Blogs
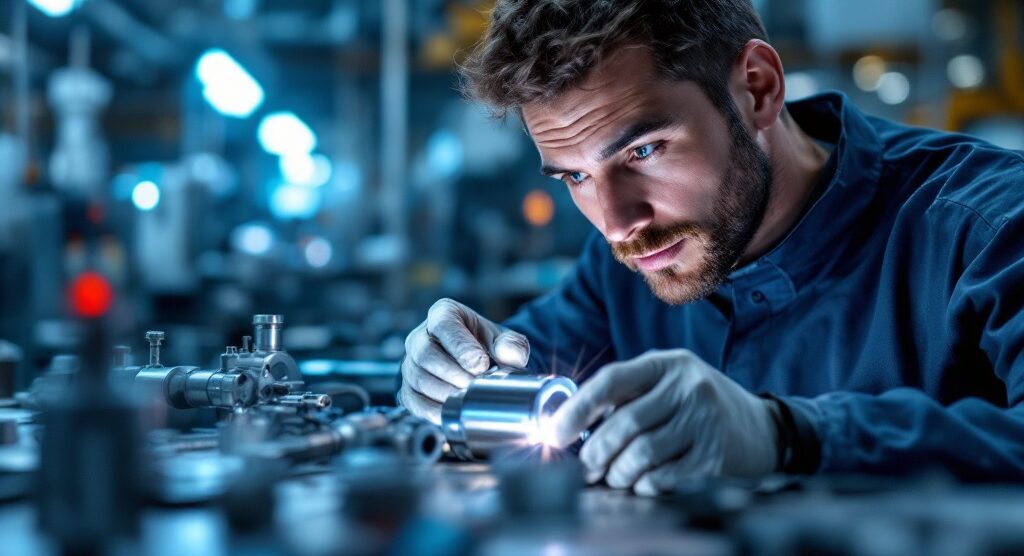
Understanding High Alloys: An In-Depth Tutorial on Properties and Applications
Introduction
In the realm of industrial applications, high-performance alloys are not merely materials; they are the backbone of innovation and efficiency. As sectors grapple with the challenges of extreme conditions, the significance of high-temperature alloys becomes increasingly evident. These alloys, paired with advanced insulation solutions like Mica Tape, offer unparalleled durability and reliability, essential for applications ranging from aerospace to automotive.
Procurement managers are tasked with navigating a complex landscape of material properties, cost considerations, and evolving manufacturing techniques. By understanding the nuances of high alloys—such as the distinct advantages of:
- Nickel-based variants
- Cobalt-based variants
- Iron-based variants
decision-makers can ensure optimal performance and compliance with industry standards. As the market continues to face fluctuations and supply chain disruptions, strategic procurement becomes imperative, paving the way for sustained operational excellence in demanding environments.
Introduction to High Alloys: Understanding High-Temperature Alloys
High-performance materials, particularly high-temperature types, are essential in sectors where substances must withstand extreme conditions. In addition to these alloys, Mica Tape products are designed for high-temperature durability and outstanding electrical insulation, rendering them essential in diverse uses across sectors. The Mica Insulation Tape, for example, is intended for high-temperature durability and provides excellent dielectric capability, ensuring dependability in both home devices and industrial equipment.
Meanwhile, Mica Sheet Tape offers strong insulation for large flat surfaces, especially in aerospace and automotive uses, where mechanical strength and temperature durability are crucial. Procurement managers should recognize the subtleties among various high alloys, including:
- Nickel-based compositions for thermal stability in gas turbines
- Cobalt-based formulations for wear durability
- Iron-based mixtures for cost-effectiveness
Grasping the unique characteristics of these materials, together with the benefits of Mica Tape, including its flame resistance, is essential for informed choice and procurement, ensuring optimal performance in challenging scenarios.
As the sector develops, improvements in metal processing methods and insulation substances such as Mica Tape can further boost effectiveness, especially in aerospace and industrial furnace uses. Considering the existing challenges in the high-performance materials market, like price variations and supply chain interruptions, strategic procurement choices, encompassing both metals and insulation solutions, are more crucial than ever.
Types of High Alloys: Corrosion-Resistant and Beyond
FAQ: Common Applications of Copper Nickel Alloys
Q1. What are the typical uses of copper nickel mixtures?
Copper nickel alloys are widely recognized for their extensive use in marine engineering.
They excel in uses such as ship hulls, offshore platforms, and seawater piping systems, owing to their excellent corrosion resistance, which makes them preferable over stainless steel in these environments. In the automotive sector, copper nickel mixtures are also utilized in brake lines and hydraulic systems, showcasing their versatility across different industries. Beyond these applications, they find use in electronics, heat exchangers, and coinage.
The advantages of copper nickel mixtures are particularly significant in marine environments, where their durability and reliability are paramount. Additionally, nickel combinations, including Inconel and Monel, are recognized for their superior resistance to high temperatures and harsh conditions, making them suitable for extreme environments like aerospace. This highlights the importance of selecting materials that not only meet performance criteria but also align with sustainability goals.
As metallurgists emphasize, ‘Recycling does more than conserve physical resources; it also plays a crucial role in enhancing the lifecycle management of materials.’ Furthermore, the nickel industry engages globally to maximize efficiencies and improve health standards, contributing to sustainability and climate change reduction. Comprehending these classifications and their specific uses enables procurement managers to make strategic decisions, ensuring adherence to industry standards while optimizing operational efficiency.
Additionally, research on the kinetics of sigma phase formation in Duplex Stainless Steel reveals critical insights into the challenges encountered when working with high alloys, which further informs material selection strategies.
