Blogs
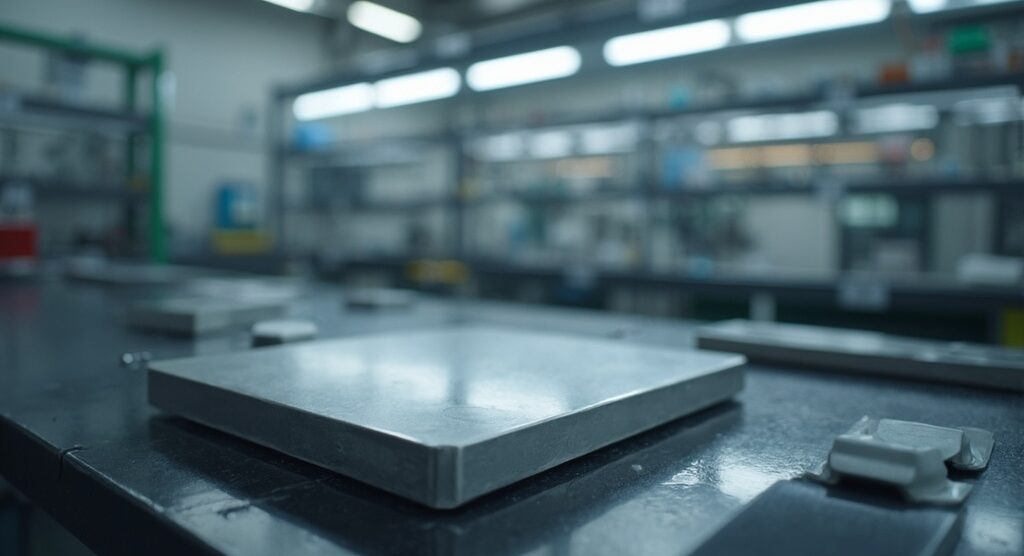
Understanding Monel 400 Composition: A Complete Tutorial for Engineers
Introduction
In the world of engineering materials, Monel 400 stands out as a premier choice, celebrated for its remarkable properties and versatility across various industries. Comprising a unique blend of nickel and copper, this alloy is engineered to withstand the most demanding environments, particularly in marine and chemical processing applications. As procurement managers navigate the complexities of material selection, understanding Monel 400’s composition, mechanical characteristics, and wide-ranging applications becomes essential.
This article delves into the critical aspects of Monel 400, exploring its key properties, comparative advantages over other alloys, and vital procurement considerations that ensure optimal performance and reliability in engineering projects.
An Overview of Monel 400 Composition
The material 400 is a nickel-copper mixture defined by its chemical makeup, which generally contains about 67% nickel and 30% copper, along with trace elements like iron, manganese, carbon, and silicon. This unique blend grants this alloy 400 exceptional corrosion resistance, particularly in harsh marine environments, making it indispensable in industries requiring durability and reliability.
The mixture also exhibits impressive mechanical properties, with tensile strengths for regular temper wire under ½ inch ranging from 110,000 psi (758 MPa) to 140,000 psi (965 MPa). Acknowledged as a robust solution strengthened alloy under ASTM B164, and with ASTM B167 detailing standards for seamless pipes and tubes crafted from this material, 400 is designed for diverse uses.
For procurement managers, understanding alloy 400’s chemical makeup and mechanical properties is vital when selecting materials for extreme conditions. Its versatility allows for use in sectors such as marine engineering, chemical processing, and aerospace, where resistance to corrosive environments is critical.
For instance, alloy 400 is frequently utilized in marine applications, including:
– Propeller shafts
– Pump components
– Valves
where its corrosion resistance is paramount. Additionally, it is employed in chemical processing equipment and aerospace components, demonstrating its broad applicability.
Moreover, Domadia’s commitment to quality ensures that each product undergoes rigorous testing and inspection processes, guaranteeing that this alloy meets the highest industry standards. Recent advancements in nickel-copper alloys further highlight the importance of 400’s significance, underscoring its continued relevance in modern engineering solutions.
