Blogs
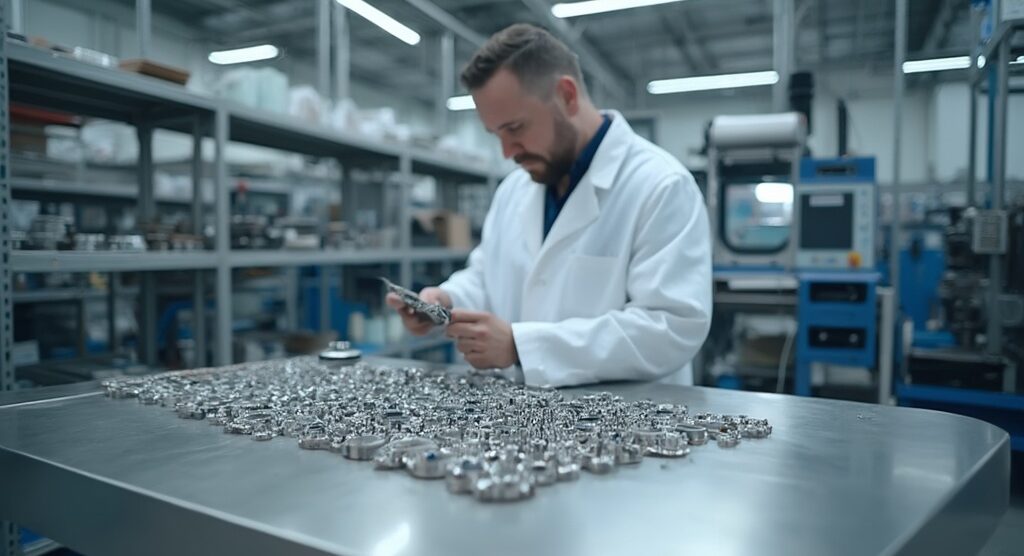
How to Choose the Right Turbine Alloys: A Step-by-Step Guide
Introduction
In the intricate world of turbine manufacturing, the selection of alloys is not merely a technical decision but a strategic imperative that can significantly influence performance and reliability. As procurement managers navigate the complexities of material choices, understanding the critical factors that govern alloy selection becomes paramount. From mechanical properties and corrosion resistance to cost considerations and compliance with industry standards, each element plays a vital role in ensuring that turbine components can withstand the rigors of operation.
This article delves into the essential considerations for selecting turbine alloys, explores various alloy types suited for demanding applications, and outlines effective strategies for evaluating supplier capabilities. By equipping procurement professionals with expert insights and practical solutions, it aims to facilitate informed decision-making that supports the long-term success of turbine operations.
Key Considerations for Selecting Turbine Alloys
When selecting turbine alloys, it is imperative to consider several key factors that will influence performance and reliability:
Mechanical Properties: The material’s mechanical properties, including tensile strength, fatigue resistance, and creep performance at operational temperatures, are paramount. Recent findings indicate that the All Weld Metal in the aged condition achieves a yield strength of 105.4 ksi (727 MPa) and an ultimate tensile strength of 151.6 ksi (1045 MPa). These attributes are essential for guaranteeing the composite can withstand the severe conditions usually faced in engine operations. Additionally, a case study on All Weld Metal tensile data for a 0.5″ (12.7 mm) cruciform joint welded using GMAW shows a maximum yield strength of 105.4 ksi (727 MPa) and ultimate tensile strength of 151.6 ksi (1045 MPa) in the aged condition, highlighting the robustness of the weld metal.
Corrosion Resistance: Considering the severe conditions in which these machines function, assessing a metal’s resistance to oxidation and corrosion is crucial. Copper nickel mixtures are recognized for their excellent resistance to corrosion in marine settings, making them a strategic option for high-performance rotor uses. Additionally, nickel-based superalloys, including DOMADIA Nickel Molybdenum Iron Alloy, are preferred due to their exceptional corrosion resistance, thermal stability, and unmatched strength, ensuring reliability in critical applications. Ongoing research highlights advancements in corrosion resistance ratings, with projections for 2024 indicating further improvements in this area. Machine learning is being employed to examine failed experiments, paving the way for new material discoveries that could improve corrosion resistance in engine components.
Weight and Density: The mass of the mixture plays a crucial role in efficiency of the rotor. Lighter materials can significantly enhance performance by reducing overall weight, which is critical for dynamics and fuel efficiency. Therefore, the density of the mixture should be carefully examined to enhance the design of rotor parts.
Cost and Availability: A thorough analysis of the cost implications associated with sourcing the chosen material must be conducted. Availability in the market is equally crucial to ensure alignment with budget limitations while maintaining the required quality standards for energy solutions.
Compliance with Standards: Finally, ensure that the chosen materials meet relevant international standards and industry regulations. Adherence is essential not only for safety and performance but also for preserving the integrity of operations in various industrial sectors. By adhering to these guidelines, procurement managers can make informed decisions that support the long-term success of their projects.
Ease of Fabrication: Copper nickel mixtures are also acknowledged for their ease of fabrication, permitting efficient manufacturing processes and versatility in various uses. This characteristic is essential for ensuring that component parts can be produced with precision and speed.
