Blogs
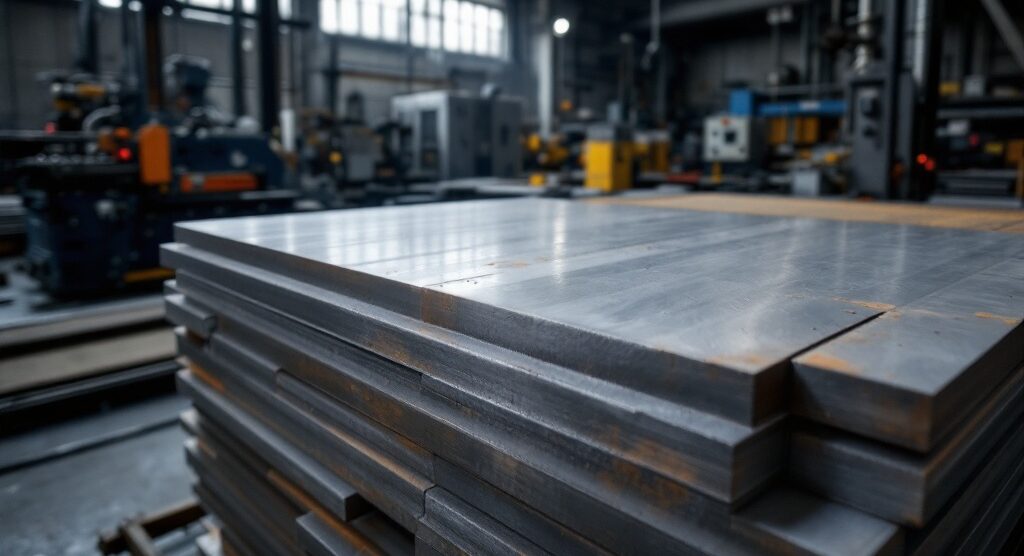
Understanding Monel 400 Plates: An In-Depth Tutorial on Properties and Applications
Introduction
In the realm of advanced materials, Monel 400 stands out as a premier choice for procurement managers seeking reliability and versatility. Comprising a unique blend of nickel and copper, this alloy is celebrated for its exceptional corrosion resistance, particularly in harsh marine environments, making it indispensable in industries ranging from marine engineering to chemical processing.
With its impressive mechanical properties and adaptability, Monel 400 not only meets the rigorous demands of various applications but also offers long-term cost savings through reduced maintenance requirements.
This article delves into the composition, key characteristics, and extensive applications of Monel 400, providing insights that empower procurement professionals to make informed decisions in material selection.
Whether navigating the complexities of marine engineering or ensuring compliance in chemical processing, understanding the advantages of Monel 400 is essential for optimizing performance in challenging environments.
Introduction to Monel 400: Composition and Characteristics
Nickel-copper material 400 is mainly made up of roughly 67% nickel and 23% copper, along with minor quantities of iron, manganese, carbon, and silicon. This distinct composition results in remarkable corrosion resistance, particularly in seawater and other aggressive environments, making it highly valued in marine applications. As part of our varied selection of copper nickel mixtures at Domadia, 400 serves not only in marine engineering but also has applications in automotive and electrical sectors.
The average physical properties of alloy 400 further illustrate its effectiveness:
- Density: 0.319 lb/in³ (8.83 g/cm³)
- Electrical resistivity: between 20.1 to 23.2 microhm-in
- Modulus of elasticity: 26.0 X 10^6 psi (179 GPA)
- Tensile strength at 425°C: over 370 MPa
Additionally, the proposed operating conditions for spring temper heat treatment vary from -300°F to 500°F (-184°C to 260°C), offering procurement managers insight into the material’s processing requirements. These characteristics, along with its capacity to withstand stress corrosion cracking and pitting, underscore its suitability in chemical processing industries.
