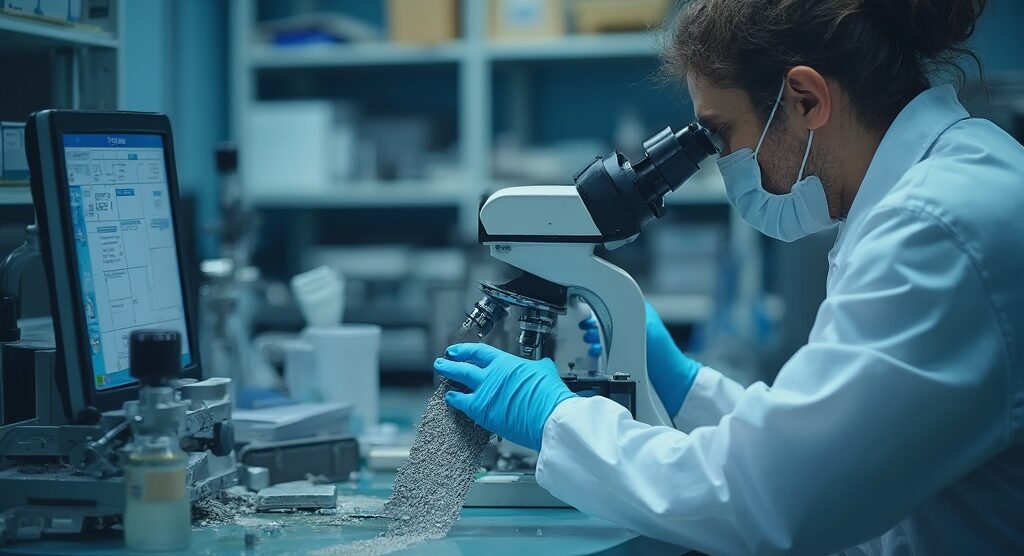
What Is Alloy Corrosion? Understanding the Basics and Implications
Introduction
In the realm of material science, alloy corrosion stands as a formidable adversary, threatening the integrity and performance of critical components across various industries. As environments become increasingly corrosive, procurement managers must navigate the complexities of selecting appropriate materials that not only withstand degradation but also enhance operational efficiency. Understanding the types of corrosion—uniform, pitting, and galvanic—alongside the economic implications of corrosion-related failures, is essential for making informed decisions.
With innovative advancements in alloy technology and predictive modeling, organizations can leverage data-driven insights to bolster their corrosion resistance strategies. This article delves into the multifaceted challenges of alloy corrosion, offering practical solutions and highlighting the significance of strategic material selection to safeguard investments and ensure long-term reliability in automotive and electronics applications.
Defining Alloy Corrosion: What You Need to Know
Alloy corrosion presents a significant challenge in the degradation of metallic materials, especially in aggressive environments, which impacts the reliability and performance critical to sectors like automotive and electronics. Factors such as moisture, chemical exposure, and temperature fluctuations contribute to deterioration, which can manifest as alloy corrosion in forms such as:
- Uniform
- Pitting
- Galvanic
Each form has distinct characteristics that procurement managers must consider during material selection.
The composition and microstructure of an alloy are vital to its resistance to alloy corrosion, making a thorough evaluation essential. Domadia addresses these concerns by providing high-quality electrical wire insulation sleeves made from superior materials, ensuring durability and efficiency in corrosive environments. Our proven execution in fulfilling both small and large batch orders guarantees that you receive your products on time, every time.
Furthermore, our Beryllium Copper solutions are distinguished by their remarkable strength, conductivity, and resistance to alloy corrosion, establishing industry benchmarks for excellence. Recent advancements, such as the integration of silica nanorods into Al-10Zn mixtures, have shown enhanced rust resistance with minimal additions, demonstrating innovative methods in material enhancement. Furthermore, a new machine learning model has enhanced predictive accuracy for identifying essential material compositions for resistance to degradation by up to 15%.
As mentioned by Michael Rohwerder, ‘We trained the deep-learning model with intrinsic data that contains information about deterioration properties and composition.’ This model empowers procurement managers to make informed decisions based on data-driven insights. Furthermore, the rise of IoT in the electric vehicle industry is transforming how material selection is approached, emphasizing the need for substances that ensure longevity and performance.
