Blogs
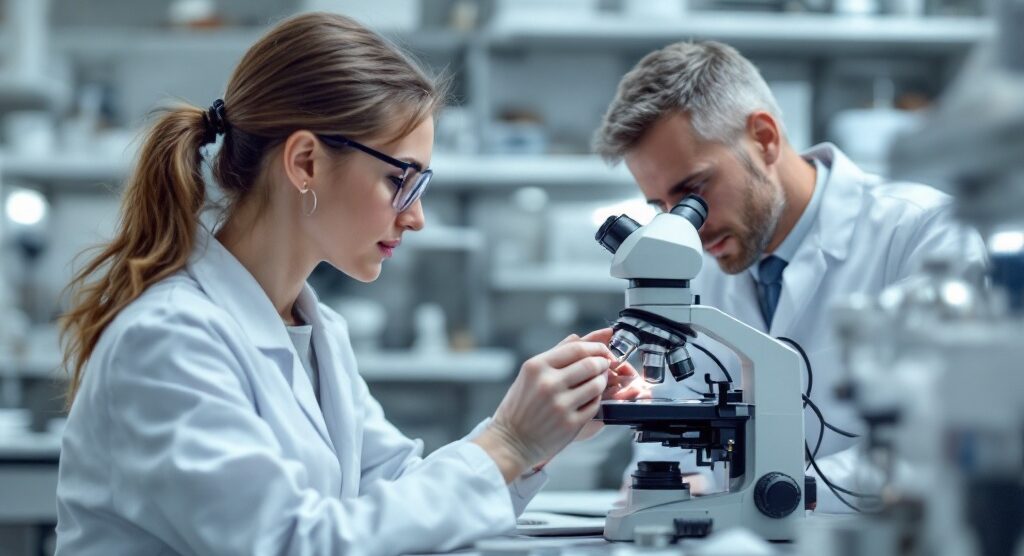
What Elements Are Often Used in Magnets? A Comprehensive Overview
Introduction
In the realm of modern manufacturing and technology, the significance of magnets cannot be overstated. From powering electric vehicles to enabling advanced medical imaging, the diverse applications of various magnet types underscore their critical role across industries. As procurement managers navigate the complexities of magnet sourcing, an in-depth understanding of:
- Magnet composition
- The unique properties of materials like neodymium and Alnico
- The challenges posed by rare earth element supply chains
is essential. This article delves into the key elements that define magnet performance, explores the latest trends in magnet technology, and examines the strategic considerations necessary for optimizing procurement decisions in an ever-evolving market landscape. With insights into future developments and industry projections, this exploration aims to equip professionals with the knowledge needed to make informed choices that can drive operational efficiency and innovation.
Key Elements in Magnet Composition
Magnets fundamentally rely on ferromagnetic materials, which possess the capacity to be magnetized and display pronounced magnetic properties. Iron, cobalt, and nickel are examples of what elements are often used in magnets, as they are the main components that make up magnetic material. Iron stands out as the most prevalent element, recognized for its ease of magnetization, which illustrates what elements are often used in magnets, making it a staple in the creation of various magnetic devices.
Cobalt plays a crucial role in improving both the magnetic strength and thermal stability of the device, highlighting what elements are often used in magnets to ensure dependability in various uses. Nickel is one of the key components to consider when discussing what elements are often used in magnets, as it improves corrosion resistance, which is critical for maintaining performance in challenging environments. This is where the exceptional characteristics of copper nickel alloys come into play, offering superior corrosion resistance, excellent thermal and electrical conductivity, and mechanical properties that make them suitable for demanding uses in the marine, automotive, and electrical sectors.
Furthermore, rare earth materials, especially neodymium and samarium, have gained significance for their capacity to produce extraordinarily strong permanent devices. These components greatly enhance the performance of the device, making them essential in uses spanning from electric motors to sophisticated electronic systems. As highlighted by industry specialists, including SNS Insider, Molycorp Inc. has revealed intentions to increase its production capacity for neodymium and dysprosium in 2023, emphasizing the rising demand for these essential materials in high-performance uses.
