Blogs
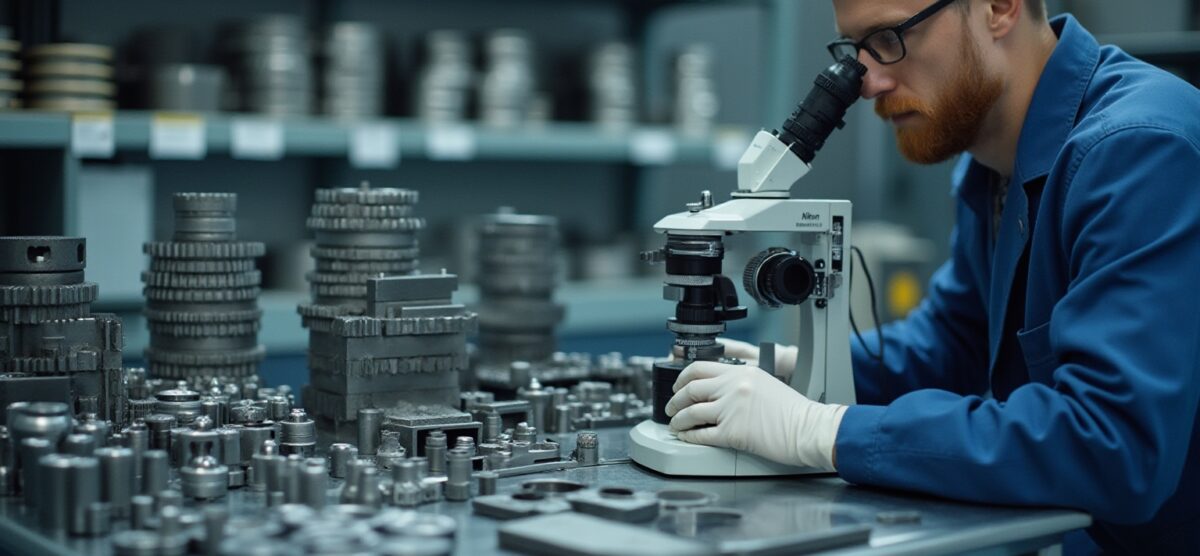
Understanding Nickel and Cobalt Alloys: An In-Depth Tutorial on Properties and Applications
Overview
Nickel and cobalt alloys are crucial in various industries due to their exceptional properties such as corrosion resistance, high strength, and thermal stability, making them ideal for applications in aerospace, automotive, electronics, and medical devices. The article elaborates on these alloys’ vital roles in enhancing performance and safety, particularly in non-sparking tools for explosive environments, thereby underscoring their importance in modern manufacturing and procurement strategies.
Introduction
Nickel and cobalt alloys stand at the forefront of modern engineering, distinguished by their remarkable properties that cater to a myriad of industrial applications. With an unparalleled combination of corrosion resistance, high strength, and thermal stability, these alloys are indispensable in sectors ranging from aerospace to healthcare.
As industries evolve and demand for advanced materials increases, understanding the fundamental characteristics and applications of nickel and cobalt alloys becomes essential for procurement managers. This article delves into the critical properties of these alloys, their diverse industrial applications, and the manufacturing processes that ensure their quality, while also highlighting future trends that promise to reshape their role in various sectors.
By exploring these facets, procurement professionals can make informed decisions that align with both performance requirements and strategic objectives.
Fundamental Properties of Nickel and Cobalt Alloys
Nickel and cobalt alloys possess several fundamental properties that render them invaluable across a range of applications, including non-sparking tools used in explosive environments. Key characteristics include:
Corrosion Resistance: These materials demonstrate remarkable resistance to oxidation and corrosion, making them ideal for challenging environments, particularly within chemical processing and marine sectors. Recent studies indicate that certain nickel mixtures, such as Ni6, exhibited a staggering 500-fold decrease in polarization resistance after just seven days in Ringer’s solution. This statistic highlights the critical need for careful selection based on corrosion performance. Moreover, a case study named “Corrosive Behavior of Dental Materials in Ringer’s Solution” assessed the corrosive behavior of various nickel and cobalt alloys based dental materials, revealing that while CoCr specimens maintained a stable passive layer, Ni4, Ni5, and Ni6 experienced significant degradation, emphasizing the importance of understanding material performance in practical uses.
High strength is a key characteristic of nickel and cobalt alloys, which maintain outstanding strength at high temperatures, making them essential for components used in aerospace and automotive sectors. This high strength of nickel and cobalt alloys also ensures reliability and safety for non-sparking tools that must perform under stress in explosive environments.
Thermal Stability: Able to endure elevated temperatures without considerable deterioration, nickel and cobalt alloys are ideally suited for high-performance uses, including non-sparking tools where thermal resilience is essential.
