Blogs
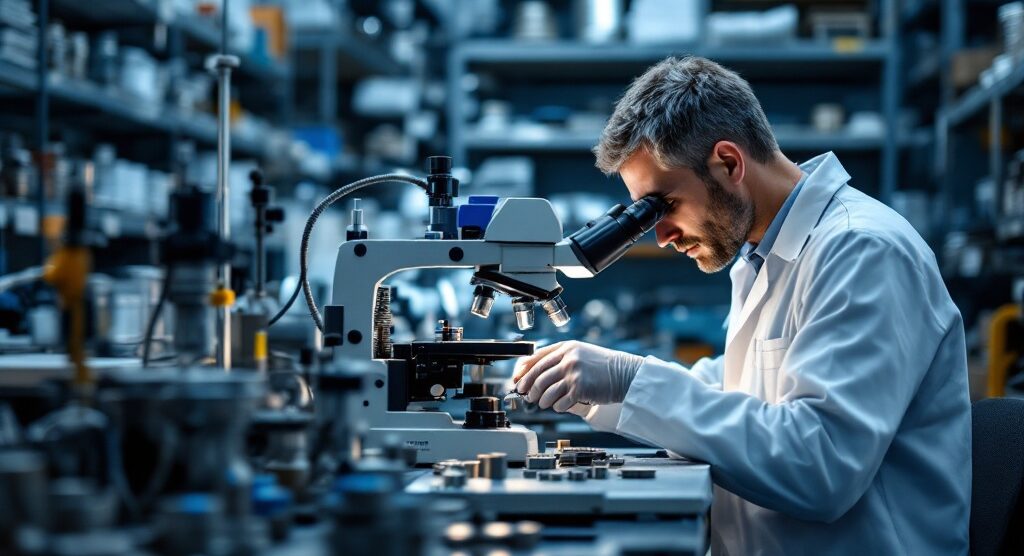
What Are Nickel Alloys Properties? A Comprehensive Overview
Introduction
In the realm of advanced materials, nickel alloys stand out as a cornerstone of modern engineering, prized for their exceptional properties and versatility across diverse industries. Comprised primarily of nickel and often enhanced with various elements, these alloys exhibit remarkable resistance to corrosion, mechanical strength, and stability at elevated temperatures. Their significance is underscored by the fact that stainless steel accounts for a substantial portion of global nickel consumption, reflecting the alloy’s integral role in manufacturing.
However, the landscape of nickel alloy production is shifting, with forecasts indicating a decline in output within Europe due to geopolitical factors. As industries increasingly turn to these materials for applications ranging from aerospace to chemical processing, a comprehensive understanding of nickel alloys—including their types, properties, and limitations—becomes essential for procurement managers seeking to leverage their unique advantages while navigating the challenges they present.
This article delves into the intricacies of nickel alloys, offering insights that will empower decision-makers to make informed choices in their procurement strategies.
Introduction to Nickel Alloys: Definition and Overview
Nickel-based mixtures are sophisticated metallic substances primarily consisting of this metal, frequently augmented with different elements to enhance particular traits. Renowned for their outstanding resistance to corrosion, exceptional mechanical strength, and stability at high temperatures, the nickel alloys properties make these materials integral to numerous industrial applications. As emphasized by the Nickel Institute Organization, stainless steel by itself represents over two-thirds of worldwide consumption of this metal, highlighting its essential role in contemporary manufacturing.
However, the creation of metal mixtures in Europe is projected to decline by nearly -4% in 2023, indicating reduced output from the Russian Federation. Additionally, FeNi production saw a significant decline of 10% in 2022, down to 341,000 tons, due to shutdowns and operational disruptions across several sites. The versatility of nickel alloys properties enables their application in extreme environments, making them essential in sectors such as aerospace and chemical processing.
For example, VDM Metals recently collaborated with Rosswag Engineering to utilize VDM Powder 699 XA, a nickel-chromium-aluminum composition designed for highly corrosive environments in the petrochemical sector. This case study illustrates the material’s resistance to corrosion, which is crucial for uses in synthesis gas processes for producing hydrogen, ammonia, and methanol. A comprehensive understanding of the meaning and intrinsic traits of nickel alloys properties is crucial for assessing their varied attributes and extensive uses in later discussions.
Key Properties of Nickel Alloys: Mechanical and Physical Characteristics
Nickel alloys properties are characterized by several crucial attributes that differentiate them from other metals, rendering them indispensable in various industrial uses. These nickel alloys properties encompass the following:
Corrosion Resistance: The nickel alloys properties demonstrate exceptional resistance to oxidation and corrosion, which is especially beneficial in severe environments like marine settings.
