Blogs
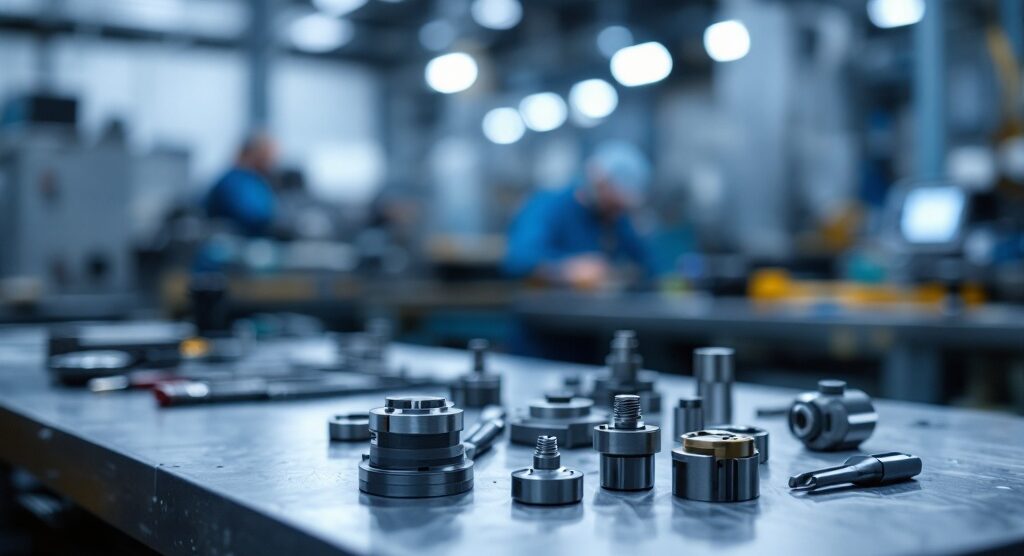
What is Invar Tooling? Understanding Its Properties and Applications in Manufacturing
Introduction
In the realm of modern manufacturing, the quest for precision and stability has led to the rising prominence of Invar tooling. Renowned for its extraordinary low coefficient of thermal expansion, Invar stands out as a pivotal material that addresses the stringent demands of high-precision industries such as aerospace, automotive, and composite manufacturing.
This article delves into the unique properties of Invar, exploring its:
- Exceptional machinability
- Thermal stability
- Magnetic characteristics
These features make it indispensable for intricate tooling applications. As the market evolves, understanding the comparative advantages of Invar over traditional materials and its economic implications becomes crucial for procurement managers aiming to enhance operational efficiency and product quality.
With an eye on future trends and technological advancements, the insights provided here will equip industry professionals with the knowledge needed to navigate the complexities of Invar tooling in an increasingly competitive landscape.
Exploring the Unique Properties of Invar Tooling
This material is characterized by its exceptionally low coefficient of expansion (CTE), which can vary from 0.5 to 0.9 /°F, or up to .010″. This characteristic is nearly one-tenth that of carbon steel, as highlighted by industry experts who state,
This 36% nickel-iron alloy possesses a rate of thermal expansion approximately one-tenth that of carbon steel at temperatures up to 400°F (204°C).
Such a low CTE is especially beneficial for applications requiring high precision, making invar tooling a great choice, as it significantly reduces dimensional changes caused by temperature variations.
Furthermore, this material demonstrates excellent machinability and weldability, enabling the fabrication of intricate design components. Its unique magnetic properties also render it suitable for applications where magnetic interference must be minimized. For instance, minimizing thermally induced tool distortion can be achieved by controlling the heating and cooling rates during the full anneal heat treatment.
- Stabilizing the tool at 500°F before increasing the temperature, along with managing the cooling rate, helps maintain the tool’s contour, particularly for longer tools.
- Additionally, when tapping the alloy, it is recommended to use a tap drill that is slightly larger than the standard drill, and a two or three fluted tapping tool should be utilized on automatic machines, with a speed of about 20 FPM.
Collectively, these attributes position this material as an ideal choice for manufacturing applications that require invar tooling to ensure unwavering accuracy and stability under fluctuating thermal conditions.
When compared to other metals, this alloy’s characteristics, including its low CTE and outstanding machinability, make it an excellent option for precision manufacturing applications that utilize invar tooling.
Applications of Invar Tooling in Modern Manufacturing
Invar tooling is essential to various high-precision industries, particularly aerospace, automotive, and composite production. In the aerospace sector, invar tooling is crucial for developing precise instruments that adhere to strict tolerances—especially vital in the manufacturing of aircraft fuselages and wings, where dimensional accuracy is of utmost importance. Aerospace engineers emphasize the significance of the alloy’s low thermal expansion, which improves the dependability of equipment during production.
The invar tooling production market has faced considerable obstacles, documenting a significant effect of -30.5% due to the pandemic, underscoring the necessity for resilience in production practices. In the automotive industry, specialized equipment is employed for creating high-precision molds and dies, which are essential for producing intricate components with precise dimensional specifications. Furthermore, in composite manufacturing, the remarkable thermal stability of this material is utilized to create equipment capable of enduring the curing processes of composite substances.
This adaptability highlights the company’s reputation as a preferred choice among manufacturers striving for efficiency and accuracy in their production processes. As indicated by Stratview Research, prominent participants in the market consist of firms such as Ascent Aerospace and Baker Industries, emphasizing the competitive environment of specialized manufacturing. Furthermore, the market is primarily segmented into aerospace and other industries, with aerospace being the larger and faster-growing segment, as illustrated in a recent end-use industry analysis.
As the invar tooling manufacturing market continues to evolve, its applications are likely to expand further, particularly with the demand for high-performance components in modern production.