Magnetic Characteristics: Cobalt mixtures display unique magnetic characteristics, which are crucial in numerous electronics and electrical uses, offering functionalities that other substances cannot replicate.
Weldability: Many nickel and cobalt alloys are easily weldable, facilitating their use in diverse fabrication processes and ensuring versatility in manufacturing, including the production of non-sparking tools.
Grasping these characteristics not only assists in material choice but also guides strategic decisions for procurement managers aiming to enhance performance and durability in their uses. As Baipo Shu stated, “The assessment of these materials through thorough investigations is essential for progressing understanding in corrosion resistance and improving their usage potential.” This emphasis on expert insights further underscores the importance of thorough material assessment, especially when considering the critical role of non-sparking tools in maintaining safety in explosive environments.
Applications of Nickel and Cobalt Alloys in Industry
Nickel and cobalt alloys are integral to numerous industries, thanks to their remarkable properties, which include high strength, thermal stability, and corrosion resistance. Their applications are notably diverse:
Aerospace: These materials are vital in aircraft engines and components, where performance under extreme conditions is non-negotiable.
With the aerospace sector witnessing robust growth—evidenced by Airbus’s backlog of 8,749 aircraft as of September 2024—materials that can withstand high temperatures and pressures are essential. As Laura Wood, Senior Press Manager at ResearchAndMarkets.com, notes, the aerospace industry is increasingly relying on advanced materials to meet growing demands.Automotive: In the automotive sector, nickel and cobalt alloys are essential in turbines, exhaust systems, and battery parts, due to their durability and resistance to corrosion.
Recent advancements emphasize the automotive industry’s growing dependence on these materials, especially with innovations such as the partnership between Aperam S.A. and Tekna, focused on improving spherical powder production of specialty metals.Electronics: Nickel and cobalt alloys are frequently employed in electrical contacts and magnetic materials, attributed to their superior magnetic properties, which are essential in modern electronic devices.
Chemical Processing: The capacity of certain metal mixtures to withstand corrosive conditions renders them perfect for chemical reactors and piping systems, guaranteeing dependability in challenging chemical operations.
Medical Devices: Nickel-titanium compositions, especially nitinol, are increasingly utilized in medical devices such as stents due to their biocompatibility and unique shape memory properties, showcasing their importance in healthcare innovation.
Energy Sector: In power generation and oil drilling, the use of nickel and cobalt alloys, as well as other metal mixtures, is crucial for maintaining safety and efficiency in equipment designed for extreme conditions.
In addition to these uses, Non-Sparking Tools are essential in explosive environments, offering a safe alternative for operations where traditional tools may pose risks.
These tools are specifically designed to prevent sparks that could ignite flammable substances, making them indispensable in industries like oil and gas, mining, and chemical processing. Comprehending these tools empowers procurement managers to align their sourcing strategies with industry trends and project requirements.
The insights presented are supported by a detailed research methodology employed by Stratview Research, which includes extensive secondary research and primary interviews with industry stakeholders, ensuring high-quality insights and data validation.
By integrating these elements, procurement managers can select optimal materials and tools that meet both performance and regulatory standards.
Manufacturing Processes for Nickel and Cobalt Alloys
Frequently Asked Questions about Copper Nickel Alloys
Q1. What are the typical uses of copper and its combined metals?
Understanding the practical applications of copper nickel alloys is crucial for procurement managers, particularly their advantages over stainless steel in marine environments and electrical applications:
Marine Engineering:
Copper copper-based mixtures excel in marine environments, offering superior corrosion resistance, making them ideal for components such as ship hulls, offshore platforms, and seawater piping systems. Their durability ensures long-lasting performance, reducing maintenance costs.Automotive Systems:
In the automotive sector, copper copper-based materials are employed for brake lines and hydraulic systems. Their excellent corrosion resistance enhances the reliability and safety of critical vehicle components.Electronics:
The mixtures are also utilized in electronics, where their conductive properties are advantageous. They play a vital role in ensuring efficient performance in various electronic applications.Heat Exchangers:
Copper copper-based materials are preferred in heat exchangers because of their resistance to erosion and biofouling, which enhances efficiency and durability.Currency:
Their applications extend to currency, where the unique properties of copper-based mixtures contribute to the durability and aesthetic appeal of money.
By understanding these applications, procurement managers can make informed decisions regarding material selection, ensuring they choose the best mixtures for their specific needs.
