Blogs
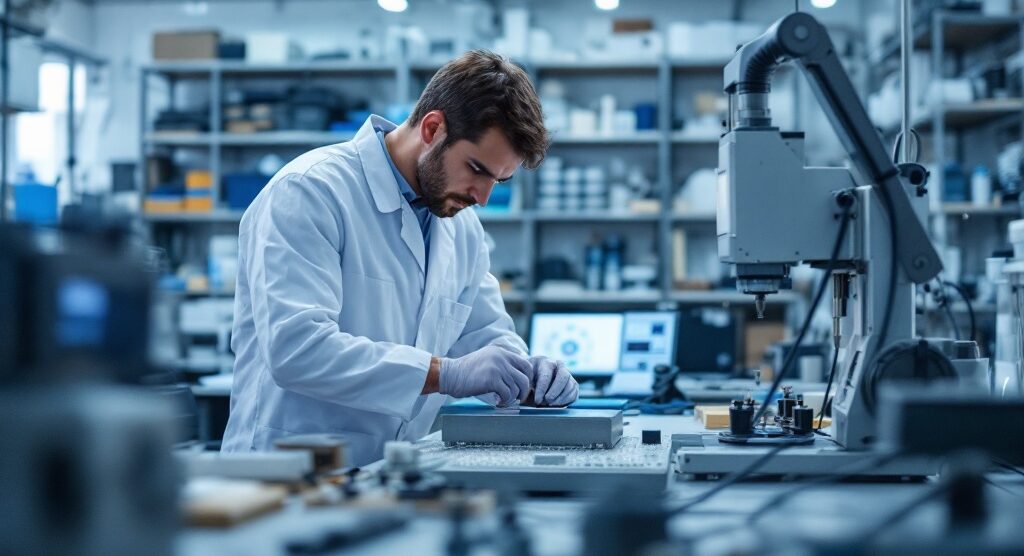
Understanding Coefficient of Friction for Different Materials: An In-Depth Tutorial
Introduction
Understanding the coefficient of friction (COF) is essential for procurement managers and engineers navigating the complexities of material selection and performance optimization. This critical numerical value not only quantifies the frictional forces between surfaces but also informs decisions that impact product design across various industries, from automotive to electronics.
With two primary classifications—static and kinetic—COF plays a pivotal role in enhancing efficiency and safety, particularly in environments where friction can lead to catastrophic failures. As the demand for advanced materials grows, recognizing the factors that influence COF, such as surface texture, material properties, and environmental conditions, becomes increasingly vital.
This article delves into the intricacies of COF, exploring its implications in engineering practices, the significance of low-friction materials, and the methodologies for accurate measurement, equipping professionals with the insights necessary to make informed decisions in their procurement strategies.
Defining the Coefficient of Friction: An Overview
The coefficient of friction for different materials is a critical numerical value that quantifies the frictional force occurring between two materials in contact. This dimensionless quantity is affected by the particular substances involved and their respective external conditions. COF is generally classified into two main types: static, which applies when the surfaces are at rest, and kinetic, which pertains to surfaces in motion.
For procurement managers and engineers, a comprehensive understanding of COF is essential, as it directly influences selection, product design, and overall performance across a wide array of applications, including automotive and electronics. In explosive environments, the choice of low friction substances can be crucial for safety, particularly when using Non-Sparking Tools that minimize the risk of ignition. Recent studies emphasize the significance of selecting substances that have an optimal coefficient of friction for different materials to enhance efficiency and reliability.
For instance, descriptive statistics reveal that the average COF values for various substances include:
1. A mean of X
2. A median of Y
3. A standard deviation of Z
4. Minimum and maximum values ranging from A to B
Additionally, the case study titled ‘Visualization of COF Data’ employed Python scripts to illustrate how COF values change over time, providing insights into the wear characteristics of substances. Dimitrova, R. emphasizes in her study on advanced composites that ‘the production and tribological characterization of substances are essential for understanding their performance in engineering applications.’ This emphasizes the essential function of COF in engineering practices, particularly when evaluating the use of Non-Sparking Tools in settings where resistance is a concern.
