Blogs
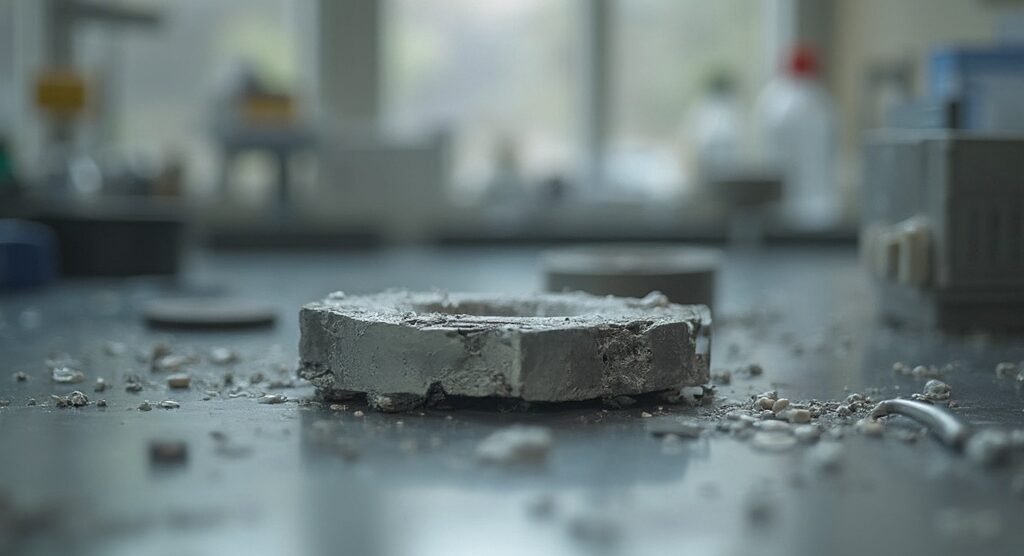
An In-Depth Study of 718 Alloy: Properties and Industrial Uses
Introduction
In the demanding realms of aerospace, automotive, and other high-performance industries, selecting the right materials is crucial for ensuring durability and efficiency. One such material that has proven indispensable is the 718 alloy. Known for its remarkable strength, heat resistance, and corrosion resistance, the 718 alloy stands out as a superior choice for components subjected to extreme conditions.
This article delves into the chemical composition, physical and mechanical properties, heat treatment processes, and diverse applications of this versatile alloy. By understanding the intrinsic qualities and industrial benefits of the 718 alloy, procurement managers can make informed decisions to enhance their operations and maintain a competitive edge in their respective fields.
Chemical Composition of 718 Alloy
The 718 mixture, known for its robust composition, primarily consists of nickel (50-55%), chromium (17-21%), and iron (up to 19%). These elements are strategically combined with molybdenum (2.8-3.3%) and niobium (4.75-5.5%), which significantly enhance the material’s strength and resistance to oxidation and corrosion. This unique composition makes the 718 mixture an ideal candidate for high-performance applications in extreme environments such as aerospace and automotive industries, where materials are pushed to their limits.
Moreover, the inclusion of trace elements like titanium and aluminum further bolsters its mechanical properties, ensuring durability and reliability under severe conditions. The 718 metal’s capacity to preserve excellent mechanical characteristics over a broad range of heat levels overcomes the challenges encountered by conventional metals, which frequently experience brittleness in cold conditions or insufficient performance in hot conditions. This makes it an indispensable material for advanced industrial applications where both strength and resilience are paramount.
Physical and Mechanical Properties of 718 Alloy
‘Famous for its outstanding performance, the 718 material stands out because of its extraordinary tensile strength and yield strength, frequently surpassing 1,200 MPa at ambient conditions.’. The remarkable ductility of this metal enables simple shaping and joining, rendering it adaptable for numerous industrial uses. The 718 metal retains its mechanical properties even at high temperatures, with an operational range extending up to 1300°F (704°C). This heat resistance is crucial for industries that operate in extreme environments, such as aerospace and petrochemical sectors.
Moreover, the 718 mixture exhibits low thermal expansion and excellent fatigue resistance, essential for demanding conditions. These properties ensure reliability and longevity, reducing the risk of component failure under cyclical loading. The metal’s adaptability to high-pressure and high-stress environments makes it invaluable in advanced air mobility and other cutting-edge applications. As emphasized in recent industry reports, the need for materials that can endure extreme conditions and pressures is essential for the future of efficient and sustainable manufacturing processes.
The mixture’s capability to sustain elevated strength and flexibility across a broad thermal spectrum creates opportunities for its application in contemporary sectors such as aviation and cryogenic marine activities. Systematic characterizations have demonstrated that mixtures such as 718 can maintain a significant yield strength and good ductility even at temperatures reaching 1000°C. This makes it an excellent choice for applications requiring both high performance and durability.
Heat Treatment of 718 Alloy
The heat treatment of the 718 metal involves a two-step process: solution treatment and aging. The solution treatment is conducted at approximately 1800°F (982°C), which dissolves the gamma prime precipitates. This is followed by rapid cooling to retain the solutionized structure. Next, the mixture undergoes an aging process at around 1325°F (718°C) for several hours. This step is critical as it enhances the strength of the mixture through the formation of gamma double prime precipitates. This careful heat treatment procedure is crucial to enhance the mechanical characteristics of the 718 metal, rendering it appropriate for challenging industrial uses such as aerospace and automotive sectors, where substances must withstand intense heat and pressures.
