Blogs
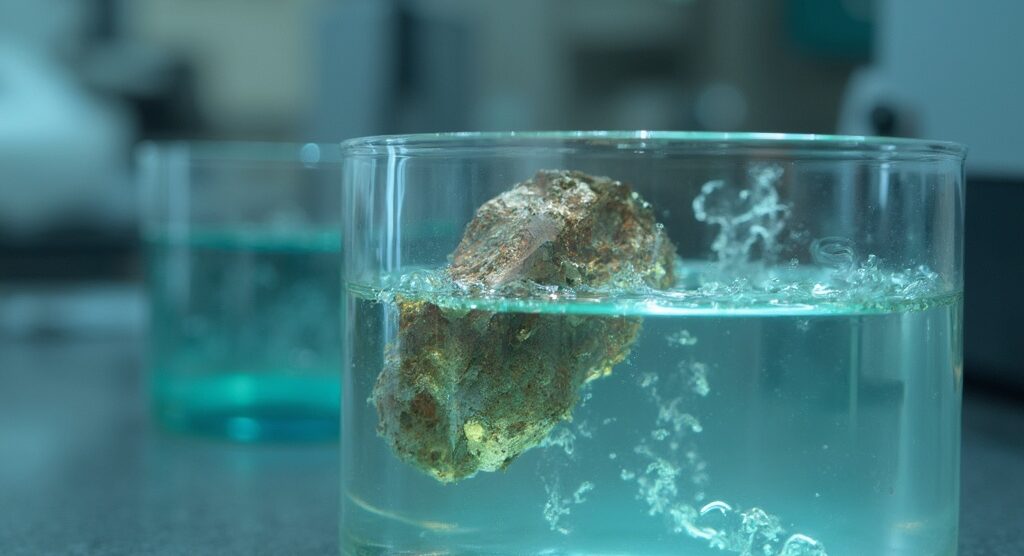
Exploring the Industrial Applications of Alloy Copper and Nickel Metals
Introduction
Copper-nickel alloys are a cornerstone in both marine and non-marine applications, owing to their unique blend of mechanical properties, corrosion resistance, and thermal stability. These alloys are particularly celebrated in industries that demand durability and minimal maintenance, such as shipbuilding, offshore oil rigs, and desalination plants. Their ability to withstand harsh marine environments, coupled with their biofouling resistance, positions them as an indispensable material in naval and commercial shipping, offshore wind farms, and power generation.
Beyond the marine sphere, their antimicrobial properties find utility in coinage, while their strength and thermal resistance are invaluable in the automotive and cryogenic sectors. This exploration delves into the multifaceted advantages of copper-nickel alloys, their applications, and the critical considerations for their fabrication and design, providing procurement managers with insightful guidance on leveraging these advanced materials for optimal performance and longevity.
Properties of Copper-Nickel Alloys
Copper-nickel mixtures demonstrate exceptional mechanical characteristics, featuring high strength and ductility. These characteristics make them resistant to wear and tear, ensuring their reliability in demanding environments. The addition of nickel greatly improves the mixture’s durability against corrosion, particularly in ocean environments. This makes copper-nickel mixtures perfect for uses that demand durability and longevity, such as shipbuilding and offshore oil rigs. The mixtures’ thermal stability and durability against biofouling further strengthen their status as a favored material in sectors where performance and longevity are crucial.
Corrosion Resistance and Macrofouling Reduction
Copper-nickel mixtures are well-known for their extraordinary ability to withstand corrosion, a characteristic that renders them essential in oceanic uses. These alloys effectively resist biofouling—the build-up of microorganisms, plants, algae, or small animals on wetted surfaces. This resistance significantly enhances operational efficiency and reduces maintenance costs in aquatic environments.
The 2024 State of the Science Report emphasizes the significance of monitoring and environmental evaluations in renewable energy (MRE) projects. For instance, experts have identified that the risk of collision to aquatic animals from tidal turbines needs further research. This emphasizes the necessity for substances such as metal mixtures that can endure severe oceanic conditions while reducing ecological effects.