Key Factors Affecting the Coefficient of Friction
The coefficient of resistance is influenced by several essential factors that procurement managers must consider when choosing materials for optimal performance:
- Texture: The texture of a material plays a pivotal role in resistance behavior. Rougher textures generally exhibit a higher coefficient of friction for different materials due to an increased number of contact points, while smoother textures tend to lower this coefficient. Significantly, recent findings emphasize that a roughness (Ra) of 0.8 to 1.6 μm leads to a dark glossy finish, suggesting advanced processing appropriate for components exposed to greater variable stress. The geometry and sequence of the surface texturing process are also crucial, as they can significantly affect the tribological properties, influencing how surfaces interact under load.
- Substance Properties: The intrinsic characteristics of substances, such as hardness and elasticity, are crucial determinants of the coefficient of friction for different materials. For example, tougher substances generally show lower wear rates, resulting in a more stable coefficient of friction for different materials under various operational conditions. Materials like Mica Tape are particularly valuable due to their exceptional high-temperature resistance and electrical insulation, making them indispensable in electrical engineering applications, such as in the manufacture of fire-resistant cables and other critical electrical insulation systems.
- Environmental Conditions: External factors like temperature, humidity, and the presence of lubricants significantly impact frictional behavior. Research has demonstrated that the total volumetric wear of tribological systems can rise more than threefold with increasing temperatures, which highlights the necessity for careful selection of the coefficient of friction for different materials based on expected operating environments. In explosive environments, the use of Non-Sparking Tools is essential to prevent ignition sources, further emphasizing the significance of choosing substances that ensure safety.
- Texture Roughness Measurement: A case study utilizing scanning electron microscopy (SEM) illustrates the precision of texture roughness measurements. SEM offers highly precise images of height lines, enabling a comprehensive characterization of roughness, which is essential for informed selection of substances. By thoroughly understanding these factors, procurement managers can make informed decisions that improve performance in their specific applications. As Alaitz Zabala, Coordinator of the Surface Technologies research group, emphasizes, > surface metrology and tribology are essential in optimizing materials for diverse industrial applications, highlighting the interconnectedness of these elements in achieving optimal performance.
Materials with Low Coefficient of Friction: Examples and Applications
Substances with minimal resistance to sliding contribute significantly to improving efficiency and minimizing wear in various sectors. Notable examples include:
PTFE (Polytetrafluoroethylene): Renowned for its exceptional non-stick properties and minimal friction, PTFE is extensively utilized in bearings, seals, and various industrial applications. Its low level of resistance greatly enhances the durability and efficiency of machinery.
UHMW (Ultra-High-Molecular-Weight Polyethylene): This material features an incredibly low COF, making it ideal for high-wear applications such as conveyor systems. Its durability and resistance to abrasion enable reliable performance in demanding environments.
Graphite: Commonly employed as a lubricant, graphite demonstrates a low coefficient of resistance, effectively mitigating wear in mechanical systems. Its unique characteristics render it a valuable resource in engineering applications where resistance reduction is critical.
The incorporation of these substances is crucial in areas such as automotive, aerospace, and production, where optimizing resistance levels can result in improved operational efficiency and prolonged equipment lifespan. Methods for assessing the coefficient of friction for different materials, including the dead load and inclined plane tests, are essential for evaluating the performance of these substances. Additionally, recent statistics indicate that the speed at entry 0.5 mm and exit 2300 mm is 6050 mm/s, providing insight into the operational parameters of these substances.
As Weimin Liu, a recognized expert in the field, states, “The strategic choice and use of low resistance substances are essential for advancing engineering practices and enhancing machinery efficiency.” Recent advancements in low resistance technologies, such as the application of machine learning in forecasting frictional values, further support their strategic use in selecting substances.
