Blogs
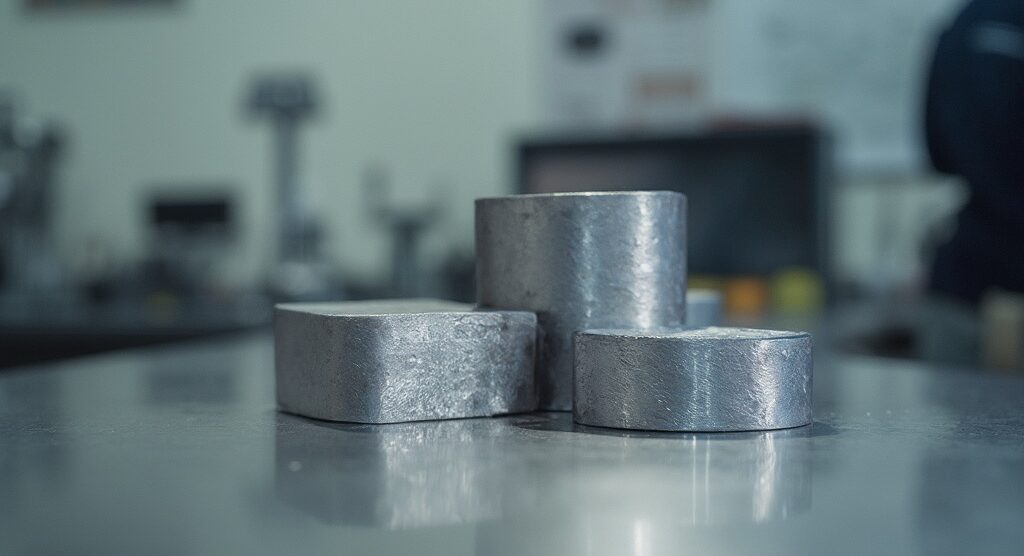
Understanding the Factors Affecting Titanium Tensile Strength
Introduction
Titanium’s unique properties have positioned it as a critical material across various high-performance industries, including aerospace, automotive, and medical fields. The atomic structure of titanium, which shifts between hexagonal close-packed (HCP) at lower temperatures and body-centered cubic (BCC) at elevated temperatures, underpins its remarkable tensile strength. The strategic addition of alloying elements, such as aluminum, vanadium, and iron, further enhances its mechanical properties, creating alloys capable of withstanding extreme conditions and demanding applications.
In high-stress environments, the choice of alloy composition plays a pivotal role. For example, the Ti-6Al-2Sn-4Zr-2Mo (Ti-6242) alloy is specifically engineered for high-temperature applications, making it ideal for turbine engine parts and aircraft skins. However, the performance of titanium is not solely dependent on its composition.
Environmental factors like temperature and hydrogen embrittlement, as well as stress concentrations and fatigue, can significantly impact its tensile strength. Advanced processing techniques and a thorough understanding of these factors are essential to ensure the durability and reliability of titanium components.
Additionally, when comparing titanium to traditional materials like steel, titanium’s superior strength-to-weight ratio offers significant advantages for weight-sensitive applications. However, the choice between titanium and steel is often influenced by specific application requirements, cost considerations, and environmental resilience. This article delves into the intricate details of titanium’s atomic structure, alloy compositions, and the key factors influencing its tensile strength, providing valuable insights for procurement managers and industry professionals seeking to optimize their use of this versatile material.
Atomic Structure and Alloy Composition
Titanium’s remarkable properties are rooted in its unique atomic structure, which exhibits a hexagonal close-packed (HCP) configuration at lower temperatures and a body-centered cubic (BCC) structure at elevated temperatures. This allotropic behavior significantly affects its tensile durability. The alloying components, including aluminum, vanadium, and iron, can be accurately modified to improve the mechanical characteristics of the metal, boosting both its durability and ductility.
For instance, the Ti-6Al-2Sn-4Zr-2Mo (Ti-6242) material is highly valued for its high-temperature strength, making it ideal for demanding applications like turbine engine components and aircraft skins. The stringent manufacturing processes involved in creating high-strength metal forgings ensure exceptional performance, making them indispensable in sectors like aerospace, automotive, and medical industries.
Recent advancements in metal mixtures, driven by innovative research, are paving the way for next-generation materials that can endure extreme environments. Researchers are developing mixtures that withstand high-temperature oxidation, essential for uses in aerospace and nuclear energy sectors. As Noronha emphasizes, metal metamaterials demonstrate potential for upcoming uses, possibly enduring temperatures as high as 600 °C, rendering them appropriate for aerospace and firefighting drones.