With Domadia, you’re not merely sourcing products; you’re investing in reliable, high-performance solutions that elevate your projects.
The Implications of Alloy Corrosion in Everyday Applications
Alloy corrosion presents notable challenges across various applications, particularly within the automotive sector, where components such as rims, engines, and electrical connectors frequently encounter harsh environmental conditions. For example, the degradation of aluminum mixtures in automotive rims can lead to structural failures, negatively impacting both safety and performance. Notably, corrosion-resistant alloys like Carpenter Technology NiMark Alloy 300 can attain a yield strength of over 1862 MPa (270 ksi), showcasing their performance capabilities in environments where alloy corrosion is a concern.
Furthermore, the financial implications are significant; deterioration not only escalates maintenance costs but also diminishes the lifespan of critical components, ultimately undermining operational efficiency. A recent study evaluating biodiesel’s impact on the total acid number (TAN) highlighted that higher concentrations of biodiesel blend lead to increased TAN values, indicating fuel oxidation that can worsen deterioration in metals like copper and brass, which are particularly vulnerable compared to aluminum, zinc, and stainless steel. As pointed out by Săpunaru, O.V., the degrading impact of biodiesel-diesel mixtures on various metals can significantly lead to alloy corrosion affecting automotive parts.
In the electronics sector, corrosion can severely impair conductivity, leading to device failures that may result in substantial economic losses. Therefore, it is imperative for procurement managers to prioritize sourcing resources that meet stringent durability and performance standards. This strategic focus on corrosion-resistant alloys, alongside exploring Domadia’s Mica Tapes, which offer excellent high-temperature electrical insulation and resistance to chemical degradation, enhances product reliability.
Furthermore, the variety of electrical insulating products, including Mica Tapes, electrical insulating papers, and high-temperature fabrics, offers extensive solutions for diverse uses, enhancing customer satisfaction and protecting investments in both automotive and electronic industries. Moreover, the use of Non-Sparking Tools is essential in explosive settings, offering a secure option that aids in reducing risks linked to deterioration and electrical insulation failures.
Common Types of Alloy Corrosion and Their Characteristics
There are several common types of metal corrosion, each with unique characteristics:
- Uniform Corrosion: This is the most common type, characterized by a uniform loss of material across the surface of the metal. It often happens in settings where the metal is consistently exposed to corrosive agents.
- Pitting Corrosion: This type manifests as small, localized pits or holes on the surface of the alloy, which can lead to significant structural damage if not addressed. Alloy corrosion is often caused by chlorides and is particularly concerning in stainless steels.
- Galvanic Corrosion: Occurs when two dissimilar metals are in contact in the presence of an electrolyte, leading to accelerated corrosion of the more anodic metal. This is critical in applications where mixed metals are used. In contrast, copper nickel mixtures present significant advantages in corrosive environments, particularly marine settings. Their high resistance to alloy corrosion, especially in saline or brackish waters, makes them a superior choice over stainless steel, which is more susceptible to pitting and galvanic corrosion. Furthermore, these alloys excel in thermal and electrical conductivity, offering outstanding performance in heat exchangers and electrical uses. Their excellent ductility and simplicity of fabrication further increase their attractiveness, along with their significant antimicrobial properties, which are crucial for scenarios where hygiene is critical. Grasping these types of deterioration is crucial for choosing substances that will endure particular environmental circumstances in automotive and electronics uses.
Preventive Measures Against Alloy Corrosion
Efficient avoidance of metal deterioration is essential for guaranteeing the durability and dependability of substances in diverse applications. Several key strategies can be employed:
- Material Selection: It is essential to choose alloys that possess inherent corrosion resistance, such as stainless steel or aluminum alloys, particularly those treated with protective coatings. This selection process is vital, especially in environments with high corrosivity. According to the CPC Checklists Tool, 70% of corrosion-related failures can be attributed to unsuitable selection of substances.