‘Luc Doan, a Senior Materials Engineer, emphasizes the value of advanced materials in aquatic environments, noting that technologies like cold spray are revolutionizing repair processes.’. This corresponds with the growing use of copper-nickel mixtures due to their durability and low maintenance needs.
Moreover, the International Energy Agency forecasts a fifteen-fold rise in global offshore wind capacity by 2040, emphasizing the necessity for materials that can withstand harsh ocean conditions. Copper-nickel mixtures stand out in this regard, offering both economic and environmental advantages.
Marine Applications
Copper-nickel mixtures are crucial in oceanic uses, renowned for their outstanding resistance to seawater corrosion. These metal mixtures are indispensable in naval and commercial shipping, offshore oil and gas production, desalination plants, and power generation. ‘Their robustness in withstanding harsh aquatic environments makes them a top choice for critical components such as piping systems, heat exchangers, and ship hulls.’. As emphasized by the International Energy Agency, the growing offshore wind sector, which requires high production efficiency and substantial energy output, also gains from the resilience of metal combinations. This focus on resilience and efficiency propels their ongoing application and innovation in nautical engineering and related fields.
Non-Marine Applications
Aside from aquatic uses, these metal mixtures also discover applications in various non-aquatic settings. For example, their antimicrobial properties make them ideal for use in coinage and currency, ensuring a hygienic medium of exchange. In the automotive industry, their strength and thermal durability benefit brake tubing and other essential components. Furthermore, mixtures of copper and nickel are crucial in cryogenic uses and are utilized in resistance wire for thermocouples, ensuring durability and dependability in extreme conditions. As the need in different industries such as automotive and construction keeps rising, the adaptability of these metal mixtures renders them more and more precious.
Fabrication and Design Considerations
When working with copper-nickel alloys, special attention must be given to fabrication and design to ensure optimal performance. Key welding techniques, such as gas tungsten arc welding (GTAW) and gas metal arc welding (GMAW), play a crucial role in maintaining the integrity of joints. Proper preheating and post-weld treatments are vital to enhancing performance and minimizing defects. One often overlooked component in the welding process is the welding liner, which serves as the backbone of the system by guiding the wire from the feeder to the weld. Issues such as burnbacks, erratic arcs, and inconsistent wire feeding can frequently be traced back to problems with the liner or its setup. Therefore, evaluating and maintaining the welding liner is essential to ensure successful welding outcomes and adherence to best practices.
Conclusion
The exploration of copper-nickel alloys reveals their essential role in both marine and non-marine applications, driven by their exceptional mechanical properties and corrosion resistance. These alloys stand out in demanding environments such as shipbuilding and offshore oil rigs, where durability and longevity are critical. Their unique thermal stability and resistance to biofouling further enhance their suitability, making them a preferred choice in industries that prioritize performance and minimal maintenance.
In marine contexts, the corrosion resistance of copper-nickel alloys not only improves operational efficiency but also reduces maintenance costs, aligning with the growing emphasis on environmental sustainability. As industries pivot toward renewable energy sources, the demand for materials capable of enduring harsh marine conditions is set to increase. Copper-nickel alloys are positioned to meet this demand, offering significant economic and ecological advantages, particularly in the burgeoning offshore wind sector.
Beyond their marine applications, the versatility of copper-nickel alloys extends into various non-marine sectors. Their antimicrobial properties make them ideal for applications in currency and hygiene-sensitive environments, while their strength and thermal resistance are invaluable in automotive and cryogenic applications. As the demand for robust materials continues to rise across multiple industries, copper-nickel alloys are poised to play a vital role in advancing technology and enhancing operational reliability.
Attention to fabrication and design considerations is crucial when working with these alloys. Employing appropriate welding techniques and ensuring the integrity of components like the welding liner can significantly impact performance outcomes. By understanding the unique properties and applications of copper-nickel alloys, procurement managers can make informed decisions that leverage these advanced materials for optimal performance and longevity in diverse applications.