Corrosion resistance statistics demonstrate that alloy 400 can withstand various corrosive media, solidifying its status as a preferred choice in demanding environments.
Key Properties and Characteristics of Monel 400
Alloy 400 distinguishes itself through several critical properties that make it an ideal choice for a wide range of engineering uses:
Corrosion Resistance: Monel 400 demonstrates exceptional resistance to corrosion across various environments, particularly in marine settings and reducing conditions. In fact, the corrosion rate in strongly agitated seawater typically does not exceed 0.026 mm/a. However, it is important to note that while it excels in highly dynamic environments, it is susceptible to pitting corrosion in still seawater, which is a critical consideration for applications in marine environments.
High Strength and Toughness: This material maintains its strength over an extensive temperature range, showcasing remarkable toughness in both cold and heated settings. Compared to other alloys, this material exhibits superior toughness and strength, making it particularly suitable for structural components that undergo varying operational conditions.
Ductility: The ease of fabrication associated with this alloy is a significant advantage, as it displays good ductility and workability. This facilitates diverse manufacturing processes, making it a favorite among engineers.
Weldability: Alloy 400 can be joined using traditional methods, increasing its adaptability for uses that necessitate strong and dependable connections. This feature also simplifies repair processes in critical environments, reducing downtime and maintenance costs.
Thermal Conductivity: With moderate thermal conductivity, Alloy 400 is well-suited for heat exchanger uses, where efficient heat transfer is essential for operational effectiveness.
Recent advancements in corrosion-resistant materials have further enhanced the uses of Alloy 400, making it a competitive choice in various industries. Comprehending these properties provides engineers and procurement managers with the knowledge necessary to make strategic choices concerning the use of alloy 400 in various applications, ranging from chemical tanks to marine hardware. The mixture’s chemical composition—consisting of a minimum of 63% nickel and a maximum of 34% copper—further underscores its desirable mechanical and corrosion-resistant properties, as highlighted in the case study on Monel® Alloy 400.
Applications of Monel 400 in Engineering
Alloy 400 is a highly sought-after material due to its exceptional properties, making it invaluable across various industries. Its key applications include:
Marine Engineering: Alloy 400 is extensively used in shipbuilding and marine hardware, prized for its remarkable resistance to seawater corrosion. This property is crucial for ensuring the longevity and durability of marine structures in harsh environments. A notable case study in this area is the use of alloy 400 in the construction of the Nimitz-class aircraft carriers, where its corrosion resistance has proven essential in prolonging the lifespan of critical components.
Chemical Processing: The metal is integral in the construction of chemical tanks and pipework, where its ability to withstand caustic environments is paramount. Recent statistics indicate that this material remains the leading choice in chemical processing uses, with utilization reported at around 40% of all nickel-based materials in this field. This reflects its critical role in ensuring safety and efficiency in chemical manufacturing processes.
Aerospace Components: In aerospace, alloy 400 is utilized in components that demand high durability and strength under extreme conditions. This includes essential fasteners and valves that must perform reliably during rigorous operations.
Oil and Gas Sector: The alloy is well-suited for downhole uses, capable of withstanding high pressures and exposure to corrosive media. Its reliability in such challenging conditions is vital for maintaining operational integrity in oil and gas extraction.
Pharmaceutical Manufacturing: In this sector, alloy 400 is employed in equipment that adheres to stringent cleanliness and corrosion resistance standards, ensuring the safety and efficacy of pharmaceutical products.
These diverse applications not only illustrate alloy 400’s versatility but also underscore its reliability, making it a preferred choice for engineers operating in demanding environments. As noted by Manoj Phagare, Senior Research Analyst at Cognitive Market Research,
In 2023, the alloy 400 segment accounted for a noticeable share of the global alloy market and is projected to experience significant growth in the near future.
Recent market sentiment in Europe has displayed mixed reactions due to fluctuating raw material costs; however, the overall outlook for alloy 400 remains positive, particularly in the marine engineering and chemical processing sectors.
