Blogs
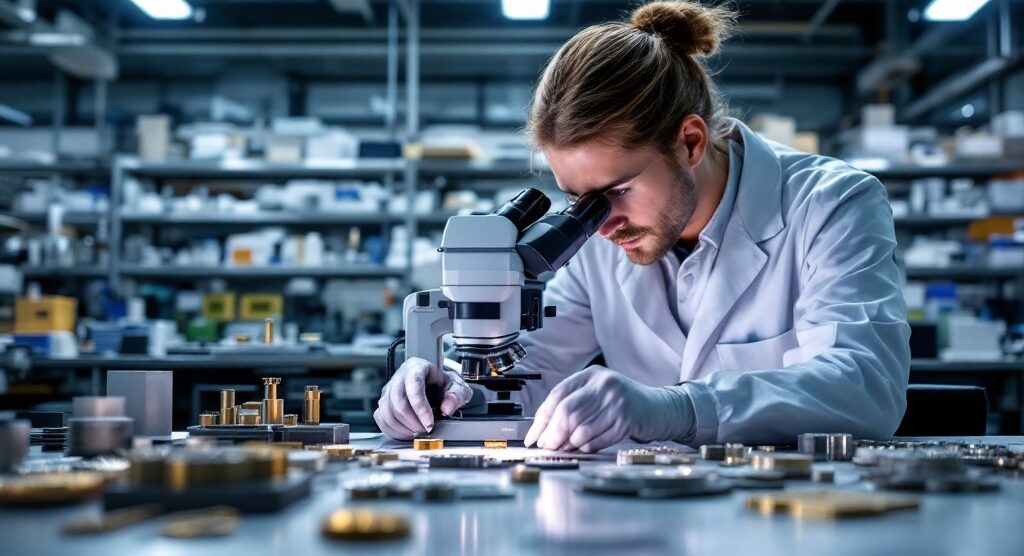
What Is the Strongest Titanium Alloy? A Deep Dive into Its Properties and Applications
Introduction
The significance of titanium alloys in modern engineering cannot be overstated. Renowned for their exceptional strength-to-weight ratio and remarkable corrosion resistance, these materials are integral across a multitude of industries, from aerospace to biomedical applications. Understanding the intricate properties and strength factors of titanium alloys is crucial for professionals tasked with material selection, as the performance of these alloys is heavily influenced by their microstructure and the presence of specific alloying elements.
As the demand for advanced materials continues to rise, particularly in high-performance sectors, a comprehensive analysis of both current and emerging titanium alloys reveals not only their versatility but also their potential to drive innovation.
This article delves into the key characteristics, applications, and future trends of titanium alloys, providing valuable insights for procurement managers and industry experts alike.
Understanding Titanium Alloys: Key Properties and Strength Factors
Titanium mixtures are celebrated for their remarkable strength-to-weight ratio, corrosion resistance, and stability under high temperatures. The main elements affecting the durability of these mixtures include their microstructure, which is greatly impacted by heat treatment and the incorporation of additional materials. For example, Ti-6%Al-4%V, a commonly used metal mixture, includes aluminum and vanadium to improve its mechanical characteristics while maintaining a lightweight structure.
Recent advancements in metal composite heat treatment have shown that optimizing these processes can lead to enhanced toughness, even as strength levels rise. Furthermore, current research underscores the critical role of alloying elements—like aluminum, vanadium, and molybdenum—in maximizing titanium’s performance. Significantly, Ti-6%Al-2%Sn-4%Zr-6%Mo features a thermal conductivity of 7.1 W/m·K, whereas Ti-6%Al-3%Sn-4%Zr-0.5%Mo-0.5%Si Ti 1100 has a density of 4.50 g/cm³, demonstrating the varied uses enabled through meticulous material selection.
According to Arulraj P., if yield strength exceeds the specified range of 275-450 MPa (with testing showing a value of 485 MPa for Titanium Gr. 2 Plate), understanding the reasons behind this yield is crucial for material selection. Furthermore, a case study on the chemical makeup of metal mixtures emphasized the significance of maintaining uniformity and the lack of metal inclusions, especially for their efficacy in healthcare uses.
Comprehending these properties is essential for choosing the suitable titanium mixture when considering what is the strongest titanium alloy for specific applications, as they directly affect performance and durability.
Applications of Titanium Alloys: From Aerospace to Biomedical Uses
In discussions about what is the strongest titanium alloy, titanium mixtures are pivotal across various industries due to their exceptional strength-to-weight ratio and corrosion resistance. In the aerospace sector, alloys such as Ti-6Al-4V are integral to the construction of airframes and engine components, leading to inquiries about what is the strongest titanium alloy to minimize weight and enhance fuel efficiency. The aerospace industry witnessed a notable increase in demand, with 661 commercial aircraft delivered in 2022—a significant 8% rise from 2021, as noted by Airbus SE, which emphasized that the commercial aviation sector saw a significant rise in deliveries.