Comparative Advantages of Invar Tooling Over Other Materials
In the landscape of invar tooling materials, this alloy presents distinct advantages over aluminum and steel. NILO® 48, for instance, contains 48% nickel and is appropriate for uses up to 450°C (840°F), highlighting its temperature stability. While aluminum is acknowledged for its lightweight and cost-effectiveness, it is encumbered by a higher coefficient of expansion (CTE), which can introduce inaccuracies in precision applications.
Steel, although strong, is often heavier and exhibits greater instability with temperature fluctuations. In contrast, its low CTE facilitates exceptional dimensional accuracy, making it the material of choice for high-precision manufacturing demands that utilize invar tooling. Moreover, the material’s natural resistance to distortion under heat stress guarantees stable equipment integrity over time, enhancing its excellence in settings where invar tooling is critical.
NILO alloys, like NILO 36 and NILO 42, are also nickel-iron alloys with low expansion coefficients, making them suitable for aerospace and microelectronic applications. Additionally, in high-temperature environments, Mica tape products are invaluable for electrical insulation and thermal resistance, often used alongside specialized tooling to enhance safety and performance in critical applications. The significance of non-sparking tools in explosive settings cannot be ignored, as they offer crucial safety measures when handling materials such as Mica.
Recent studies have highlighted these advantages, positioning this material as an essential component in advanced manufacturing, particularly in aerospace and microelectronics, where invar tooling is critical for maintaining dimensional fidelity. As Michael, the host of Michael Talks Metal, puts it, ‘Thanks for watching, this is Michael with Michael Talks Metal, OUT!
Cost Considerations and Economic Impacts of Invar Tooling
While the initial investment in specialized equipment may exceed that of other materials, its long-term financial benefits often yield substantial returns that warrant the upfront expenses. The exceptional durability and thermal stability of this alloy reduce the necessity for frequent replacements and maintenance, thus lowering operational expenses over time. Improved accuracy obtained through invar tooling results in higher product quality, which effectively reduces waste and rework expenses.
This efficiency not only streamlines production but also bolsters the overall profitability of manufacturing operations. Simon Price, Managing Director, observes,
Compared to the alternative, using this material at the minimum surface thickness (plus surface area) presents a significant cost-reduction opportunity and the chance of obtaining a production-ready tool in 1-2 weeks instead of months.
In contrast, traditional invar tooling typically requires 9-12 months for machining, highlighting the efficiency of alternative materials.
Furthermore, trials with the 360 material have demonstrated its compatibility with standard machinery, eliminating the need for specialized tools. This capability enables organizations to produce equipment in-house, further reducing costs and enhancing efficiency. The outcome of these trials indicates a significant reduction in equipment costs and improved production timelines.
For procurement managers, a thorough cost-benefit assessment is essential when considering the incorporation of specialized equipment into production strategies, as it can result in long-term financial advantages that significantly enhance the bottom line. Furthermore, comprehending the pricing framework for market intelligence reports, which differs by license type, can offer additional context for those contemplating investment in related products.
Future Trends in Invar Tooling and Manufacturing Technologies
The path of specialized equipment is set for change, propelled by major progress in production technologies such as additive manufacturing and automation. The Global Tool market anticipates a robust growth rate of 5.9%, reflecting the increasing reliance on high-precision instruments capable of enduring the demands of automated production environments. As industries integrate Industry 4.0 principles, the need for specialized tooling solutions that enhance efficiency and precision will intensify.
The competitive environment includes specialized producers concentrating on high-quality molds and dies crafted from a specific alloy, which is essential for satisfying the increasing need for accuracy in production. However, the Tooling market faces challenges, including high costs and limited availability of the material, which can restrict its use in price-sensitive industries. Advancements in material science are anticipated to produce improved alloys, providing exceptional performance traits crucial for contemporary industrial requirements.
Furthermore, the hardness and machinability of this alloy present production challenges, requiring specialized processes and equipment. Furthermore, the emphasis on sustainability is encouraging manufacturers to explore more environmentally responsible sourcing and production methods for specialized materials. As noted by HTF Market Intelligence:
Its focus will be on more sustainable production, connectivity, and e-mobility.
For procurement managers, staying informed about these trends is vital for effectively leveraging invar tooling in their manufacturing strategies, especially given these challenges.
Conclusion
Invar tooling represents a significant advancement in manufacturing technology, particularly for industries that demand the highest levels of precision and stability. Its exceptional low coefficient of thermal expansion, coupled with remarkable machinability and unique magnetic properties, positions Invar as a superior choice for tooling applications across aerospace, automotive, and composite manufacturing sectors. As detailed in the article, the advantages of Invar over traditional materials like aluminum and steel are clear; it offers exceptional dimensional accuracy and resistance to thermal distortion, making it indispensable for complex and high-precision tooling.
Moreover, the economic implications of using Invar tooling cannot be overlooked. While the initial costs may be higher compared to alternatives, the long-term benefits in terms of durability, reduced maintenance, and improved product quality often justify the investment. Procurement managers are encouraged to conduct thorough cost-benefit analyses to fully appreciate the potential for operational efficiencies and profitability that Invar tooling can bring to their manufacturing processes.
Looking ahead, the Invar tooling market is set for growth, driven by advancements in manufacturing technologies and a heightened focus on sustainability. As industries adopt more automated and precise production methods, the demand for high-performance tooling solutions is expected to rise. Staying abreast of these trends will be crucial for procurement managers aiming to leverage Invar tooling effectively in an evolving market landscape. The insights provided here serve as a valuable resource for those seeking to enhance operational efficiency and maintain a competitive edge.