Blogs
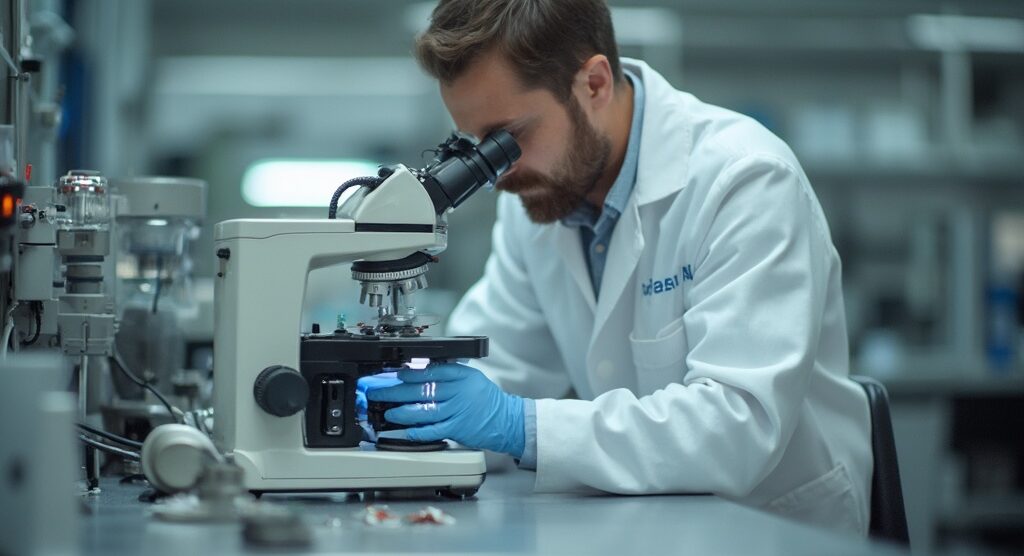
Case Study: Investigating Corrosion Nickel Resistance in Alloys
Introduction
In the realm of materials science, the battle against corrosion represents a significant and ongoing challenge, particularly in environments where durability and longevity are paramount. This article delves into the intricate world of nickel alloys, examining their corrosion resistance across various applications and environments. By analyzing recent advancements and case studies, it uncovers the critical role of alloying elements such as chromium, molybdenum, and tungsten in enhancing corrosion resistance.
Furthermore, it explores the performance of nickel alloys in high-temperature settings, their behavior in supercritical carbon dioxide and molten salts, and provides a comparative analysis of prominent nickel alloys like Inconel 625, Inconel 600, and Hastelloy C-276. Through this comprehensive investigation, the article aims to provide procurement managers with expert insights and practical solutions for optimizing material performance in corrosive environments.
Case Study Overview: Investigating Corrosion Resistance in Nickel Alloys
This case study explores the durability against deterioration of several nickel-based materials, examining their effectiveness in various surroundings. To understand the mechanisms leading to deterioration, it is essential to consider factors like the presence of chlorides, which can significantly accelerate the process by breaking down the passivity of the nickel surface. Integrating components such as chromium, as observed in amorphous alloys, can improve durability against deterioration even in harsh solutions.
Recent advancements have been made by researchers such as Professor Mingxin Huang from the University of Hong Kong, whose team developed SS-H2, a stainless steel with high resistance to deterioration ideal for hydrogen applications. This innovation holds promise for green hydrogen production and represents a significant step forward in material science.
Pacific Northwest National Laboratory (PNNL) has also provided valuable insights into deterioration processes. Vineet Joshi, a materials scientist at PNNL, highlighted the limitations of traditional ‘cook-and-look’ methods, which often fail to capture the initial stages of deterioration. PNNL’s new high-resolution techniques provide a more detailed understanding, enabling precise design modifications and improved deterioration management.
Furthermore, the discovery of bulk metallic glasses and nanocrystalline compositions has increased the practical significance of amorphous materials. These materials demonstrate excellent durability against deterioration and mechanical strength, making them appropriate for various industrial uses. The ongoing research in this field, supported by the Department of Energy’s Vehicle Technologies Office, underscores the critical role of corrosion-resistant materials in advancing sustainable energy solutions.