Antimicrobial Characteristics: Moreover, the antimicrobial characteristics of copper nickel mixtures render them especially appropriate for scenarios where cleanliness is essential, providing an additional benefit for their utilization in turbine-related uses.
Exploring Different Alloy Types for Turbine Applications
In turbine applications, various alloy types are utilized to meet the demanding requirements of high performance and reliability:
Nickel-Based Superalloys: Renowned for their exceptional high-temperature strength and oxidation resistance, nickel-based superalloys such as Inconel and Hastelloy are integral to turbine blades and components that operate under extreme conditions. These metal mixtures can withstand temperatures up to 850 °C, maintaining strength even at over 70% of their melting temperature (1280 °C). Notably, anti-phase boundary (APB) shearing in these materials is initiated with a critical resolved shear stress of approximately 195.82 MPa, highlighting their mechanical robustness.
Titanium Compositions: Defined by their lightweight quality combined with remarkable strength, titanium compositions, especially Ti-6Al-4V, are perfect for compressor sections where weight reduction is crucial. The utilization of these materials enhances fuel efficiency without compromising performance.
Cobalt-Based Materials: Recognized for their exceptional wear resistance and stability at high temperatures, cobalt materials are favored for components that undergo significant stress and wear, ensuring durability and operational reliability.
Aluminum Compositions: Although not usually appropriate for high-temperature areas, aluminum compositions discover their role in low-temperature uses or non-structural parts of engines, where minimizing weight is beneficial without requiring high strength.
Steel Compositions: High-strength steel compositions are extensively used in rotor systems that require remarkable strength and durability. These materials are frequently employed in structural elements and enclosures, offering a strong foundation for operational systems.
In the context of recent innovations, research has shown that the addition of ruthenium (Ru) to nickel-based single crystal superalloys enhances their microstructural stability and performance under operational conditions. This is particularly evident in the case study titled “New Insights into the Microstructural Stability Based on the Element Segregation Behavior at γ/γ′ Interface in Ni-Based Single Crystal Superalloys with Ru Addition.”
Moreover, mica tape products can play a crucial role in electrical insulation within turbine uses, especially in high-temperature environments. Their high-temperature resistance and electrical insulation properties enhance the use of high-performance materials, ensuring safe and efficient operation.
When choosing a metal mixture, it is essential to take into account particular usage needs, including temperature ranges, mechanical loads, and environmental conditions. As metallurgists highlight, these factors guarantee peak performance and dependability across uses involving turbines.
Evaluating Supplier Capabilities
To effectively assess the capabilities of suppliers in the context of high-performance alloys for wind turbine applications, consider the following strategic steps:
Evaluate Quality Certifications: Start by confirming that vendors possess appropriate quality certifications, such as ISO 9001 or other industry-specific certifications designed for component parts. Statistics indicate that roughly 70% of manufacturers hold ISO 9001 certification, ensuring compliance with established quality management standards and demonstrating a commitment to ongoing enhancement in production processes.
Review Production Capacity: It is crucial to analyze the provider’s production capabilities thoroughly. Evaluate whether they can consistently meet your volume requirements and delivery timelines, while also possessing the flexibility to scale production as demand fluctuates. Statistics show a rising average production capability among manufacturers of metal components, which emphasizes the significance of this assessment.
Evaluate Technical Expertise: Assess the provider’s knowledge regarding turbine alloys and their specific applications. Suppliers with a strong technical background can provide not only products but also invaluable insights and recommendations tailored to your unique needs, enhancing your project outcomes.
Check References and Track Record: Request references from past clients and critically review the provider’s track record in terms of reliability and product quality. Understanding their reputation within the industry can significantly influence your decision-making process. For instance, the case study titled ‘Evidence for Quality Management Systems in the Wind Power Sector‘ found that providers with robust quality management systems tend to perform better in terms of reliability and customer satisfaction.
Negotiate Terms: Establish clear terms regarding pricing, lead times, and quality assurance processes. Engaging in thorough negotiation can lead to more favorable pricing structures and conditions, aligning with your procurement strategy. Charles J. Corbett emphasizes the importance of understanding vendor dynamics by stating,
In short, this means that firms that export goods or services to a particular country may simultaneously be importing that country’s management practices.
This insight highlights the need for a well-rounded approach to vendor evaluation, which includes not only certifications but also management practices and relationship dynamics.
Additionally, recent findings suggest that ISO certification alone is insufficient to establish positive relationships in the supply chain. This emphasizes the necessity of assessing wider sector-specific certification tools that can improve collaboration among vendors.
In summary, a thorough assessment of supplier abilities is essential for guaranteeing high performance in your acquisition of metal components, ultimately resulting in enhanced results in industrial applications.
Understanding Alloy Testing and Certification
Alloy testing and certification play a critical role in ensuring the performance and reliability of materials used in turbine manufacturing. The process typically encompasses the following key stages:
Material Testing: This initial stage involves comprehensive mechanical and metallurgical evaluations to determine the material’s properties, such as tensile strength, hardness, and fatigue resistance. Common testing methods include tensile tests, impact tests, and microstructural analysis, which help determine the suitability of the materials for high-performance applications. Recent advancements in testing methods, such as non-destructive testing techniques, are increasingly employed to enhance accuracy and efficiency in assessing material performance.
