Blogs
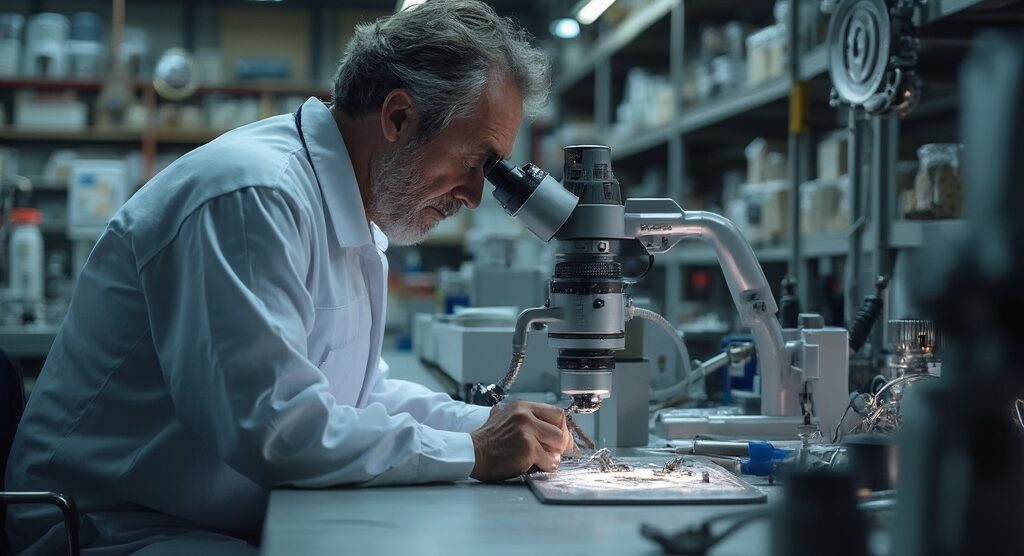
Understanding N04400: An In-Depth Tutorial on Monel 400 Alloy Properties and Uses
Introduction
In the realm of advanced materials, Monel 400 stands out as a premier nickel-copper alloy, celebrated for its remarkable resistance to corrosion and exceptional strength. With a composition that typically includes around 67% nickel and 30% copper, this superalloy is engineered to excel in some of the most demanding environments, including:
- Marine
- Chemical processing
- Aerospace industries
As the need for reliable materials intensifies, understanding the unique properties, applications, and fabrication techniques of Monel 400 becomes essential for procurement managers seeking to enhance operational efficiency and safety. This article delves into the intricacies of Monel 400, offering valuable insights into its applications, physical properties, and best practices for sourcing and fabrication, all while ensuring compliance with industry standards.
Introduction to Monel 400 Alloy: Composition and Classification
Alloy 400, which is classified as UNS N04400, is a nickel-copper mixture renowned for its exceptional resistance to corrosion, particularly in seawater and acidic environments, as well as its high strength. Typically made up of around 67% nickel and 30% copper, with small quantities of iron and manganese, Monel 400 is categorized as a superalloy, rendering it particularly useful in challenging environments. Its unique properties enable it to withstand corrosive environments, making it ideal for various industrial uses such as:
- Marine engineering
- Chemical processing
- Electrical sectors
Additionally, at Domadia, we offer a diverse range of copper nickel alloys, ensuring the perfect solution for your project needs. We also provide non-sparking tools, which are essential for safe operations in explosive environments. Discover our comprehensive product catalog, featuring mica tape items engineered for high-temperature resistance and electrical insulation, vital for uses in electrical engineering and more.
Applications of Monel 400: Where and Why It Is Used
Alloy 400 is widely utilized in several sectors due to its remarkable resistance to corrosion and high-temperature strength. While this section primarily concentrates on Alloy 400, it is important to note that Non-Sparking Tools made from n04400 are essential in explosive environments, and materials like n04400 can play a role in related uses. Key applications of alloy 400 include:
Marine Engineering: Its ability to resist corrosion in seawater makes this alloy an ideal choice for components such as propeller shafts, pumps, and valves in marine environments.
Chemical Processing: Alloy 400 is often utilized in chemical processing equipment, including heat exchangers and piping systems, due to its resistance to various acids and alkalis.
Oil and Gas: The alloy’s durability and resistance to sour gas environments make it suitable for components in oil and gas extraction and processing.
Aerospace: Alloy 400 is utilized in aerospace contexts where lightweight and corrosion-resistant substances are essential for performance and safety.
Electrical Uses: Due to its outstanding electrical conductivity, Alloy 400 is utilized in electrical connectors and other components where reliability is essential.
Overall, the versatility of n04400 makes it a favored choice across various sectors, contributing to improved performance and durability in challenging uses. Its properties may complement the use of Non-Sparking Tools in environments where safety and material integrity are paramount.
Physical Properties of Monel 400: Understanding Strength and Durability
Monel 400 exhibits impressive physical properties, including:
- Tensile Strength: Typically ranges from 70,000 to 90,000 psi, making it suitable for high-stress uses.
- Ductility: Monel 400 can be easily formed and shaped without fracturing, allowing for a variety of fabrication processes.
- Corrosion Resistance: It excels in resisting corrosive environments, particularly in acidic and saline conditions, thus ensuring longevity in uses.
- Temperature Resistance: Monel 400 maintains its strength and stability at elevated temperatures, making it ideal for scenarios where thermal resistance is critical.