- Protective Coatings: The application of coatings, including paints, galvanization, or anodizing, creates a robust barrier against corrosive agents. These coatings not only enhance the aesthetic appeal but also significantly prolong the lifespan of components by preventing direct exposure to harmful elements. Robert Herron, a student in materials science, emphasizes, “Protective coatings are essential for extending the life of metal mixtures in corrosive environments, as they act as the first line of defense against alloy corrosion and degradation.”
- Cathodic Protection: This method involves the use of a sacrificial anode, which acts as a shield for the primary alloy, effectively reducing deterioration rates. It is widely utilized in pipelines and marine applications where exposure to aggressive environments is common.
- Environmental Control: Maintaining controlled environments—specifically managing humidity and temperature—can greatly reduce the risk of deterioration. This proactive approach is especially beneficial in facilities where alloys are exposed to varying atmospheric conditions.
The case study titled ‘Long-Term Corrosivity At NASA Kennedy Space Center As A Function Of Distance And Time From The Atlantic Ocean’ highlights the importance of understanding deterioration rates and chloride concentrations. Long-term data gathered at NASA indicates that deterioration rates rise considerably within a specific range from the Atlantic Ocean, emphasizing the necessity for educated substance selections in both ground and spaceflight initiatives. This long-term corrosivity data will function as an updated benchmark for NASA’s deterioration management requirements, demonstrating the significance of informed decision-making in material selection.
By implementing these preventive measures, procurement managers can enhance the durability and performance of alloys, ultimately mitigating the costs associated with alloy corrosion failures.
The Economic Impact of Alloy Corrosion
Alloy deterioration poses substantial economic challenges for businesses, especially in sectors where performance and reliability are paramount. The Department of Defense’s staggering $20 billion annual cost linked to deterioration exemplifies the gravity of this issue, particularly as the automotive industry faces similar challenges. Corrosion-related failures can trigger recalls, tarnishing a company’s reputation and threatening its financial health.
The direct costs linked to repairs and replacements are compounded by indirect expenses such as lost production time and diminished product reliability. As maintenance costs for corroded components can escalate significantly over time, they can severely impact operational budgets. Tom White of the National Association of Corrosion Engineers (NACE) highlights the significance of a Management System (CMS), stating,
a CMS is the documented set of processes and procedures required for planning, executing, and continually improving the ability of an organization to handle the threat of deterioration for existing and future assets and asset systems.
By proactively addressing the economic implications of alloy corrosion, procurement managers can effectively advocate for investing in higher-quality resources and preventive measures. This approach not only mitigates costs but also enhances product longevity, ensuring a sustainable operational strategy. Furthermore, recent trends in material technology are anticipated to reduce reliance on traditional steel, simultaneously improving vehicle efficiency and potentially reshaping automotive steel prices in the coming years.
Case studies, such as those from Metal.com, which offers real-time market analysis and price tracking tools, illustrate how informed purchasing decisions can be made based on current market trends, allowing manufacturers to adjust budgets effectively in response to the evolving landscape.
Conclusion
Alloy corrosion presents significant challenges that demand careful consideration from procurement managers across various industries, particularly automotive and electronics. Understanding the different types of corrosion—uniform, pitting, and galvanic—alongside the economic implications of corrosion-related failures is crucial for effective material selection. By prioritizing corrosion-resistant alloys and employing preventive measures such as protective coatings and cathodic protection, organizations can minimize the risks associated with corrosion and ensure the longevity of their components.
The economic impact of alloy corrosion cannot be overstated, with substantial costs associated with maintenance, repairs, and potential product recalls. As highlighted, the Department of Defense’s annual expenditure of $20 billion due to corrosion illustrates the urgency of addressing this issue. By implementing a Corrosion Management System, procurement managers can strategically invest in high-quality materials that not only reduce costs but also enhance operational efficiency and reliability.
In conclusion, the integration of innovative technologies and data-driven insights is essential for navigating the complexities of alloy corrosion. As industries evolve, embracing advanced material solutions and predictive modeling will empower organizations to make informed decisions that safeguard investments and ensure long-term performance. Prioritizing corrosion resistance is not merely a technical choice; it is a strategic imperative that fosters resilience and sustainability in an increasingly corrosive environment.