Compliance Testing: It is essential to confirm that the materials meet the necessary industry standards, such as ASTM or ASME specifications. This may involve third-party testing and certification, providing an independent verification of compliance that is crucial for procurement managers. Compliance rates for rotor materials with ASTM standards are typically high, reflecting the industry’s commitment to quality and safety in manufacturing.
Documentation: Accurate and thorough documentation of all test results and certifications is vital. This documentation not only supports audits but also enhances the quality assurance processes that are fundamental in high-stakes industrial environments.
Continuous Monitoring: To ensure ongoing compliance with industry standards, implementing a continuous monitoring process is advisable. Regular audits and re-testing are often necessary to maintain certification, helping to mitigate risks associated with material failure.
Supplier Certification: Ensuring that suppliers also adhere to rigorous certification processes for their manufacturing practices and quality control systems fortifies the assurance regarding the quality of sourced materials. This step is crucial in establishing a reliable supply chain for high-performance materials.
Recent studies highlight that approximately 20% of potential recovery material is lost during the re-melting process, underscoring the importance of meticulous testing and certification methods. As highlighted by Amrita Basak in her commentary on the creation of metallic single crystal blades, rigorous testing is essential to the manufacturing process, emphasizing that effective compliance testing not only meets standards but also enhances overall material performance. Mechanical property evaluations of repaired areas often demonstrate that they have higher hardness values than the substrate, indicating that advancements in material testing methods are continually evolving to meet the demands of modern applications.
Implementing a Strategic Procurement Plan
To execute a successful strategic procurement plan for specialized materials, consider the following essential steps:
Define Objectives: Establish clear procurement objectives, focusing on critical areas such as cost savings, quality enhancement, and vendor diversification. A well-defined set of goals provides a roadmap for decision-making and performance evaluation. Notably, 56% of supply chain leaders identify sourcing for low-volume builds as a significant barrier to innovation, underscoring the necessity of precise objectives in procurement planning.
Conduct Market Research: Engage in comprehensive market research to analyze prevailing trends and identify potential providers of turbine materials. Comprehending the dynamics of the alloy market, including emerging technologies and changes in provider capabilities, is crucial for negotiating favorable terms and ensuring competitive advantage. Consider vendors with proven execution capabilities for both small and large batch orders, particularly those offering high-performance materials like electrical insulation papers, high-temperature fabrics, and other related products.
Develop Vendor Relationships: Cultivate strong partnerships with key vendors. Building trust and collaboration can lead to enhanced pricing models, improved service levels, and robust quality assurance practices. As Fareen Mehrzai, Senior Director Analyst in Gartner’s Supply Chain Practice, notes, addressing skill gaps is crucial for organizations, which highlights the importance of developing vendor relationships to foster collaboration and resilience in the supply chain. Concentrate on vendors that specialize in high-temperature materials, such as those providing electrical insulation papers and high-temperature sleeving, and understand the unique requirements of your procurement needs.
Establish Evaluation Criteria: Create clear and rigorous criteria for assessing vendors and their products. Important considerations include product quality, cost-effectiveness, delivery timelines, and compliance with industry standards. A structured evaluation process is crucial for maintaining high procurement standards. This aligns with findings from a recent case study revealing that only 14% of procurement leaders feel they have adequate talent to meet future needs, emphasizing the need for continuous improvement in evaluation practices.
Monitor and Adjust: Consistently review the performance of the procurement plan against established objectives. Be prepared to make adjustments based on market fluctuations and supplier performance. Continuous improvement is essential to adapting to the evolving landscape and achieving long-term success in procurement.
Conclusion
Selecting the appropriate alloys for turbine manufacturing is a multifaceted endeavor that requires careful consideration of various critical factors. The mechanical properties of the alloys are paramount, ensuring they can withstand the demanding conditions of turbine operations. Equally important is corrosion resistance, particularly in environments that present significant challenges.
Weight and density also play a crucial role in optimizing turbine efficiency, while cost and availability must align with budgetary constraints without sacrificing quality. Compliance with industry standards further ensures the reliability and safety of turbine components.
The exploration of different alloy types reveals a range of options suited for specific applications, from nickel-based superalloys to titanium, cobalt, aluminum, and steel alloys. Each type offers distinct advantages that cater to the high-performance demands of turbine applications. Furthermore, evaluating supplier capabilities is essential, as quality certifications, production capacity, technical expertise, and a solid track record all contribute to the reliability of the supply chain.
Alloy testing and certification processes are indispensable in verifying that materials meet the required performance and compliance standards. By implementing a strategic procurement plan that encompasses clear objectives, thorough market research, strong supplier relationships, and rigorous evaluation criteria, procurement managers can enhance their decision-making processes.
Ultimately, the effective selection of turbine alloys and the evaluation of supplier capabilities form the backbone of successful turbine operations. By prioritizing these considerations, procurement professionals can ensure that their projects are not only successful but also contribute to the long-term reliability and efficiency of turbine systems.