Comparative Analysis with Other Alloys
In the realm of material selection, a comparative analysis of alloy 400 against other alloys reveals significant distinctions:
Alloy 400 vs. Inconel: While Inconel is renowned for its exceptional resistance to high temperatures, alloy 400 excels in marine applications due to its outstanding corrosion resistance in seawater environments. This unique property makes alloy 400 a superior choice for industries that depend on marine or saltwater exposure, offering longevity and reliability in harsh conditions.
Stainless Steel: Alloy 400 is often preferred over stainless steel in highly corrosive settings. Stainless steel can struggle against certain acids and aggressive salts, while the unique composition of alloy 400 ensures enhanced durability and resistance. Moreover, alloy 400 is less prone to pitting and crevice corrosion, making it a more robust option in challenging environments. However, it is important to acknowledge that stainless steel usually demonstrates better mechanical properties at elevated temperatures, which may still make it a viable choice in specific scenarios.Alloy 400 vs. Titanium: Although titanium is lighter and offers excellent corrosion resistance, Alloy 400 is frequently more cost-effective and easier to fabricate for a variety of applications. This combination of economic viability and ease of handling makes alloy 400 an appealing alternative in many projects, particularly when budget constraints are a consideration.
This comparative framework equips engineers and procurement managers with the insights necessary to evaluate the strengths and limitations of alloy 400 relative to other materials, facilitating informed decisions tailored to specific engineering requirements.
Procurement Considerations for Monel 400
When procuring Monel 400, several critical factors warrant careful consideration:
Supplier Certification: It is imperative to ensure that suppliers adhere to international standards, such as ISO 9001, which governs quality management systems. According to recent statistics, 85% of suppliers certified in ISO 9001 report enhanced product quality and consistency, making this certification crucial for ensuring product reliability in all contexts.
Material Traceability: Collaborate with suppliers who can furnish mill certifications and comprehensive traceability documentation. This verification is crucial for confirming the material’s origin and its compliance with stringent industry standards. For instance, Dynamic Forge & Fittings has demonstrated effective practices in material traceability, ensuring that their alloy 400 products meet the necessary compliance requirements.
Cost vs. Quality: A judicious balance must be struck between cost considerations and the necessity for high-quality materials. Choosing less expensive options might result in reduced performance, especially in essential applications where the distinct characteristics of alloy 400 are necessary.
Long-term Relationships: Developing strong, trustworthy relationships with reliable suppliers can enhance negotiation terms, ensure timely deliveries, and facilitate responsive customer service. As Ms. Florence Tang, General Manager, states, “Establishing long-term partnerships with certified suppliers is crucial for maintaining supply chain integrity and performance.”
Market Trends: Staying informed about market trends and price fluctuations for alloy 400 is essential. Staying informed enables strategic purchasing decisions that align with project requirements and budget constraints.
By considering these procurement aspects, professionals can effectively source Monel 400, ensuring that engineering and project management teams have access to the materials necessary for successful project execution.
Conclusion
Monel 400 emerges as a vital alloy in the engineering materials landscape, distinguished by its unique composition of nickel and copper. Its unparalleled corrosion resistance makes it particularly valuable in marine and chemical processing applications, where durability and reliability are non-negotiable. The alloy’s impressive mechanical properties, including high strength, toughness, and excellent ductility, further bolster its standing as a preferred choice among engineers and procurement managers.
The versatility of Monel 400 is evident across various industries, from marine engineering and chemical processing to aerospace and pharmaceutical manufacturing. Each application highlights the alloy’s ability to withstand extreme conditions, ensuring long-lasting performance. Comparative analyses with other materials such as Inconel, stainless steel, and titanium reveal Monel 400’s unique advantages, particularly in corrosive environments where it outperforms competitors.
As procurement managers navigate the complexities of sourcing Monel 400, key considerations such as supplier certification, material traceability, and the balance between cost and quality become paramount. By prioritizing these factors, professionals can secure the necessary materials that uphold project integrity and operational efficiency. Ultimately, understanding the critical aspects of Monel 400 not only enhances material selection but also positions organizations for success in demanding engineering projects.