As stated in the Nickel Global Market Report 2024, the worldwide market for nickel, which is crucial in the composition of magnets, is expected to expand due to rising uses in different sectors. Understanding what elements are often used in magnets, along with the intricacies of these ferromagnetic components and the technical specifications of copper nickel alloys, such as their corrosion and oxidation resistance, is essential for evaluating the suitability of these materials in specific applications, as different elemental compositions yield varying magnetic characteristics that can impact operational efficiency. Moreover, insights into the financial performance of leading companies like Asea Brown Boveri can provide further context on the economic aspects of the industry, highlighting the importance of strategic investments in ferromagnetic materials.
Exploring Different Types of Magnets: Neodymium and Alnico
Neodymium magnets, commonly referred to as NdFeB magnets, stand out as some of the most powerful permanent magnets available, illustrating what elements are often used in magnets, primarily composed of neodymium, iron, and boron. Their remarkable strength-to-size ratio makes them exceptionally effective for compact uses such as electric motors, hard disk drives, and a variety of consumer electronics. This superior magnetic strength is attributed to their unique crystalline structure, enabling high-energy product values that are crucial in contemporary technological uses.
In contrast, Alnico alloys, which consist of aluminum, nickel, and cobalt, excel in high-temperature environments, showcasing what elements are often used in magnets due to their impressive temperature stability and resistance to demagnetization. These devices are often employed in situations requiring high efficiency at elevated temperatures, such as uses in guitar pickups and industrial sensors. For procurement managers, grasping the fundamental distinctions between neodymium and Alnico magnets is crucial for choosing optimal materials suited to particular uses, thereby ensuring both improved performance and compliance with industry standards.
Significantly, alongside magnetic components, Mica Tape Products serve an essential function in high-temperature resistance and electrical insulation across various uses. Mica Insulation Tape is designed for high-temperature resistance and electrical insulation, ensuring reliability in various uses, while Mica Sheet Tape provides a robust solution for insulating large flat surfaces, particularly in aerospace and automotive sectors. Additionally, Mica Tape for Electrical applications offers excellent flame resistance and dielectric strength, making it essential for manufacturing fire-resistant cables and other critical electrical insulation systems.
As the market for permanent materials evolves, with projections indicating a robust growth rate of 11.9% CAGR from 2024 to 2033, this growth reflects increasing demand in sectors such as electric vehicles and renewable energy technologies. The strategic choice of both high-performance components and quality insulation materials, such as Mica Tape Products, will be essential in maintaining competitive advantage in these advancing sectors.
The Role of Rare Earth Elements in Magnet Production
To understand what elements are often used in magnets, it is important to note that rare earth materials, particularly neodymium and dysprosium, are essential in the creation of high-performance devices. Neodymium materials are acknowledged as some of the strongest available, primarily because of what elements are often used in magnets that impart unique properties. Dysprosium is especially important as it is frequently included to enhance the thermal stability of neodymium magnets, highlighting what elements are often used in magnets to allow them to operate effectively in high-temperature contexts.
However, the procurement of these rare earth resources is fraught with challenges related to geopolitical tensions and complex supply chains. As highlighted by recent trends, with clean energy applications driving demand growth—especially from electric vehicles—procurement managers are faced with the critical task of navigating these sourcing hurdles. In 2024, supply chain statistics indicate that addressing these challenges is essential for ensuring a consistent supply of these vital materials.
This necessitates a careful balancing act of cost, availability, and performance criteria within sourcing strategies. Notably, 72% of executives of global metals companies are willing to invest in IoT technologies, which could serve as a potential solution to enhance supply chain visibility and efficiency. The International Energy Agency has projected a sixfold increase in mineral requirements for clean energy technologies by 2040, further emphasizing the urgency of tackling these sourcing issues effectively.
Additionally, Asia-Pacific was the largest region in the rare earth metals market in 2023, underlining the region’s strategic importance in this sector. Grasping the influence of dysprosium on neodymium performance and remaining updated on current reports regarding dysprosium in production will be essential for procurement professionals in this changing landscape. Furthermore, the case study on future projections for rare-earth element demand highlights that global demand is projected to grow significantly due to the electric vehicle economy, necessitating more rare-earth elements for their production.
Applications of Different Magnet Types in Industry
Various kinds of attractors play a crucial role in diverse industries, each serving specialized applications. Neodymium components, recognized for their exceptional strength and compact size, illustrate what elements are often used in magnets, as they are widely employed in electric motors, wind turbines, and magnetic resonance imaging (MRI) machines. Their high energy density makes them particularly suitable for scenarios where space is at a premium.