Grasping these atomic and mixture composition traits is crucial for enhancing the performance of this metal, providing a combination of lightweight resilience and durability that keeps transforming numerous high-performance uses.
Key Factors Affecting Titanium Tensile Strength
Multiple important elements affect the tensile resilience of this metal. The specific alloying elements used in the composition are paramount. For instance, the Ti-6Al-2Sn-4Zr-2Mo (Ti-6242) alloy, recognized for its high-temperature strength, is frequently used in high-stress scenarios such as turbine engines and aircraft skins. Processing methods play a crucial role as well. Methods such as metal 3D printing have demonstrated the ability to surpass conventional manufacturing constraints, leading to stronger and more dependable components. Microstructural characteristics, such as grain size and phase distribution, are also significant. These elements enhance the overall strength and effectiveness of metal materials, rendering them crucial for important uses in aerospace and various other sectors.
Alloying Elements and Their Impact
Alloying components play a crucial role in improving the tensile durability and overall performance of the metal. For instance, adding aluminum to metal combinations not only enhances durability but also keeps a low density, making it perfect for aerospace uses where weight and performance are essential. This combination is evident in the widely used Ti-6Al-4V material, known for its excellent balance of strength and weight, which is crucial for aircraft components like airframes and engine parts.
Vanadium, another crucial component in metal mixtures, greatly enhances the durability of titanium-based materials, aiding in their capacity to endure intense pressure and challenging surroundings. The Ti-6Al-4V alloy, which also contains vanadium, is a prime example of how these elements work together to enhance the material’s properties, making it suitable for high-performance applications such as turbine engines and medical implants.
Iron, when combined with this metal, enhances its workability, allowing for easier processing and fabrication. This is particularly important in manufacturing sectors where precise machining and shaping are required. For instance, high-strength metal forgings, which often contain a mix of aluminum, vanadium, and iron, are used in critical industries such as aerospace, automotive, and medical due to their superior mechanical properties and workability.
‘The strategic use of these alloying elements ensures that these metal mixtures meet the rigorous demands of modern engineering applications, from aerospace to medical fields, by providing a combination of power, durability, and workability.’.
Environmental Conditions: Temperature and Hydrogen Embrittlement
Environmental factors are essential in influencing the performance of titanium, particularly its tensile capacity. Elevated temperatures can cause phase changes, resulting in a decrease in durability. For example, the Ti-6Al-2Sn-4Zr-2Mo (Ti-6242) alloy, known for its high-temperature strength, is commonly used in turbine engines and aircraft skins but can suffer from surface defects during machining due to the heat generated. Additionally, the presence of hydrogen can lead to embrittlement, compromising the material’s integrity and causing cracks and failures. This hydrogen embrittlement is particularly concerning in high-performance applications where reliability is paramount. Comprehending these ecological effects is crucial for guaranteeing the longevity and dependability of this metal in numerous sectors, ranging from aerospace to automotive. As emphasized by researchers at the Johns Hopkins Applied Physics Laboratory, the need for materials that maintain durability under extreme conditions is critical, making the study of these effects even more important.
Stress Concentrations and Fatigue
Stress concentrations, often arising from design imperfections or notches, significantly impact the tensile strength of this metal. These areas are especially prone to fatigue failure under cyclic loading conditions, where repeated stress can cause progressive and localized structural damage. Appropriate design and material choice are essential to reduce these risks and improve the durability of metal components.
For instance, the utilization of titanium-based mixtures such as Ti-6Al-2Sn-4Zr-2Mo (Ti-6242) in elevated-temperature uses like turbine engines illustrates the significance of enhancing these substances. Despite their high-temperature strength, challenges such as poor machining performance and high chemical activity limit their wider use, particularly in the medical field. Researchers are continuously investigating methods to enhance the wear properties and long-term resilience of these materials to lessen the necessity for modifications in applications such as hip replacements, which are expected to increase by 170% by 2030.
Research has demonstrated that the gradual reduction of bone support and inadequate processing of metal mixtures are primary reasons for failure in medical implants. Methods such as the finite element approach (FEM) are widely used in examining the cutting processes of titanium-based alloys to tackle these challenges. By understanding and addressing the factors that contribute to stress concentrations, designers and engineers can significantly improve the performance and reliability of metal components across various industries.
High-Speed Wear and Corrosion Resistance
Titanium’s inherent corrosion resistance significantly contributes to its tensile strength, preventing degradation even under extreme conditions. While high-speed operations might cause wear, advanced surface treatments and specialized coatings can enhance its durability. This enables the metal to retain its strength over extended durations, making it perfect for high-performance uses. For instance, high-strength metal forgings, created through stringent manufacturing processes, exhibit exceptional mechanical properties, crucial for the aerospace, automotive, and medical sectors. Furthermore, the creative application of lattice formations in metal composites, influenced by natural patterns such as hollow-stemmed vegetation, has shown a 50% enhancement in durability compared to conventional alloys. Such advancements emphasize the significance of comprehending the interaction between wear resistance and tensile force for uses in hostile environments.