They maintain corrosion rates typically below 0.0025 mm/yr, a feature critical for industries like pulp and paper milling. Significantly, copper-copper mixtures surpass stainless steel in saline or brackish waters, providing excellent corrosion resistance and rendering them perfect for heat exchangers and electrical uses. Furthermore, their antimicrobial properties render them appropriate for uses where hygiene is paramount.High-Temperature Strength: Many nickel compositions retain strength and stability at elevated temperatures, essential for applications in aerospace and power generation sectors. This high-temperature strength is supported by ongoing advancements in composite formulations and the use of high-temperature materials, including electrical insulation papers and heat protection fabrics from reputable suppliers.
Ductility and Toughness: These materials demonstrate excellent ductility, allowing substantial deformation without fracturing. This asset is crucial during manufacturing, ensuring that components can be shaped effectively due to nickel alloys properties, which is vital for producing reliable Non-Sparking Tools for explosive environments.
Magnetic Traits: Certain nickel mixtures exhibit distinctive magnetic features, rendering them appropriate for electronic uses where such traits are essential.
The significance of these traits cannot be exaggerated, as they directly affect the appropriateness of nickel alloys properties for specific applications, ultimately impacting both performance and durability. For instance, a recent study on Alloy 718 highlighted the effects of chemistry and microstructure on localized corrosion performance. As J.R. Kish noted, ‘Corrosion of Surface-Treated Type 304 Stainless Steel in Alkaline Subcritical Water’ emphasizes the critical nature of corrosion resistance in material performance.
Furthermore, the case study titled ‘SEM Analysis of Crevice Attack Morphology’ illustrates the practical implications of these properties, showing how Alloy 718 samples exhibited signs of crevice and pitting corrosion under specific conditions. For procurement managers, considering suppliers of electrical insulation papers, heat protection fabrics, and other related materials is essential for ensuring the best quality and performance.
Types of Nickel Alloys: Composition and Variations
Nickel alloys can be broadly categorized into distinct types, each tailored to specific applications and characterized by unique properties:
The nickel alloys properties of Nickel-Copper compositions are renowned for their remarkable corrosion resistance and high strength, making these materials particularly advantageous in marine environments. Copper-nickel mixtures selected for seawater applications usually include 10 to 30 percent of the metal, greatly improving their performance. W. H. Hatfield remarked, “We discovered that incorporating nickel into these mixtures would render them highly resistant to corrosion,” emphasizing their appropriateness for seawater use.
Nickel-Chromium Mixtures: With superior heat resistance, nickel-chromium mixtures are essential in high-temperature applications, such as gas turbines. The nickel alloys properties that allow them to maintain structural integrity under extreme thermal conditions make them invaluable in energy generation and aerospace sectors.
Nickel alloys properties, particularly those of nickel-molybdenum compositions, are specifically designed to endure aggressive environments, making them ideal for chemical processing industries. The nickel alloys properties of their composition allow for exceptional resistance to pitting and crevice corrosion, ensuring reliability in harsh operational conditions.
Superalloys, representing the pinnacle of nickel-based metal technology, are designed to maintain their nickel alloys properties at high temperatures and stress levels. They are predominantly used in aerospace and turbine sectors, where performance under extreme conditions is critical.
At Domadia, we provide a diverse selection of copper materials designed for various uses, including marine engineering and electronics. Our dedication to quality guarantees that each material undergoes rigorous testing and inspection processes to meet the highest industry standards, reinforcing reliability and performance. The unmatched expertise of our team allows us to provide both standard and custom solutions tailored to your specific needs.
Additionally, our non-sparking tools are essential in explosive environments, ensuring safety and preventing ignition in potentially hazardous situations. Our mica tape products also provide high-temperature resistance and electrical insulation, crucial for safety and performance across various industries. This comprehensive approach highlights the versatility and reliability of nickel materials in real-world scenarios.
Applications of Nickel Alloys: Where They Are Used
Nickel alloys properties are integral to a multitude of industries, primarily due to their exceptional characteristics that enhance performance and safety. Their notable applications include:
- Aerospace: Nickel mixtures are extensively utilized in engine components and structural parts, where their high-temperature strength and oxidation resistance are critical.
Recent research highlights the evolution of Ni-based superalloys, particularly in the design of single crystal gas turbine blades, showcasing a significant advancement from earlier generations derived from columnar grained materials. Ahmad Mortazavi notes,
The chemistry of the Ni-based superalloys designed for single crystal gas turbine blades has significantly evolved since the development of the first generation of materials derived from columnar grained substances.
- Chemical Processing: In this sector, nickel-based materials are essential for producing equipment and piping systems that manage corrosive substances, ensuring both durability and safety. The rise of cobalt and titanium levels in nickel base mixtures, from 1.08% & 9.31% to 2.68% & 10.78%, has been demonstrated to significantly improve nickel alloys properties, such as ultimate tensile strength, yield strength, and hardness.
These improvements are vital for enhancing the performance of nickel alloys properties in challenging environments.
- Electronics: The alloys are also utilized in connectors and components where electrical conductivity and corrosion resistance are paramount, making them ideal for various electronic uses. Complementing this, Mica Tape Products from Domadia, recognized for their high-temperature resistance and electrical insulation, are crucial in electrical engineering uses, ensuring reliability in critical environments.
