Blogs
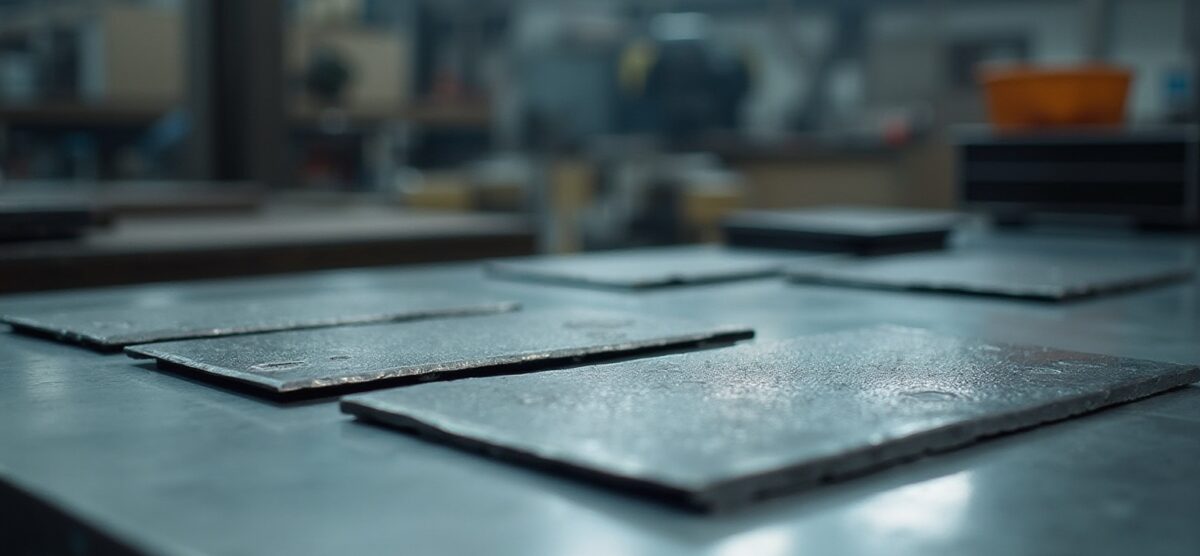
Understanding Monel Hardware: An In-Depth Tutorial on Properties and Uses
Overview
Monel hardware, primarily composed of nickel and copper, is valued for its exceptional corrosion resistance and mechanical strength, making it suitable for demanding applications in marine, chemical processing, and aerospace industries. The article supports this by detailing the unique properties of various Monel alloys, such as their ability to withstand extreme conditions and retain strength at high temperatures, which are critical for ensuring safety and efficiency in industrial settings.
Introduction
Monel alloys represent a pinnacle of engineering innovation, distinguished by their unique composition of nickel and copper that endows them with remarkable properties. With a significant presence in industries ranging from marine engineering to chemical processing, these alloys are celebrated for their exceptional resistance to corrosion and mechanical strength, even in the most demanding environments.
As procurement managers navigate the complexities of material selection, understanding the advantages and limitations of Monel alloys becomes crucial. This article delves into the intricate characteristics of Monel, exploring its diverse applications, comparative benefits over other materials, and the strategic considerations necessary for effective procurement.
By examining the nuances of Monel alloys, professionals can make informed decisions that enhance operational efficiency and ensure the longevity of critical components.
Introduction to Monel Alloys: Composition and Characteristics
These mixtures, primarily consisting of around 67% nickel and 30% copper, contain small quantities of iron, manganese, carbon, and silicon, leading to distinctive characteristics crucial for numerous uses. These metal mixtures, like monel hardware, demonstrate exceptional resistance to corrosion, particularly in marine environments, making them invaluable in sectors such as marine engineering, automotive, and electrical industries. With a thermal expansion coefficient of 13.9 µm/m°C and a thermal conductivity of 21.8 W/m·K, these materials ensure structural integrity and performance in demanding conditions.
Their high strength and toughness remain consistent even under elevated temperatures, reinforcing their importance in critical uses, including chemical processing and consumer products. Recent advancements in nickel-copper mixtures, such as Alloy 800, exemplify its adaptability and ongoing relevance. Alloy 800 has proven effective in heat exchangers within the petrochemical industry due to its remarkable resistance to stress corrosion cracking in chloride environments.
Moreover, the material’s application in nuclear engineering further underscores its mechanical strength and corrosion resistance, which are vital for maintaining safety and functionality in critical systems. At Domadia, we provide a varied selection of materials, including monel hardware like Alloy 800, customized for your project requirements. Our products meet compliance standards and are available in various sizes and weights, ensuring you have the perfect solution for your procurement requirements.
