Blogs
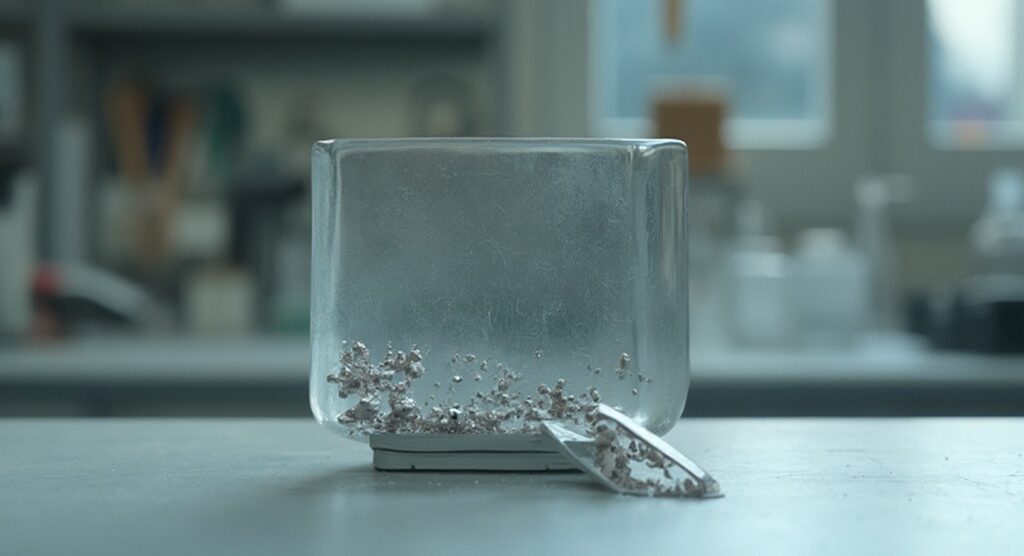
Advanced Applications and Properties of Pure Titanium Metal
Introduction
Titanium, with its chemical symbol Ti and atomic number 22, is renowned for its unique properties that make it indispensable across various industries. This article delves into the chemical and physical attributes of titanium, highlighting its low density, high strength, and exceptional resistance to corrosion. These qualities render it highly suitable for applications requiring high-temperature stability and durability, such as in aerospace, medical, automotive, and chemical processing sectors.
The exploration extends to titanium’s mechanical properties, illustrating its high tensile strength, durability, and ductility, which are enhanced through meticulously engineered alloys. Additionally, the article examines the diverse applications of titanium, from aircraft components to medical implants, and discusses recent advancements that further underscore its strategic importance. Despite its advantages, titanium faces limitations such as high costs and machining challenges, which are being addressed through innovative technologies like additive manufacturing.
The future developments in titanium applications promise to enhance its accessibility and performance, ensuring its vital role in modern industry and technology.
Chemical and Physical Properties of Titanium
Titanium, denoted by the symbol Ti and atomic number 22, is notable for its remarkable properties, including low density, great strength, and exceptional corrosion resistance. With a melting point of around 1,668 °C (3,034 °F), it is highly suitable for uses that demand high-temperature stability. Its physical characteristics feature a silver-gray metallic sheen and an excellent strength-to-weight ratio that exceeds that of steel.
Titanium’s notable biocompatibility makes it an ideal material for medical applications. For example, it is extensively used in artificial joints and dental implants due to its compatibility with the human body. Moreover, the metal’s resistance to rust and superior durability are beneficial in chemical processing facilities, heat exchangers, and valves.
In the aerospace sector, the low weight and high strength of this metal make it indispensable for aircraft, rocket, satellite, and engine components. This material also has uses in the automotive sector for high-performance vehicle components, as well as in sports gear like bicycle frames and golf clubs.
Recent advancements have further highlighted the advantages of this metal. For instance, the Ti-6Al-2Sn-4Zr-2Mo (Ti-6242) alloy is commonly used in high-temperature applications like turbine engines due to its excellent performance at elevated temperatures. Such alloys are used in thin sheets for aircraft skins and engine exhaust frameworks, demonstrating titanium’s versatility and reliability across various industries.
Mechanical Properties of Titanium
Titanium stands out with its remarkable mechanical properties, making it a prime choice in various industries. This metal shows significant tensile strength, often exceeding 1,400 MPa, and maintains its strength even at elevated temperatures. Its exceptional durability and resistance to fatigue ensure long-term reliability in structural applications. Furthermore, the metal’s high ductility enables it to be shaped into various forms effortlessly.
Moreover, metal alloys can be meticulously engineered to enhance specific mechanical properties. For example, the Ti6Al4V alloy, a blend of metal, aluminum, and vanadium, is commonly utilized because of its exceptional durability and adaptability. Titanium forging parts, produced through stringent manufacturing processes, offer superior mechanical properties and are crucial in industries such as aerospace, automotive, medical, and military.
Innovations in metal applications are continuously evolving. Significantly, studies and progress in alloy formulations are tackling both durability and deformability, resulting in items with ideal performance attributes. This ongoing development underscores the strategic importance of this metal in solving complex engineering challenges, as highlighted by recent studies and technological breakthroughs in the field.