Comparative Analysis: Titanium vs. Steel
When assessing titanium compared to steel, it’s essential to acknowledge that titanium has a considerably greater strength-to-weight ratio, rendering it an optimal selection for weight-sensitive uses like aerospace and automotive sectors. Titanium’s lightweight quality, paired with its remarkable durability, allows for enhanced performance and efficiency in these sectors. Nevertheless, steel frequently offers better tensile resistance at a reduced price, rendering it a favored choice for scenarios where financial limitations and maximum load-bearing abilities are essential, like in building and industrial equipment.
The choice between the two metals depends on the particular needs of the use case, including factors of weight, durability, and environmental exposure. For example, metal forgings, recognized for their excellent mechanical characteristics, are widely utilized in high-performance scenarios where longevity and resistance to harsh conditions are essential. These uses encompass aerospace, automotive, medical, and military fields, where the exceptional strength and lightweight characteristics of this metal are indispensable.
On the other hand, steel’s widespread availability and cost-effectiveness make it a staple in various industrial sectors. The North American market, in particular, has seen significant growth in the production and use of stainless steel, driven by its advantages in automotive, construction, electronics, and renewable energy industries. This growth is supported by increasing awareness of the benefits of stainless steel, such as its durability and resistance to corrosion.
In summary, while this metal provides unparalleled strength-to-weight benefits for certain high-performance uses, steel continues to be a strong and cost-effective option for wider industrial purposes. The choice between these materials should be guided by the specific demands of the application, balancing factors like cost, weight, and environmental resilience.
Applications and Considerations for Titanium Use
The remarkable tensile strength of this metal, especially in its composite versions like the Gr5 variant (Ti6Al4V), renders it essential in numerous high-performance sectors including aerospace, automotive, and medical. This alloy is a mixture of aluminum and vanadium, which function together to produce a material that is not only lightweight but also exceptionally strong and durable. High-strength metal forgings, produced through stringent manufacturing processes, offer superb mechanical properties that are essential in demanding applications.
However, the cost and processing challenges of this material necessitate a thorough understanding of application-specific requirements. For instance, the aerospace industry heavily relies on this metal for its strength-to-weight ratio and resistance to extreme temperatures and corrosion. Russia, once the main provider of aerospace-grade metal, supplied half of the globe’s aerospace metal until 2022. The recent disruptions in supply chains have led to delays and resource crunches in manufacturing and maintenance schedules. This shortage has prompted consideration of alternative sources, such as China, which has now become the leading producer of this metal. Nevertheless, this shift poses its own set of challenges, as dependency on another nation could lead to similar supply issues.
Alongside these geopolitical factors, the ecological consequences of producing and processing this metal are increasingly becoming a major issue. As industries strive for sustainability, there is a growing emphasis on eco-friendly manufacturing processes. Events such as CompositesWorld’s CW Tech Days showcase the most recent trends and advancements in composite materials, which are being utilized more and more as substitutes or additions to conventional metal mixtures in different industries.
Comprehending the elements influencing the tensile strength of this metal and its alloy compositions, like the Gr5 alloy, is essential for making informed choices regarding its application in high-stress settings. This knowledge helps in optimizing procurement strategies, ensuring that the selected titanium products meet the specific demands of each industry application.
Conclusion
Titanium plays a vital role in high-performance industries due to its unique atomic structure and the effective use of alloying elements. Its transition between hexagonal close-packed and body-centered cubic structures enhances tensile strength, making alloys like Ti-6Al-4V and Ti-6242 essential for aerospace, automotive, and medical applications.
However, titanium’s performance is affected by environmental conditions and manufacturing processes. Challenges such as temperature fluctuations and hydrogen embrittlement can compromise integrity, while stress concentrations and fatigue must be managed to ensure durability. Advanced techniques, such as metal 3D printing and specialized coatings, are crucial for optimizing titanium’s performance in demanding environments.
In comparing titanium to steel, it is important to recognize their respective advantages. Titanium offers a superior strength-to-weight ratio, ideal for weight-sensitive applications, while steel remains a cost-effective choice for broader industrial use. The decision between these materials should be guided by specific application requirements, weighing performance, cost, and environmental factors.
In conclusion, a thorough understanding of titanium’s properties, including its atomic structure and alloy compositions, is essential for procurement managers and industry professionals. This knowledge facilitates informed material selection and effective application in high-performance settings, driving innovation and efficiency across sectors.