This growth emphasizes the critical role of this metal in meeting these expanding demands. The unique properties of aerospace metal not only facilitate advancements in aircraft design but also contribute to safety and performance improvements. Additionally, in the biomedical field, metal composites are preferred for their biocompatibility and strength, leading to the question of what is the strongest titanium alloy for use in implants and prosthetics.
Ti-6Al-4V is commonly utilized in surgical instruments and dental implants, raising the question of what is the strongest titanium alloy based on its versatility and reliability. Recent advancements in biomedical applications have demonstrated that metal mixtures represent a significant portion of the implant market, propelled by their capacity to integrate smoothly with human tissue. The market size for metal mixtures attained USD 15.92 billion in 2022, indicating their economic importance.
Furthermore, the automotive sector is progressively utilizing metal mixtures for high-performance parts that demand durability and lightweight features. The significance of these materials in promoting technological progress across various domains raises the question of what is the strongest titanium alloy, rendering them essential for both present and future uses.
Comparative Analysis of the Strongest Titanium Alloys
When evaluating what is the strongest titanium alloy, Ti-6Al-4V often stands out as a top choice due to its remarkable tensile durability and exceptional fatigue resistance. However, when discussing what is the strongest titanium alloy, alloys like Ti-5Al-2.5Sn and Ti-6-2-4-2 should not be disregarded, as they also demonstrate remarkable durability, especially in high-temperature conditions. Notably, Ti-6-2-4-2 is recognized for its superior creep resistance, leading to the inquiry of what is the strongest titanium alloy for aerospace components that must endure extreme conditions.
As Arulraj P. points out, if yield strength exceeds the specified range of 275-450 MPa for Titanium Gr. 2 Plate, it raises questions about the underlying reasons, which can be critical in material selection. For instance, Ti-6%Al-2%Sn-4%Zr-6%Mo boasts a thermal conductivity of 7.1 W/m·K and a beta transus of 932°C, further underscoring its suitability in demanding aerospace fields.
Furthermore, the protective oxide layers created by both this metal and aluminum enhance their corrosion resistance and durability, making them ideal candidates for various applications. Dynamic Metals offers no minimum order quantities and prides itself on customer service, which is vital for procurement managers seeking reliable suppliers. Moreover, the Jiga Supplier Quoting Process simplifies the procurement of metal mixtures, enabling users to effectively source materials while improving workflow efficiency.
The choice of a metal mixture is contingent upon the specific requirements of the project, including load-bearing capacity, environmental exposure, and manufacturing methodologies. Understanding these nuances is critical for procurement managers aiming to make strategic material choices that align with their project needs.
Future Trends in Titanium Alloy Development
The trajectory of metal composite development is on the brink of remarkable advancements, particularly driven by innovations in additive manufacturing and the exploration of novel material compositions. Ongoing studies focus on developing metal mixtures that not only improve fatigue resistance but also lower manufacturing expenses. For example, China’s vehicle output hit 26.09 million units in 2021, indicating a 3% rise from 2020, highlighting the increasing need for metal composites in the automotive sector.
In settings with explosive potential, the use of Non-Sparking Tools is essential, as developments in metal mixtures can greatly improve their efficiency. These tools provide a safe alternative for operations requiring non-sparking applications, particularly as the properties of Copper Titanium Alloy may offer improved performance in such scenarios. The burgeoning field of 3D printing is revolutionizing the manufacturing landscape, allowing for the fabrication of intricate geometries that traditional methods could not achieve.
As industries progressively pursue substances that are both lighter and stronger, the development of copper-based composites will be crucial in meeting these requirements. This dynamic landscape encourages ongoing research and collaboration within the materials science community, highlighting the significance of addressing unresolved inquiries regarding these substances. Furthermore, procurement managers can address unexpected expenses by reviewing spending, tapping into savings, and negotiating with vendors, ensuring that they stay within budget while leveraging the cost-effectiveness of new titanium alloy developments.
Conclusion
The exploration of titanium alloys reveals their unparalleled significance across multiple domains, primarily driven by their exceptional strength-to-weight ratio and corrosion resistance. From aerospace to biomedical applications, the versatility of titanium alloys like Ti-6Al-4V and Ti-6-2-4-2 showcases their ability to meet the rigorous demands of modern engineering. Understanding the influence of microstructure and alloying elements on their performance is essential for professionals engaged in material selection, ensuring that the right alloy is chosen for specific applications.
As industries continue to evolve, the applications of titanium alloys expand, reflecting their critical role in advancing technological innovations. The aerospace sector’s increasing reliance on these materials for aircraft construction and the biomedical field’s adoption of titanium for implants underscore the economic and functional importance of titanium alloys. Moreover, the comparative analysis of various titanium alloys highlights their unique strengths, paving the way for informed decision-making that aligns with project requirements.
Looking ahead, the future of titanium alloy development is poised for transformative changes, particularly through advancements in additive manufacturing and the exploration of new compositions. The ongoing research into enhancing fatigue resistance and reducing production costs will further solidify the role of titanium alloys in meeting the demands of diverse industries. For procurement managers, staying abreast of these trends will be crucial in leveraging the benefits of titanium alloys while ensuring strategic material choices that align with both performance needs and budgetary considerations.