Key Criteria for Selecting High Alloys in Industrial Applications
Choosing high-performance materials, including high alloys, for industrial applications requires a thorough understanding of several critical criteria. Among these, mechanical characteristics such as tensile strength, ductility, and fatigue durability are paramount in high alloys. Research by E. Bousquet et al. illustrates that the relationship between microstructure and microhardness significantly impacts the performance of high alloys under various conditions, including corrosion sensitivity.
Furthermore, environmental resistance factors, such as corrosion and oxidation, need to be assessed together with thermal stability, especially with a solution temperature standard of 256 °C, which is vital for numerous applications involving high alloys. For instance, the case study on Aluminum 2024-T4 and 2024-T351 highlights their good machinability and high strength, making them suitable for structural applications like aircraft fittings and hydraulic valve bodies.
Cost considerations, including the availability of high alloys and current pricing trends, are equally vital in procurement decisions, as they can directly influence project budgets. As mentioned by Mahmoud Shehata, a Technician in the Non-Ferrous department at CMRDI, ‘The authors thank everyone who contributed to conducting the experiments for this research,’ highlighting the collaborative effort in material selection.
Additionally, adherence to international standards and regulations is essential to ensure that the chosen materials, such as high alloys, meet industry requirements, thereby facilitating successful project outcomes.
Understanding these factors allows procurement managers to make informed decisions that balance performance with the economic viability of high alloys.
Mechanical Properties of High Alloys: Performance Insights
High-performance materials are defined by their exceptional mechanical attributes, which are essential for various industrial uses. Properties such as tensile strength, yield strength, and elongation are important metrics that measure a material’s ability to withstand stress and its ductility. These characteristics are profoundly shaped by the composition and processing methods of high alloys.
Alongside alloys, Mica Tape Products also play an essential part in high-temperature and electrical insulation uses. Our Mica Insulation Tape, designed for high-temperature durability, offers superior electrical insulation, making it essential in both household appliances and industrial machinery. The Mica Tape for Electrical uses offers outstanding flame resistance and dielectric capability, ensuring safety in fire-sensitive settings like the production of fire-resistant cables.
Furthermore, our Mica Sheet Tape is particularly designed for insulating large flat surfaces, featuring high mechanical durability and resistance to extreme temperatures, perfect for aerospace and automotive uses. Furthermore, our Insulating Mica Tapes are designed for outstanding thermal and electrical insulation characteristics, rendering them crucial in the creation of coils and capacitors that need superior insulation for safety and performance.
Recent studies have indicated that high alloys, particularly nickel-based mixtures with compositions containing 72-83% nickel, demonstrate remarkable high-temperature durability and optimal magnetic properties, making them suitable for challenging uses such as turbine components and transformers. This is illustrated in the conclusions derived from testing on the DZ951G superalloy, where improvements in tensile capacity were associated with the addition of high alloys such as Hafnium (Hf) and Tungsten (W). The research additionally clarified the intricate connection between high alloys and mechanical performance.
In contrast, titanium mixtures are renowned for their remarkable strength-to-weight ratio, crucial for aerospace uses. Their high yield strength and elongation make them suitable for components subject to dynamic loads. As the industry consistently develops, comprehending the complex mechanical characteristics of both high-performance metals and Mica Tape Products is essential for procurement managers aiming to choose the appropriate materials for particular applications, ensuring reliability and safety in critical sectors.
Emerging Trends in High Alloy Manufacturing Techniques
Recent advancements in high-grade manufacturing techniques, particularly in the realm of additive production, have revolutionized the production landscape. This innovative approach enables the creation of complex geometries while minimizing material waste, which is crucial for procurement managers seeking efficient sourcing options. Notably, the maximum tensile strength achieved in the T6 condition is an impressive 483 MPa, demonstrating the significant enhancements in mechanical properties that advanced manufacturing techniques can deliver.
Leading companies in the additive manufacturing space, such as:
- Proto Labs
- 3D Systems
- Stratasys
are at the forefront of these developments, continuously pushing the boundaries of what’s possible. However, it is essential to acknowledge that, as noted, even if additive manufacturing were to dramatically increase production speed and volume performance, it would still be unable to manufacture large single parts. Furthermore, innovations in casting and forging processes are continually enhancing the performance of high alloys in demanding applications.
For instance, the pioneering work by XJet in metal 3D printing showcases their Nanoparticle Jetting technology, which creates highly detailed metal parts with excellent surface finishes. Additionally, research on NiTi alloys reveals how variations in laser scanning strategy can significantly influence grain morphology and mechanical behavior. Automation is also emerging as a pivotal factor, driving efficiency and cost reductions across manufacturing operations.
Keeping abreast of these trends allows procurement managers to strategically leverage new technologies, ensuring access to high-performing materials that meet the evolving demands of their industries.
Conclusion
High-performance alloys, particularly high-temperature variants, are essential for industries that operate under extreme conditions. The interplay between these alloys and advanced insulation solutions, such as Mica Tape, underscores their importance in ensuring durability and reliability across various applications. Understanding the specific advantages of nickel-based, cobalt-based, and iron-based alloys is crucial for procurement managers as they navigate the complexities of material selection. These insights enable informed decisions that align with both performance requirements and cost considerations.
As the landscape of high-performance materials evolves, so too do the manufacturing techniques that enhance their effectiveness. Emerging trends, particularly in additive manufacturing and innovative casting processes, offer exciting opportunities for improved mechanical properties and efficiency. Staying updated on these advancements allows procurement professionals to strategically optimize their sourcing strategies, ensuring compliance with industry standards while mitigating risks associated with supply chain fluctuations.
In conclusion, the strategic procurement of high-performance alloys and insulation materials is vital for operational excellence in demanding environments. By prioritizing informed decision-making and embracing technological advancements, procurement managers can secure the necessary materials that drive innovation, performance, and sustainability across their industries.