Blogs
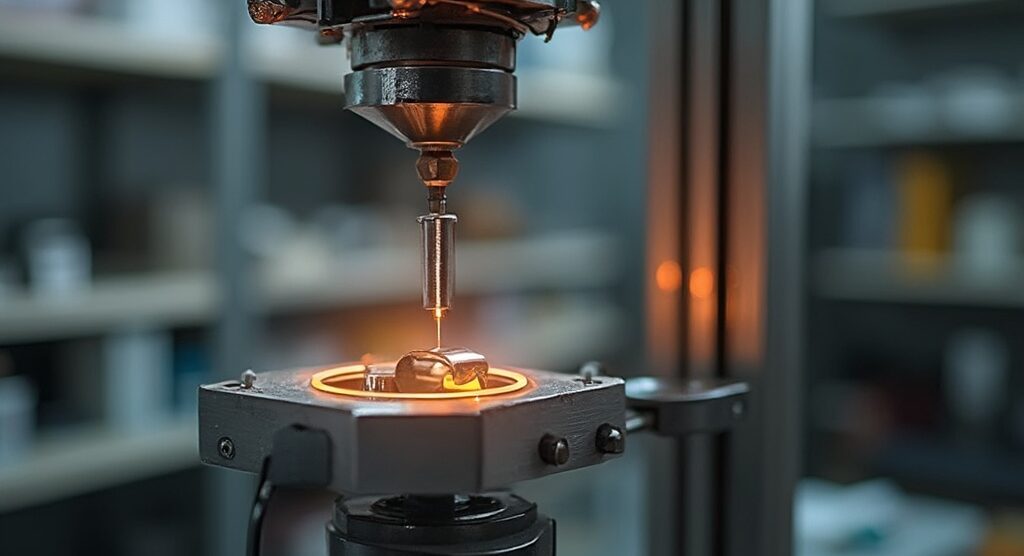
Evaluating the Copper Tensile Strength: Methods and Implications
Introduction
Copper, a material renowned for its versatility and conductivity, finds extensive use across various industries. However, its tensile strength—a critical factor determining its performance under mechanical stress—can be influenced by numerous elements. This article delves into the key factors affecting copper’s tensile strength, exploring how alloy composition, microstructural characteristics, and processing techniques converge to enhance or compromise its mechanical properties.
By understanding these influences, professionals can optimize the use of copper in applications requiring exceptional durability and reliability.
Factors Affecting Copper Tensile Strength
The tensile durability of this metal is notably affected by several elements, such as its alloy makeup, microstructure, and fabrication techniques. The inclusion of alloying elements like zinc or tin can significantly improve its durability. For instance, zinc is often added to improve mechanical properties due to its ability to form solid solutions with copper, while tin contributes to better corrosion resistance and overall structural integrity.
Microstructure plays a crucial role, with grain size being a primary factor in durability. Processes such as annealing or cold working alter the grain structure, impacting the material’s performance. According to the Hall-Petch relationship, copper and its alloys display enhanced durability with decreased grain size down to a certain threshold. However, as the grain size diminishes below 500-1000 nm, further strengthening occurs due to enhanced dislocation contributions. Conversely, when the grain size drops below 70-150 nm, the durability decreases again due to thermally-activated phenomena and reduced dislocation activity.
Processing methods like annealing and cold working are instrumental in defining the grain structure and, consequently, the mechanical properties. Annealing can refine the grain size and relieve internal stresses, enhancing durability. Cold processing, conversely, can lead to work hardening, which greatly enhances pulling power.
The purity of copper is another critical factor. Impurities can negatively influence the ability to withstand force by creating weak points within the metal structure. Therefore, maintaining high purity levels is essential to achieve optimal mechanical properties. Research has indicated that the presence of elements like magnesium or aluminum in small amounts can stabilize grain boundaries and enhance durability, but excessive impurities can result in harmful effects.
In summary, the stretching capacity of the metal is a complex interplay of alloy composition, microstructural characteristics, and processing techniques. Understanding and controlling these factors can lead to significant improvements in the performance and reliability of copper-based materials.
Methods for Evaluating Copper Tensile Strength
Standardized testing methods such as ASTM E8 and ISO 6892 are essential in assessing the pulling force of copper. These procedures involve preparing a specimen for a uniaxial stretching test, where a controlled load is applied until the specimen fails. This procedure produces important measurements, including yield resistance, ultimate stretch resistance, and elongation at fracture, which are vital for comprehending the substance’s performance under pressure.
Dr. Paul Griffiths, a senior lecturer in applied mathematics, emphasizes the significance of these metrics in ensuring that substances can endure operational stresses in various applications. For example, stretching strength and yield strength specifically assess the durability and load-bearing capacity, ensuring the substance’s reliability. These evaluations are vital in sectors like automotive and aerospace, where substances must preserve integrity under extreme conditions.
Moreover, the creation of cutting-edge testing techniques, such as the application of Michelson type optical interferometers for assessing dynamic attributes under impact stretching, illustrates the continuous progress in this area. These methods provide precise data that enhance the reliability of substances used in critical applications.