Applications of 718 Alloy
The 718 metal, renowned for its exceptional mechanical properties and resilience under extreme conditions, is a cornerstone in various industrial applications. In the aerospace sector, it plays a critical role in the fabrication of over 50% of advanced aircraft engine components, including gas turbine engines, seals, and combustion chambers. ‘These components must endure heat levels rising to 1090°C in high-performance areas, yet the metal retains its integrity up to 650°C, thanks to its strong microstructure consisting of multiple phases like γ-matrix, γ′, and δ-phase.’.
Beyond aerospace, the metal’s exceptional resistance to corrosion and surface degradation makes it essential in oil and gas exploration, where severe environments require materials that can withstand. Its application extends to nuclear reactors, whereby its stability under radiation and elevated temperatures ensures safe and efficient operation. Furthermore, the medical field gains from the metal’s biocompatibility and durability, especially in devices that require both strength and resistance to bodily fluids.
The increasing complexity and cost of cooling techniques in turbine blades highlight the need for advanced manufacturing methods such as additive manufacturing (AM). IN718’s high weldability and compatibility with AM processes like laser powder bed fusion (LPBF) offer promising alternatives to traditional fabrication, potentially overcoming challenges related to machinability and geometric complexity. This adaptability highlights the mixture’s versatility and ongoing significance across various high-stakes industries.
Industrial Uses of 718 Alloy
‘718 metal is renowned for its ability to maintain exceptional performance under extreme conditions, making it indispensable across multiple high-stress industries.’. In the aerospace sector, it is integral in the fabrication of turbine blades, spacers, and structural components, all of which demand high strength and resistance to heat. The oil and gas sector depends on 718 metal for essential downhole tubing and valves, where its durability and resistance to corrosion are vital. Furthermore, the healthcare sector gains from the material’s biocompatibility and strength, employing it in the production of surgical tools and implants. This versatility highlights the material’s pivotal role in advancing technology across diverse fields.
Benefits of Using 718 Alloy in Various Industries
The extensive use of 718 material in different sectors is mainly because of its outstanding characteristics. Its high strength-to-weight ratio significantly reduces the weight of components, which is crucial for enhancing fuel efficiency in aerospace applications. This advantage corresponds with the discoveries of Dale Hopkins from NASA, who observed that such materials can contribute to more sustainable aviation by reducing operating costs and enhancing overall fuel efficiency. Furthermore, the mixture’s resistance to oxidation and corrosion not only prolongs the service life of products but also reduces maintenance expenses and improves safety. This is particularly relevant as industries like nuclear power and fossil fuel power stations increasingly rely on such materials for their durability and performance under extreme conditions. Moreover, the properties of 718 material to sustain its performance under elevated temperatures render it an excellent option for essential applications. This characteristic is vital for sectors that demand high reliability and efficiency, such as aerospace and power generation, where materials are subjected to extreme operational environments. These advantages together promote the use of 718 composition, making it a favored material across various industries.
Corrosion Resistance and High-Temperature Applications
The 718 metal stands out due to its exceptional resistance to pitting and stress corrosion cracking, making it indispensable for applications in harsh environments. Its strong performance in elevated conditions is further improved by its oxidation resistance, ensuring both integrity and reliability. This makes the metal mixture an ideal choice for critical components in engines and systems operating under extreme thermal conditions. Notably, the alloy’s ability to maintain structural integrity under such conditions is crucial for advanced industries like aerospace and nuclear power, where material performance at varying temperatures can be a matter of safety and efficiency.
Conclusion
The 718 alloy has emerged as a pivotal material in high-performance industries, notably aerospace and automotive, due to its exceptional chemical composition and mechanical properties. With a robust blend of nickel, chromium, and strategic trace elements, this alloy offers unparalleled strength, heat resistance, and corrosion resistance, making it an optimal choice for components operating under extreme conditions. Its ability to maintain superior mechanical properties across a wide temperature range further distinguishes it from traditional alloys, ensuring reliability and durability where it matters most.
The meticulous heat treatment process of the 718 alloy enhances its mechanical properties, enabling it to withstand the rigors of demanding applications. This process not only optimizes the alloy’s performance but also aligns with the increasing complexity and requirements of modern industrial applications. From aerospace engine components that endure extreme temperatures to critical oil and gas exploration tools, the versatility of the 718 alloy is evident across various sectors.
Moreover, the benefits of using the 718 alloy extend beyond its mechanical properties. Its high strength-to-weight ratio contributes to improved fuel efficiency, particularly in aerospace applications, while its resistance to oxidation and corrosion translates into reduced maintenance costs and enhanced safety. As industries continue to prioritize sustainability and efficiency, the 718 alloy’s role in advancing technology and performance in high-stakes environments remains indispensable.
In summary, the 718 alloy represents a strategic asset for procurement managers seeking to enhance operational efficiency and maintain a competitive edge in their respective fields. Understanding its intrinsic qualities and diverse applications is essential for informed decision-making, ensuring that organizations are equipped to meet the challenges of modern manufacturing and technological advancement.