Key Properties of Monel: Strength and Corrosion Resistance
Alloys based on nickel-copper, particularly grade 400 and grade K-500, are celebrated for their exceptional strength and excellent resistance to corrosion, especially in both acidic and alkaline conditions. While their chemical compositions significantly influence their properties, the importance of Non-Sparking Tools in explosive environments cannot be overlooked. Non-Sparking Tools serve as the best alternative for safe use in such hazardous conditions, highlighting the need for reliable materials and tools in industries where explosive potential exists.
For example, K-500, which contains aluminum and titanium, boosts its strength, rendering it appropriate for drilling tools and parts that endure extreme pressure and temperature conditions. Their ability to retain mechanical properties at elevated temperatures makes them ideal for applications subject to extreme heat and pressure. Notably, the yield strength of this alloy can reach up to 60,000 psi, with tensile strength exceeding 100,000 psi, affirming its status as a formidable player among high-performance materials.
Terence Bell, a metal expert, emphasizes the importance of these alloys, stating,
This particular alloy is one of the few that retains its strength in sub-zero temperatures, so it is utilized in those conditions.
This resilience is complemented by the material’s exceptional resistance to pitting and stress corrosion cracking, enhancing its applicability in marine environments and chemical processing industries. Furthermore, welding this alloy, especially grade 400, to other metals requires specific techniques to ensure a strong bond, while machining presents challenges due to work hardening.
Effective machining necessitates careful parameter control and specialized tools to achieve high precision and quality in fabricated parts. Recent research further verifies that the mechanical characteristics of these metal mixtures remain strong even under elevated temperature conditions, establishing them as a dependable option for challenging uses, alongside the crucial role of Non-Sparking Tools in ensuring safety and efficiency. Significantly, suppliers like [Supplier Name] and [Manufacturer Name] offer a variety of Non-Sparking Tools and specialized metals, ensuring that industries have access to the materials necessary for safe operations in explosive environments.
Applications of Monel Alloys in Industry
Certain alloys are recognized for their exceptional properties, making them indispensable in numerous industrial applications. In the marine industry, monel hardware, which is a nickel-copper alloy, is extensively utilized for critical components such as valves, pumps, and fittings that are subjected to the harsh conditions of seawater. The unique corrosion resistance of this alloy makes monel hardware ideal for prolonged durability in these challenging environments.
Notably, the MODTRIP-130 composition exhibits significant partitioning of nickel and higher concentrations of titanium and aluminum, resulting in an additional nickel-aluminum rich phase and increased susceptibility to cracking, which is crucial for understanding its performance in demanding applications.
In the chemical processing sector, monel hardware is the preferred material for manufacturing equipment that handles aggressive corrosive substances, including pipes and tanks, due to its strength and resilience. Recent studies indicate a significant market share of this alloy, specifically monel hardware, in these industries, highlighting its vital role in maintaining operational efficiency and safety. For instance, microhardness measurements beneath the WEDM machined surface of nickel-copper materials extend up to 40 µm, demonstrating its durability and effectiveness in harsh conditions.
Furthermore, a relevant case study titled ‘PSO for AISI 4340 Steel Optimization’ by Manay et al. demonstrates the use of particle swarm optimization in transforming AISI 4340 steel to improve machining efficiency and tool durability, which can also be relevant to similar materials in comparable industrial settings.
Aerospace further benefits from monel hardware, where its superior strength-to-weight ratio is crucial for performance. Additionally, monel hardware finds utility in heat exchangers, electrical components, and fasteners, all of which leverage its durability and resistance to environmental factors. Prof. John Dupont highlights the significance of the material’s properties, stating that ‘the foundation of the Clyne and Davies solidification cracking model illustrates its performance under various conditions, offering insight into its uses in challenging environments.’
As sectors keep advancing, the strategic application of monel hardware as a corrosion-resistant metal remains vital for improving equipment longevity and efficiency.
Challenges and Limitations of Monel Alloys
Certain alloys, while recognized for their strength and corrosion resistance, present several challenges that procurement managers must consider. One of the most significant hurdles is their cost; this alloy is generally pricier than commonly used stainless varieties such as 304 and 316, which can greatly influence project budgets. Recent pricing reports from the MEA region indicated a slight decline in Monel hardware prices, with Alloy 400 Sheet priced at USD 38,335/MT in the UAE.