Quality Control and Standards in Nickel and Cobalt Alloys
Ensuring high standards in the procurement of special metals is critical, with quality control governed by rigorous specifications, including:
- ASTM Standards: The American Society for Testing and Materials has established comprehensive specifications for various nickel and cobalt alloys, including a reference to ASTM F1684-06(2021), which outlines essential performance metrics and quality benchmarks. The active Standard A 1056 continues to guide best practices in material procurement, ensuring that resources meet current industry standards.
- ISO Certifications: A significant number of manufacturers pursue ISO certification, reflecting their dedication to robust quality management systems and continuous improvement in manufacturing processes. Statistics show that ISO-certified manufacturers are more likely to maintain high-quality standards, serving as a benchmark for assessing a manufacturer’s reliability and commitment to quality.
- Testing Methods: Key testing protocols are employed to validate the integrity and performance of metal mixtures. These include tensile strength tests, corrosion resistance evaluations, and microstructural analysis, all designed to confirm that the materials adhere to established specifications.
- Supplier Audits: Conducting regular audits of suppliers is vital for ensuring compliance with quality standards. These audits not only verify adherence to specifications but also provide procurement managers with valuable insights into the operational practices of their suppliers.
- Financial Considerations: Additionally, procurement managers should be aware of the shipping fees associated with their orders; for instance, orders of $5000.00 and higher incur a shipping fee of $225.00. This practical financial aspect is crucial for budgeting and cost management in procurement decisions.
By thoroughly understanding these quality control measures, procurement professionals can effectively mitigate risks linked to material defects, ensuring the acquisition of superior-quality metals that meet stringent performance criteria.
Future Trends in Nickel and Cobalt Alloy Applications
As industries keep advancing, the uses of metal mixtures are set for substantial growth across various sectors.
- Electric Vehicles (EVs): The shift towards electric mobility is driving an increased demand for lightweight and high-strength materials. Advanced alloys, specifically nickel and cobalt alloys, are becoming essential for enhancing battery production and structural components, meeting the stringent requirements of modern EVs.
Notably, the difference between the highest and lowest projections for nickel production represents about 60% of the current supply, highlighting potential volatility in availability.
- Renewable Energy: The durability and performance of materials in renewable energy applications are critical. Nickel and cobalt alloys are currently under extensive research to improve their effectiveness in wind turbines and solar panels, contributing to the efficiency of these sustainable technologies.
However, lithium supplies will likely be tight globally, causing pricing volatility along with potential supply chain risks, which can affect the availability and pricing of alloys containing other metals.
Additive Manufacturing: The emergence of 3D printing technology offers new possibilities for using nickel and cobalt-based materials. This innovative approach allows for the creation of complex parts with reduced waste, which aligns with current industry trends towards efficiency and sustainability.
Medical Advancements: The demand for high-performance medical devices drives innovations in biocompatible materials. Nickel and mixtures are increasingly being utilized in surgical tools and implants, highlighting their significance in progressing healthcare technology.
Sustainability: As the demand for eco-friendly solutions increases, the repurposing of metals is receiving focus. This focus not only enhances material sustainability but also supports the development of more responsible procurement strategies.
For instance, a recent case study highlighted that in 2022, the average battery price was about USD 150 per kWh, with rising material prices impacting overall battery costs. This underscores the importance of nickel and cobalt alloys in the evolving landscape of battery technology, allowing procurement managers to stay informed of these trends and strategically position their organizations to capitalize on emerging market opportunities, ultimately driving growth and innovation in their respective fields.
Conclusion
Nickel and cobalt alloys play a pivotal role in the modern industrial landscape, characterized by their exceptional properties such as corrosion resistance, high strength, and thermal stability. These attributes make them indispensable across various sectors, including:
- Aerospace
- Automotive
- Electronics
- Healthcare
The diverse applications of these alloys highlight their versatility and the critical need for procurement managers to understand their unique characteristics when making sourcing decisions.
The manufacturing processes and quality control measures surrounding nickel and cobalt alloys further emphasize the importance of rigorous standards and testing protocols. By adhering to ASTM specifications and ISO certifications, procurement professionals can ensure that the materials they select meet the stringent performance requirements necessary for their applications. This meticulous approach helps mitigate risks associated with material defects and enhances overall project success.
Looking ahead, the future trends in nickel and cobalt alloy applications present exciting opportunities for innovation and growth. The shift towards electric vehicles, advancements in renewable energy technologies, and the rise of additive manufacturing are reshaping the landscape of material usage. By staying abreast of these developments, procurement managers can align their strategies with industry trends, ensuring they source materials that not only meet current demands but also position their organizations for future success.
In summary, the strategic understanding of nickel and cobalt alloys is essential for procurement managers aiming to optimize performance and durability in their operations. By leveraging expert insights and industry knowledge, organizations can make informed decisions that enhance their competitive edge and drive sustainable growth in an ever-evolving market.