Applications of Titanium
Titanium’s unique properties make it indispensable across various industries. In aerospace, metal mixtures are essential for creating airframes and engine components because of their light weight, high durability, and resistance to rust and elevated temperatures. This material’s significance is underscored by its extensive use in global aerospace production by companies like Boeing and Airbus. However, recent geopolitical disruptions have resulted in shortages of the metal, impacting aircraft manufacturing and maintenance schedules.
In the medical field, this metal’s biocompatibility and strength make it an ideal choice for implants and prosthetics. Sophisticated items, like Grade 5 metal alloy discs, are favored because of their outstanding characteristics, featuring an impressive strength-to-weight ratio and resistance to corrosion. This ensures that medical implants are durable and reliable, thus improving patient outcomes.
The chemical sector also gains considerably from this element, especially in the production of reactors and heat exchangers. Titanium’s resistance to corrosion and ability to withstand high temperatures ensure the longevity and efficiency of these critical components.
Furthermore, the automotive and sports equipment sectors utilize the lightweight and durable nature of this metal. High-strength metal forgings and components are increasingly used to enhance performance and fuel efficiency in vehicles, while sports equipment manufacturers utilize its properties to produce durable, high-performance gear.
Overall, the adoption of innovative technologies like 3D printing and advanced composite materials is being explored to mitigate supply chain challenges related to this vital material, ensuring its continued availability across industries.
Benefits of Using Titanium
Titanium stands out due to its exceptional high strength-to-weight ratio, superior corrosion resistance, and biocompatibility, making it indispensable for numerous demanding applications. Its remarkable resistance to various corrosive environments extends the lifespan of components, significantly reducing maintenance and replacement costs. For instance, metal alloys are extensively used in modern aircraft engines, including turbofan motors. These engines power the majority of the world’s most popular commercial aircraft, highlighting the essential role of this metal in producing key engine components such as the fan, compressor, combustion chamber, and turbine.
The lightweight quality of this metal contributes greatly to fuel efficiency in aerospace and automotive uses, enhancing overall performance. This is particularly crucial in the aerospace sector, where fuel efficiency directly impacts operational costs and environmental footprint. Furthermore, the metal’s capacity to endure extreme temperatures and stresses renders it perfect for high-performance environments, such as advanced manufacturing fields where innovative technologies like metal 3D printing are utilized to produce stronger and more efficient components.
Recent research published in the journal Advanced Materials revealed a lattice structure design that makes this metal 50% stronger than the next most robust alloy of similar density used in aerospace applications. This innovation, inspired by nature’s own design principles, demonstrates the ongoing advancements in manufacturing methods aimed at overcoming traditional limitations. These developments are crucial, especially given the current shortage of this metal caused by geopolitical factors and decreased production in key regions like Ukraine, which has led to a global production drop of approximately 12% over the last five years and subsequent price increases.
Such advancements emphasize the significance of this metal in contemporary technology and its essential function in preserving structural integrity while minimizing weight. As industries continue to innovate, this metal remains at the forefront, offering unparalleled strength and durability essential for future technological progress.
Limitations and Future Developments
Despite its numerous advantages, this metal faces certain limitations. Its high cost compared to other metals can hinder its broad adoption. Furthermore, machining this metal is challenging due to its hardness and toughness. These factors make it less attractive for some applications. However, recent advancements are changing this landscape. Additive manufacturing and improved alloy compositions are making this metal more cost-effective. For instance, companies are investing in 3D printing technologies that streamline production processes and reduce dependency on specialized labor. These innovations are not only cutting costs but also addressing supply chain issues exacerbated by geopolitical events, such as the war in Ukraine. This conflict has significantly disrupted the production of this metal, leading to shortages and increased prices, particularly in the aerospace sector. As a result, manufacturers are seeking alternative sources and adopting new technologies to mitigate these challenges. Future developments will likely focus on further enhancing titanium’s properties and making it more accessible for various applications, from aerospace to medical devices.
Conclusion
Titanium’s unique combination of properties—low density, high strength, and exceptional corrosion resistance—positions it as a crucial material across multiple industries. Its applications range from aerospace components, where lightweight and strength are paramount, to medical implants that benefit from its biocompatibility. The versatility of titanium alloys, such as Ti-6Al-4V, further enhances its appeal, providing tailored mechanical properties that meet the demands of various sectors.
However, the advantages of titanium are tempered by challenges, including high costs and machining difficulties. These limitations have prompted innovations in manufacturing techniques, particularly additive manufacturing, which aim to reduce production costs and improve accessibility. The ongoing geopolitical factors, particularly disruptions in titanium supply chains, underscore the need for strategic sourcing and technological advancements to ensure stable availability.
As industries continue to evolve, the strategic importance of titanium will only grow. Future developments are expected to focus on enhancing its properties and expanding its applications, thereby reinforcing its role as an essential material in modern technology. The commitment to overcoming existing challenges will ensure that titanium remains at the forefront of engineering solutions, driving advancements in performance and sustainability across various sectors.