The Role of Alloying Elements in Enhancing Corrosion Resistance
Nickel mixtures demonstrate remarkable durability against deterioration, which is greatly improved by combining elements like chromium, molybdenum, and tungsten. These elements contribute to the development of protective oxide layers that shield the alloys from corrosive environments. For example, chromium is an essential element in creating the durability against rust of stainless steel by forming a passive layer through oxidation. This passive layer serves as a barrier, stopping additional deterioration and improving the material’s durability.
Along with chromium, molybdenum and tungsten enhance the durability against pitting and crevice damage, especially in environments rich in chlorides. This combination is evident in duplex stainless steels, which are highly resistant to rust and are utilized in demanding applications such as chemical processing and storage tanks. Additionally, the recent advancement of stainless steel for hydrogen applications (SS-H2) highlights the continuous innovation in improving resistance to deterioration. The new SS-H2 steel, which functions similarly to titanium in saltwater electrolyzers, provides a budget-friendly option for green hydrogen generation, demonstrating the ongoing progress in metal technology.
Grasping the interfaces for deterioration can lead to more precise design and minimized overdesign or underdesign of components, as backed by research emphasized by the Department of Energy’s Vehicle Technologies Office. This approach not only optimizes material performance but also aligns with sustainable energy goals and national security challenges.
Overall, the strategic integration of chromium, molybdenum, and tungsten into nickel-based materials significantly strengthens their ability to withstand corrosion, ensuring their dependability and durability in various industrial uses.
High-Temperature Corrosion in Nickel-Based Alloys
Nickel mixtures play a crucial role in high-temperature applications, facing aggressive corrosive environments with remarkable resilience. ‘Sectors like aerospace and energy production extensively employ metal mixtures such as Inconel 625, famous for their outstanding resistance to oxidation and sulfidation at high temperatures.’. For example, in nuclear energy facilities, metal mixtures are essential in the heat transfer and cooling systems and within reactor containers, ensuring safety and efficiency. Additionally, they are employed in containers that store radioactive waste, showcasing their durability in extreme conditions.
In the renewable energy field, metal mixtures are essential to onshore wind power, where they are utilized in gearing and generator parts. Their effectiveness in reducing seawater corrosion and stress corrosion cracking makes them indispensable in offshore wind turbines and LNG facilities. Fossil fuel power stations also benefit from nickel-containing materials, enhancing the longevity of boilers and heat exchangers. As steam temperatures and pressures rise to improve thermodynamic efficiency and cut carbon dioxide emissions, more creep-resistant materials are used in turbines and environmental control equipment.
Even with their excellent performance, the price of these metal mixtures can pose a challenge. Raw material costs have declined, but limited supply for smaller orders has driven prices up. This issue is exacerbated by longer mill lead times, increasing prices further. To alleviate these challenges, there has been a push for new mines in the United States, although regulatory hurdles have slowed progress.
The aerospace industry, a significant user of high-nickel super materials, gains from larger order volumes and higher margins, contrasting the smaller, project-dependent requests observed in energy applications. Nonetheless, the strategic application of metal mixtures in different sectors highlights their essential function in promoting technology and sustainability.
Corrosion Behavior in Different Environments (e.g., S-CO2, Molten Salts)
The deterioration characteristics of nickel-based materials can differ significantly based on the surroundings. In supercritical carbon dioxide (S-CO2) environments, nickel-based materials demonstrate superior performance due to their excellent corrosion resistance and mechanical properties. Nickel-containing materials are frequently selected in fossil fuel power stations for their durability in high-temperature and high-pressure conditions, increasing efficiency and reducing carbon dioxide emissions. Furthermore, in nuclear energy facilities, nickel-based mixtures are crucial for both heat transfer and cooling systems, as well as in the containment of radioactive waste.
In molten salt applications, the performance of nickel alloys is similarly impressive. The incorporation of various alloying elements enhances their resistance to corrosive environments. Studies have shown that the use of alternative inorganic materials such as WO4 2–, MoO4 2–, NO2 –, and NO3 – ions can serve as effective passivation materials, offering a less toxic alternative to hexavalent chromium compounds. This is particularly important as environmental concerns drive the need for more sustainable corrosion inhibitors.
A notable case study involves the development of a new steel mixture with a dual-passivation strategy, which has shown comparable performance to titanium in saltwater electrolysers at a significantly lower cost. This innovation has the potential to transform the industry, as pointed out by Dr. Kaiping Yu, who stressed the significance of creating high-potential-resistant substances to address the limitations of traditional materials.