Significantly, case studies show that Alloy K500, a variant of a nickel-copper material, exhibits superior resistance to hydrofluoric acid, highlighting the durability of nickel-copper substances in harsh chemical environments and further underscoring the resilience of the monel 400 plate in challenging uses. For procurement managers, understanding these foundational properties and the extensive applications of the monel 400 plate is essential for informed material selection in various projects. We encourage you to browse our product catalog to uncover the complete selection of copper nickel materials offered at Domadia, including 400, and see how they can fulfill your project requirements.
Key Properties of Monel 400 Plates: Strength, Durability, and Corrosion Resistance
Monel 400 plates are distinguished by their exceptional strength and durability, showcasing remarkable toughness even at elevated temperatures. Recent evaluations indicate that this alloy achieves a yield strength of approximately 30,000 psi (about 195 MPa) and an impressive tensile strength of around 75,000 psi (approximately 480 MPa). Notably, the Monel 400 plate is approved for pressure vessels from -10 up to 425°C according to VdTUV Material Sheet 263 and for temperatures up to 480°C by ASME Boiler and Pressure Vessel Code.
A significant trait of the Monel 400 plate is its exceptional corrosion resistance; it effectively endures both acidic and alkaline conditions, making the Monel 400 plate especially appropriate for chemical processing uses. Additionally, alloy 400 demonstrates low magnetic permeability, which is advantageous for certain electronic uses. The hot worked/sr hardness of Monel 400 ranges from a minimum of 552 MPa to a maximum of 276 MPa, with tensile strength at elevated temperatures exceeding 370 MPa at 425°C.
Understanding these properties is crucial for assessing the material’s performance across various contexts, particularly in industries that require reliability under challenging conditions. Furthermore, the Monel 400 plate is available in different shapes including bars, strips, and forgings, conforming to several standards such as DIN, ISO, ASTM, and NACE, ensuring adherence to industry standards and fulfilling diverse requirements. In environments where explosive potential exists, the importance of utilizing non-sparking tools cannot be overstated, as they provide a safe alternative for maintenance and operations.
Particular uses of copper nickel mixtures, such as their role in marine engineering for ship hulls and seawater piping systems, along with automotive systems for brake lines and hydraulic components, emphasize their versatility and effectiveness. Furthermore, the benefits of copper nickel mixtures over stainless steel in these applications reinforce their critical consideration for procurement managers.
Applications of Monel 400: Where and Why It Is Used
This monel 400 plate is a highly desired material across various sectors due to its remarkable characteristics, particularly its resistance to seawater corrosion, making it essential in the marine industry. It is frequently utilized in the manufacturing of boat propellers, pump shafts, and valves from monel 400 plate, where durability and performance under harsh marine conditions are essential. Additionally, the modulus of elasticity of Alloy 400 is 26.0 X 10^6 psi or 179 GPA, further underscoring its mechanical strength.
In the chemical processing sector, the monel 400 plate serves critical roles in equipment such as:
- Heat exchangers
- Reactors
- Piping systems that manage corrosive substances
Recent case studies demonstrate that the metal combination, primarily composed of nickel and copper, exhibits corrosion rates of no more than 0.03 mm/year, even in severe environments, solidifying its reliability over traditional copper mixtures. The case study named ‘Performance Analysis of a Nickel-Copper Alloy’ emphasizes its superior corrosion resistance in comparison to copper alloys, especially in maritime contexts.
Furthermore, its uses extend into the aerospace and oil and gas sectors, where components must endure extreme conditions. As procurement managers evaluate materials for a wide range of uses, the adaptability of the monel 400 plate stands out as a notable benefit, ensuring enduring performance and lower maintenance expenses. Sourcing high-quality alloy is essential, and Ulbrich Stainless Steel has been a leader in producing specialty metals and alloys for over a hundred years.
As pointed out by industry authority Fengyuan Yan,
The Tribo-Corrosion Behavior of 400 Alloy in Marine Environment at Varied Rotational Velocities
further highlights its appropriateness for challenging uses.
Advantages of Monel 400 Plates: Why Choose This Alloy?
Monel 400 plate is characterized by several significant benefits that render it suitable for challenging environments. The monel 400 plate offers exceptional resistance to corrosion, combined with high strength and durability, ensuring reliability in applications exposed to harsh conditions. Furthermore, the monel 400 plate is readily weldable, facilitating seamless integration into various designs without compromising structural integrity.