As the neodymium market is projected to experience a compound annual growth rate (CAGR) of 7.7%, with volume increasing from 35.4 kilotons in 2022 to 64.6 kilotons by 2030, the demand for such powerful materials continues to rise. Notably, in the medical field, neodymium components are integral to advanced MRI technology, exemplifying their critical industrial applications. They are also utilized in magnetic separators and actuators, highlighting their diverse industrial relevance.
Alnico materials excel in environments that require temperature stability and resistance to demagnetization, illustrating what elements are often used in magnets. They are frequently utilized in sensors, relays, and guitar pickups, where reliability and performance are paramount. For instance, in the music industry, alnico components are favored in guitar pickups for their tonal characteristics, contributing to the overall sound quality.
Ferrite materials, composed of iron oxide, are significant players in the market, especially when considering what elements are often used in magnets, due to their cost-effectiveness and adequate magnetic properties. These objects are commonly found in consumer electronics, toys, and fridge decorations.
By comprehending the uses and characteristics of these devices, procurement managers can strategically align their sourcing choices with industry needs, ensuring that the most appropriate materials are chosen for optimal performance across diverse uses. As Brian Moore, VP of NICCA USA, Inc., remarked, ‘The quality of research they have conducted for us has been excellent,’ highlighting the significance of informed sourcing in maximizing the potential of these devices. Furthermore, the neodymium market is segmented by application, end-use, and region, providing additional context for procurement managers regarding market dynamics.
Future Trends in Magnet Materials and Technology
The trajectory of magnetic substances and technology is set to undergo substantial transformation, driven by the escalating demand for energy-efficient solutions and the miniaturization of electronic devices. Enhanced magnetic technology in motors contributes to a significant reduction in the overall carbon footprint of vehicles, emphasizing the importance of energy-efficient innovations. Ongoing research is investigating alternative substances to rare earth elements, which could significantly reduce supply chain vulnerabilities.
Notably, advancements in 3D printing for producing magnetic components are gaining momentum, enabling the creation of customized geometries with enhanced performance characteristics. As industries increasingly prioritize sustainability, the recycling of these items and the innovation of eco-friendly materials have emerged as critical areas of focus. As one expert noted, ‘Facing supplier shortages?
Here’s how to negotiate for faster deliveries and maintain your inventory levels, including building supplier rapport and offering flexibility.’
Procurement managers must remain vigilant in monitoring these trends, as adapting strategies to incorporate these advancements will be essential for navigating the rapidly evolving magnet technology landscape. By understanding these shifts, they can better position their organizations to leverage new opportunities while mitigating potential risks associated with supplier shortages and market fluctuations.
A pertinent case study on building trust during private equity exit strategies highlights that regular communication and transparency about risks can significantly enhance stakeholder confidence, a lesson that resonates within supply chain management.
Conclusion
Magnets are undeniably integral to the modern manufacturing and technology landscape, with their diverse applications spanning various industries. Understanding magnet composition, particularly the roles of ferromagnetic materials like iron, cobalt, and nickel, alongside the unique properties of neodymium and Alnico magnets, is crucial for procurement managers aiming to optimize their sourcing strategies. The challenges associated with rare earth element supply chains, particularly in the context of neodymium and dysprosium, further complicate the procurement landscape but also highlight the importance of strategic planning in navigating these complexities.
The applications of different magnet types underscore their significance in driving innovation across sectors. Neodymium magnets, with their exceptional strength and compact size, are pivotal in electric vehicles, medical imaging, and renewable energy technologies. In contrast, Alnico magnets provide reliability in high-temperature environments, showcasing the need for tailored material selection based on specific application requirements. As the market for permanent magnets is projected to grow substantially, understanding these dynamics will empower procurement managers to make informed decisions that align with industry demands.
Looking ahead, the evolution of magnet materials and technology is poised to reshape the industry landscape. The drive for energy-efficient solutions and sustainable practices is fostering innovations such as 3D printing and alternative materials to rare earth elements. By staying abreast of these trends and adapting procurement strategies accordingly, professionals can position their organizations for success in an increasingly competitive and dynamic market. Ultimately, a strategic approach to magnet sourcing not only enhances operational efficiency but also contributes to the broader goals of sustainability and innovation in technology.