However, even with this decline, the cost remains a crucial factor when evaluating material options. As noted by Kat de Naoum, stainless steel is often referred to as ‘inox’ or rustless steel and is made of around 70–80% iron, with at least 10.5% chromium for the protective oxide layer. This composition aids in its cost-effectiveness and extensive utilization in comparison to Monel hardware.
Conversely, copper nickel mixtures present considerable benefits in marine settings and electrical contexts, including:
- High resistance to corrosion, especially in seawater
- Outstanding thermal and electrical conductivity
- Excellent ductility and simplicity of fabrication
- Antimicrobial properties, making them suitable for environments where hygiene is paramount
These advantages place copper nickel mixtures as a competitive option to both similar alloys and stainless steel in certain uses, especially in marine and electrical fields where resistance to corrosion is essential.
However, it is crucial to take into account possible drawbacks of copper nickel mixtures, such as their performance in highly acidic or alkaline settings, which may influence their durability. Specific applications where copper nickel materials excel include:
- Shipbuilding
- Offshore platforms
- Heat exchangers
In terms of workability, this alloy’s toughness necessitates specialized machining techniques and tools, complicating the fabrication process. This requirement often leads to extended production times and increased labor costs. Furthermore, these metal mixtures may not be appropriate for every environmental condition, especially where contact with specific corrosive substances might threaten their structural stability over time. As highlighted by industry insights, understanding these limitations is essential for making informed decisions regarding material selection and budget management in procurement strategies.
Moreover, while stainless materials such as 316 show enhanced resistance to chlorides and industrial solvents, as evidenced in numerous uses, the distinctive characteristics of copper nickel alloys must also be thoughtfully considered against these aspects to identify the most suitable option for particular uses.
Monel vs. Other Alloys: A Comparative Analysis
A comprehensive comparison of nickel-copper alloy and stainless materials reveals significant differences that affect material choice in diverse applications. Alloy 400 is renowned for its exceptional corrosion resistance, especially in marine settings and acidic environments. This makes it an ideal choice for industries where reliability and longevity are paramount.
In contrast, stainless material, often praised for its cost-effectiveness and ease of machining, tends to be favored in less aggressive environments. Significantly, stainless alloy 316, although cost-effective, cannot equal the corrosion resistance provided by a nickel-copper alloy in highly corrosive environments. Furthermore, the mechanical characteristics of this alloy at high temperatures are better than those of standard stainless grades.
As emphasized in the brittleness assessment, neither alloy nor stainless material is inherently brittle; however, the first maintains its ductility even under low-temperature conditions, significantly reducing the risk of brittleness—an important factor for uses exposed to extreme temperatures. This assessment highlights the appropriateness of monel hardware for low-temperature uses.
According to the latest insights, the decision between these alloys must take into account not only the specific use requirements but also the cost implications and environmental challenges. For instance, stainless alloy has a coefficient of thermal expansion of 16.0 µm/m·K, which may affect its performance in certain applications compared to Monel.
Ultimately, the choice to use monel hardware or stainless alloy hinges on a careful analysis of the operational requirements, where the advantages of monel hardware in corrosion resistance and mechanical integrity are weighed against the cost benefits and machining ease of stainless alloy. As noted by Kat de Naoum, stainless steel, sometimes referred to as ‘inox’ or rustless steel, is made of around 70–80% iron and at least 10.5% chromium for the protective oxide layer, which is essential to consider when evaluating its properties.
Conclusion
Monel alloys stand out as a premier choice for industries demanding exceptional strength and corrosion resistance. Their unique composition, primarily of nickel and copper, ensures remarkable performance in challenging environments, particularly within marine engineering, chemical processing, and aerospace applications. The alloys’ ability to maintain mechanical integrity at elevated temperatures and resist stress corrosion cracking makes them invaluable assets in critical operations.
Despite their advantages, procurement managers must navigate the challenges associated with Monel, including higher costs compared to alternatives like stainless steel and copper nickel alloys. Understanding these economic factors is essential to making informed decisions that align with project budgets while ensuring long-term reliability and safety. The comparisons drawn between Monel and other materials highlight the importance of selecting the right alloy based on specific application needs, environmental conditions, and operational requirements.
In conclusion, the strategic use of Monel alloys can significantly enhance the longevity and efficiency of equipment across various sectors. As industries continue to evolve and face new challenges, the insights gained from examining the properties and applications of Monel will empower procurement managers to make decisions that not only meet current demands but also anticipate future needs. Embracing the potential of Monel alloys positions organizations for success in a competitive landscape, ensuring that they remain at the forefront of engineering innovation.