Domadia provides a range of Mica Tape products, such as Mica Insulation Tape, Mica Tape for Electrical, and Mica Sheet Tape, each crafted for distinct uses and high-performance standards.
- Marine Uses: In ship construction and offshore structures, the resistance of nickel-based materials to seawater corrosion is essential, facilitating their use in settings where exposure to severe conditions is common.
These uses highlight the adaptability of nickel-based materials and their crucial role in fostering technology across various sectors, showcasing the important nickel alloys properties. Furthermore, the importance of Non-Sparking Tools in explosive environments cannot be understated, as they provide safe operational solutions in potentially hazardous locations.
Recent case studies, such as those concentrating on α-Ti materials for aeronautic uses, demonstrate that while modifications can enhance yield strength, they often involve trade-offs in ductility, thereby emphasizing the need for careful consideration in material selection for specific uses.
Additionally, ongoing research identifies key factors influencing stray grain formation in metal alloys, including the angle of primary grain dendrites and thermal gradients, highlighting the importance of these advancements in aerospace applications.
Domadia’s dedication to quality, vast industry expertise, product variety, and competitive pricing further establishes them as a leading provider of pure metal. Customers have praised Domadia for their exceptional service and product quality, stating,
‘Domadia’s pure nickel products have consistently met our high standards, and their team is always ready to assist with our needs.’
This ensures that procurement managers have access to the best solutions for their needs.
Limitations of Nickel Alloys: Challenges and Considerations
Nickel mixtures, while highly valued for their unique properties, present several limitations that procurement managers must carefully evaluate:
Cost: Nickel mixtures are often more expensive than alternative materials, which can significantly influence project budgets. Recent reports suggest that the U.S. market for nickel-based materials was valued at roughly USD 38.6 billion in 2024, primarily fueled by demand from the automotive and aerospace industries. This cost factor requires vigilant consideration during procurement processes. Additionally, the 0.2% proof stress of CuNi30Fe2Mn is 145 N/mm, highlighting the material’s strength which can justify its cost in high-performance applications.
Machinability: The toughness and hardness of specific metal mixtures can create machinability challenges. These metal mixtures often necessitate specialized equipment and techniques, complicating manufacturing processes. Machinability statistics indicate that certain metal mixtures may require more time and resources to machine compared to other materials, thereby increasing overall project costs. For instance, operational considerations in palladium-nickel mixture electroplating demonstrate that factors such as surface quality and part complexity can significantly affect costs, making it essential to evaluate these aspects during procurement.
Availability: The capacity to procure particular metal combinations can be challenging, especially in areas without strong supply networks. This limitation can lead to delays and increased costs, necessitating strategic planning to ensure timely access to required materials. Furthermore, for projects in explosive environments, procurement managers should consider the accessibility of non-sparking tools from reputable suppliers like Domadia, which ensures that quality tools are readily available to maintain safety and efficiency in operations. Non-sparking tools are essential in such environments as they prevent accidental ignition, thereby safeguarding personnel and equipment.
Environmental Considerations: The production and disposal of nickel alloys properties raise significant environmental concerns. Compliance with regulatory standards is essential to mitigate potential impacts, making environmental considerations a critical part of the decision-making process. Procurement managers should evaluate suppliers not only on product quality but also on their adherence to environmental regulations and sustainability practices.
Understanding these limitations is crucial for procurement managers. By addressing cost, machinability challenges, sourcing issues, and environmental implications, alongside the importance of selecting reliable suppliers for non-sparking tools, they can make informed decisions that align with their project goals and budgetary constraints. Additionally, reviewing user manuals for non-sparking tools can provide valuable insights into their proper usage and selection, further enhancing procurement strategies.
Conclusion
Nickel alloys are an indispensable component of modern engineering, offering a combination of exceptional properties that cater to a wide range of industrial applications. Their remarkable corrosion resistance, high-temperature strength, and unique magnetic characteristics make them vital in sectors such as aerospace, chemical processing, and electronics. As industries increasingly rely on these materials, understanding the distinct types of nickel alloys and their specific applications becomes critical for procurement managers aiming to optimize their supply chains and project outcomes.
However, the landscape of nickel alloy production faces challenges, particularly with predicted declines in output in Europe due to geopolitical factors and market fluctuations. The associated costs and machinability issues pose additional hurdles that decision-makers must navigate. It is imperative for procurement managers to weigh these limitations against the unique advantages that nickel alloys provide, ensuring that their selections align with both technical specifications and budgetary considerations.
In summary, a strategic approach to procuring nickel alloys requires a comprehensive understanding of their properties, types, and applications, as well as an awareness of the challenges involved. By leveraging this knowledge, procurement managers can make informed choices that not only enhance operational efficiency but also contribute to the long-term success of their projects in an increasingly competitive landscape.