Measuring the Coefficient of Friction: Techniques and Standards
Several established techniques for measuring the coefficient of friction are instrumental in material selection, each adhering to international standards for accuracy and reliability:
Pin-on-Disk Test: This standardized method involves pressing a pin against a rotating disk, allowing for precise measurement of the frictional force under controlled conditions. It is widely utilized for its repeatability and ability to simulate various operational environments, making it a staple in testing.
Inclined Plane Test: In this method, a sample is positioned on a slanted area, and the angle at which it starts to slide is recorded. This angle directly relates to the static resistance constant, providing a straightforward and effective means of evaluating resistance properties.
Dynamic Friction Testing: This technique evaluates the frictional force during the relative motion between two surfaces, offering insights into how materials will perform under operational conditions.
The coefficient of resistance is calculated in accordance with ASTM D1894 by dividing the force needed to move a sled by its weight, separately for static and kinetic resistance, providing a concrete example of measurement.
Additionally, the case study titled “ASTM C724 Acid Resistance of Ceramic Decoration on Architectural Glass” illustrates the practical application of these measurement techniques, emphasizing the importance of adhering to technical standards for quality and maintenance.
These techniques not only promote the precise evaluation of resistance characteristics but also ensure that the coefficient of friction for different materials is comparable across various substances and uses. The compliance with global testing standards, along with standardized approaches for assessing the resistance to sliding, strengthens the dependability of the gathered data, which is essential for procurement managers in making informed choices regarding resources.
Practical Implications of Coefficient of Friction in Engineering
The coefficient of friction for different materials is paramount in engineering disciplines, influencing a range of applications that demand precision and reliability. Key areas include:
- Brake Systems: Choosing substances with the right COF is crucial for achieving optimal braking performance. This balance not only ensures effective stopping power but also minimizes wear and extends the lifespan of braking components. Recent studies, particularly those involving braking cycles BC1 and BC2 with 10 braking events each, have shown that thermal imaging of brake discs with perforations enhances pressure distribution and heat transfer, thereby reducing hot spot formation and improving braking stability.
- Bearing Design: The utilization of low-friction substances is vital in reducing energy losses in rotating machinery. By reducing resistance, these substances improve operational efficiency, which is vital for both performance and sustainability in engineering designs.
- Substance Compatibility: A comprehensive understanding of the coefficient of friction for different materials aids in the selection of compatible substances in assemblies, thereby lessening risks linked to excessive wear or early failure. Insights gained from multiple regression analyses of resistance metrics in railway disc brakes have demonstrated strong correlations between braking parameters and resistance values, providing a robust framework for predicting performance. Notably, the case study revealed a significant relationship between these parameters, underscoring the importance of precise material selection, particularly regarding the coefficient of friction for different materials, which is integral to optimizing designs and enhancing product performance across various engineering sectors. As Jakub Kowalczyk aptly noted in his research,
Modeling the Average and Instantaneous Friction Coefficient of a Disc Brake on the Basis of Bench Tests, precise modeling is essential for achieving reliable outcomes in brake system design.
Conclusion
Understanding the coefficient of friction (COF) is integral for procurement managers and engineers aiming to optimize material selection and enhance product performance. This article has explored the fundamental aspects of COF, including its definition, the factors influencing it, and the practical implications in various engineering applications. Recognizing the distinction between static and kinetic COF is crucial, as is the awareness of how surface texture, material properties, and environmental conditions affect frictional behavior.
The importance of selecting low-friction materials cannot be overstated, particularly in high-stakes environments where safety and efficiency are paramount. Materials like PTFE, UHMW, and graphite exemplify how strategic choices can lead to significant operational advantages across industries such as automotive and aerospace. Moreover, the methodologies for measuring COF, including standardized tests like the pin-on-disk and inclined plane methods, provide the necessary framework for accurate assessment, ensuring that procurement decisions are based on reliable data.
In conclusion, a thorough understanding of the coefficient of friction equips professionals with the insights needed to make informed material selections that enhance safety, efficiency, and performance. As industries continue to evolve, the strategic application of COF knowledge will remain a cornerstone in driving innovation and achieving operational excellence.