Overall, standardized strength testing methods are essential for evaluating the mechanical properties of copper and ensuring its appropriateness for demanding engineering applications.
Tensile Testing: Principles and Procedures
Tensile testing is an essential procedure in materials science to evaluate how materials behave under tension. The process begins by meticulously preparing a test specimen, which is then secured in a testing machine equipped with grips. This machine applies a consistent stretching force while measuring the resulting elongation. The data gathered is plotted on a stress-strain curve, revealing critical mechanical properties such as yield limit, ultimate tensile capacity, and elongation at break.
High-entropy alloys (HEAs), for instance, are materials made by combining several elemental metals. These alloys, known for their potential in extreme conditions, have shown significant improvements in strength and ductility through advanced testing methods. Researchers have utilized techniques like neutron and X-ray scattering to understand these enhancements, crucial for applications in industries where durability and resistance to fracturing are paramount.
Additionally, the integration of AI and ML in tensile testing is revolutionizing the field by processing vast datasets and identifying complex patterns. This advancement improves the accuracy and efficiency of testing, ensuring that products can withstand the rigorous demands of their intended applications. For example, AI algorithms can analyze the extensive data generated during testing, providing precise predictions and insights into substance behavior under stress.
Understanding Tensile Test Results: Strength and Elongation
Analyzing the results of a stretching test requires a thorough examination of both resilience and elongation metrics. The ultimate tensile resistance (UTR) indicates the maximum stress a substance can endure before failure, which is essential for ensuring the substance’s durability and load-bearing capability. On the other hand, yield strength indicates the stress level at which a substance starts to deform permanently, a key metric for assessing its capacity to uphold structural integrity under operational stresses.
Elongation, represented as a percentage, assesses the substance’s ductility by showing how much it can stretch before breaking. This property is fundamental for applications where flexibility and stretchability are critical. For instance, in the automotive industry, substances with high elongation are preferred for components that must withstand deformation without breaking.
Grasping these stress test outcomes is crucial for uses demanding specific performance standards. For example, in the production of electrical components, the surface finish and mechanical properties directly impact electrical conductivity and reliability. Likewise, in structural uses, high resistance to stretching and yield strengths guarantee that the substances can endure mechanical loads and environmental factors for extended durations, thereby improving the product’s longevity.
To illustrate, a study on the use of sisal fiber composites in vehicle body applications demonstrated that different fiber orientations significantly improved mechanical properties, offering a lightweight and durable substitute to conventional substances. This emphasizes the significance of thorough strength testing to confirm material performance for particular industrial uses.
Implications of Copper Tensile Strength in Various Applications
The stretching capability of the metal is vital in multiple industries, especially in the growing North American data center market. With the market anticipated to expand from $33 billion in 2020 to $70 billion by 2030, and $185 billion by 2040, the demand for this metal is set to increase significantly. Copper consumption in data centers is expected to rise from 197,000 tonnes in 2020 to 238,000 tonnes in 2030, reaching 293,000 tonnes by 2040.
This demand arises from the unique characteristics of the metal, including high tensile strength, which enables the creation of thinner, yet sturdy electrical wires crucial for effective data transmission. For instance, Microsoft’s $500 million data center in Chicago utilized 2,177 tons of a reddish-brown metal. The material’s thermal conductivity also facilitates the creation of efficient heat exchangers, critical for cooling systems in data centers.
Furthermore, this metal’s ductility and malleability make it ideal for manufacturing compact system components like electrical connectors, ensuring they can endure operational stresses without compromising performance. This is especially important in the electronics industry, where the dependability and durability of connectors and circuit boards rely on the strength characteristics of the metal.
Integrating this metal into design processes not only bolsters structural integrity but also aligns with the expanding green economy, as it can be completely recycled without losing its advantageous properties. Thus, engineers must consider the tensile strength of copper to enhance the durability and efficiency of their designs, whether in electrical, structural, or electronic applications.
Conclusion
Copper’s tensile strength is shaped by several key factors, including alloy composition, microstructure, and processing techniques. The incorporation of alloying elements such as zinc and tin enhances mechanical properties, while grain size plays a crucial role in determining strength. Processing methods like annealing and cold working refine the grain structure, contributing to improved durability.
Maintaining high purity levels is essential, as impurities can create weak points that compromise tensile strength.
Standardized testing methods, such as ASTM E8 and ISO 6892, are vital for assessing copper’s performance under stress. These tests provide critical metrics like yield strength, ultimate tensile strength, and elongation, ensuring reliability in demanding applications across industries like automotive and aerospace. Advanced testing techniques, including AI and ML, further enhance the accuracy of tensile testing, enabling better predictions of material behavior.
In the growing data center market, the implications of copper’s tensile strength are increasingly significant. Rising demand for copper underscores its ability to produce thinner, robust electrical wires and efficient heat exchangers, essential for effective data transmission and cooling systems. By strategically focusing on copper’s tensile properties, improvements in durability and efficiency can be achieved across various applications, from electrical components to structural designs.
This understanding not only supports product longevity but also aligns with sustainability goals, emphasizing copper’s critical role in modern engineering practices.