This characteristic is particularly beneficial in industries such as aerospace and chemical processing, where monel 400 plate materials must perform under elevated temperatures. In environments with explosive potential, incorporating Non-Sparking Tools, such as those made from aluminum bronze or copper-based alloys, alongside alloy 400 ensures safety and compliance with industry standards, making them an essential choice for procurement managers. As noted by Team Baosheng, ‘The versatility of alloy 400 allows for complex shapes to be manufactured, providing significant design flexibility.’
Procurement managers acknowledge the long-term cost savings linked to the monel 400 plate, thanks to its extended lifespan and reduced maintenance needs. With a machinability rating of 45%, alloy 400 not only provides performance but also improves economic efficiency, making it a top choice for essential uses.
Maintenance and Care for Monel 400 Plates: Best Practices
Effectively maintaining the Monel 400 plate requires a strategic approach, beginning with regular inspections to identify any early signs of wear or corrosion. While Alloy 400 is characterized by its nickel-copper composition—approximately 67% nickel and 30% copper—understanding its properties is crucial. In marine settings, copper nickel mixtures are frequently favored over stainless steel because of their excellent corrosion resistance, especially in seawater uses, which makes them perfect for parts such as ship hulls and offshore structures.
The benefits of copper nickel mixtures over stainless steel include:
- Improved resistance to biofouling
- Reduced maintenance requirements, leading to cost savings over time
Additionally, copper nickel alloys are utilized in automotive systems for brake lines and hydraulic uses, where their corrosion resistance is critical. For optimal maintenance of the Monel 400 plate, it is advisable to clean the surfaces using mild detergents, steering clear of abrasive materials that could compromise its integrity.
In environments where exposure to harsh chemicals is prevalent, applying protective coatings can further enhance longevity. Proper storage conditions—avoiding direct sunlight and controlling humidity—are vital for preventing degradation. A case study on Alloy 400 highlights its outstanding resistance to swiftly moving brackish or seawater, showcasing its appropriateness for uses needing cavitation and erosion resistance.
Notably, the alloy exhibits an ultimate tensile strength of 70.0 ksi (480 Mpa) and a yield strength of 25.0 ksi (170 Mpa), which are important considerations in its maintenance and application. Additionally, recent findings reveal that corrosion of a specific alloy in artificial seawater can affect mechanical degradation, with the corrosion product layer providing lubrication but increasing material loss rate and friction coefficient with rotational velocity. By adhering to these best practices, procurement managers can ensure that Monel 400 plates remain in peak condition over extended periods, thereby maximizing the return on their investment.
As Amjad Baig notes, > the significance of parameters like burr height remains largely unexplored <, highlighting the need for continued evaluation of maintenance practices to optimize performance. Furthermore, copper nickel alloys are also applied in electronics and heat exchangers, showcasing their versatility across various industries.
Conclusion
Monel 400 emerges as a premier choice for procurement managers seeking a robust material that excels in challenging environments. Its unique composition of nickel and copper grants it exceptional corrosion resistance, particularly in marine and chemical processing applications. The alloy’s impressive mechanical properties, including high tensile strength and durability, further solidify its position as a reliable option across various industries.
The extensive applications of Monel 400 illustrate its versatility, from marine engineering to automotive systems, demonstrating its ability to perform under extreme conditions. The alloy not only meets but often exceeds industry standards, ensuring compliance and reliability in critical operations. Furthermore, its weldability and design flexibility make it an attractive choice for complex projects, providing procurement managers with a strategic advantage.
By understanding the advantages and best practices for maintaining Monel 400, procurement professionals can maximize the longevity and performance of their investments. Regular inspections and appropriate care can significantly reduce maintenance costs, reinforcing the long-term economic benefits of utilizing this alloy. As industries continue to evolve and demand materials that can withstand the test of time, Monel 400 stands out as a strategic solution, combining reliability, performance, and cost-effectiveness for a wide range of applications.