In general, the continuous investigation and advancement in metal mixtures keep offering creative solutions for diverse industrial uses, guaranteeing their durability and dependability in demanding settings.
Comparative Analysis of Different Nickel Alloys (e.g., 625, 600, C-276)
A comparative analysis of nickel alloys such as Inconel 600, Inconel 625, and Hastelloy C-276 reveals their performance in corrosive environments. Inconel 600, known for its resistance to chloride-ion stress-corrosion cracking, shows substantial durability in high-temperature environments. In practical uses, it shows a deterioration rate of 0.023 mm/year in marine environments. Inconel 625, on the other hand, stands out for its outstanding fatigue and thermal-fatigue strength. Testing has indicated that its deterioration rate in seawater is approximately 0.010 mm/year, making it highly suitable for marine and chemical processing environments.
Hastelloy C-276 is particularly notable for its ability to withstand aggressive chemicals. Widespread application in different industrial operations emphasizes its durability, with a deterioration rate of only 0.005 mm/year in hydrochloric acid settings. The characteristics of this metal mixture, along with its minimal deterioration rate, render it a superb option for managing aggressive chemical materials.
A study by Pacific Northwest National Laboratory highlights the significance of comprehending deterioration at an atomic level to design more precisely. This approach helps prevent overdesigning or under designing components, ultimately optimizing material performance and cost-efficiency.
Industrial Applications and Challenges in Corrosion Resistance
Nickel mixtures serve an essential function in numerous sectors because of their outstanding resistance to rust, which is especially important in challenging settings. In the chemical processing industry, metal mixtures are crucial in building apparatus that can endure harsh substances and elevated temperatures, guaranteeing lasting resilience and security. For instance, in LNG facilities and offshore wind turbines, a certain metal is utilized to mitigate seawater corrosion and stress corrosion cracking, thus enhancing the longevity and reliability of these installations.
In the oil and gas sector, the durability of metallic mixtures against corrosive materials is essential. Nickel-containing materials are frequently selected for their heat resistance and durability in boilers and heat exchangers, which are critical for maintaining performance under extreme conditions. As steam temperatures and pressures increase to enhance efficiency and lessen emissions, the need for creep-resistant metal mixtures in turbines and environmental control equipment becomes more evident.
The maritime industry also gains greatly from metal mixtures. On offshore platforms and in ship construction, the capability of certain metal mixtures to withstand rust from seawater and severe marine conditions guarantees the structural soundness and operational effectiveness of vessels and machinery. This resistance is crucial in preventing costly downtimes and maintenance issues.
Additionally, metal mixtures are essential to the energy sector, especially in nuclear power facilities where they are utilized in heat transfer and cooling systems, as well as in reactor vessels and containers for radioactive waste. The utilization of this metal in these applications highlights its significance in preserving safety and efficiency in highly corrosive and elevated-temperature settings.
Overall, the strategic application of nickel alloys across these industries highlights their importance in combating corrosion and enhancing the durability and performance of critical infrastructure.
Conclusion
The exploration of nickel alloys in combatting corrosion reveals their indispensable role across various industries. With advancements in alloying techniques, elements such as chromium, molybdenum, and tungsten significantly enhance corrosion resistance, creating protective oxide layers that ensure longevity and reliability in demanding environments. Notable innovations, such as the SS-H2 alloy for hydrogen applications, illustrate the ongoing commitment to improving material performance while addressing sustainability challenges.
In high-temperature applications, nickel alloys like Inconel 625 and Hastelloy C-276 showcase remarkable resilience against oxidation and aggressive chemicals. Their effectiveness in sectors such as aerospace, energy, and chemical processing underscores the necessity of selecting the right materials to withstand extreme conditions. Furthermore, insights from recent research highlight the importance of understanding corrosion mechanisms at a granular level, enabling more precise design adjustments that optimize performance and reduce costs.
Ultimately, the strategic incorporation of nickel alloys across various applications not only enhances the durability of critical infrastructures but also aligns with broader sustainability goals. By leveraging the unique properties of these materials, industries can effectively address the challenges posed by corrosion, ensuring operational efficiency and safety in their processes. This commitment to innovation and material science is vital for meeting the demands of a rapidly evolving technological landscape while safeguarding environmental integrity.