In sectors where safety is paramount, the use of non-sparking tools is essential, especially in explosive environments. Moreover, integrating mica tape products, like Mica Insulation Tape and Mica Sheet Tape, recognized for their high-temperature resistance and electrical insulation characteristics, can further improve reliability and safety in electrical engineering contexts. Mica Insulation Tape is frequently utilized in essential uses, while Mica Sheet Tape offers strong insulation for extensive flat surfaces.
These properties together enhance the reputation of n04400 as a dependable and long-lasting substance in industries where performance cannot be compromised. For procurement managers, sourcing these materials from reputable suppliers and manufacturers is crucial for ensuring quality and compliance in applications.
Fabrication Techniques for Monel 400: Best Practices
When fabricating alloy 400, several best practices should be meticulously followed to ensure optimal performance and integrity:
Machining: Employ carbide tools for machining, as this alloy’s toughness can pose significant cutting challenges. Utilizing slower speeds combined with higher feeds can significantly enhance tool longevity, thereby reducing operational costs. This is particularly critical in explosive environments, where the use of Non-Sparking Tools, such as aluminum or bronze tools, is paramount to avoid ignition risks. According to Vollertsen, a clear explanation of the transition from conventional to micro-manufacturing processes highlights the importance of precision in machining, which is further supported by the spatial resolution improvement to 0.72 μm/pixel at a pixel resolution of 2592 × 1944.
Welding: Implement gas tungsten arc welding (GTAW) or gas metal arc welding (GMAW) techniques, ensuring the use of compatible filler substances. These methods are essential for attaining robust joints that maintain the substance’s intrinsic corrosion resistance, a crucial feature of 400 series. The transition to these advanced welding techniques aligns with the insights shared by Vollertsen on micro-manufacturing processes.
Forming: Adopt hot working techniques at approximately 1700°F (927°C). This temperature range enhances ductility, facilitating more effective forming operations and reducing the risk of failure.
Heat Treatment: Consider post-fabrication heat treatment to refine the mechanical properties of Monel 400. This process can improve the substance’s performance in particular uses, thereby prolonging its functional lifespan.
A practical example of these best practices can be observed in the case study titled ‘Machining By Feel,’ where a thermostat device customer sought a smooth and effortless sensation in their threaded assembly. After implementing the recommended machining techniques, the optimum ‘feel’ was achieved and documented, resulting in substantial cost savings.
Additionally, sourcing Non-Sparking Tools and other high-temperature materials from reputable suppliers, such as Electrical Insulation Paper Manufacturers and High-Temperature Fabric Suppliers, ensures that your operations comply with safety standards while maintaining product integrity. Following these best practices not only protects the integrity of n04400 throughout the fabrication process but also prepares it for superior performance in its intended applications.
Cost Considerations in Procuring Monel 400
When acquiring alloy 400, several cost factors should be considered:
- Market Fluctuations: Prices for nickel and copper can vary significantly, impacting the overall cost of the alloy n04400. Staying informed about market trends is essential.
- Supplier Relationships: Building strong relationships with suppliers can lead to better pricing and terms, as well as access to high-quality materials.
- Volume Discounts: Consider purchasing larger quantities to benefit from volume discounts, which can lower the overall procurement cost.
- Quality Assurance: Investing in quality assurance measures is crucial, as lower-quality n04400 can lead to higher long-term costs due to failures or reduced performance.
Additionally, it’s important to recognize the advantages of copper nickel alloys, particularly when comparing them to substances like stainless steel. These alloys exhibit exceptional corrosion resistance in marine environments, superior thermal and electrical conductivity, good ductility, ease of fabrication, and notable antimicrobial properties. Specifically, copper nickel alloys outperform stainless steel in marine environments due to their superior corrosion resistance, especially in saline or brackish waters.
They also possess superior thermal and electrical conductivity in comparison to stainless steel, making them perfect for heat exchangers and electrical uses. By understanding these factors, procurement managers can make informed decisions that balance cost with quality and performance, ensuring their projects meet the highest standards.
Compliance and Standards for Monel 400
Monel n04400 must comply with various industry standards and regulations, such as:
- ASTM Standards: n04400 is often specified under ASTM B164 for nickel-copper alloy products, ensuring quality and performance.
- NACE Standards: For applications in the oil and gas sector, adherence to NACE MR0175 is critical to prevent corrosion in sour service environments.
- ISO Standards: Compliance with ISO 9001 standards for quality management systems can enhance supplier credibility and ensure consistent quality.
Being aware of these standards is vital for procurement managers to ensure that the materials sourced meet the necessary requirements for safety, reliability, and performance.
Conclusion
Monel 400 emerges as a leading choice in the domain of advanced materials, particularly for industries facing challenging environments. Its unique composition and exceptional properties, including outstanding corrosion resistance and high tensile strength, make it indispensable for applications across marine engineering, chemical processing, aerospace, and more. Understanding these attributes allows procurement managers to make informed decisions that enhance operational efficiency and safety.
The importance of adhering to best practices in fabrication cannot be understated. Techniques such as:
– precise machining
– effective welding
– appropriate heat treatment
not only preserve the integrity of Monel 400 but also ensure its optimal performance in demanding applications. Furthermore, navigating cost considerations and supplier relationships can significantly impact procurement strategies, enabling managers to secure high-quality materials at competitive prices.
In conclusion, Monel 400 is not merely a material choice; it is a strategic asset that can drive performance and reliability in critical applications. By prioritizing quality, compliance with industry standards, and informed sourcing practices, procurement managers can leverage the advantages of Monel 400 to foster innovation and maintain a competitive edge in their respective fields.